Dust Suppression Trials – reduction in fugitive dust emission from construction site haul roads using water additives
A review of construction activities within High Speed Two (HS2) construction sites determined that haul roads are a major contributor to fugitive dust emissions, and can have significant detrimental effects for nearby ecological sites and people living and working in the vicinity of large construction sites. Significant quantities of water are used in the construction sector to reduce and control fugitive emissions of dust from construction activities and water suppression of dust is a method widely used across the HS2 Phase One Northern section construction sites. This represents a significant use of water, itself a limited resource at some sites, in addition to the associated costs and time to apply water for the suppression of dust.
A desktop review of available dust suppression additives was undertaken to identify potential additives that could be used to help reduce water usage on HS2 construction sites. Four products were identified in this process and taken forward to site trials and compared against two controls – the use of water as current best practice, and no dust suppression. The aim of the site trials was to help determine the potential benefits of using dust suppression additives on HS2 construction sites in terms of cost saving and fugitive dust control, and recommending which products should be considered for purchase.
Site trials were undertaken from June 2023 to October 2023. The results of the trial concluded that the use of dust suppression additives can present a significant reduction in the amount of water used, with a similar benefit in terms of reducing dust generation. Costs savings are possible but are affected by factors such as if water needs to be purchased or is readily available, required frequency of application of dust suppression and if savings can be made in equipment hire and labour.
Background and industry context
Within the UK, construction sites are required to ensure that their activities do not lead to significant detrimental effects on the people living and working in the vicinity of the site, or on adjacent ecology sites. This includes potential effects on the amenity of people’s properties, effects on their health and effects on sensitive ecological sites from deposition on vegetation or changes in soil chemistry. Uncontrolled emissions of dust from construction sites, referred to as fugitive dust, can cause significant effects on the receiving environment, and often require control measures to prevent them. Within construction sites, the movement of material – such as soils and aggregates – and the movement of vehicles and plant on internal unsealed haul roads represent significant sources of fugitive dust emissions and can be difficult to control due to the physical extent of construction works, the level of activity or the proximity of the activity to the boundary of offsite sensitive receptors. In order to control fugitive emissions, water is typically used to dampen haul road surfaces or stockpiles to maintain higher moisture contentto prevent fine material becoming airborne, effectively binding them into larger particles which are less likely to become airborne.
The same is true across High Speed Two (HS2) construction sites, and water is extensively used by the sublots to reduce fugitive dust emissions. In order to be effective, water needs to be applied to every haul road or exposed area within a sublot between three to five times per day during dry periods. This is a significant undertaking, representing a significant use of water, labour, equipment and time, all of which have direct costs associated with them.
This paper is presented as part of the works to deliver the Main Works Civils Contract (MWCC) for the northern section of High Speed Two (HS2) Phase One including Long Itchington Wood Green Tunnel to Delta Junction and Birmingham Spur and the Delta Junction to the West Coast Main Line (WCML) tie-in, being delivered by the BBV Integrated Project Team. . BBV produced a Dust and Water Management Plan to demonstrated compliance with HS2 requirements to control emissions from their construction sites, including the use of dust suppression additives where appropriate to reduce water use and control fugitive dust emissions. There are a wide variety of products available on the market for use as a dust control additive. To decide which product would provide the greatest benefit to HS2 in terms of water savings, dust control and cost reduction, AECOM was commissioned by BBV to review the available literature on dust suppression additives and design site trials to assess the different products and compare them to the existing current practice of using purely water as a suppressant and against a baseline of no suppression. AECOM reviewed the current construction activities on HS2 construction sites, and it was decided that haul roads and earthworks presented the greatest risk in terms of fugitive dust generation. A section of haul road in Sublot 8 was identified to undertake site trials. This section of haul road was relatively isolated from other dust sources, so that the haul road’s contribution to dust levels could be determined from the data without other external influences.
Approach
Product selection
The first stage reviewed the different products currently available on the market within the UK, using previous studies to help identify particular product types and possible benefits they could offer. Suppliers’ literature was reviewed to identify four additives to take to site trials, based on the following attributes:
- Mode of action for dust suppression.
- Potential hazards to human health, ecology, and equipment.
- Potential cost saving against current best practice.
- Cost per unit reduction of fugitive dust.
- Potential savings in the use of water.
- Ease of application onsite.
The intent was to identify representative products to decide if there was a particular type of product that would provide the best all round benefits. A key parameter was that any product used would be required to be non-hazardous to human health and the environment, and not likely to damage equipment (some salts and brines used for dust suppression can increase corrosion of steel equipment but are otherwise non-hazardous). This review process identified four products for site trials:
- Company 1 – Product 1 – Organic additive
- Company 2 – Product 2 – Water absorbing salt (Calcium Magnesium Acetate)
- Company 3 – Product 3 – Synthetic polymer
- Company 4 – Product 4 – Organic additive
The trials also included two control areas: one area without any dust suppression (neither water nor additives) used to represent a baseline; and one area which only used water as part of the normal site operations.
Products were selected based on their chemical type, their availability on the UK market at the time of the trial, their advertised water usage (e.g. if they required dilution), and their anticipated ease of use. Some research into available products had been conducted by Sublots 4 and 8, with Sublot 8 purchasing a small volume for a simple trial into ease of use. However, no monitoring data was available as to the outcomes of trial, and these products were included in trial as they were considered representative of different types of dust suppression additive. Product 4 was used in Sublot 8’s trial, and was included in this trial as it claimed to use no additional water and remained effective for up to 3 months.
The use of dust suppression additives has been referred to in some published guidance (IAQM (2016) Guidance on the assessment of dust from demolition and construction v2.2 [1], Mayor of London (2014) The control of dust and emissions during construction and demolition, Supplementary Planning Guidance, July 2014)[2], mainly linking to research on the use of calcium magnesium acetate (CMA) as a dust suppression additive for trackout on roads near construction and waste management sites (Barrett B et al (2012), Evaluation of the impact of dust suppressant application on ambient PM10 concentrations in London [3], prepared for Transport for London under contract to AECOM (URS Infrastructure & Environment Ltd.), Kings College London). This research details the different sites where CMA was used, and for this reason a CMA based product was selected as part of the trial (Alumichem’s “Dust-Away”).
Beyond the research and guidance, each product had some published marketing literature. This mainly contained some claims as to how they were used, however no other case studies or published literature was found to demonstrate a wider use of specific products.
Trial design
The site trials were completed along a stretch of haul road in Sublot 8. The haul road was divided into 200m sections with a separation of at least 50m between each section. Each section was treated with a different product. In addition to the selected products, two other sections were included to allow for comparison against common practice, one section for water and one section left untreated as a control.
For each section, two continuous particulate matter monitors were placed on either side of the haul road at approximately the midpoint of the section. This monitor placement was designed to reduce the likelihood of interference and contamination from other sections and the untreated sections in between. The dust monitors used were DustTrak II, an indicative monitor used widely across the northern section of the route for monitoring construction dust emissions from normal site activities. These monitors are MCERTs certified for monitoring PM10 (particulate matter with an aerodynamic diameter of 10 micrometres) and are routinely serviced to keep filters and inlets clean. The monitors were within calibration and QA/QC procedures as per the supplier’s instructions and best practice were implemented. An example of the monitor set up can be seen in Figure 1, showing the pair across the haul road from each other. Other monitors in the different trial areas were set up in the same configuration.
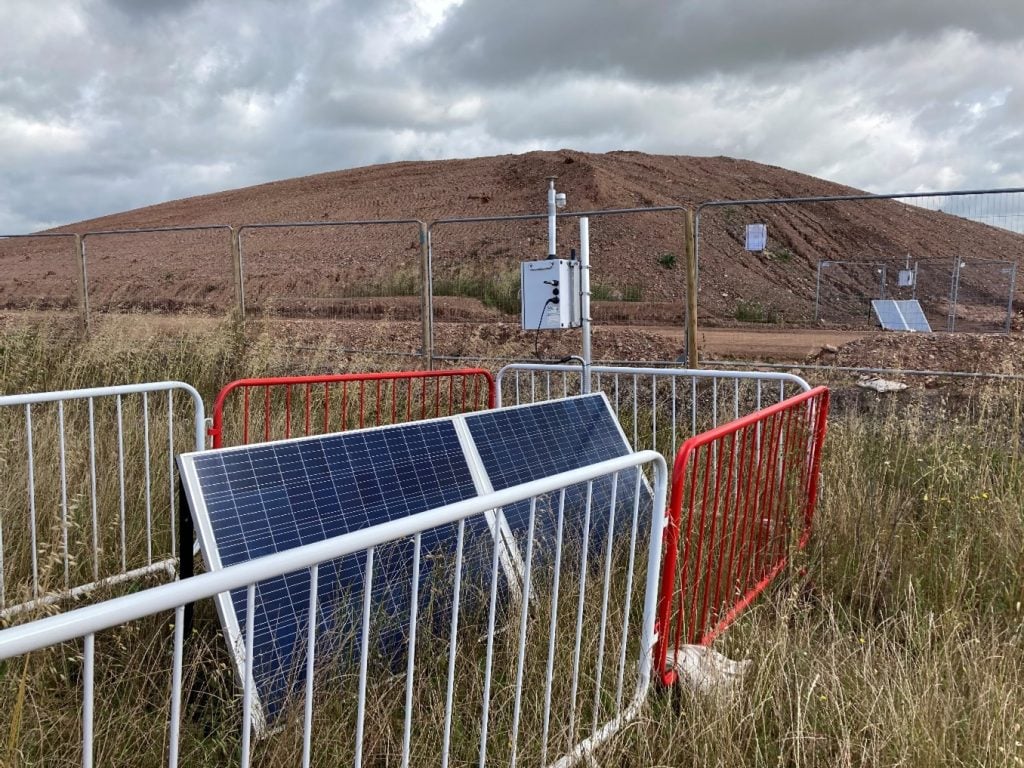
In addition to the continuous monitors, spot measurements were also taken using a handheld dust meter. The handheld meter is capable of recording concentrations of different size fractions, specified as Total Particulate Matter, PM10, PM2.5 and PM1. This was used at downwind monitor location within each trial area to determine the rate of decrease in dust concentrations with distance from the haul road, but also to determine if there was a difference in the behaviour of the different size fractions.
Product application
Prior to the commencement of the site trials, the correct quantity of each dust suppression additive product to be tested needed to be purchased. Using the suppliers’ literature for dilution and application rate, and an assumption that each trial area is of the same area (200m long by 10m wide, giving an area of 2000m2), the required volume of each product was purchased. A summary of the product application data is shown in Table 1.
Product | Application number | Proportion in water | Application rate (L/m2) | Total volume (L) | Volume water required (L) | Volume of product required (L) |
---|---|---|---|---|---|---|
Product 1 | 1 | 33% | 1.5 | 3000 | 2000 | 1000 |
Product 2 | 1 | – | 0.4 | 800 | -* | 800 |
Product 3 | 1 | 15% | 2 | 4000 | 3400 | 600 |
2 | 10% | 2 | 4000 | 3600 | 400 | |
Product 4 | 1 | – | 1 | 2000 | – | 2000 |
* Product 2 required water to be used 10 days after initial application during dry conditions. It was assumed that this would require a similar amount of water as that used for existing dust suppression.
The monitors were initially deployed on 12th June 2023, to capture a baseline prior to the application of dust suppression additives. During this period, the intention was that no dust suppression (either water or additives) would be used, to allow a comparison during the trials. Through discussions with the dust suppression additive suppliers, it was determined that a period of 3 days of dry weather would be needed to allow application of the dust suppression additives and to allow them to dry. The weather did lead to a delay of 3 months before the trials could begin, and on 7th September 2023, the dust suppression additives were applied over two days.
The application process used equipment that is currently available on the sublot construction sites. Two tractors and 9000L water bowsers were sourced from the sublot, including operators and safety personnel to enable safe working on the haul road. The dust suppression additives were pumped into the bowser and mixed with water as required. The contents of the bowser were applied to the 200m trial area designated for the dust suppression additive in use, ensuring an appropriate amount was applied.
The figures below were taken during the application process and show the methods and coverage of the dust suppression additives. Water would also show a similar pattern of coverage.
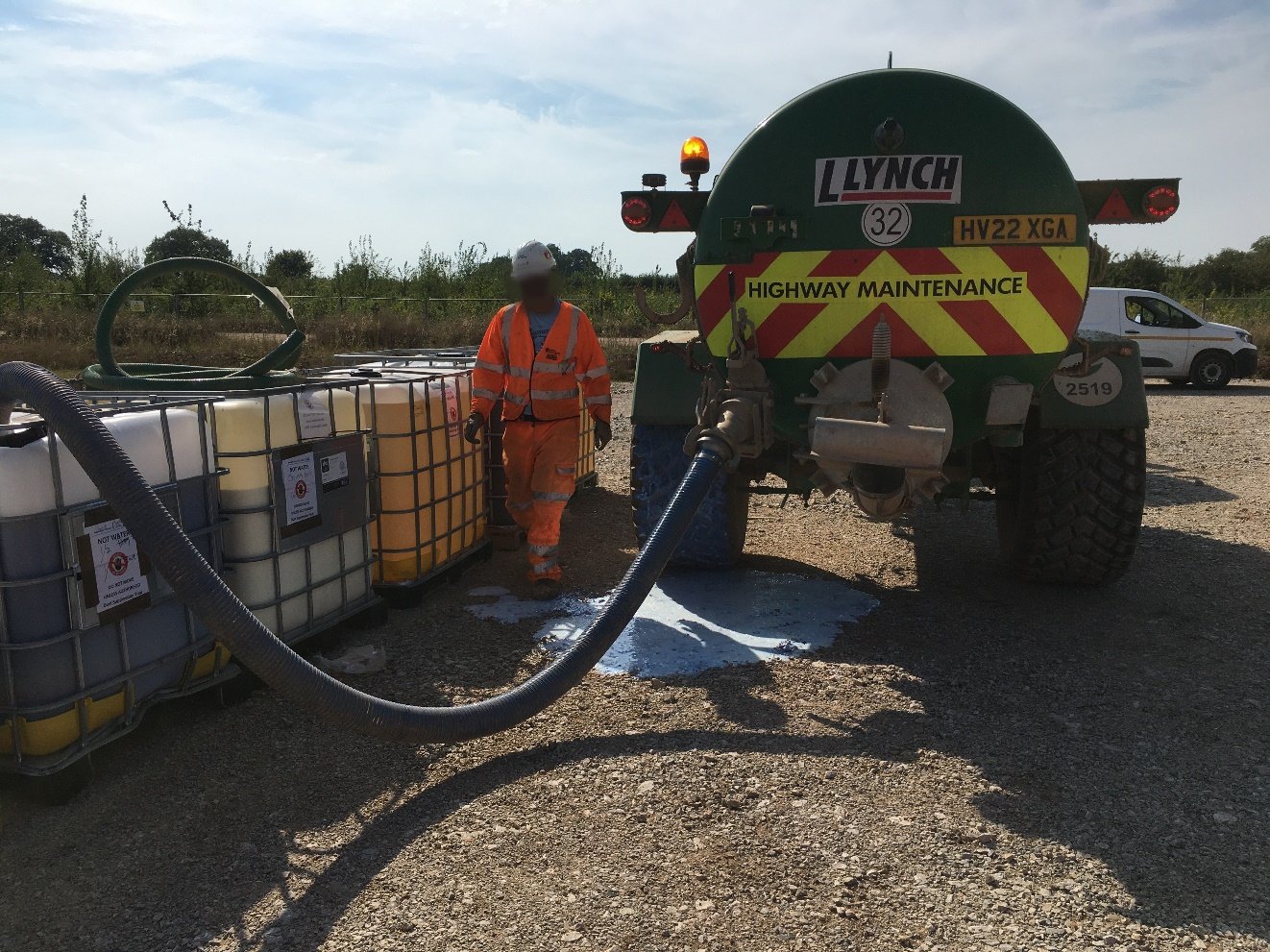
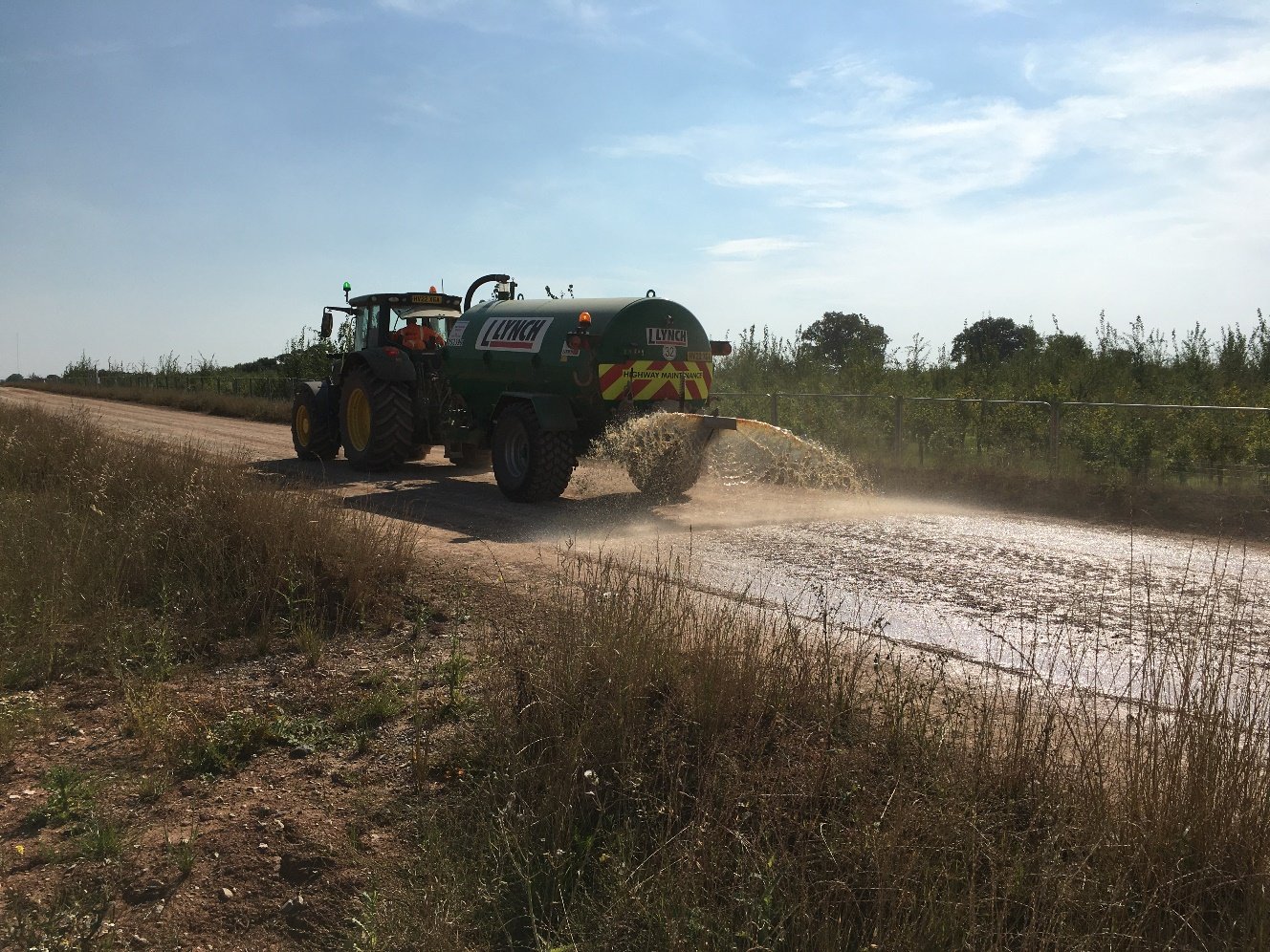
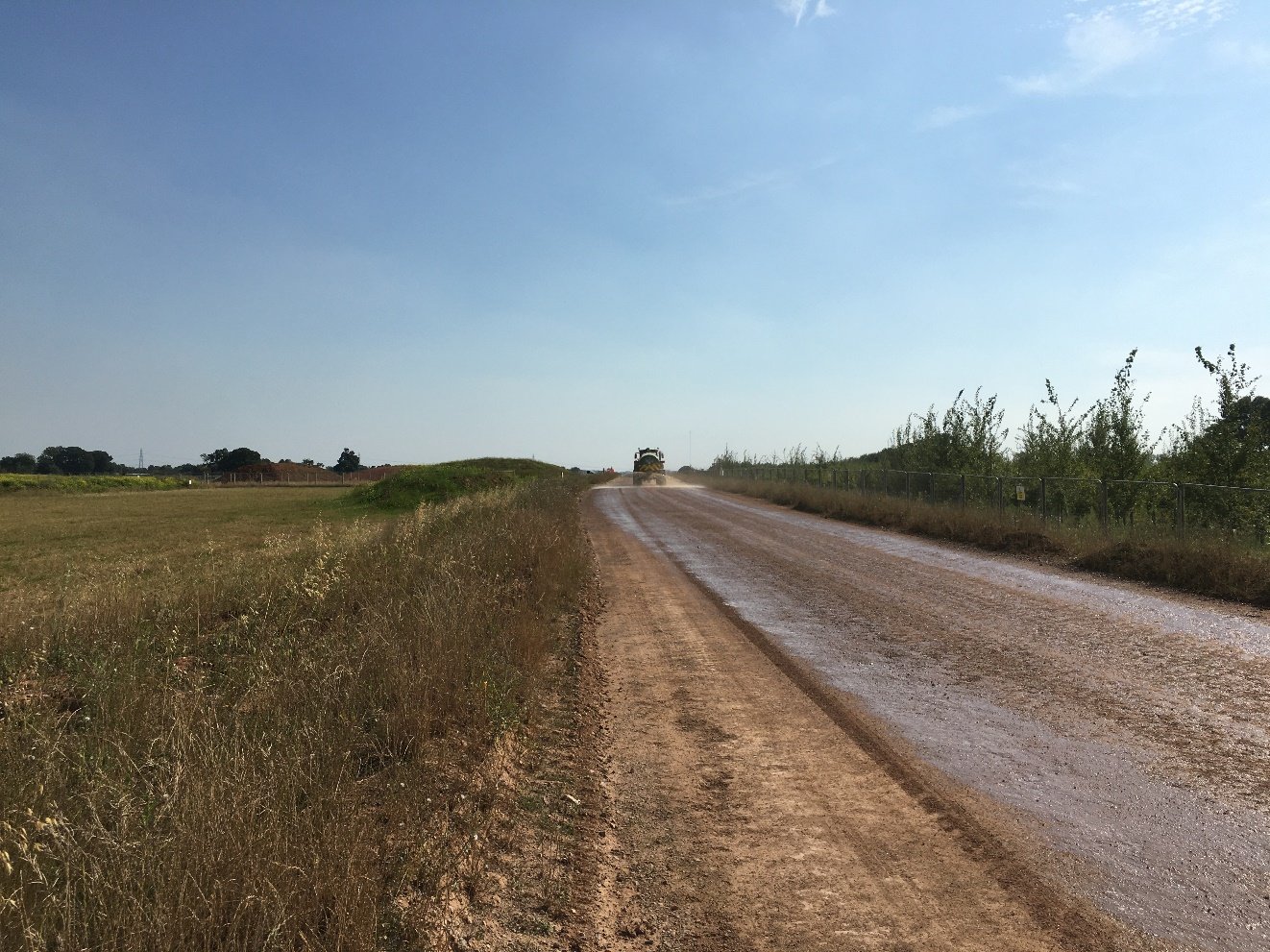
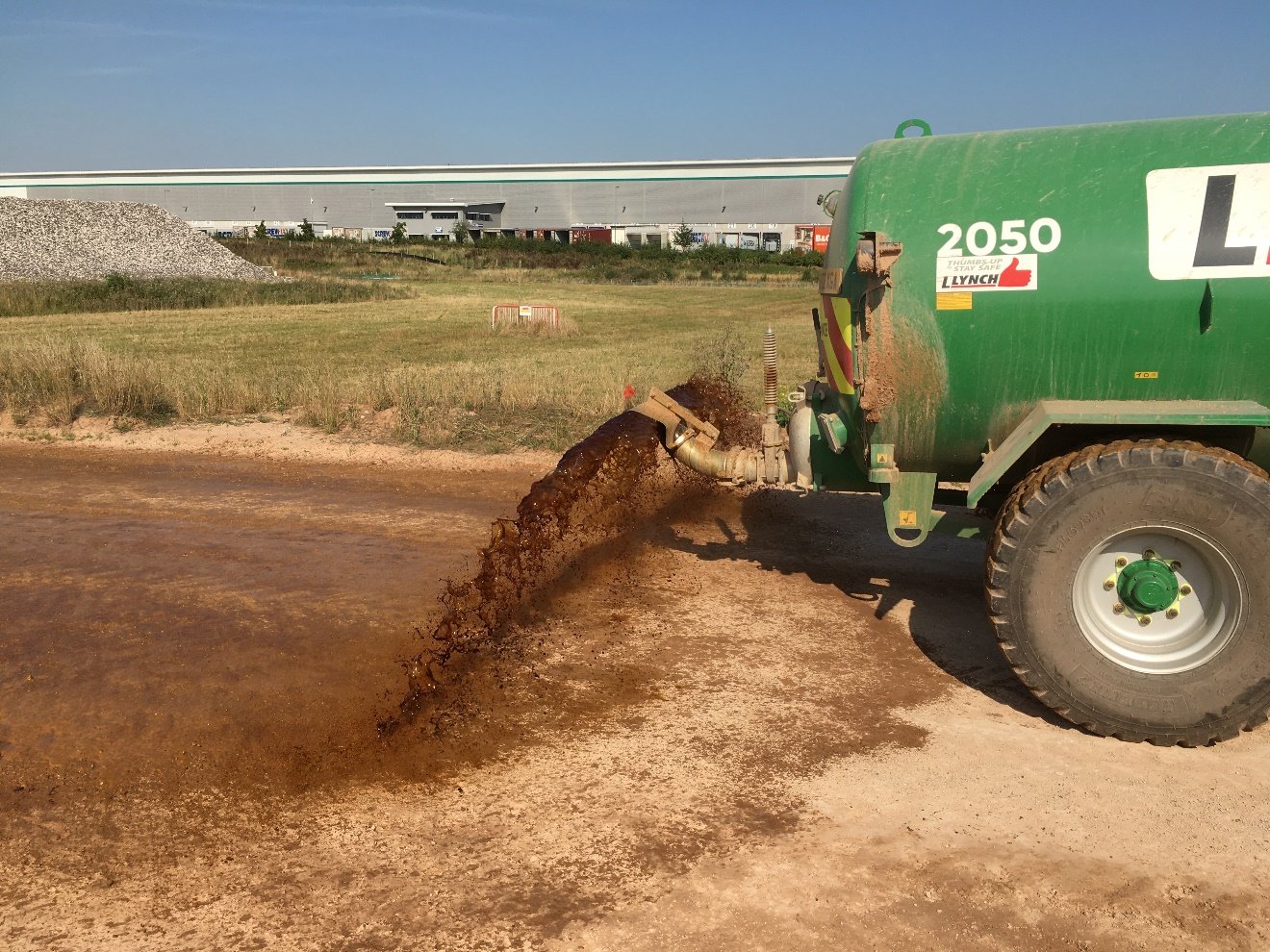
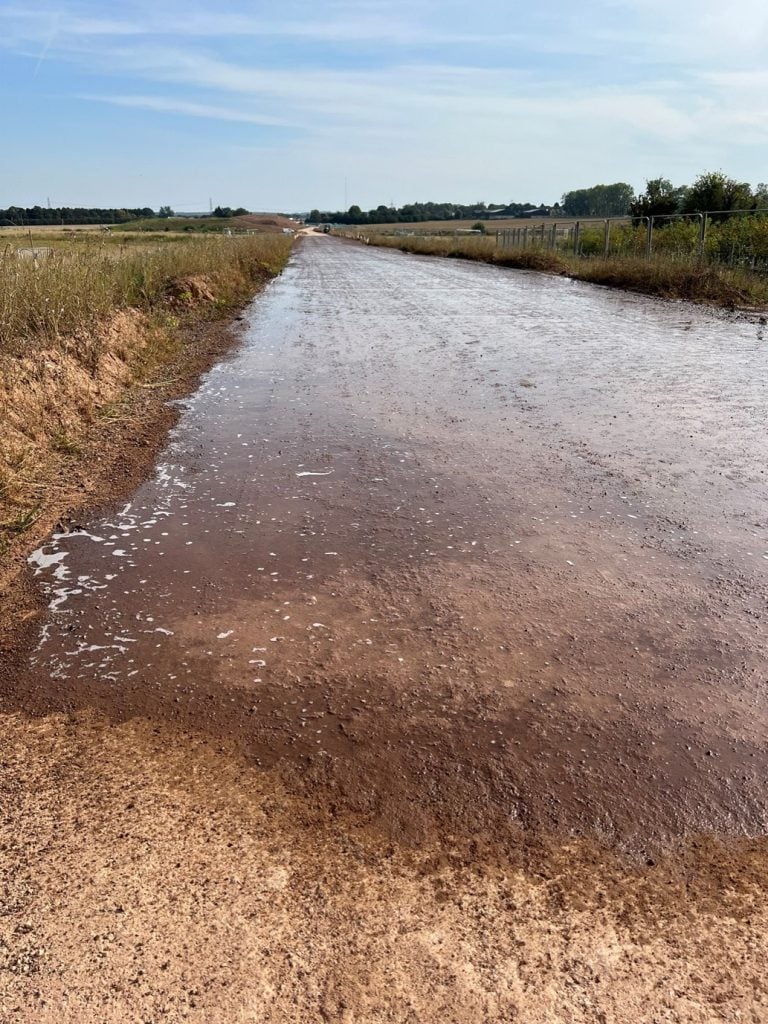
Following application of the dust suppression additives, each area was allowed to dry without traffic for a minimum of 24 hours, before allowing normal operation of the site.
Spot measurements were undertaken using the handheld meter once a week for 4 weeks after application.
Outcomes
Limitations and uncertainty
During and following the trials, the following observations of likely limitations and uncertainty in the use of dust suppression additives were made:
- The bowsers total liquid capacity was determined to be approximately 9300L and fitted with a visual gauge to determine liquid level in the tank. The gauge did not have any markings to represent volume of liquid in the tank, nor was there any equipment available to accurately measure liquid into the tank. Products which required mixing with water were therefore only approximately dilute, which is considered a realistic scenario for how product would be applied on a construction site.
- The available bowsers are not fitted with any accurate flow rate control, and was dependent on how wide open the valve was set and the speed of the tractor during application. There was therefore no accurate control over application rate during the trial. To overcome this, the bowser was only filled with sufficient additive and water (if required) to cover the trial area, and the bowser completed multiple passes until the bowser was empty. This ensured the correct application rate was applied, although during general use the number of runs with a full bowser will need to be determined.
- During application, it was noted that the spray from the bowser wasn’t quite sufficient to cover the haul road running surface evenly in a single pass. To compensate for this, multiple passes were done down each side to ensure adequate coverage.
Results
The use of dust suppression additives demonstrated a consistent reduction in concentrations of PM10 recorded at the continuous monitors, with a reduction in peak concentrations and frequency when compared to the baseline period before dust suppression additives were applied.
Peak concentrations decreased by up to 88% for most products including water, indicating that all dust suppression methods were capable of reducing fugitive dust emissions by similar degrees. The frequency of concentrations over the Site Action Level of 190 µg/m3 also decreased consistently for all dust suppression methods. Before application of the dust suppression there were 13 periods when the 1 hour mean concentration of PM10 exceeded 190 µg/m3, while after application there was only 1 period where this occurred. No single additive, or water, stood out as providing a greater benefit in reducing fugitive dust emissions.
An example chart showing the 1-hour mean PM10 concentrations for one of the dust suppression additives is shown in Figure 7. The dark blue section shows the period before application of the additives, and the pink section the period after. The chart clearly shows a reduction in the number of peak events. A similar pattern was recorded at all trial locations, with the exception of the control area (no dust suppression in use), where peak concentrations were noted to be higher.
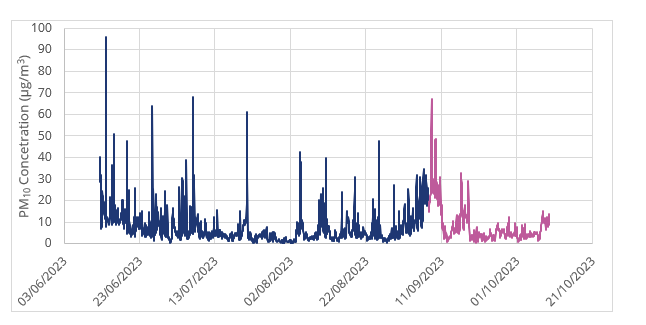
From a review of the monitoring data and available weather data, there was some indication that dust suppression additives did result in a slight decrease in longer term average concentrations (e.g. daily or monthly), but this reduction was slight.
At the start of the trial period, June and July were relatively wet and cool with average temperatures of 18°C in June and 16°C in July and August. July also saw relatively high rates of precipitation, which remain regular through July and August. At the start of the product application on the 7th September, the temperature did increase and there was a decrease in the rate of precipitation. Wind speeds consistently averaged at about 1m/s, but did show a slight increase during the periods of wet weather. Following application of the products, winds speeds did peak at approximately 3.4m/s during the dry period, and at 6m/s towards the end of September and start of October. There were no periods of high wind speed and dry weather during the trial period.
The weather remained relatively dry for the first two weeks of September, and allowed a comparison of all the products in the same environment. As wetter weather arrived in mid- to late September, it also allowed a comparison of the longevity of the products following periods of wet weather and increased surface water.
The data from the handheld meter during the spot measurements indicated that there was a change in the size fraction composition of the dust when dust suppression was use, regardless of the method. At roadside locations, smaller size fractions made up a greater proportion of the measured dust concentrations compared to the control using no dust suppression and pre-application results, indicating that larger size fractions were not becoming airborne as readily as smaller size fractions. The change in proportions of each size fraction was less pronounced with distance from the road side, as larger size fractions tend to drop out of the air sooner, and therefore have less of an impact at locations further away.
The next stage was to consider the potential costs and water usage for each method. A summary of the supplied costs and potential savings based on provision of the products at the supplied cost are shown in Table 2 to Table 4. A full breakdown of the assumptions made to support these calculations are given in the support material.
* Price of water based on 9000L bowser for £850, assumed same price for application and dilution of products
** Includes cost of water application 10 days after initial application
† water application based on 4 applications per day for an average of 148 dry days per year
Product | Cost/km/year | Annual equipment and labour costs | Total annual cost* | Total Potential Saving vs. water |
---|---|---|---|---|
Product 1 | £95,666.67 | £7,380.00 | £1,442,380.00 | -£724,106.67 |
Product 2 | £94,416.67 | £18,819.00 | £1,435,069.00 | -£731,417.67 |
Product 3 | £114,333.33 | £7,380.00 | £1,722,380.00 | -£444,106.67 |
Product 4 | £63,980.77 | £2,460.00 | £962,171.54 | -£1,204,315.13 |
Water | £139,777.78 | £69,820.00 | £2,166,486.67 | – |
* Based on an indicative haul road length of 15km
Product | Total annual cost* | Total Potential Saving vs. water* | Maximum reduction in peak concentrations | Price per microgram reduction in peak concentrations |
---|---|---|---|---|
Product 1 | £1,442,380.00 | -£724,106.67 | 86% | £3,308.39 |
Product 2 | £1,435,069.00 | -£731,417.67 | 87% | £3,283.75 |
Product 3 | £1,722,380.00 | -£444,106.67 | 86% | £3,984.46 |
Product 4 | £962,171.54 | -£1,204,315.13 | 79% | £2,425.21 |
Water | £2,166,486.67 | – | 88% | £4,899.21 |
* Based on an indicative haul road length of 15km
The information presented in the tables above demonstrate that there is a potential cost saving with the use of dust suppression additives when compared to the use of water only, with savings of up to £1,200,000 per year for a 15km section of haul road based on the use of Product 4. This represents a potential maximum in ideal circumstances, and the use of other dust suppression additives are likely to have smaller potential savings. For large sites or sites where water is a limited resource (i.e. where water needs to be bought in in tankers, abstraction from surface water or aquafers is limited, or where there is insufficient space for storage ponds), then the use of dust suppression additives can help conserve water, and savings can be made. However, for some construction sites, water is less limited and is more freely available, and such cost savings as summarised in Table 2 to Table 4 may not be realised.
While not examined in detail in the trials, there are other environmental benefits associated with the use of dust suppression additives, such as:
- A reduced demand on water resources, particularly where there are multiple users of the same source (e.g. farming, industry).
- Reduced pressure on ecological sites (e.g. streams, ponds and wetlands).
- Reduction in the number of vehicle movements on local roads (e.g. from water deliveries) and on haul roads, and lower emissions.
- Less runoff of water and haul road surface material into the local environment (e.g. streams and ponds).
- With less runoff, there is likely to be a slight decrease in the deterioration of the haul road.
These benefits are less straightforward to quantify; however, they highlight wider sustainability issues facing the construction industry. In instances where there is limited cost benefit, then other sustainability issues may justify the use of dust suppression additives.
Learnings and recommendations
The use of dust suppression additives can be beneficial for sublots as a means to reduce water use, costs and labour time for dust suppression on haul roads.
Where a sublot is required to purchase water solely for dust suppression, then there is a predicted cost benefit to reduce the amount of water purchased by the use of dust suppression additives. On sublots where there is no cost for water, then any cost benefit may be marginal. The use of dust suppression additives needs to be considered on a site by site basis, to ensure the most appropriate method is used and cost savings can be realised.
The cost savings noted above are dependent on the possibility of any savings in operational costs, not solely procurement costs for water. For current dust suppression, the equipment is hired for a prolonged period of time, as the use of water for dust suppression requires near constant application, up to 4 times per day every day the site is in operation. With the use of dust suppression additives, application frequency is between once per month to once every 3 months. The scale of cost reduction is only possible where the equipment and operative can either be used for other construction activities or are not on hire when they are not in use.
The use of dust suppression is highly dependent on the weather conditions, and the costs associated with it are also highly variable. As an example, 2023 saw a relatively cool, wet summer compared to 2022. While there were periods of dry weather, the trials were delayed for approximately 6 weeks as there were no periods of dry weather considered appropriate to allow site teams to apply the dust suppression additives. Dust suppression additives typically require a period of time to dry, up to 24 hours, although this can be shorter in warm weather. During this time, the haul road shouldn’t be used or get too wet (e.g. rain), which can present a limitation on site work if a haul road needs to be shut for a day. While appropriate scheduling can go some way to ensure this isn’t an issue, plans may be forced to change if the weather is different to what is forecast. The use of water for dust suppression is flexible and can be applied quickly and at short notice without any restrictions in construction activities, while dust suppression additives require some degree of planning in advance, although once dry they are less susceptible to being washed out and don’t need to be applied after every rainfall (in fact, Product 2 works by retaining moisture in the haul road surface, and some wet weather can help prolong the period it is effective for).
Conclusion
Dust suppression additives do have a benefit in the reduction of fugitive dust generation from unsealed haul roads on construction sites, when compared to no dust suppression. The use of dust suppression additives is as effective as the use of water, but using water on its own can represent a significant cost to sublots, and dust suppression additives can offset this in the correct conditions.
Before purchasing or using dust suppression additives, sublot managers should consider the following points:
- Can the cost of dust suppression additives be offset by a reduction in the amount of water purchased, a reduction in equipment hire costs and/or a reduction in labour for application?
- Which areas of the site require dust suppression? Are there haul roads / uncovered ground / stockpiles in a position such that they represent a risk to sensitive receptors? What is the total area that requires dust suppression?
- Are there other issues which should be considered besides cost (e.g. potential impacts on water environments due to abstraction/runoff)?
- What is the weather forecast? How long is dust suppression required?
Acknowledgements
The dust suppression additives review was commissioned by Sam Williams, BBV Noise, Vibration and Air Quality Lead, who also provided practical guidance and management support to allow the trials to go ahead. Sam also undertook a technical review of the final report.
Special thanks to Christy Ho, BBV Noise and Vibration Specialist, who helped organise the site trials at Sublot 8 and the purchase of additives from suppliers. Christy also provided guidance and technical review of the final report.
The AECOM team who supported the trials through reporting, site work and technical review are:
Gareth Collins – Team Lead, Air Quality, Quality Management
Garry Gray – Technical Director, Air Quality, Technical review
Elisa Uginet – Air Quality Consultant
Liam McGurk – Air Quality Consultant
Ellis Langdon – Graduate Air Quality Consultant
Amy Foulds – Graduate Air Quality Consultant
References
- IAQM (2016) Guidance on the assessment of dust from demolition and construction v2.2
- Mayor of London (2014) The control of dust and emissions during construction and demolition, Supplementary Planning Guidance, July 2014).
- Barratt, B., Carslaw, D., Fuller, G., Green, D., & Tremper, A. (2012). Evaluation of the impact of dust suppressant application on ambient PM10 concentrations along ‘hot spot’ highway corridors. Kings College London, University of London.
All references for during the dust suppression additives review and trial are set out in the supporting material.
Supporting materials
This submission is supported by the following document:
1MC08-BBV_AEC-EV-REP-N000-000026 – Water Additive Dust Suppression Study – Site Trial Results and discussion Report