Digital in transit concrete monitoring system
Existing digital in-transit truck monitoring technology has been utilised in a novel way to directly replace standard concrete compliance testing of fresh properties (i.e. concrete consistence). The adoption and validation of digital systems as the primary means of control instead of manual testing has never previously been approved for this purpose.
There is no existing standard for this and as such, collaboration between client, concrete supplier, technology provider and BBV led to definition of agreed metrics and compliance for adoption.
However, the use of this technology alone is only part of the solution. To realise the benefits in resource efficiencies for site testing, a new approach to compliance testing of hardened concrete properties was also required. The demonstration of mix performance and derivation of mix families to monitor compliance was essential.
VERIFI® (a Saint-Gobain system) was highlighted during early stages of concrete supply contract engagement as an available solution with both BBV and Tarmac having direct experience with this technology. The provision for adopting VERIFI® was also included within the specific concrete supply contracts and rates used to inform the incentive budget.
However, experience of using VERIFI® was limited to a small scope of uses and mixes. This extensive trial looked at how the system works and evaluated differences between manual testing and the automated system across a range of mixes and applications including how this system could be used to reduce / eliminate the requirement for site technicians.
It is anticipated that this approach will change the way that ready-mix concrete is supplied and assessed for compliance. The updates within the recent publication of BS 8500:2023 allow the use of digital monitoring (under the provision of digital surveillance).
This learning legacy documents the key stages and learning outcomes of the trial completed demonstrating proof of concept of the solution and
will provide useful references and inform controls to enable wider adoption by both concrete producers and customers.
Background and industry context
Concrete has traditionally been batched and dispatched with no visibility of the properties of the concrete load (apart from mix proportions) until arrival at site and manual testing by a concrete technician.
Digital systems enabling visibility of the concrete and its properties throughout the delivery cycle have been developed. The use of these tools has to date been limited to supplier control rather than by contractors or customers to determine compliance.
Balfour Beatty Vinci (BBV) is delivering the Main Works Civils Contract (MWCC) for the northern section of High Speed Two (HS2) Phase One (also known as Area North) including Long Itchington Wood Green Tunnel to Delta Junction and Birmingham Spur and the Delta Junction to the West Coast Main Line (WCML) tie-in.
The BBV concrete supply strategy for Area North is based on dedicated on-site batching plants to supply 1.9 million m3 of concrete. Controlling the performance from batching, during transit to quality checks prior to placing in the works is essential to the successful delivery of consistent compliant concrete. Due to the scale of the HS2 Area North concrete demand, it was determined during the tender stage that manual consistence (or “workability”) testing of every single concrete load (as typically specified) would not be practical due to the considerable level of staff and equipment required. With the significance of many structural assets and the high-profile nature of the project, lower test frequencies were not deemed acceptable. Manual testing is also inherently at risk of being affected by human error.
Therefore, an alternative method was required to ensure the quality control of each load of concrete supplied. An innovative solution was adopted based on the use of digital in-transit truck monitoring for compliance assessment. As this technology has never previously been adopted for this purpose or accepted by a client, this is a world-first innovation.
Approach
The idea to use digital in-transit truck monitoring technology for concrete compliance assessment on-site was identified at an early phase during Stage 1 of the project. Early engagement with concrete suppliers and the technology provider resulted in provision of digital surveillance being included in the supply orders at this early stage.
During early works, a successful trial was completed, demonstrating proof of concept. Following this, a departure from standards submission was made and subsequently approved. This learning legacy documents the key stages and learning outcomes of this solution.
Standard testing arrangements – What did we do before?
- Producer control testing – Manual testing at concrete plant carried out when required prior to dispatch and/or visiting technician to customer site.
- End user / Customer testing – Supplementary testing requirements specified by designer or client to validate the quality of concrete supplied. This involves sampling and testing of loads supplied to site with every load typically tested for concrete used in key structural elements.
The Technology
VERIFI® (a Saint-Gobain system) was highlighted during early stages of concrete supply contract engagement as an available solution with both BBV and Tarmac having direct experience with this technology. Figure 1 shows the key components of the VERIFI ® system.
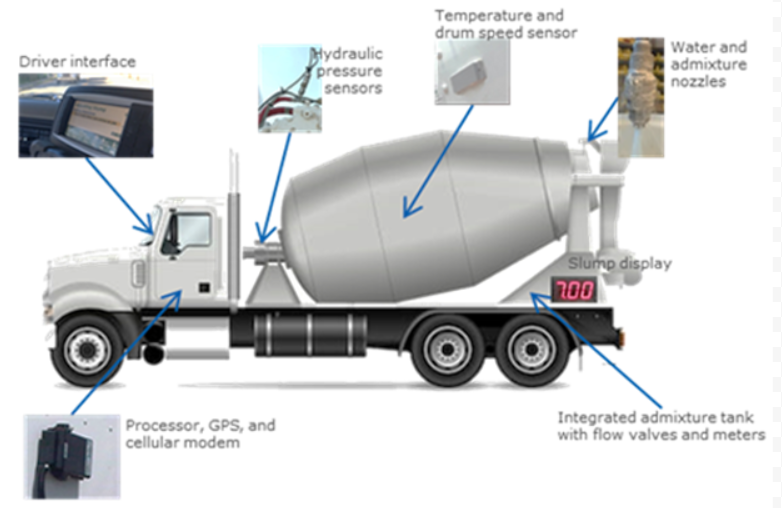
Hydraulic pressure sensors and drum rotation sensors via the VERIFI® system enable rheological (i.e. flowability) measurements by analysing the force required to move a particular concrete at different drum speeds. Using well-established rheological models, consistence predictions can be developed based on these hydraulic pressures and drum speeds.
In addition, a controlled amount of water or admixture can be added in-transit to adjust consistence if the total water does not exceed the design water-to-cement ratio.
With GPS tracking being an embedded feature of this system, all stages from loading through transport and discharge are time stamped enabling full transparency and traceability for the concrete supplied.
The use of technology to reduce manual testing was implemented to optimise testing resources and improve productivity.
Stage 1 – Resource planning
The provision for adopting VERIFI® was included within the specific concrete supply contracts and rates used to inform the incentive budget.
The approach for controlling concrete digitally was agreed between the Producer, Technology Supplier and Main Works Contractor with costs agreed on an open-book basis.
The use of this technology was also built into the materials testing forecast, reducing the overall number of testing technicians budgeted.
Stage 2 – Trial
Experience of using VERIFI® was limited to a small scope of uses and mixes. This extensive trial looked at how the system works and evaluated differences between manual testing and the automated system across a range of mixes and applications including how this system could be used to reduce / eliminate the requirement for site technicians.
This proof-of-concept trial was planned to coincide with initial supply to early programmed assets. The scope of the trial covered approximately 20,000m3 of concrete produced from the first temporary mobile plant located at Fosseway compound. This covered several mix types allowing assessment of the accuracy of VERIFI® in monitoring normal consistence structural concrete and high flow mixes for ground engineering.
Once this volume was complete, the data for each objective below was reviewed collaboratively between the three parties to decide how VERIFI® performed and whether it would be suitable for onward roll out for HS2 concrete supply. The following objectives were used to decide if VERIFI® in-transit management is a viable alternative to manual testing on this project:
- Assess the risk to supply if VERIFI® consistence data was used to pass / fail loads at the job site.
- Validate the ability of VERIFI® to accurately adjust slump automatically with water and admixture within the water / cement ratio of the design.
- Assess the risk to supply if VERIFI® site delivery temperature data was used to pass / fail loads at the job site.
- Measure the effects on concrete properties when water and admixture are added continuously during transit instead of at the plant or jobsite only.
- Highlight the Safety, Sustainability and Resource benefits of VERIFI®’s features for the project.
Trial outputs
The consistence measurements taken by BBV technicians at the site were collated and compared with the relevant VERIFI® reading for the load. This analysis was reviewed periodically to establish whether there was a comparable output between the 2 types of measurement.
The trial demonstrated a close correlation between digital monitoring and manual testing across the range of mixes. More importantly, there were no significant differences in outcome for acceptance / rejection with correlation at each end of the tolerance range proven to be satisfactory.
The trial also confirmed the specific mix properties which influence the accuracy of the system – these were determined to be:
- Cement type (by GGBS proportion)
- Aggregate size and type
The trial validated that digital monitoring could be used to replace or reduce the amount of manual testing required without compromising assessment. Families of mix types were determined based on cement type, aggregate size and shape and by specific use.
Stage 3 – Implementation process
A series of technical review meetings were held with the technical leads from both designer (DJV) and client (HS2). As part of the technical proposal, specific equipment and technology calibration, maintenance and operational checks were agreed. These are covered below in the section Validation and Use.
A staged approach was proposed to replace manual testing with digital monitoring progressively, based on validation of ongoing data to ensure continued accuracy.
To realise efficiencies with testing resources, testing of hardened concrete needed to be considered in addition to the testing of fresh concrete properties. The relatively high frequency of sampling for compressive strength testing (1 set of cube specimens / 24m3) would be reduced in line with the progressive reduction of fresh concrete testing. This would allow testing technicians to visit multiple pour locations in a given day rather than a single technician assigned to a single pour. The framework for the testing reduction is included in Appendix A.
A departure from standards technical proposal was submitted to the client specifically for the following changes to testing methodology:
- Change the primary method for assessing compliance of concrete consistence by slump / flow table method only to VERIFI® digital monitoring system. The frequency of inspection and testing i.e. each load, is unchanged although the digital method proposed to replace manual testing is outside of current standards. In addition, a reduced frequency of standard manual testing would be maintained to ensure ongoing correlation and confidence.
- Fresh concrete temperature monitoring would be managed in a similar way to that detailed for consistence compliance. Digital monitoring using VERIFI® is also proposed as the primary method of compliance assessment. The method for measuring this is stated in BS 8500-2: 2019 Cl5.4. This standard also permits the use of an alternative form of temperature measuring device. Therefore, the adoption of VERIFI® digital monitoring in lieu of a manual temperature reading is not a departure from standards. However, calibration of VERIFI® thermometer probes would be addressed. In addition, a reduced frequency of standard manual testing would be maintained to maintain ongoing correlation and confidence.
- Compressive strength testing frequency reductions were also proposed. A staged approach aligned to gradually reducing manual fresh concrete testing frequencies was proposed. These stages required passing hold points where compliance and consistency of results had to be achieved.
Following the Departure from Standards approval, the designer updated the project specification to specifically include the adoption of digital monitoring with corresponding reduced manual test frequencies. The Inspection and Test Plan (ITP) was also updated in line with the revised project specification.
Validation and use
BBV defined the metrics as part of the Departure in Table 1 to prove compliance of the VERIFI® system.
The following control measures were approved as part of the technical proposal to ensure that VERIFI® is functioning correctly:
- HS2 Area North dedicated VERIFI® technical support on-site engineer due to the scale and importance of the project. A BBV digital data co-ordinator was also appointed to ensure quality of reporting.
- Ongoing correlation of digital monitoring with manual testing as per Table 1 and Appendix A.
- Driver behaviour is monitored by Supplier/VERIFI® who discuss performance weekly. If poor driver behaviour is identified in respect of operating the VERIFI® system re-training will be undertaken and recorded in training record.
- A specific calibration and maintenance schedule of equipment fitted to truck mixers as per Table 2.
Category | Metric | Result/Data | Metric reasoning |
---|---|---|---|
Manual test / VERIFI® correlation satisfactory? |
Clear correlation line? |
Although correlation coefficient is not necessarily the best indicator (See Anscombe Quartet), and the differences in outcome as below can be considered more critical, the correlation provides a good indicator of performance. | |
Are 95% of results within agreed tolerance? |
30mm slump variability / 60mm flow variability (between VERIFI® and manual test) derived from reproducibility values from test standards. | ||
Acceptance / rejection satisfactory? |
No. loads rejected: |
Are the suppliers correctly utilising VERIFI® to optimise their batching process and deliver the efficiencies anticipated from implementing the system? | |
No. loads accepted: | |||
Rate of rejection: | |||
No. differences in outcome between manual and VERIFI®: |
Would VERIFI® have allowed any loads BBV manual test would have rejected? | ||
Cube strengths satisfactory? |
Maximum strength: |
This data will be used to ensure ongoing concrete performance. | |
Minimum strength: | |||
Running Mean Strength (RMS): | |||
No. sets taken: | |||
No. non-compliant results: | |||
Standard Deviation: | |||
Maturity Correlation: |
Item | Frequency | Method | Person responsible |
---|---|---|---|
Sensors |
Daily |
Online check within working range |
Technology provider / Producer |
External Digital Display working (if applicable) |
Daily |
Visual inspection |
Driver |
In cab Digital Display working (if applicable) |
Daily |
Visual inspection |
Driver |
Truck visibility on digital application |
Daily |
Visual inspection |
Technology provider / Producer |
Flowmeter [1][2] |
Annually or otherwise as agreed between producer and specifier |
Check vs calibrated vessel |
Technology provider / Producer |
Thermometer |
Annually or otherwise as agreed between producer and specifier |
Manufacturers calibration certificate for probe Scheduled battery life check where fitted Ongoing check vs calibrated thermometer (number of readings to be agreed between producer and specifier) |
Technology provider / Producer |
Drum concrete build-up |
6 monthly or if online sensor detects fault |
Visual inspection and check after removal. |
Producer (Physical check and or pressure Sensor check) |
[1] Flowmeter calibration required for in-transit tempering where used under the control of the Producer[2] Cold weather protection procedure such as drain down recommended to mitigate inaccurate water flow and flowmeter damage. |
Changes to project processes:
- Project specification updated to specifically include digital monitoring and revised ITP for concrete testing demonstrating implementation of staged procedure and hold points.
- Metric to be produced to validate passing each hold point as per Appendix B
- Briefings to operational teams on implementation, concrete acceptance criteria and issue resolution – briefing guide can be found in Appendix C
- Compliance criteria for consistence classes is fitted to each truck mixer as per Figure 2 for ease of assessment.
- Testing technicians briefed regarding their role in implementation of VERIFI® – briefing guide can be found in Appendix D
- Digital pour record reporting system linked into BBV existing reporting folder structure – example in Appendix E
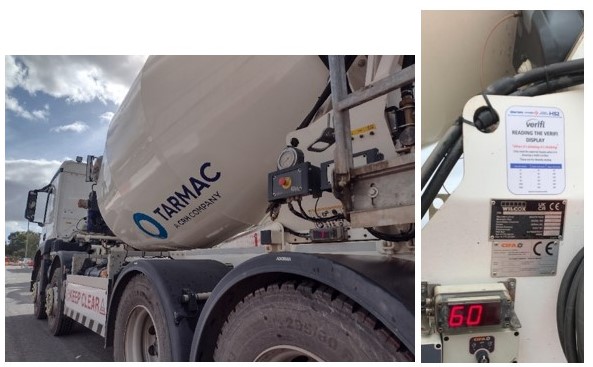
Outcomes
Key benefits and outcomes, and the changes which led to them, are highlighted in Table 3 below. Further explanation is also provided.
- Evidence of current performance of the system can be found in Appendix B <learning legacy team to insert link to supporting document>. This shows ongoing conformity of the system in accordance with HS2 agreed metrics in Table 1.
A further benefit is that implementing VERIFI® has led to the production of digital quality records, which can be produced without attendance at the pour. This ensures that all quality data is available digitally with no gaps.
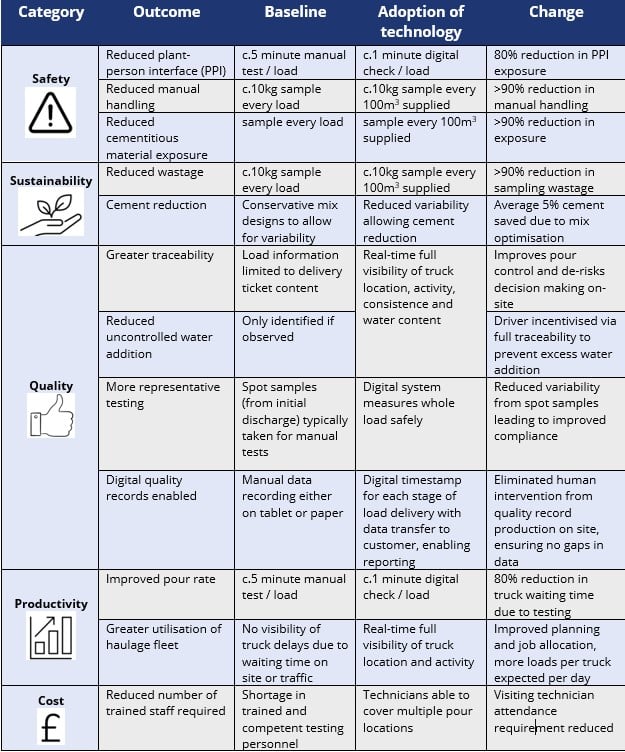
Further detail of the key benefits can be found below:
Safety
- Improves job site safety as measurement method reduces vehicle / person interaction.
- Reduced out of hours working where manual testing would otherwise be required.
- Reduced manual handling due to reduced sampling and manual testing.
- Reduced exposure to cementitious materials through reduced sampling and testing.
Sustainability
- Reduced wastage from sampling where access to the concrete delivery point to return it is not safely or logistically achievable.
- Enables visibility of the fresh concrete properties throughout the delivery cycle which means only compliant concrete should leave the plant, minimizing rejections and waste concrete.
- Cement reduction due to reduced variability of batching plant output.
- Optimisation opportunities for w/c ratio designed mixes.
Productivity
- Improved pour rate due to reducing testing delay.
Quality
- Enables visibility of the fresh concrete properties throughout the delivery cycle which means only compliant concrete should leave the plant.
- Controlled water or admixture addition within maximum allowable range by digital system, under producer control, will improve “Right First Time” deliveries.
- Reduction in uncontrolled water addition at site due to full visibility enables its occurrence to be addressed.
- Digital consistence monitoring systems provide a more representative reading of consistence as it measures the complete batch of concrete within the truck as opposed to the spot sample used for site testing.
- Digital fingerprint from batching to discharge.
- Digital quality records produced, improving ease of data sharing.
Cost
- Reduced number of trained staff required to carry out consistency / workability testing of the concrete on site, reducing project costs.
- Maximises utilisation of haulage as the overall visibility of truck movements allows quick detection and resolution of bottlenecks, pour analysis tools help prevent over trucking and there is no testing delay before discharging.
- Potential reduced waiting time due to greater visibility to manage this.
Learnings and recommendations
The implementation of digital surveillance encourages greater collaboration between all parties (client, specifier, contractor / end user, concrete supplier and technology provider).
- The metrics adopted for initial system correlation against manual test for each mix type proved to be onerous. However, good control of both digital system and testing technician accuracy enabled compliance. The control of testing technicians needed a real focus – reproducibility between technicians is as big a focus as reproducibility between manual data population and digital data population could be a potential source of variation. A full time BBV digital data co-ordinator was appointed to monitor compliance and trends, liaising with the dedicated VERIFI® engineer. Furthermore, it was necessary to provide training and instruction to end users (operational BBV site teams and sub-contractors). Specific briefing aids were produced and are included in Appendices C and D (see below in supporting materials).
A large population of data was required for approval as this was proof of concept. It is acknowledged that the extensive upfront correlation work (required for proof of concept) would not be feasible for the majority of schemes, and should not necessarily be required henceforth. While adoption of digital surveillance can significantly reduce manual testing requirements, ongoing validation and testing of other concrete properties (such as compressive strength), may also be required for which a reduced frequency of sampling and testing may be agreed.
With the laboratory team also providing the quality records for all concrete placed in the works, a data management solution was also required to enable these records to be generated when a technician was not present on site. Extensive work between BBV, concrete suppliers and the technology provider enabled specific order details and unique asset identification codes to be specified and included on electronic delivery tickets. Data transfer between parties and their respective systems was collated and downloaded into a single digital file for each shift. This allowed BBV to filter records for each asset and produce the quality records required without specific attendance on site.
The digital solution was transferable across a wide range of concrete types. It was appropriate for normal-consistence concrete (controlled by slump test) and high-flow mixes (controlled by flow-table test). It should be noted that the repeatability and reproducibility is different for the different test methods and as such varying correlation tolerances were chosen. Further work to explore feasibility for other special concretes controlled by different test methods (self-compacting mixes and very dry mixes) is required.
Some batching command systems interface more easily with this technology than others and as such, compatibility should be considered at an early stage. This led to delayed implementation from certain batching plants. This was overcome with IT solutions following collaboration between supplier, digital technology provider and contractor.
Knowledge has been shared across HS2 Main Works Contractors and within parent companies (Vinci and Balfour Beatty). A press article has been released by HS2.
A new technical guidance note for digital concrete monitoring has been drafted in collaboration with i3P (Infrastructure Industry Innovation Partnership), a community of client and supply chain organisations. This guidance outlines the approach to correlation and implementation which is suitable for projects of all sizes. This guidance will soon be published by the Concrete Society as part of the Good Concrete Guide Series
Summary of learnings and recommendations:
- Encouraged greater collaboration between all parties.
- Digital dashboard and reporting system developed for real-time monitoring.
- Compliance metrics adopted were onerous.
- Control of testing technicians demands focus.
- Site teams controls and guidance must be issued.
- Appropriate means of correlation and validation to be established and standardised.
- Further work required for correlation with concrete controlled by other standard consistence test methods.
- Ensure batching command systems interface with this technology.
- Digital surveillance should be specified where required as part of a concrete supply agreement.
- New digital standard (technical guidance) under development via i3P.
Conclusion
This is the first time that digital technology has been adopted as the primary fresh concrete compliance assessment method to reduce manual testing. A departure from standards was approved enabling implementation.
The key steps to allow this were:
- Provision for digital surveillance included in supply orders at very early stage.
- Successful full-scale trial across 20,000m3 with proof of concept demonstrated.
- Compliance metrics and approval hold points agreed as part of departure submission.
- Training and guidance delivered to all users.
- Digital quality record reporting system developed.
- Full time monitoring role in-place to ensure system performance and compliance.
The key benefits of the system are:
- Improved safety due to reduction in vehicle / person interface, manual handling and exposure to cementitious materials
- Sustainability benefits due to reduced wastage and optimised mix designs.
- Improved quality, eliminating uncontrolled water addition with full traceability and digital reporting of quality records.
- Improved productivity with higher pour rates and better truck utilisation.
- Cost benefits from reduced requirement for competent staff and reduced truck waiting time.
The learning legacy is the adoption of digital surveillance of fresh concrete properties by the customer for the purpose of compliance assessment on site. At the time of writing, the adoption of digital surveillance was not covered by standards and adoption was limited to supplier control only. BS 8500:2023 now includes for the provision of digital surveillance but no standard methodology has yet been published. The methodology described above forms the basis of the new technical guidance being developed in collaboration with i3P. This puts HS2 and BBV at the forefront of this step change in concrete compliance assessment.
Acknowledgements
Balfour Beatty Vinci, Main Works Civils Contractor, HS2 Phase 1 Area North
Mott McDonald-Systra Design Joint Venture, Main Works Civils, HS2 Phase 1 Area North
Tarmac, Supply Chain Partner to BBV and HS2
Aggregate Industries, Supply Chain Partner to BBV and HS2
Saint Gobain Construction Chemicals
References
Contract documents
- Specification for Civil Engineering Works – Series 1700: Structural Concrete
- Specification for Civil Engineering Works – Series 1600: Piling and Embedded Retaining Walls
- Specification for Civil Engineering Works – Series 1000: Road Pavements – Concrete Materials
- Specification for Civil Engineering Works – Series 2600: Miscellaneous
- Main Works Civils Contract Works Information WI 310 Contractor’s assurance
Standards
- ISO 9001: 2015 Quality Management System
- ISO 14001: 2015 Environmental Management System
- ISO 45001: 2018 Occupational Health and Safety
- BS EN 206:2013 Concrete – Specification, performance, production and conformity
- BS 8500:2019 Parts 1 and 2 Concrete – Complementary British Standard to BS EN 206
- BS EN 12350-1:2009 Testing fresh concrete: Sampling
- BS EN 12350-2:2009 Testing fresh concrete: Slump-test
- BS EN 12350-5:2009 Testing fresh concrete: Flow table test
- ASTM C94 / C94M – 21 Standard Specification for Ready-Mixed Concrete
Supporting materials
Appendix A: Flowchart for implementation of VERIFI®
Appendix B: Example of compliance dashboard against agreed metrics
Appendix C: Site team guidance
Appendix D1: Testing team guidance
Appendix D2: Consistence and temperature limits
Appendix D3: Example of digitally produced pour record
Peer review
- Jon KnightsHS2 Ltd