Materials by Rail (MbR) to HS2 on-site stockpiles
The efficient distribution of construction materials, fully compliant with HS2’s ambition to be carbon neutral and considerate to its neighbours, presented a unique range of materials challenges and it became obvious that Materials by Rail (MbR) would play a significant part.
The alternative MbR strategy Ref: RAT EK MbRRail 290819[1], developed by the rail specialists engaged by EKFB, utilised the existing rail network connection to deliver a large proportion of the materials directly to the line of route, thus eliminating an equivalent proportion of the road movements that would have been required.
Following an initial trial volume by rail to prove the concept at one location, four railheads in the central section have opened and operated which will deliver close to 4.5 million tonnes direct to the line of route, by rail, by the end of the current programme in Q1 2026.
The rail operation has proven its value and gained excellent support from stakeholders who recognise the value it has brought to such a large-scale project. MbR not only provided a significant financial saving of more than £11.2 million, it also greatly improved the safety of the material delivery operation through the greatly reduced number of truck movements on local roads and through villages, as well as reducing the project’s carbon footprint.
This paper would be of use to construction project strategists and project logistics teams responsible for developing transport solutions for bulk materials deliveries to any civils or rail project with adjacent existing railway access.
Background and industry context
Rail operation has successfully provided material logistics solutions to many major civil engineering projects over the years. HS1, West Coast Route Modernisation, The Olympic Park and the nuclear power station build at Hinkley point C to name but a few.
Rail solutions were considered at the early stages of planning for all these projects. This was standard practice for rail projects (HS1 established the Beechbrook Farm rail hub at the outset, West Coast Route Modernisation was a Network Rail project delivered entirely by rail during a series of blockades – road deliveries were discounted other than for small volume specialist materials). This enabled early rail supply market engagement, feasibility and logistics solutions development as an integral part of project planning. Like the Olympic Park build which used the Bow East Logistics Centre (BELC) as its rail hub, HS2 identified, early in the strategic planning stage, the impact on the road network that would result from the removal of millions of tonnes of excavated material in and around London. As such, the use of rail was mandated through the Undertakings and Assurances (U&As Section 880)[2].
However, the import of bulk materials to areas of the HS2 outside London was not mandated in U&As and thus the use of rail deliveries direct to site was not considered or mandated at the early planning stage. As a result, there was little direct engagement with the rail supply market for these areas. Instead, responsibility for the material logistics methodology and planning was passed down to the material suppliers (quarry companies), against a backdrop of constantly evolving requirements and constraints. Ultimately, this resulted in a sub-optimal material logistics plan, based entirely on last miles by road.
As part of HS2 construction in the 80km central section, the Main Works Civils Contract (MWCC) for the central section of High Speed Two (HS2) Phase One which includes the North Portal Chiltern Tunnels to Brackley and Brackley to South Portal of Long Itchington Wood Green Tunnel, being delivered by the EFKB Integrated Project Team, is required to import over 7m tonnes of aggregates materials. Most of this geography is rural countryside which presented a logistical challenge to the construction team.
The aggregate fill materials delivery strategy was based on bulk delivery by rail to supplier railhead stockpiles close to, but not on, the line of route. This meant that the final delivery to stockpiles or worksites would all be road delivered, over the most highly restricted local roads surrounding the sites.
Approach
A team of rail subject matter experts was engaged to develop an alternative bulk materials strategy[1] to optimise the use of rail. The need for a rail advisory team was initiated by the MWCCs Head of Security and Logistics towards the end of the Stage 1 planning stage. It had become apparent that the Logistics Team lacked expertise in managing delivery of materials by rail and identified severe risks to the delivery of materials by road plans as the Schedule 17 road movement applications to local authorities were being rejected or severely constricted. A Rail Advisory Team Scope of Works Scope (Ref: 1MC06-CEK-SPE-C002-700001)[3] was produced and approaches were made through rail experts in HS2 and Network Rail to identify companied with the requisite skills. The chosen provider was selected based on the individuals’ extensive rail experience and breadth of expertise and knowledge which Operations, Engineering, Planning. Network Rail Processes and Commercial. This team worked collaboratively with project and rail industry stakeholders, (see acknowledgements) to:
- Determine direct rail access points from the existing network to locations on the HS2 trace
- From examination of Quail – Railway Track Diagrams
- Analyse material demand profile over the life of the project
- From master materials demand spreadsheets – Materials Team
- Identify materials types and volumes that could be switched to rail
- In conjunction with Materials Team and Materials Suppliers
- Minimum 1650 tonnes of material to operate an economically viable train
- Identify stockpile locations and available space/stock holding capacity
- Based on available suitable land and proximity to existing rail lines and sidings.
- Avoiding residential areas
- Design railhead and stockpile layouts
- Example for Calvert North (Ref: MC12-EKF-CL-PLN-CS08-0000113)[4]
- Determine licensing requirements for sites and secure requisite permissions
- Planning consents of outside HS2 boundary limits
- Schedule 61 applications to determine available operating hours
- Identify train paths from material supplier source quarries
- Study of Network Pathing system (FTAC)
- In collaboration with Material Suppliers, Railway Operating Companies, Network Rail, other MWCCs (clash avoidance)
- Confirm available train resources: locomotives, wagons and traincrew
- Ref: OS-PRO 7464 – Resource Validation Process[5]
- Ref: OS-PRO-7465 – Rail Supplier Mobilisation Validation Process[6]
- Establish safe system of work for each the railhead
- Included in site plan: Ref: OS-PRO-7463 V002[7]
- Build business cases for each identified stockpile site to support the switch of volume from road to rail
- Developed P&L spreadsheet for each railhead to determine establishment cost, operating costs and road costs avoided to determine value created
- Support commercial negotiations with rail suppliers
- Using market knowledge of train cost by time and distance and resources deployed
- Build railheads and stockpile areas
- Input to design of layouts. Built by local MWCC Works Teams
- Create a detailed material plan for rail deliveries in collaboration with materials suppliers, selected rail operators and other rail stakeholders for each railhead
- Published timetable of services per Network Rail planning system
- Develop a rail delivery control and management system to measure performance and forward planning
- Daily Log and train monitoring system measuring train departures, arrivals, delays, delay causation, wagons on train, material type, material volumes, train discharge time duration, failure reasons and responsible party
- Measure performance and ongoing status of each and all railheads, train deliveries and suppliers via a bespoke balanced scorecard
- Bespoke dashboard to measure delivery performance at each railhead
In parallel, key rail industry partners (see acknowledgements) played crucial roles in identifying network capacity and adjusting plans to accommodate the required train paths.
Outcomes
First material was delivered to a site-based railhead stockpile via train within 13 weeks of order to proceed. Further opportunities to utilise rail use over road were identified, with three further railhead stockpiles commissioned and operational. Three train services operated per day delivering 4,800 tonnes of aggregates which is the equivalent of 240 truckloads (480 truck journeys) per day being taken off local roads, resulting in carbon savings of 19,000 tCO2e to date.
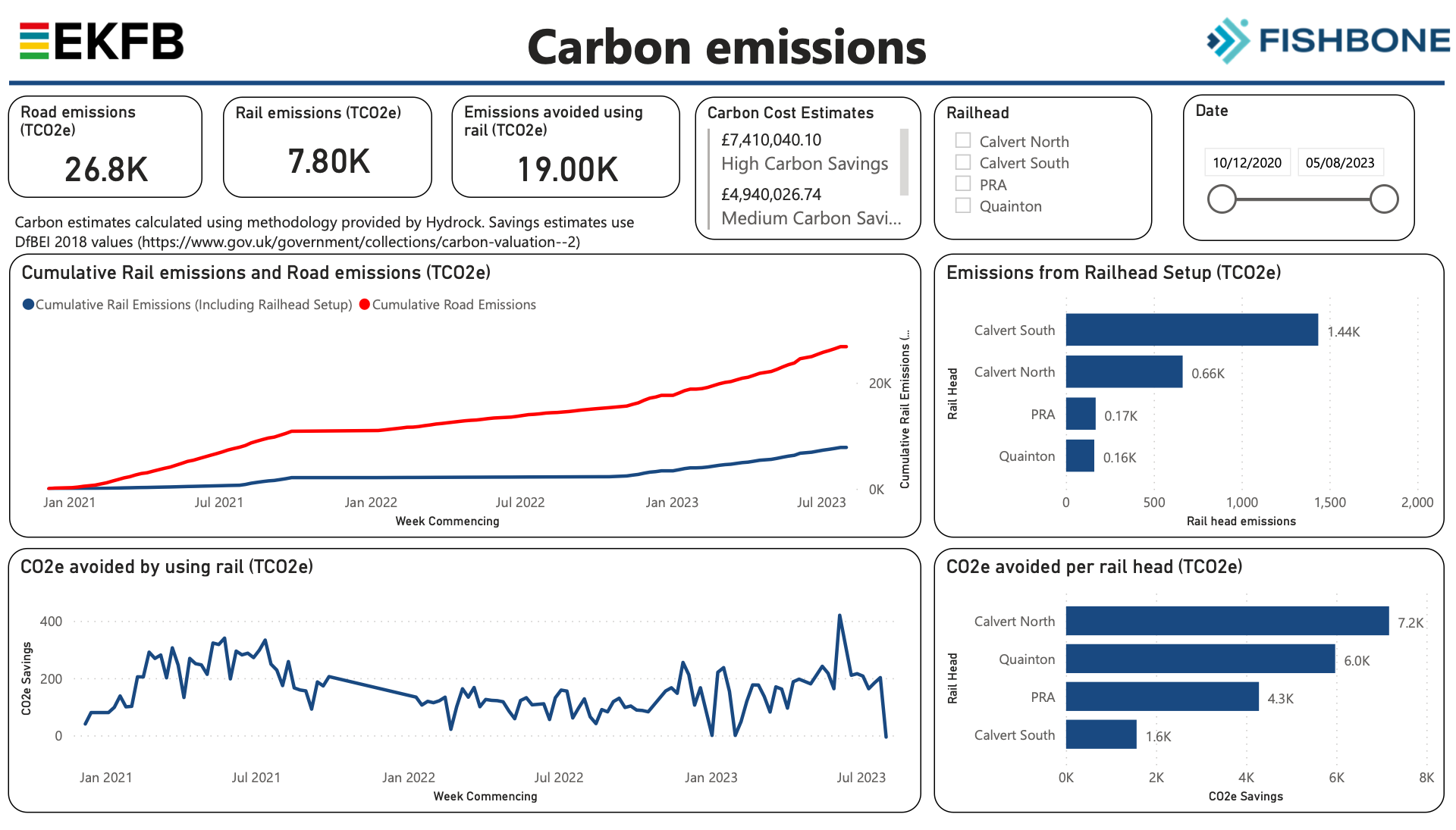
More than 1.8 million tonnes have been delivered as at 5th August 2023. It is expected, at completion in 2026, over 4.3 million tonnes will have been delivered by rail to the Central Section, equivalent to 215,000 loaded truck movements (430,000 truck journeys) avoided.
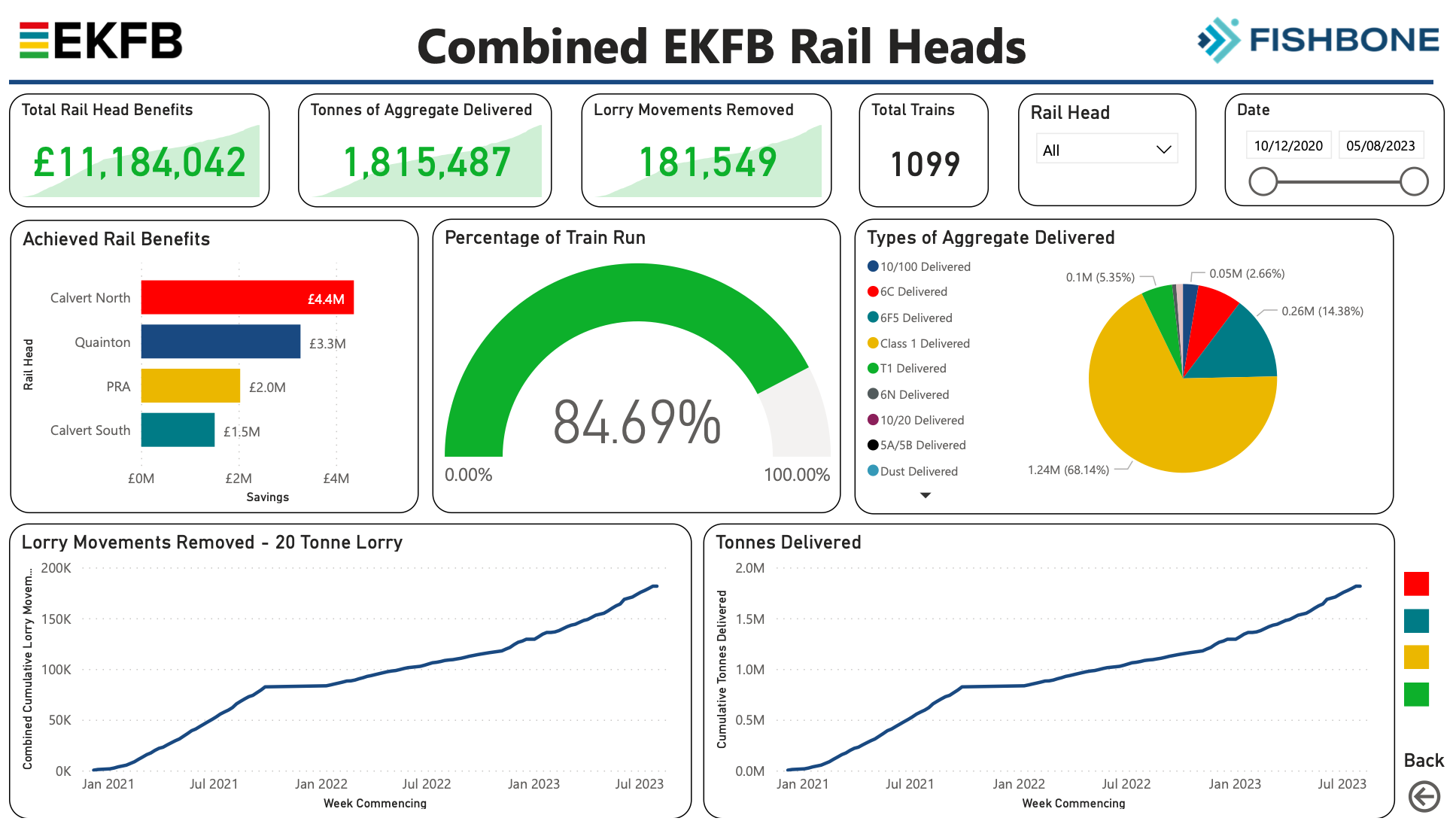
There was some negative impact of infrastructure failures on the rail network and also some strike action during the delivery phase which resulted in a small proportion of lost deliveries. These were mitigated by increasing operations from 5 days per week to 6 days per week.
Learnings and Recommendations
Earlier engagement with specialist rail advisors would have identified the benefits of rail in the logistics strategic planning stage and could have created a more competitive environment for materials supply through a more rail-oriented logistics strategy from the outset.
Knowledge of logistics and materials costs whilst developing the design and construction plans would have allowed for tailored bespoke competitive tendering.
Early determination of the value of each logistics flow, through integration with the milestone programme (Ref: xxx), would have allowed further efficiency to be derived through performance and policing regimes.
As the rail industry operates on a 44-week planning cycle (Ref: OS-PRO- 7462)[8], further benefit could have been determined through a more efficient train plan aligned to the Network Rail planning process.
The HS2 Programme has committed to significant Carbon, Community, Sustainability and Environmental targets, all of which can be optimised through the usage of Materials by Rail. A train carrying 1500 tonnes of materials is up to 4 times more carbon efficient than road over the same distance[9].
The rail network operates around the clock, and through closer consultation with HS2 considerable improvements to materials delivery could have been achieved through flexibility in arrangements around the HS2 operational hours.
Compliance with HS2 Undertakings and Assurances, Section 7 of the HS2 Act[2] is critical to the success of the programme. The development of baseline materials by road, as part of the consideration of the logistics planning process, would allow comparisons of costs, emissions, traffic, consents, carbon and community impact to be undertaken at any subsequent stage of planning and delivery.
Benefits of MbR operation
MbR, although not a new concept, has been pivotal in supporting HS2, in meeting material requirements for the project. It has also brought a series of other benefits which are outlined below.
Due to the efficiencies of scale associated with bulk rail freight, moving high volumes of material by rail provides huge carbon benefits. To date, across all EKFB rail heads, almost 19,000 tonnes of carbon emissions have been avoided to date by using rail over road as validated by a Carbon Specialist.
By utilising the rail system to transport these high volumes of materials, lorry journeys have been avoided, reducing congestion and damage on local roads. To date, 1109 trains have operated with minimal disruption and a 100% safety record with zero incidents. Trains have replaced 90,750 rigid 20t capacity lorry loads (181,500 total lorry movements) from the local roads, significantly reducing the risk of accidents/incidents involving vehicle interfaces with the public.
The MbR project has provided a significant cost saving to EKFB by greatly reducing last-leg lorry deliveries from remote supplier stockpiles through direct deliveries from supplier quarries to the site railheads. The key benefits/efficiencies were:
Rapid response – Mobilisation in less than 3 months
Efficient use of assets – three trains per day using 3 wagon sets each carrying 1650 tonnes 178 miles in each direction delivering over 1 million tonnes of project critical material in per annum.
Economic – significant cost saving versus the available alternative source option (by road from supplier railhead stockpiles). Across the 4 railheads commissioned so far, Rail has provided an average of 50% reduction in the transportation cost per tonne compared to road.
Good neighbour – The trains have operated within agreed time limits each day and have attracted positive comments from local communities, local authorities, HS2 and the media Ref: HS2 Communications Bulletin (link attached)
Safety – The services have operated with minimal disruption and a 100% safety record with zero incidents. The trains have replaced trucks from the local rural roads, minimising the risk of accidents/incidents involving vehicle interfaces with the general public.
Environmental Benefits (including carbon reduction) – The carbon benefit differential between this rail option, delivered direct from the source quarry, versus the truck option, delivering from the supplier local rail stockpiles, has been calculated at 19,000 tonnes to date (05/08/23) by EKFB’s Carbon Manager, providing a significant contribution to the project carbon reduction targets.
Conclusion
The benefits of rail versus road for high volume bulk materials is significant but as rail is generally less clearly understood than road in the construction sector, there is a tendency to ‘go with what we know.’ Only 6% of UK freight is moved by rail.
Rail operations are more complex to establish than road operations but where a rail solution is possible and suitable (typically high volume, long distance, bulk materials) the financial, environmental, safety and public relations benefits achievable provide a compelling argument to include rail at the top of any project’s logistics solution option list.
Engagement of rail subject matter experts at the project strategy stage is essential in determining an optimum materials delivery strategy.
Acknowledgements
EKFB Logistics Team, HS2 Rail EKFB Area Delivery Directors, Network Rail Freight Commercial, Network Rail Western Route, Other HS2 Contractors, Great Western Railway TOC, Chiltern Railways TOC and affected FOC partners.
References
- RAT EK MbR Rail 290819 – Final MbR Strategy
- HS2 Act Section 7 Undertakings and Assurances
- 1MC06-CEK-SPE-C002-700001 – Rail Advisory Team Scope of Works
- 1MC12-EKF-CL-PLN-Cs08-0000113m – Calvert North Railhead and Aggregates Stockpile Construction Logistics Plan
- OS-PRO 7464 – Resource Validation Process
- OS-PRO-7465 – Rail Supplier Mobilisation Validation Process
- OS-PRO-7463 V002 – Stockpile Management Process
- Rail industry operates on a 44-week planning cycle (Ref: OS-PRO- 7462)
- Department for Energy and Security and Net Zero 2023 “Greenhouse gas reporting: conversion factors 2023”. Accessed 24/8/2023.
Supporting Materials
HS2 communications bulletin “HS2 update: first delivery to Calvert construction site” [Video]10th December, 2020. Accessed 21 August 2023.
Peer review
- Charlotte Hills HS2 Ltd