Decarbonising the EWC
Carbon management on the High Speed Two (HS2) Enabling Works Contract (EWC) was the first of its kind for the industry: it was one of the first projects to request PAS 2080 certification, achieving it in 2019. In total, carbon savings of over 4800 tonnes of CO2e were delivered through the decarbonisation of operational activities. This paper describes the approach in detail and how it is applicable to others in the industry who wish to achieve similar carbon management success, including key management processes such as the Environment and Sustainability Opportunities Matrix and the project-specific Carbon Strategy. It also outlines key achievements and details of how they were enabled, such as eliminating diesel usage across the project, creating a project-wide crushing approach for demolition materials that allowed material to be transferred between sites and contractors, and rolling out carbon management training to all relevant staff.
Background and industry context
With climate change becoming an immediate threat, the effects of which are being felt presently across the world, it is vital that everyone looks to reduce their carbon footprint as much as possible. The recommended pathway in the Climate Change Committee’s Sixth Carbon Budget requires a 78% reduction in UK territorial emissions between 1990 and 2035 through four key steps: take up of low-carbon solutions; expansion of low-carbon energy supplies; reducing demand for carbon-intensive activities; and land and greenhouse gas removals.[1]
The construction industry is no different: greenhouse gas emissions from manufacturing and construction were 66 MtCO2e in 2018, which was 12% of the UK total.[1] It is now critical that the industry sees carbon emissions as a daily risk to be mitigated through every phase of works. The Enabling Works Contract (EWC) on the southern section of High Speed Two (HS2) phase one includes demolition of buildings within the wider Euston area, utility diversions, environmental and ecological monitoring and a programme of historic environment and archaeological activities, delivered by the Costain Skanska joint venture (CSjv).
Due to the dynamic scope of works being undertaken on the EWC, there was no one-size-fits-all approach to the carbon management discipline. The strategy needed to accommodate the dynamic nature of the works, and also to evolve as the project evolved over time.
Approach
Through the development of an Environment and Sustainability Opportunities process and a Project Carbon Strategy, and by working closely with HS2 and the supply chain, CSjv has realised over 4800 tonnes of CO2e reductions.
The upskilling of work package teams, along with the creation of a Carbon Leaders Forum and the development of an internal environmental communications strategy, has been implemented to drive engagement in the carbon agenda and share best practice/lessons learnt on carbon management across the project. The key output of the Carbon Leaders Forum was to empower work package teams to place carbon as a key factor during the decision-making process. The EWC ensured that environmental risks and opportunities were given the priority needed to deliver change and a lasting legacy to the construction industry.
Through the following workshops and initiatives, a culture was quickly developed across the EWC to empower and inspire the next generation of engineers to consider carbon in all aspects of works:
- Environment and Sustainability Opportunities workshops
- Designing-Out Waste Workshops
- Sustainability Impact Weeks
- Carbon Leaders Forum
- Extensive training programme
Outcomes and learning
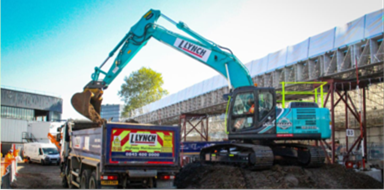
Carbon Strategy
A Carbon Strategy was developed with stretch Key Performance Indicators (KPIs) including: eliminating diesel usage across the project, delivering carbon management training to all relevant staff, and reducing plant idling by 25%. Some of the outputs/achievements of this strategy are detailed below;
- Greenhouse gas reductions: By setting out the benefits at Supplier Engagement Forums, all diesel-powered mobile and static equipment was rolled onto Green D+, a drop-in Hydrotreated Vegetable Oil (HVO) fuel manufactured from sustainable, renewable feedstocks. This was achieved even with the additional cost associated with procuring the HVO fuel, demonstrating that the culture developed on the project placed carbon at the forefront of decision making. The alternative fuel resulted in a 90% reduction in GHGs versus diesel, with 138 tonnes of carbon saved since its implementation.
- Heavy plant idling: Excessive heavy plant idling was targeted via a review of telematic data (data obtained from plant regarding plant movement timings, etc.). Through the implementation of cultural behavioural workshops and the presentation of monthly idling data updates and toolbox talks, a 25% reduction in idling was achieved. This correlated in carbon savings of over 20 tonnes and approximately £7000 in fuel costs in just excavators alone.
Other carbon reduction initiatives included the mandatory use of Renewable Energy Guarantee Origin (REGO) for all facilities connected to mains power, hydrogen/solar powered mobile welfare facilities, the use of electric vans for transfer of personnel between sites, and the use of low-carbon cement for substation foundations. The use of low-carbon cement was enabled through the upskilling and education of site teams to show that it met engineering specifications and that its life cycle was not compromised.
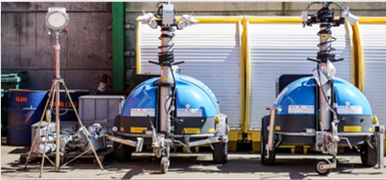
Crushing strategy
A project-wide crushing strategy was introduced to ensure as much demolition arisings as possible could be recycled and used on the site from which they originated. The strategy was implemented across 20 sites, through the upskilling of 15 contractors to consistently manage the crushing operations under the WRAP Quality Protocol.[2] The crushing strategy realized the following savings:
- >35,000 vehicles movements removed from the local road network
- 162,735 tonnes of demolition material crushed
- 1,431,342 litres of fuel savings
- 1,983.42 tonnes of carbon emissions eliminated
- £4,836,000 of saved costs
The in-situ recycling of this demolition waste, combined with numerous other waste reduction initiatives, has meant that over 97% of waste from demolition work scopes has been diverted from landfill. This also resulted in the elimination of hundreds of waste lorry movements onsite and the avoidance of landfill fees.
Sustainable materials
The procurement of sustainable materials was prioritised from the outset. Their use within the supply chain was written into the Invitation To Tender (ITT) phase and embedded within supply chain contracts. A Sustainable Procurement Plan was produced, with KPIs assigned to products with the potential for higher environmental impact. This included a requirement for 100% of all steel, timber and cement products to be supplied with third-party certification in place (including BES 6001 or a BREEAM-recognised responsible sourcing certificates). The Sustainable Procurement Plan is shared alongside the Carbon Management Plan to support this learning legacy.
Recycled aggregates
Prioritisation of recycled aggregates was driven via the use of a bespoke Material Acceptance Form which involved the Environment Team taking part in the process with the Materials Team to ensure evidenced compliance with requirements. Over 125,000 tonnes of imported recycled aggregate have been used within utility trench backfill, piling mats, laydown areas and temporary haul roads. This avoidance of virgin materials realised cost savings of £750,000, with 574 tonnes of carbon saved.
Design management
CSjv has a logical process for design modelling and rating to ensure that environmental performance is delivered and evidenced. Combining the principles of PAS 2080 [3] and design management, permanent assets are baselined at RIBA 3 (scheme design) stage and a Life Cycle Assessment (LCA) is carried out using the calculations of embodied carbon at RIBA 4 (detailed design) stage. Where viable, an As-Built LCA is also carried out for assets that are being constructed by CSjv. Throughout this process, designers and other stakeholders work collaboratively to design out or drive down the embodied and operational carbon. All interventions and innovations are documented in the Environment and Sustainability Opportunity Matrix process, involving a multidisciplinary workshop at each design stage and prior to construction where sustainability opportunities are identified, owners assigned and their progress tracked throughout the life cycle of the opportunity.
Applying the principles of PAS 2080 along with the Environment and Sustainability Matrix, CSjv has also delivered carbon reduction in permanent asset design. When contracted to be the designer for the Granby Terrace bridge extension just north of Euston station, a 13% reduction in embodied carbon (equivalent to 1000 tonnes of CO2e) through design was achieved. This was done through design interventions such as moving from a piled box to a less carbon intensive barrette solution, a reduction in the number of piers being constructed, and the replacement of Portland cement.
Recommendations
- An environmental opportunities realisation process similar to the Environment and Sustainability Opportunities Matrix process should be considered to ensure environment and sustainability opportunities are captured during the planning of works and that action plans/responsible people are assigned to ensure they are implemented as far as possible.
- Empower all staff to raise potential carbon saving interventions through engagement events, Carbon Leaders Forums, carbon training and senior leadership engagement.
- Assign Carbon Leaders/Champions across the project.
Set targets on carbon reduction and provide updates on progress to ensure engagement and momentum is maintained.
References
[1] Climate Change Committee. The Sixth Carbon Budget: Manufacturing and construction. [internet]. 2020 [cited 2021 Nov 24].
[2] WRAP and Environment Agency. Aggregates from inert waste: End of waste criteria for the production of aggregates from inert waste. 2013 [cited 2021 Dec 10].
[3] BSI. PAS 2080 Carbon Management in Infrastructure Verification. 2021 [cited 2021 Dec 10].
Acknowledgements
Kenneth Hills, Simon Taylor, Phil Alcock, Sergio Perez, Alex Davis, Kinga Holda, Siobhan Pereira, Callum Mair, Serena Ward, Alex Meek, Simon Mintoft, Robert Lockwood, Thomas Cleary, George Horsely, Mark Leadbitter, Andy Evans, Era Shah, Hanna Toorabally, Taj Daroge, Dan Brown, Mark Wotton, Jason Dingle, Clive Metti, Caroline Raynor, Aiden Marchetti.