Engineering for archaeology during major infrastructure programmes
Archaeological activities are often the first piece of work carried out under the auspices of a Principal Contractor. However, they are not always afforded the same scrutiny when it comes to risk reduction and innovation. This short paper seeks to address this by identifying ways in which archaeological works can set the tone for safety and innovation at the very first stage of on-site activities. It outlines key considerations and the engineering processes that can be employed to increase efficiency and safety.
Background and industry context
Planning the biggest dig
This paper is presented as part of the works to deliver the Enabling Works Contract (EWC) on the southern section of High Speed Two (HS2) phase one which includes demolition of buildings within the wider Euston area, utility diversions, environmental and ecological monitoring and a programme of historic environment and archaeological activities, delivered by the Costain Skanska joint venture (CSjv).
The site of St James’s Gardens is unique in both scope and scale and has presented the ideal opportunity to integrate the disciplines of archaeology and engineering, to deliver a project of unparalleled size and academic significance. Application of engineered design, resource loaded planning, and LEAN and ergonomic processes have been vital to eliminating risks. Taking a “safe by design” approach[1], all possible avenues of innovation were explored to design out all major safety and occupational health risks.
Temporary works and encapsulating the site
The first area of focus was the construction of the tent or encapsulation structure which was erected over the worksite in order to comply with Schedule 20 of the High Speed Rail Act 2017[2] and protect the archaeology from adverse weather conditions, as well as to maximise safety and productivity. Measuring 90m by 110m, this Systems Scaffold structure enclosed the works from public view and provided supporting functions such as elevated platforms for high-level photography and maintenance and integrated charging points for the 25 pieces of electric plant deployed within the structure.
It was determined that the foundations of the structure needed to be situated below the level of the burial horizon to prevent any undermining of the structure during the archaeological excavation. 15 vertical shafts were excavated in a grid arrangement across the burial ground to a depth of 6.2m below existing ground level (Figure 1). This served two key functions. Firstly, this enabled provision of low-level foundations upon which to situate the steel support towers. Secondly, the works provided a very specific window into the burial ground, allowing the archaeological team to evaluate the preservation, population density and material culture present within the burial ground.

The structure was supported on 15 prefabricated hot rolled steel towers which were fabricated off site (Figure 2). These were transported to central London, lowered into the shafts and fixed in two sections to achieve the required height (height being determined by the reach of the largest piece of plant required to support the archaeological works, thus eliminating the risk of plant striking the roof structure). Original design optioneering had included standard scaffold components as well as exploring the use of Slimshor and Megashor (off-the-shelf structural support systems) to construct the towers on site. However, it was recognised that this would require a higher than desirable number of person hours to work at height and within confined spaces. Furthermore, use of these systems also presented additional manual handling and occupational health risks. By introducing the prefabricated steel towers, over 5000 person hours of work at height and 5000 person hours of confined space working were removed from the process of erecting the towers. This saving is based on the number of person hours that would have been needed to erect equivalent tower using traditional tube and fitting scaffolding.
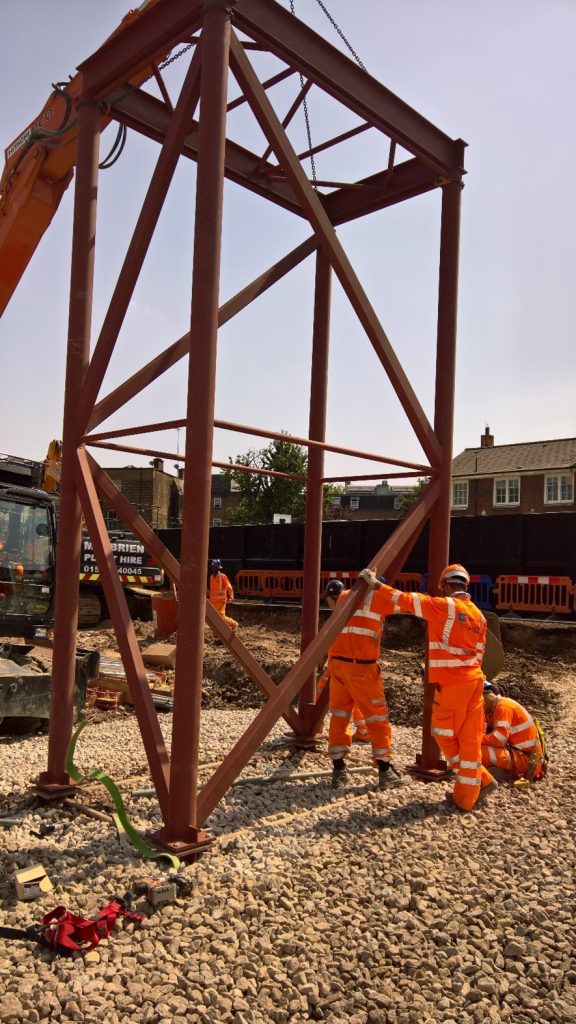
The roof structure was erected using a bird cage scaffold and an elevated scaffold working platform to hugely reduce work at height risk, with roof sections placed on nylon rollers and manually winched into place to remove the requirement for a crane on site (Figure 3).
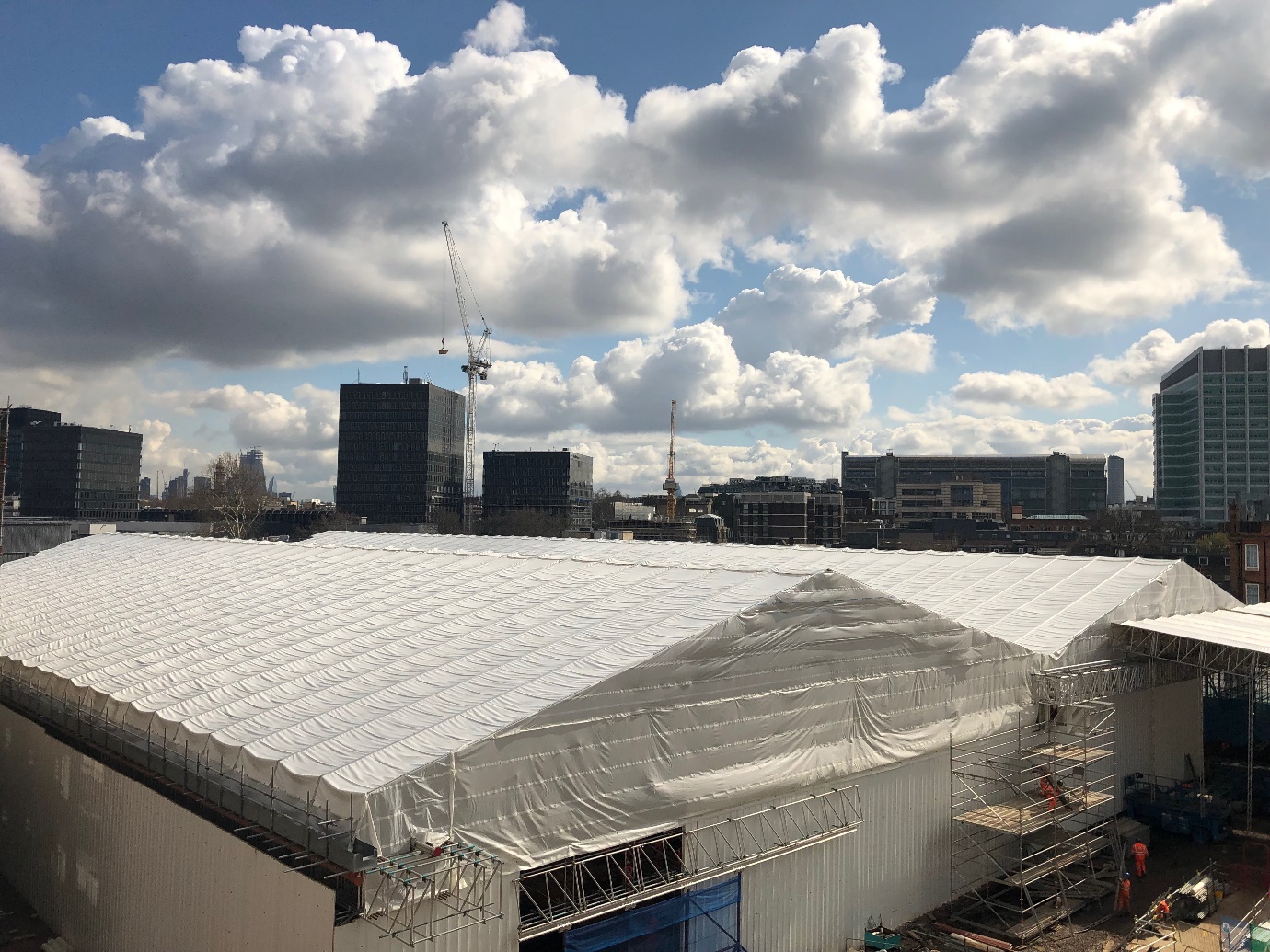
The structure was designed with an integrated rolling maintenance and viewing platform in each side of the roof canopy, which further reduced work at height risk during the 10-month use-life of the structure and ensured that maintenance could be carried out without the need to bring in plant such as scissor lifts. These would have had a negative impact on any exposed archaeology (Figure 4).
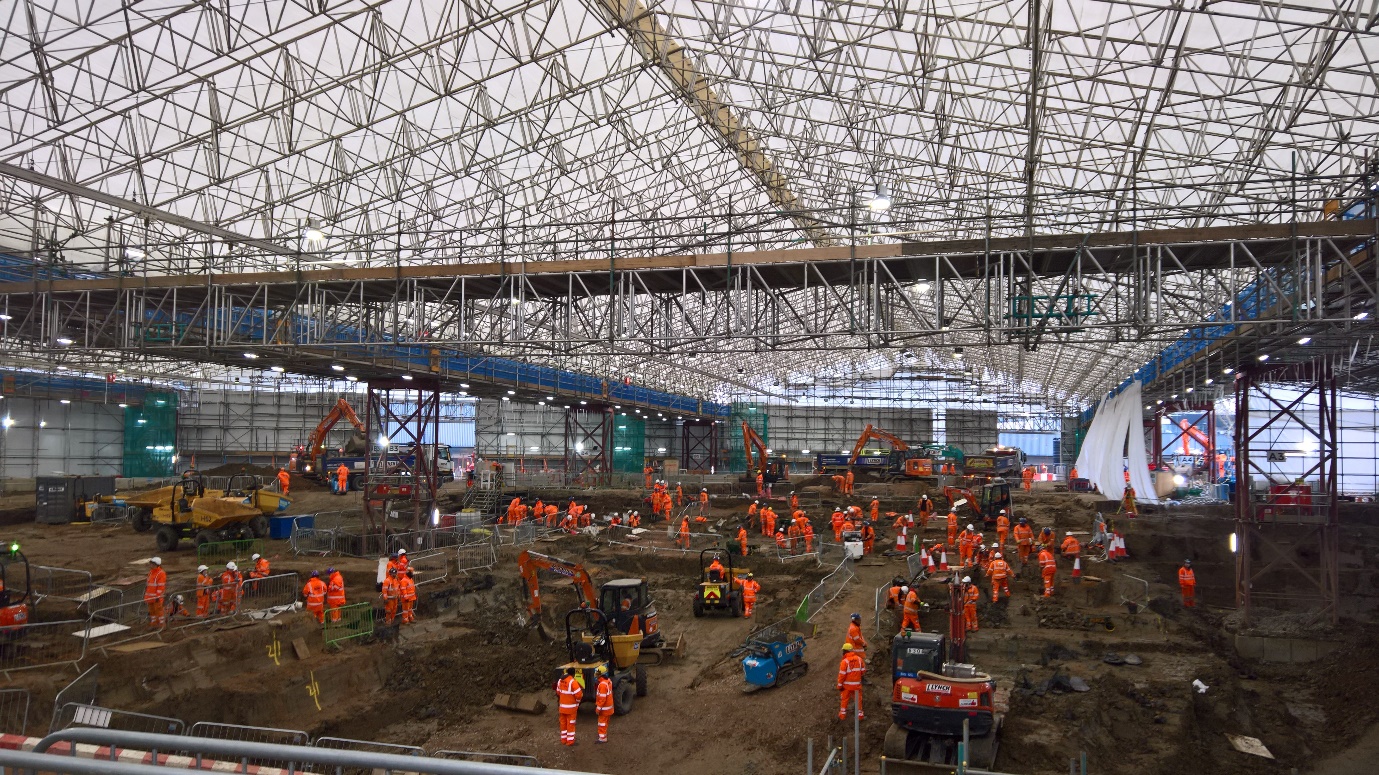
Lessons learned and successes
Full encapsulation of the site from the outset maximised the opportunity to deploy a larger archaeological team and enhanced the research and public benefit potential of the archaeology.
It also reduced the need to implement site stand downs while adjustments were made to the structure, and minimised time spent working in confined spaces by affording a safe and open working area for the archaeological team.
The design of the towers was key to reducing manual handling as well as person hours working at height and within each individual vertical shaft. The bird cage scaffold hugely reduced work at height risk during the assembly of the spine beam (three central supports) and also the assembly and placement of the roof section.
Workplace design enhanced mental health and wellbeing and increased the overall productivity of the team by a factor of five measured against an archaeological baseline of one archaeological specialist being able to excavate 1m3 per person per day. The final project outcomes and volumetric data demonstrated that at the peak of works, 5m3 per person per day was achieved.
Recommendations
Do not assume that archaeological works are less complex than any other construction related activity planned. Ensure that the needs of specialist functions such as archaeologists are investigated and understood before the design of works with a historic environment interface is embarked upon.
Archaeological excavations within complex urban areas can often have a larger number of interfaces and risks then may appear at the outset. Strategic planning and risk assessment as well as reviewing the need for temporary works is key to setting the scene for success.
The duration of an archaeological programme should also be taken into consideration where large or open excavations may need to be managed for prolonged periods.
Larger scale projects with major third-party interfaces are better managed through engineering processes in order to safeguard the requirements of stakeholders (e.g., Network Rail design approval forms and letters of no objection for statutory utilities companies), who may have assets impacted by or located next to archaeological works.
Archaeological contractors are not best placed to deal with these constraints and design requirements as they do not possess the specialist engineering knowledge, and because archaeology as a discipline does not sit within Construction Design Management (CDM) Regulations 2015.
Acknowledgements
Works designed and managed by Costain Skanska joint venture with Costain In-House Engineering, Palmers Scaffolding Ltd, RDG, Wingate Electrical Plc, MOLA Headland Infrastructure, TCS Exhumations, LLynch Plant Hire and Haulage Ltd and M O’Brien Plant Hire.
References
[1] Raynor, C. Safe by Design. Institute of Occupational Safety and Health. [internet]. 2019 Aug [cited 2021 Sept 16].
[2] High Speed Rail (London – West Midlands) Act 2017, Schedule 20: Burial grounds. [internet]. 2017 [cited 2021 Sept 16].