Decarbonisation construction activities – electric piling rig
This paper details the approach taken to developing an innovative electric powered piling rig as part of the approach to achieving a diesel-free site on Euston Approaches as part of the HS2 project. This was the first electric piling rig in the UK to be implemented, operating on a renewable energy electricity tariff, and resulted in savings in carbon, air pollution and noise.
The paper outlines the proof-of-concept work to convert on-site diesel equipment (providing equal power output) and achieving de-carbonisation on construction sites, including learning and benefits.
The rig provided a CO2 equivalent (CO2-eq) saving versus the traditional diesel comparative, resulting in zero emissions, and a notable reduction in operational noise below the HS2 re-housing trigger levels at adjacent boundaries of residential facades only one meter away.
Being emission-free the rig presents a milestone for the construction industry’s path toward reaching Net Zero, with positive benefit to local air quality and significant greenhouse gas saving. This paper is relevant to future projects considering making the change to electrically powered heavy duty plant within construction
Background and industry context
This paper is presented as part of the works to deliver the Main Works Civils Contract (MWCC) for the southern section of High Speed Two (HS2) Phase One which includes the Northolt Tunnels and the Euston Tunnel and Approaches, being delivered by the Skanska Costain STRABAG (SCS) Integrated Project Team. In particular, the Southern end of the SCS project is a construction area known as the Euston Approaches.
With an increasing global priority towards tackling climate change, environmental damage, and biodiversity loss, HS2 Ltd’s environmental sustainability vision for HS2 is to provide zero carbon rail travel for a cleaner, greener future. Design and construction of the project plays a significant role in contributing to achieving the low carbon transport and low carbon construction objectives, which are essential parts of the Government’s plans for reducing Green House Gas (GHG) impacts and meeting the UK’s carbon targets.
As part of the contribution to achieving these goals SCS continuously explore low-carbon solutions and more sustainable ways of working. SCS introduced an aspirational project-based Strategic Key Performance Indicator (SKPI) to be ‘Diesel Free by ‘23’ (as shown in Figure 1) that presented an ideal platform to challenge delivery teams and subcontractors to move all pieces of plant to renewable fuels by April 2022.
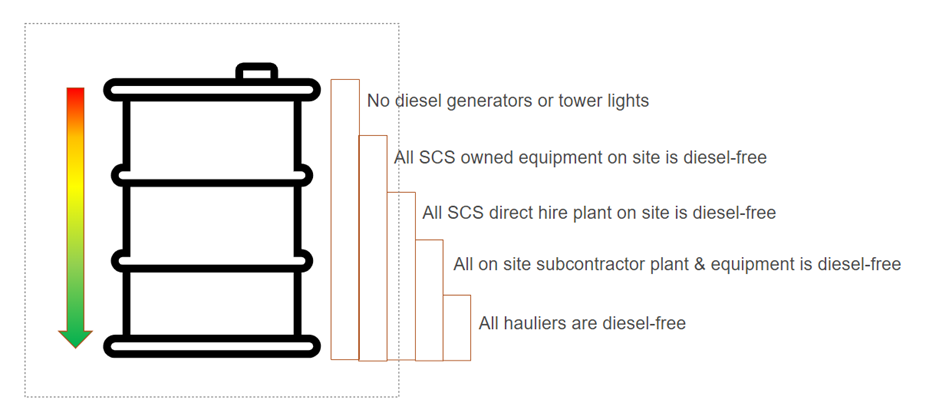
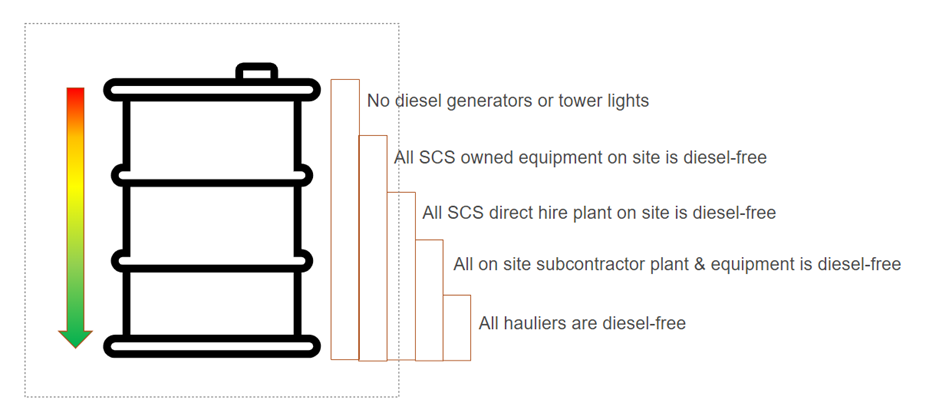
SCS wanted to move all construction plant to being fuelled by renewable fuels, to strive to bringing carbon reductions and becoming a net zero emissions site. This is a significant environmental performance step within the construction industry.
This paper details the approach taken by Euston Approaches to developing an innovative electric powered piling rig as part of their approach to achieving a diesel-free site.
Approach
Euston Approaches achieved a fully diesel-free site running from a combination of mains electricity (renewable tariff), hydrogen or Hydrotreated Vegetable Oil (HVO) biofuels. However initially, encouraging the changeover of all heavy-duty machinery towards renewable fuels met with challenges to overcome perceived misconceptions on how different fuel uses might affect the machinery performance or mechanical integrity, combined with a lack of investment to make the change to renewable sources. However, SCS Euston Approaches was able to achieve the target with the use of HVO for the conventional diesel-powered piling rigs with little or minimal modifications to plant.
Having achieved ‘diesel-free’ the natural progression was to explore the next step to seek opportunities of electric plant and for the SCS Euston Approaches team specifically to implemented innovations to align with producing a low carbon product.
With around 2000 bored piles scheduled to be installed to various depths with the SCS Euston Approaches site, the piling rigs were the dominant plant during 2022 and 2023, and therefore an ideally focus point to explore emissions reductions to zero and conventional noise outputs to acceptable levels. This was especially key as within the footprint of the piling activities, piling was within one meter of residential facades of occupied housing units, that required best practical means be applied to ensuring re-housing levels criteria was maintained.
Working with the SCS piling contractor Cementation Skanska, the team explored whether the piling rigs could be switched to electric power. The first steps were to establish, that the piling rig was able to cope with being placed on to mains electricity. The Bauer eBG 33 rig was initially tested on an HS2 Birmingham site, where the machine was run on generators to prove the feasibility of handling the cable in a live environment.
The electric rig had never been tested before on mains electricity so there wasn’t a prior understanding of the capabilities of the rig. Thereby, SCS and Cementation Skanska brought their knowledge to BAUER Maschinen GmbH’s design.
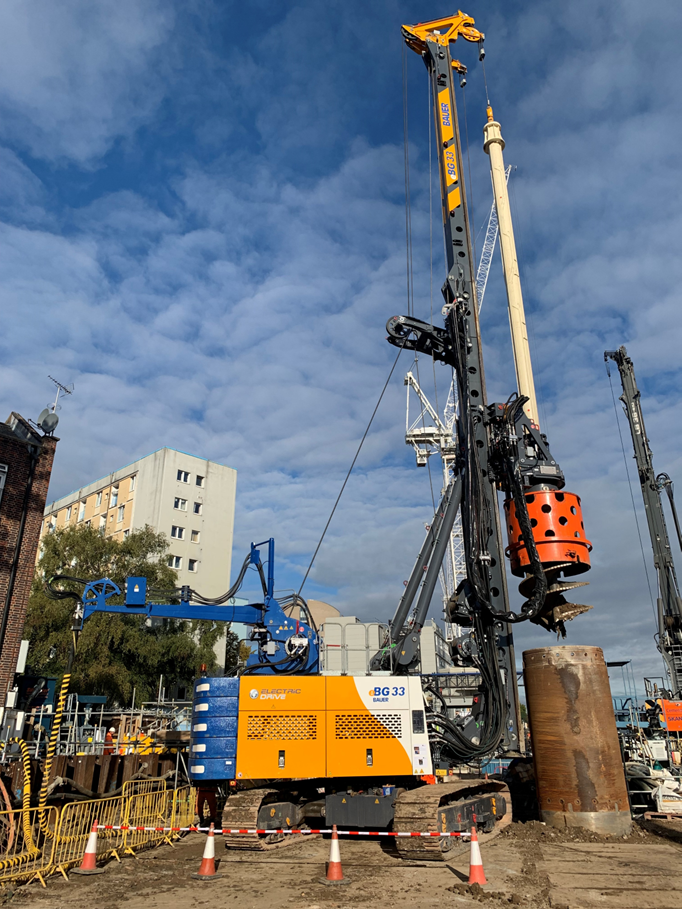
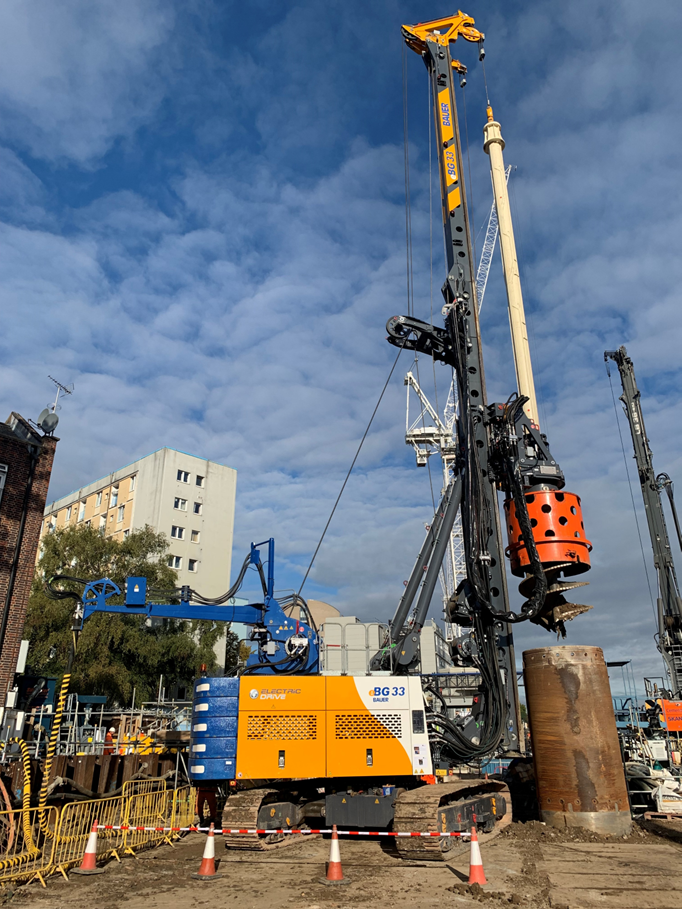
In October 2022 the piling rig shown in Figure 2 was brought to the SCS Euston Approaches site and tested and trialled to ensure that the fullest of its capabilities were being met and compliant with UK standards. Cementation Skanska, working together with manufacturer Bauer Maschinen, installed its own electric substation and was able to plug the rig into the local power grid to do a full test. By using the grid connection, the contractor does not have to rely on a back-up fuel-powered generator.
Early technical problems identified, despite having its own substation, that there was a problem with the electric piling rig and the harmonics on the UKPN system due to the oscillation of load and demand from the rig, that required a short-term return to generators until a demand filter could be procured and retrofitted to smooth out the load. nce installed the rig was able to recommence mains power operations successfully.
Being emission-free the rig presents a milestone for the construction industry’s path toward reaching Net Zero, with positive benefit to local air quality and significant greenhouse gas saving and supports HS2 vision to be totally diesel free by 2029.
Outcomes
- Cost: less energy is needed compared to a traditional diesel-powered pilling rig, but it is just as powerful.
- Quality: first of its kind, high-capacity piling rig in the world to be powered by mains electricity. Constructing 1800mm dia. piles up to 47m deep.
- Environmental: 70 tonnes of CO2 saved versus traditional diesel alternative across 320 working hours on site. Nett zero emissions and presented about a 4dB reduction in operational noise levels compared to a traditional piling rig.
- Carbon: Demonstrates that through collaborative working that decarbonisation of a major construction site is a real feasibility, with the timescales of global carbon reduction.
Learnings and recommendations
- Significant carbon savings, and zero emissions are realised when using the rig on a renewable mains electricity tariff.
- Not only can a piling rig of this type be successfully powered by mains electricity, but it can install piles as efficiently (with no reduction in outputs) as a conventional diesel-powered piling rig.
- Having discovered a harmonics issue within the power system, all parties collaborated to solve this by developing a filter to alleviate this issue.
- Lower sound levels using the electric rig versus an equivalent diesel-powered piling rig.
- Collaboration and forward hinking is vital in making industry leading change.
- There needs to be continuous investment and sharing of information if construction as an industry is going to hit net zero.
We recommend making the change to electrically powered heavy duty plant within construction now, before it is too late to make a difference.
Conclusion
This project is a definition of a collaboration. Working alongside the SCS, Skanska Cementation and BAUER Maschinen GmbH spoke about what works on site would benefit most from an electric drilling rig. All three companies wanted to push the possibilities of the rig from solely being run on generators, to being run on mains electricity. The piling process at the Southern end of the Euston Approaches site is found nearest to local high-rise housing (Cartmel and Coniston Buildings). The collaborative force of Bauer, Skanska Cementation and SCS worked on a product to be able to focus on reducing CO2-eq, air pollution and noise that could negatively affect the residential community. Proving that net zero innovations can bring additionally benefits. Thereby linking into how there needs to be continuous investment and sharing of information if construction as an industry is going to hit net zero.
Acknowledgements
Neil Beresford, SCS Euston Delivery Unit Piling Package Manger.
Deon Louw, Project Director, Cementation Skanska Ltd.
Matthew Gregory, Senior Project Manager, Cementation Skanska Ltd.
BAUER Maschinen GmbH