Innovative Logistics: Construction Consolidation Centre – HS2 C1 ALIGN
This paper focusses on the Main Works Civils Contract (MWCC) for the central section of High Speed Two (HS2) Phase One which includes the Colne Valley Viaduct and Chiltern Tunnels, being delivered by the ALIGN Integrated Project Team (ALIGN).
The paper summarises the established benefits and lessons learned from the implementation of an in-house Construction Consolidation Centre (CCC) operated by ALIGN at the Chiltern Tunnel South Portal compound.
The ALIGN CCC generated a number of benefits, including a reduction of around 500 vehicles per month to ALIGN satellite compounds, improved space utilisation on site, and the facilitation of several cost saving initiatives.
The paper is aimed at construction, logistics and procurement professionals, and anyone interested in novel ways of improving the flow of equipment to construction sites.
Background and industry context
Construction logistics as a discipline aims to improve site safety, reduce work-related road risk, maximise efficiency of the construction process, reduce costs, and minimise the social and environmental impacts of a construction project. One technique employed by construction logistics professionals to achieve these goals is the use CCCs. These facilities consist of warehousing space and/or outdoor laydown areas where deliveries can be received directly from suppliers before being delivered to the construction site in consolidated loads – thus reducing the number of vehicles attending the construction site.
An academic literature review was undertaken and the benefits of CCCs established in the literature included a reduction in vehicles travelling to the construction sites[1]; improved productivity of site labour[2], as well as increased space utilisation on site and social benefits from more efficient and less intrusive transport operations within urban areas[3].
A review of the academic literature showed that although CCCs have been used by previous construction projects both in the UK and abroad these were predominantly multi-user facilities situated away from the construction site[4]. No examples were found in the literature of CCCs implemented by a single contractor and situated on one of their construction sites.
The C1 section of HS2 is being constructed by ALIGN – a joint venture of Bouygues TP, Sir Robert McAlpine, and Volker Fitzpatrick. The C1 section of HS2 is 21.6km in length and can divided into three distinct sections; a large central compound called the South Portal, with direct access onto the M25; six satellite compounds to the north enabling construction of ventilation and access shafts for the 16km Chilterns Tunnels; and five satellite compounds to the south enabling construction of the 3.4km Colne Valley Viaduct.
Although the South Portal compound benefitted from excellent connectivity to the strategic road network, the satellite compounds were all situated on local authority roads, where a greater number of residents would have been affected by any noise or congestion. The satellite compounds were also subject to restrictions on the number of vehicles that could attend site each day. The decision was therefore taken during the pre-construction phase of the project to implement a CCC at the South Portal with the aims of reducing the environmental impact of the project whilst improving safety and maximising construction efficiency.
Approach
The ALIGN CCC was established at the start of main works in 2020 and comprised a 600m warehouse and 1200m laydown area. Figure 1 shows the team.
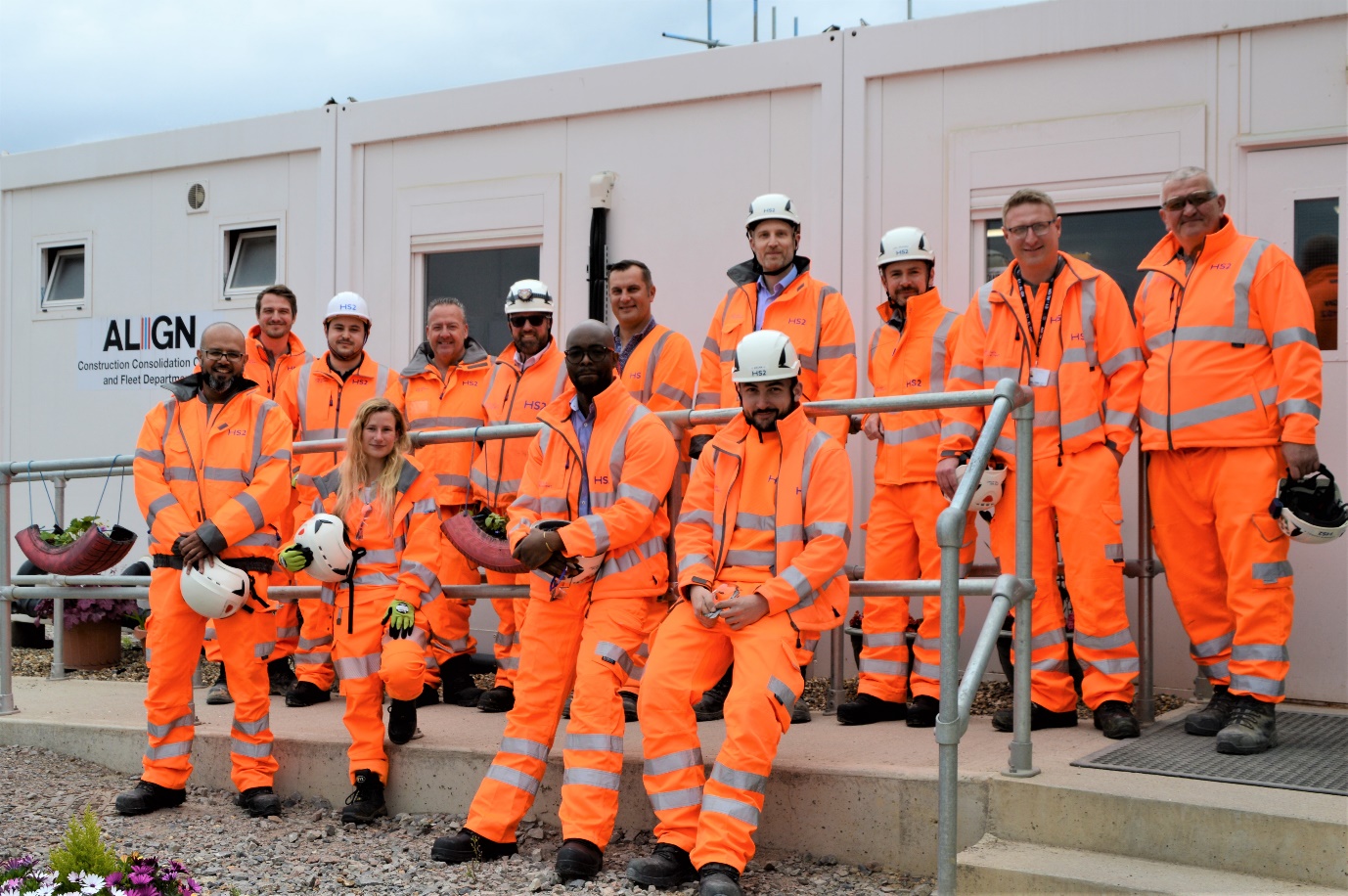
The CCC strategy was to receive all deliveries which didn’t need to go directly to site (for example abnormal indivisible loads, concrete, and steel) and consolidate them onto loads for delivery to the satellite compounds and South Portal delivery points using a ‘milk-round’ service. All courier vehicles for the project were directed to deliver to the CCC, further reducing the number of small vans attending satellite compounds. CCC delivery vehicles were then to be used for reverse logistics; removing waste and miscellaneous items back to the South Portal CCC to maximise storage at the satellite compounds.
The warehouse was fitted out with internal racking as well as waste compactors and charging stations for the CCC’s lifting equipment. A service desk was installed with IT equipment to process collections from members of the construction team.
The CCC facility was designed to segregate plant and lorry operations from light goods vehicle movements. A laydown area for larger deliveries was situated at the rear of the building and a segregated courier and postal delivery area was added at the front of the building so couriers and postal workers could make deliveries without requiring personal protective equipment (PPE), which was mandatory on the rest of the worksite.
The laydown area was secured with fencing and used to provide the construction teams with an area for the short-term storage of larger items. A 5-tonne outdoor forklift was used for loading/offloading items in the laydown area, as well as for delivering large items around the South Portal site.
The CCC processed all PPE required by the project’s workforce of over 2,000 people. A PPE-free safe walking route was installed between the CCC and the worksite’s main offices and welfare. Initially PPE stock levels were maintained based on demand from the project’s increasing workforce. A warehouse management system (WMS) was later introduced to digitally monitor transactions and enable the CCC team to manage stock levels based on monthly consumption data. This led to a reduction in value of stock held at the CCC and allowed the team to intervene if consumption of PPE by particular teams became higher than expected.
The CCC started off with just two delivery vans whilst the project mobilised and a daily delivery route was established delivering to the main areas of the South Portal and satellite compounds.
The CCC initially handled components for ALIGN’s two tunnel boring machines (TBMs) as well as courier deliveries and construction materials for the establishment of the South Portal compound. As the volume of goods increased, a large electric van was added to the fleet to deliver courier items and post, then a flatbed van was added to deal with larger items and palletised goods (see Figure 2). By 2022 the CCC was staffed by a team of 11 and a lorry with a mounted crane was hired to move larger items and use of this was opened up to the construction teams, helping them avoid the cost of hiring third party transport for a single movement.
The CCC allowed ALIGN to bulk order high use consumables, receiving bulk order discounts, and allowing items to be delivered to the construction teams on a just-in-time basis, improving efficiency of the workforce.
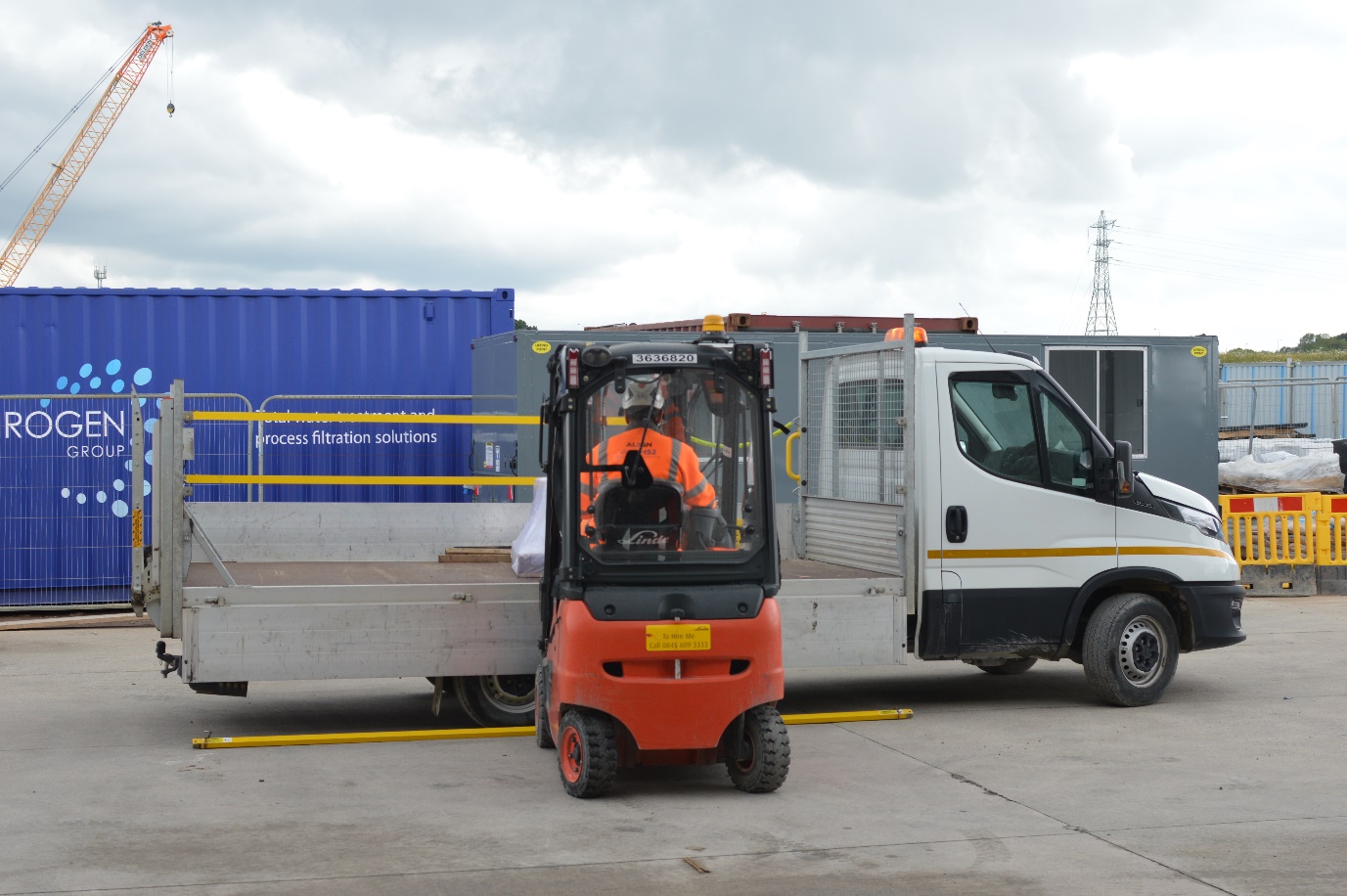
CCC synergies
The CCC created a number of opportunities for synergies, and increased collaboration with other departments and construction teams. The CCC was able used its workforce of logistics professionals to undertake tasks for areas of the project that would otherwise have required a dedicated resource. Some of these synergies are listed below.
Fleet and worker travel department
ALIGN operated a fleet of 100 vans, 4x4s and minibuses. The ALIGN fleet department shared an office space with the CCC team, and a sheltered vehicle servicing area was installed to the rear of the CCC warehouse. The servicing area was segregated from the CCC with fencing, and lockable arm barriers were installed so that the fleet team could carry out their tasks in a safe and controlled environment. This allowed the fleet team to carry out activities such as changing tyres, refuelling, cleaning and even servicing of vehicles on site. This in turn removed the reliance on public garages (something local residents had raised concerns about before the start of the project) and reduced the amount of time that vehicles spent ‘off the road’. This also removed the need for engineers and construction workers to take their vehicles to local garages for servicing.
Co-locating the fleet department and CCC allowed the teams to share resources. Fleet minibuses were used to collect and deliver small items during off-peak period and when traveling to compounds to collect/deliver passengers. Conversely, CCC vans delivering to satellite compounds were used to collect/deliver fleet passengers, avoiding the use of a large minibus to transport one or two people.
CCC lorry-mounted crane service
The CCC introduced a lorry mounted crane (Hiab) service in 2022 which was used for collections, deliveries, and planned lifts across the project. The service operated at full capacity within six months and significantly reduced the spend on lifting and general haulage by the construction teams who would otherwise have paid a day rate to hire a vehicle for a few hours’ work. Responsibility for managing the service was given to the CCC yard supervisor, who planned movements as part of his role coordinating deliveries and collections from the CCC laydown area.
Laundry service
The CCC and Health & Safety departments collaborated with ALIGN’s PPE supplier to install a laundry service based at the South Portal compound. This service was free to use once personnel had registered their details when first collecting PPE from the CCC. A unique barcoded tag was issued by the CCC, and the laundry service could be used by workers whenever their PPE required cleaning. The CCC team reissued general use items like gloves after laundering, and uncollected items were laundered and re-issued by the CCC.
This service enabled ALIGN to prolong the life of PPE, reducing costs for the project.
Visitors and new starters
Each week ALIGN received a significant number of visitors and new starters to the South Portal. The CCC team produced ‘kits’ of PPE for all visitors and new starters and delivered them to the South Portal induction centre. Once visitor items had been worn, they were sent to the laundry for cleaning before being added to stock and re-issued by the CCC. Safety boots were sanitised and cleaned in the CCC, enabling them to be re-used by future visitors.
Self-service consumables and tool hire
The CCC collaborated with a major tool and fixings supplier to install a self-service store with 24/7 access at the CCC. The store held items of high turnover consumables, such as drill bits, cutting discs and sealants, and allowed construction teams to purchase and collect these items at short notice. The facility reduced the carbon footprint of the supplier’s operation by up to 70% as they were able to avoid making numerous ‘last-minute’ deliveries to site.
Plant management area
The ALIGN plant team required an area to receive and manage plant deliveries. A section of the laydown area was reserved for plant safety checks upon arrival to the project. Items of plant could also be securely stored whilst awaiting servicing, inspection, or off-hire (see Figure 3).
Surveying department area
The surveying department required an area to store and charge surveying equipment. An area of the CCC was allocated which was covered by CCTV cameras and provided surveyors with 24-hour access to their equipment under secure and safe conditions.
Lifting equipment repair workshop
Another area of the laydown was used for repairing lifting equipment on site. This reduced waste by repairing equipment that could be re-used. It also avoided instances of equipment being sent away for repairs and taking so long to return that replacements were required.
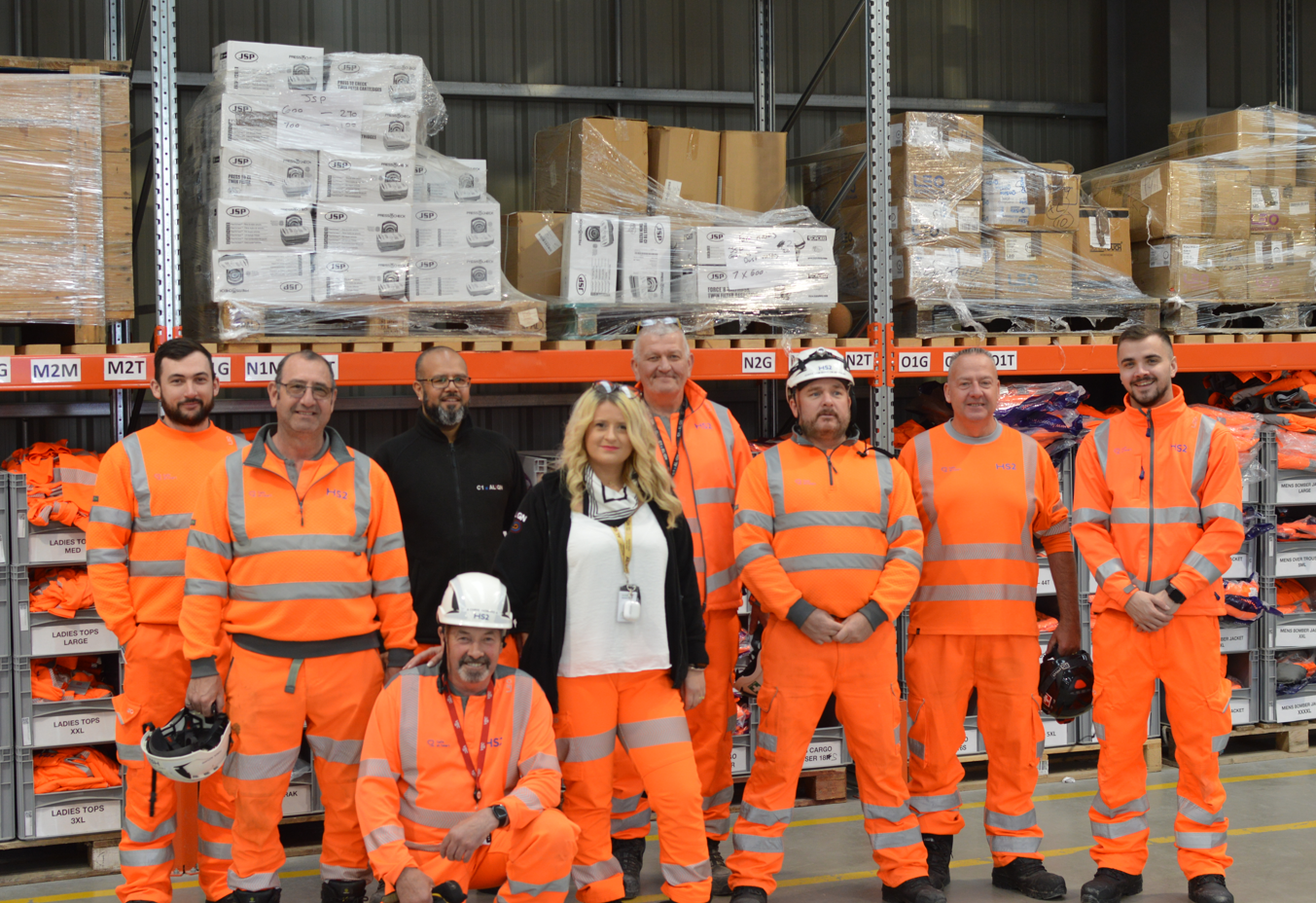
Outcomes
On average 485 courier deliveries and 104 lorry deliveries were received by the CCC each month, with 110 consolidated loads delivered by the CCC. This equates to nearly 500 vehicles per month being removed from the local road network: reducing the risk of congestion and road traffic collisions and improving local air quality around the satellite compounds.
The compound was extremely secure and prevented theft from the project. At the time of writing no thefts of tools, plant or equipment had been recorded from the CCC.
The introduction of an electronic WMS allowed the CCC team to generate reports for all incoming and outgoing stock, and record transactions electronically. Consumption data was analysed and a 50% reduction in the amount of PPE held in the warehouse was achieved. By only holding eight weeks’ worth of stock and not replenishing until levels dropped below six weeks’ worth of stock, based on an average from the preceding three months. At the time of writing the project was just over 50% complete and approximately 280,000 items of PPE had been issued by the CCC.
By utilising robust delivery recording and tracking procedures the CCC helped ALIGN avoid missing and lost deliveries. Records were kept for all items delivered to the CCC, and only items with clear delivery information were accepted. When items were delivered to (or collected by) the construction teams they were required to sign for the items and a photographic record was kept of the item with the recipient’s project ID card for traceability.
The CCC team carried out a study of glove usage across the project and established a case for laundering and re-using them. An agreement was made with various departments that gloves would be collected and sent to the laundry to be washed and re-issued to site personnel. This created a significant cost saving for ALIGN.
A re-fuelling centre was installed at the CCC laydown area which removed the need for vehicles to refuel at local filling stations, further reducing vehicle movements on public roads and reducing costs for ALIGN.
The lorry mounted crane service was utilised by multiple construction teams across the project. Having a lorry mounted crane and driver at the disposal of the CCC allowed the construction teams were able to operate in a more efficient and cost-effective manner when compared to relying on ad-hoc, hired-in, transport. By hiring the vehicle on a long-term contract ALIGN were able to obtain a significantly reduced rate (almost 50% per day) and plan lifts in advance. Using the same vehicle and driver helped with driver familiarity and improved the integration of the service into construction operations. Lifting plans (documents required by the project before any lifts could be undertaken) were obtained in advance and a lifting supervisor was pre-allocated to the task to avoid delays prior to the lift. Significant cost reductions were made by undertaking lifts for multiple construction teams, with an average of 3.4 jobs undertaken per day, increasing productivity of the vehicle and driver.
Learnings and recommendations
The ALIGN CCC produced a number of benefits for the project. These included a significant reduction in the number of vehicles attending satellite sites (approximately 500 per month), improved ordering capabilities (bulk purchases) and increased availability of storage space on the satellite compounds. In addition, many of the benefits realised by the CCC were not originally anticipated when the project started. The presence of a dedicated logistics resource – both the facility, fleet and team – created a number of synergies which would not otherwise have been possible. For these reasons it is recommended that future projects consider the use of a CCC.
Both the timing of the Covid-19 pandemic, and the availability of a management team with prior experience of operating such facilities, disrupted the initial establishment of the CCC.
At the start of operations, the management team did not have prior experience of CCCs. As a result, it took longer than anticipated to implement the project-specific management practices and operating procedures required to maximise the efficiency of the operation. The training of CCC management was further disrupted by the Covid-19 pandemic, and ‘on the job’ learning was required to reach maximum effectiveness. The CCC provided ALIGN with the operational flexibility to manage complexity on the project. The management practices and operating processes used by ALIGN would not necessarily be of use to future projects with different procurement models and complexities to manage.
With many employees working from home during the pandemic it also took longer than anticipated to fully integrate the CCC into certain areas of the project. Following the end of the pandemic face-to-face relationships increased and the CCC adapted by adding new features, such as the lorry mounted crane service, to increase the value it brought to ALIGN.
When considering CCCs for future projects early engagement with the construction teams and supply chain is critical. Early on-boarding of management teams would assist with this task, as well as allowing them to establish procedures and key performance indicators. Third-party logistics companies could also be considered to operate the CCC if experienced managers are not available.
Access to a WMS from the start of CCC operations would have been beneficial. The paper-based system used initially made it difficult to spot trends in the same way as an electronic WMS, which enabled improved better forecasting of stock utilisation and a reduction in spend.
The ALIGN CCC was well utilised, with average stock levels at around 85% of capacity despite limited storage to under eight weeks of stock. Had ALIGN self-delivered more of the works, instead of subcontracting some of the major packages, a larger CCC would have been required. Determining the required size and configuration of the CCC was based on professional judgement and using experience of previous projects the team had worked on, particularly Crossrail. The authors are not aware of a formula for specifying the required size of CCCs. The uniqueness of each construction project, both in terms of equipment requirements and delivery model (self-delivery versus subcontracting), makes this challenging, however it is hoped this paper can be used as a reference point for practitioners considering CCCs for future projects.
The use of electric vans was a priority for the CCC to maximise environmental benefits. These vehicles suffered from significant degradation in range over the life of the project and were eventually restricted to short-distance deliveries. It is recommended future electric van users consider this as a factor when profiling their fleet makeup.
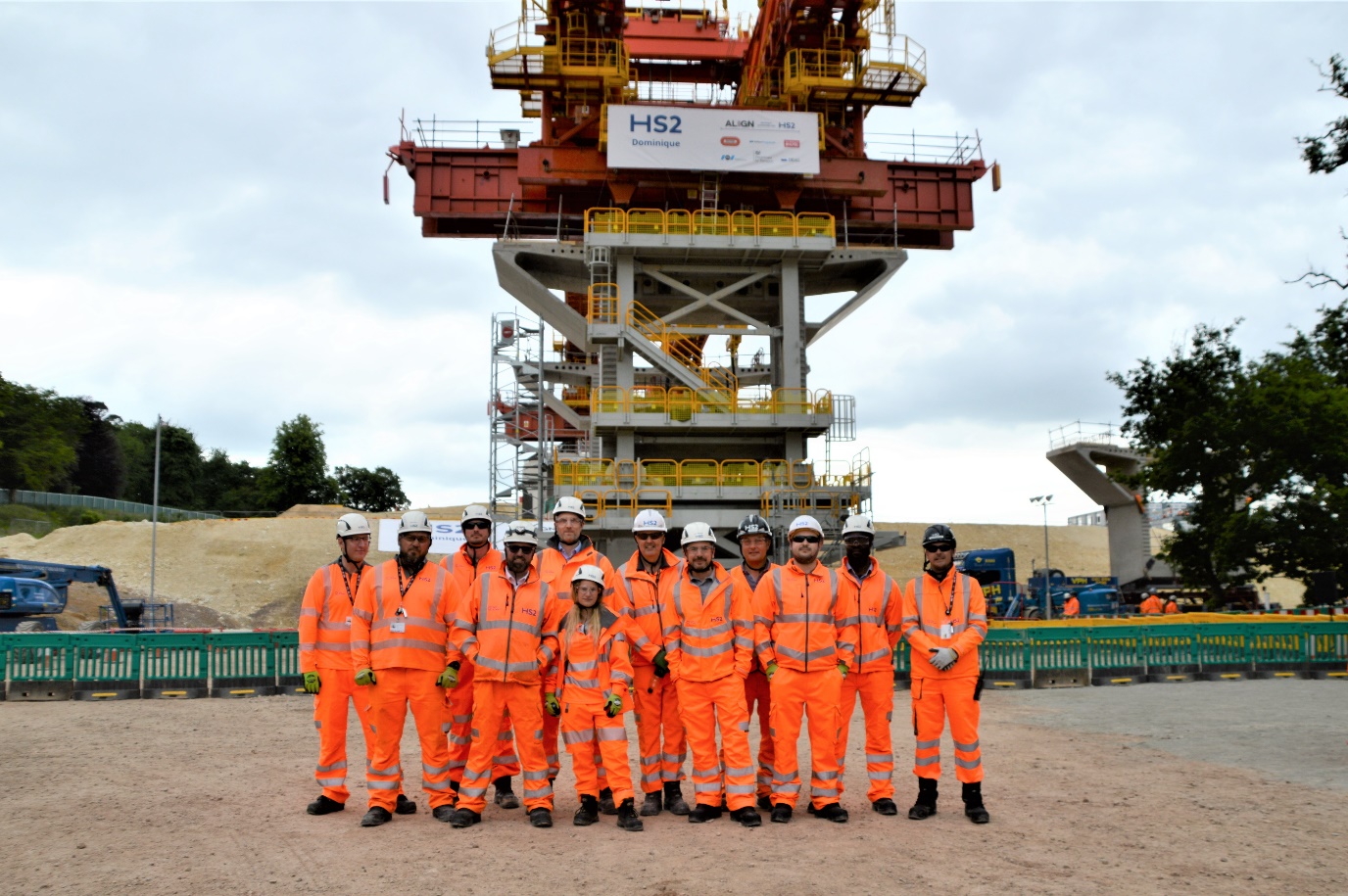
Conclusion
Although a CCC may not be suitable for every construction project, the ALIGN CCC was successful at managing the unique challenges faced on the project.
By preventing around 500 vehicles per month to ALIGN satellite compounds the CCC helped minimise the environmental impact of the project, meaning less congestion, noise, and pollution, along with improved safety. The utilisation of reverse logistics techniques meant return journeys to the CCC could be used for waste removal as well as the return of unused material, pallets and packaging for reuse and recycling.
In addition to the environmental and safety benefits, the CCC helped improve productivity on the construction sites by delivering fewer vehicles in a ‘just-in-time’ manner, removing the need for construction workers to process the extra deliveries and manage storage of equipment and materials not immediately required in the construction process.
As a secure compound operated by a team of logistics specialists, the CCC acted as a catalyst for several improvement projects, reducing cost and creating synergies with other departments that would otherwise not have been possible.
Many of the benefits delivered by the ALIGN CCC would be available to projects using off-site or third-party-operated CCCs. It is recommended that future projects carefully consider whether the use of a CCC is appropriate for the unique challenges they face. To maximise investment, it would be prudent to engage with the construction teams and the supply chain at the pre-construction phase, as well as sourcing an experienced management team to establish the facility prior to the start of construction.
Acknowledgements
David Wood – CCC Manager
References
- Allen J, Browne M, Woodburn A, Leonardi J. Supply Chain Forum: An International Journal. 2014; 15 (4) 100-112.
- Transport for London. London Construction Consolidation Centre Final Report. 2008.
- Browne M, Sweet M, Woodburn A, Allen J. Urban Freight Consolidation Centres Final Report. 2005
- Sustainable Urban Consolidation Centres for Construction (SUCCESS). Business models for construction logistics optimisation and CCC introduction. 2017
Peer review
- Sarah RichardsHS2 Ltd
- Shital-Shirsat Rohekar HS2 Ltd