Fully digital and paper-free office
The Euston Power Signal Box (PSB) office utilised an integrated digital system, enabling all site activities to operate under a paperless system with full engagement from the key supply chain partners. The digital system has replaced all paper documentation, improving efficiency, quality and environmental credentials.
The PSB digital office has set a new standard for documentation and delivery, and the team learnt crucial lessons along the journey. This report will be of interest to delivery teams who are looking to accelerate the digital transformation on projects. Key learning points can be taken from the selection of accessible technology and the behavioural changes required to complete the transition.
Background and industry context
Construction projects require daily communication of written health and safety information and a clear audit trail of receipt. Typically, the business-as-usual approach for construction sites includes paper copies of briefings, permits, inspections and designs. The production of the paper copies can be time consuming and costly, and errors often occur from implementing outdated documentation. The median cost for re-work in the US construction industry due to poor document control is estimated at $4.2 billion a year.1 The problem is also prevalent in the UK.
Approach
The Enabling Works Contract (EWC) on the southern section of High Speed Two (HS2) phase one includes demolition of buildings within the wider Euston area, utility diversions, environmental and ecological monitoring and a programme of historic environment and archaeological activities and is delivered by the Costain Skanska joint venture (CSjv).
The Euston PSB demolition team approached the project planning with digital technology in mind. The aim at the PSB site and office was to build upon existing technology, implemented within CSjv, to create a completely paperless work environment.
Technology Changes
The following technology changes were implemented:
1) Rolling Screens
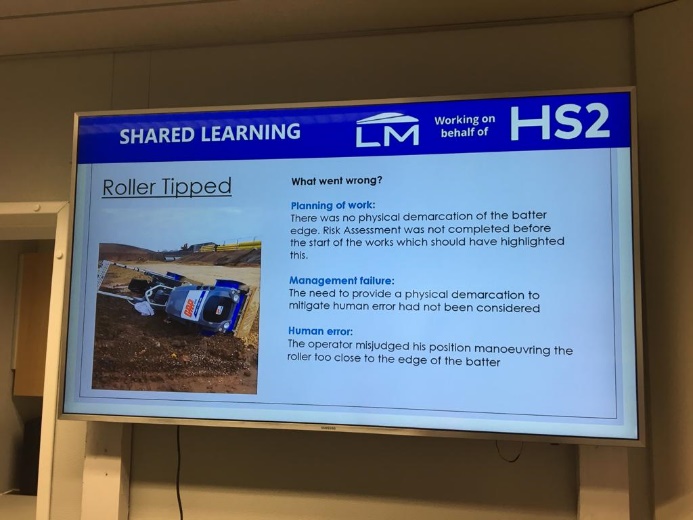
Rolling TV screens provided the latest information within the office and welfare. The screens were updated every two weeks and featured the following:
• Safety updates
• Observations – ‘you said, we did’
• Achievements and progress photos
2) Interactive touch screens to view drawings and files
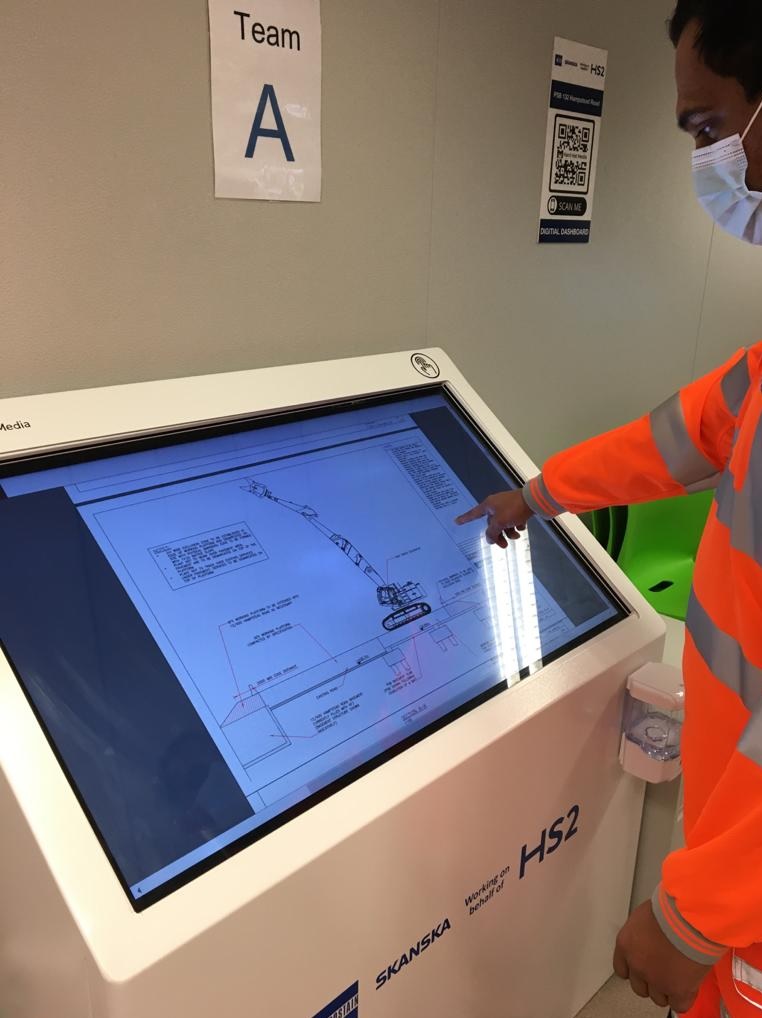
Interactive touch screens within the office provided space to view drawings and files. The screens were linked to shared online resources, enabling the latest information to be viewed.
The site anemometer provided real-time weather and wind statistics to the screens.
3) AppCan application on iPads
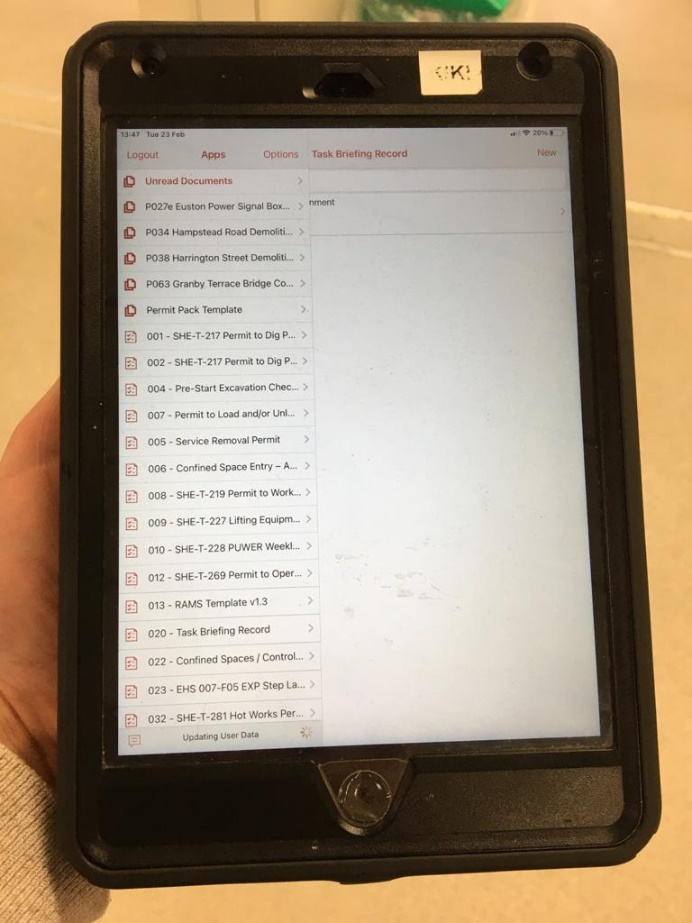
iPads provided Engineers, Site Managers and Supervisors with the latest delivery documentation. Approvals were completed remotely on the web browser version.
AppCan software was used on the iPads. AppCan is a field data collection application with the ability to create custom applications or forms. All site operatives could sign a receipt of briefing using AppCan, providing a robust evidence trail.
Each iPad was connected to a 4G network, removing the reliance on Wi-Fi connectivity.
Daily Diaries and Targeted Risk Monitoring Inspections were completed using the BIM360 Field App.
4) CSjv application on mobile phones

The CSjv app enabled all staff to report and submit observations on site.
Site staff were encouraged to provide feedback with photos using the app.
QR codes with plant inspection forms were attached to all machinery, enabling operators to submit check sheets at the point of work.
Microsoft Forms were used to record site inspections, such as daily excavation checklists.
Outcomes and Learning
Key benefits
The digital system enabled change to be efficiently managed and communicated to the site team. As designs progressed, numerous versions of the same drawing were produced, which could typically lead to version errors on site. However, managing the works information on a digital platform ensured that only the latest documentation was available.
The digital platform provided a robust audit trail of inspections and briefings, with no requirement to archive documentation at the end of the project. All temporary works inspections were captured using AppCan software, enabling photos to be taken and automatically uploaded at the point of work.
All required documentation was available at the point of work, improving efficiency and safety on site. This included utility information, method statements and permits. The paperless office and site also reduced physical resources, as no printers, paper or ink were required. The savings are presented in the table below:
Table 1 – Paperless Savings, over 12-month project period at the Euston PSB2
Volume Reduction | Cost Saving (£) | Carbon Saving (kg) | |
---|---|---|---|
Paper (A4 pages) |
26,000 |
624 |
124 |
Ink (Cartridges) |
26 |
2080 |
52 |
Printers |
2 |
4160 |
26 |
|
Total |
6864 |
202 |
Barriers to implementation
The change to a fully digital system can be daunting for staff who have spent their career working from paper documentation. 32% of employees and 28% of managers in the construction industry are still reluctant to adopt technology.3 The change requires training and encouragement for all to adopt a new way of working. Changing behaviour of the site team was the greatest challenge during the digital transition at the Euston PSB project. A Digital Champion was assigned within both the CSjv and subcontractor site teams, providing a role model for the use of digital technology and a source of knowledge to support the paperless transition.
The technology must meet the requirements of the project. Flexible software can be used where users programme the necessary formats; however, this requires training a dedicated member of the team.
Reliable internet connections are crucial; however, a cellular network connection (4G/5G) can overcome Wi-fi connection issues.
Recommendations
Small step changes should be undertaken during the digital transformation, rather than attempting to change all systems at once. By targeting key documentation, such as method statements and permits, the paperless way of working can slowly take place without causing disruption to site activities, and confidence can start to develop within the site team.
The technology selected must be accessible to all and training should be carried out from the start of the transformation. Digital champions can be effective at promoting the new systems, especially if they are leaders within the site team. All staff must buy-into the new way of working for it to be a success.
The paperless way of working should be audited on a regular basis. Achieving the last 5% of the digital transformation can be challenging, so identifying the weaker areas sooner and developing an action plan can improve the transition to fully digital.
Conclusion
Paperless delivery on a construction project can improve efficiency, reduce version errors and improve audit reliability, whilst also benefitting environmental sustainability. Within the PSB project, no version errors or defects occurred, eliminating the need for re-work, and the digital system received positive support from all supply chain partners involved. The behavioural and technological challenges must be overcome to fully integrate a paperless way of working. Accessible technology selection, small step changes and training, promoted by digital champions, can lead to a successful digital transformation.
References
- Hwuang B-G et al. Measuring the Impact of Rework on Construction Cost Performance. Journal of Construction Engineering and Management [internet]. 2009 [cited 2021 Sept]; 135(3): 187-198.
- UWE Student Union. Negative Environmental Impact. 2019 Apr.
- Horman MJ, Kenley R. Quantifying Levels of Wasted Time in Construction with Meta-Analysis. Journal of Construction Engineering and Management [internet]. 2005 [cited 2021 Sept; 131(1): 52-61.