Physical testing of noise barriers to validate an airborne noise model for a high speed railway
For any noise prediction model, it is vital that there is confidence that the forecast noise levels, within the calculated confidence limits, are going to be met in reality. This is incredibly important both in terms of contractual risk and liability and maintaining stakeholder trust.
This paper discusses the noise barrier testing and airborne sound model validation approach taken by ALIGN JV as part of the HS2 project.
Due to certain design characteristics of the Colne Valley Viaduct (CVV), it was necessary to modify the validated HS2 airborne noise prediction methodology, which is based on an empirically derived and validated train noise prediction model. The adjustments were developed using numerical modelling, and in order to validate them, full scale mock up testing was undertaken which captured the key acoustic elements of the mitigation design for the CVV. Closely linked, was the development of a bespoke validation procedure which considered the uncertainties inherent in both physical testing and numerical modelling. The validation results showed very good agreement between the modelled and measured data, and the numerical modelling allowed many different design options to be tested. Where required in more complex and/or challenging assets, these validated adjustments could be used elsewhere along the Phase One route.
Background and industry context
For any noise prediction model, it is vital that there is confidence that the forecast noise levels, within the calculated confidence limits, are going to be met in reality. This is incredibly important both in terms of contractual risk and liability and maintaining stakeholder trust.
HS2 Main Works Civils Contractors (MWCCs) are contractually obliged to demonstrate validation of the prediction of ground-borne sound, vibration and airborne sound from operation. In addition, acoustic testing is required for civil engineering assets which provide acoustic attenuation, such as noise barriers.
Due to cost and complexity, as well as programme constraints, this requirement for testing is not necessarily an industry standard, but for a high-profile project such as HS2 provides much higher level of confidence that the installed barriers will provide the predicted level of performance in operation.
ALIGN JV is the Main Works Civils Contractor for 21.6 km of high-speed rail infrastructure along the HS2 Phase 1 route. Located to the north west of London, predominantly in rural Buckinghamshire, this section includes a 3.4 km viaduct, 16 km twin-bored tunnel and five vent shafts providing both intervention and tunnel ventilation facilities.
ALIGN is required through physical testing, to derive in-situ values of noise barrier ‘insertion loss’ (a measure of the noise reduction provided by the barrier) in accordance with PD CENTS 16272-7[1]. This standard describes how insertion loss values are measured at pre-defined grid positions. For environmental noise modelling where insertion loss values at receptors could potentially range widely, the standard states that a validated calculation model may be used.
This paper discusses the noise barrier testing and airborne sound model validation approach taken by ALIGN JV.
Approach
Stretching for more than 3.4km across a series of lakes and waterways between Hillingdon and the M25, the Colne Valley Viaduct (CVV) will be the longest railway bridge in the UK.
The CVV therefore carried a high level of expectation in terms of visual appearance and extensive consultation was undertaken to minimise operational noise from the railway, whilst meeting the overall design aspirations which included the need for appropriate noise barriers along the length of the CVV.
One of the key aspects of the CVV noise barrier design was the need to meet the architectural design requirements of the barriers, which included minimising the visual impact of the barriers and allowing passenger views from the train. Specifically, this required the use of a hybrid barrier design, comprising an absorptive visually opaque lower element and a reflective transparent upper element. In addition to opaque absorptive barriers, a derailment barrier (robust kerb) was also required which was modified in design to maximise its effectiveness as a low level lineside noise barrier.
Due to the novel barrier types and arrangements required on the CVV, it was necessary to use detailed numerical models to evaluate their performance, rather than HS2’s standard prediction methodology [2,3], which is based on the train noise prediction methodology (which was originally developed for the Channel Tunnel Rail Link, now known as HS1). COMSOL Multiphysics[4], simulation software was employed to undertake the numerical modelling. Using a combination of boundary element and finite element modelling, bespoke adaptations were derived and applied to the standard HS2 noise prediction methodology.
The work described here is essentially to test the bespoke methodology and therefore validate the barrier design of the CVV (i.e. barrier and robust kerb). The approach developed by ALIGN comprised three stages:
- Physical acoustic testing of barrier insertion losses.
- COMSOL modelling (replicating mock up).
- Model validation (using the physical testing and COMSOL modelling results).
Various options were considered for the appropriate approach for the physical testing aspect. The following aspects were evaluated:
- usefulness of data;
- technical risk;
- cost;
- test programme – time to undertake testing; and
- availability of test results with respect to construction programme.
Following careful research and extensive consultation with HS2, the following barrier insertion loss testing options were considered:
- Use existing modelling to demonstrate compliance (i.e. not undertake the test).
- Scale model testing.
- Testing barrier performance adjacent to an existing operational railway.
- Off-site mock up testing (simplified arrangement).
- Off-site mock up testing (detailed arrangement).
- In-situ testing (i.e. on CVV at point of barrier installation).
The benefits and dis-benefits of these testing options were carefully considered, and a summary of the appraisal conclusions discounting the following options is provided below:
- In-situ testing data too late in programme and impractical (working at height, above water in a constrained and noisy environment on the viaduct).
- Scale modelling complex and difficult to implement.
- Monitoring at existing railway creates a new set of variables to manage, test location unlikely to be representative of CVV.
It was considered that well executed simplified off-site mock up testing would provide the most suitable data for model validation due to:
- cost vs quality of data;
- practicality, working at ground level in an open site with low ambient noise levels;
- programme – can be carried out independently of HS2 site activities and testing can be completed relatively quickly due to simplified mock-up arrangement; and
- considerably fewer constraints being away from HS2 site in terms of access, land availability and ambient noise levels whilst still being sufficient for the derivation of suitably accurate data.
Based on extensive discussions with HS2, ALIGN JV and the appointed acoustics test contractor, it was considered that off-site mock up testing was likely to remain the most practicable option if:
- costs can be controlled through managed simplification;
- materials used largely represent those to be actually installed; and
- tests can be undertaken in a timely manner.
Besides the contractual requirements, the barrier insertion loss testing provided tangible benefits to both the MWCC ALIGN and HS2, since the test results would demonstrate that the civils assets provide the required level of acoustic performance, in isolation from the two factors which are outside of ALIGN’s control:
- rolling stock sound emission levels
- track performance
Due to the required size of the test site and the need for low levels of ambient noise, testing was not possible at ALIGN’s main site compound or any of their other HS2 construction sites. Given the further need for the test to be undertaken on hardstanding (rather than an open field, for example), a disused airfield was identified as an appropriate location, with one located in East Anglia deemed suitable.
The mock up test barrier arrangement closely resembled the 4m barrier arrangement and 0.8m derailment barrier on the CVV to maximise the validity of the test. Due to cost and practicality reasons however, the mock up represented one side of the viaduct and the track form was ignored. For the same reasons, the barrier arrangement was designed to be as short as possible (30 m) to control costs, whilst sufficiently controlling lateral diffraction (i.e. sound passing around each side of the barrier), which is important for the validity of the test.
The 0.8m derailment barrier (robust kerb) was included in the mock-up to account for double diffraction.
To ensure the runway surface was not damaged, concrete blocks were used to safely support both the barrier and vertical train side structures.
As a modification to the PD CEN/TS 16272-7 test [1], a vertical reflective surface was included behind the loudspeaker to represent the body of the train. This allowed sound to reverberate in the space between the inside of the barrier and the ‘train’, much like it would on a live railway. This modification was made to enable the test to measure the performance of the combination of reflective and absorptive materials on the inner face of the barrier which are added to reduce the build-up of sound and improve the performance of the barrier.
To maximise the validity of the tests, barrier cassettes, PMMA (transparent acrylic) panels, and robust kerb absorptive treatments were the same products that will be installed on the CVV.
To minimise acoustic uncertainty around the ground conditions, the test was undertaken on the concrete runway of the airfield used for the test location.
In the absence of an actual train pass-by to generate the noise source for the insertion loss test, a loudspeaker arrangement was used, as described in PD CEN/TS 16272-7 and referred to in this standard as ‘sound source C’. However, instead of the train emission spectrum provided in PD CEN/TS 16272-7, pink noise, was used. This was because the train emission spectrum would likely cause signal to background noise ratio issues, particularly in the lower octave bands. This means that the test sound level could be insufficiently high meaning unwanted background noise at the test site (most likely caused by wind induced noise) could significantly contribute to the measured levels, adversely affecting the result.
PD CEN/TS 16272-7 requires a source height of 0.5m above rail head. To better represent the height of the modelled sources, the tests included an additional source height of 5m to account for the pantograph (the source sound level was the same at each height).
Sound pressure levels were measured at receiver positions placed at 9 locations in a grid at the midpoint of the barrier mock-up (i.e. 15m from each end), orientated perpendicular to the barriers, as indicated in Table 1.
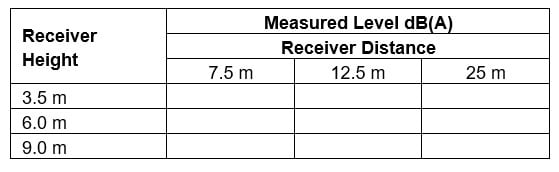
The following barrier insertion loss tests were undertaken:
- No barrier, reflective robust kerb.
- 4m reflective barrier, reflective robust kerb.
- 4m absorptive barrier, absorptive robust kerb.
- 4m hybrid barrier, absorptive robust kerb.
As shown in the table above, there were 9 measurement locations, so for each barrier type, accounting for the two source heights, there were 18 measurement locations. Thus, in total for the three barrier types there were 54 locations in total.
Whilst not part of the CVV design, a reflective barrier test was also included to provide a reference case to provide an understanding of the relative performance of the numerical model and HS2’s standard prediction methods.
Two photographs showing the testing arrangement are included in Figures 1 and 2.
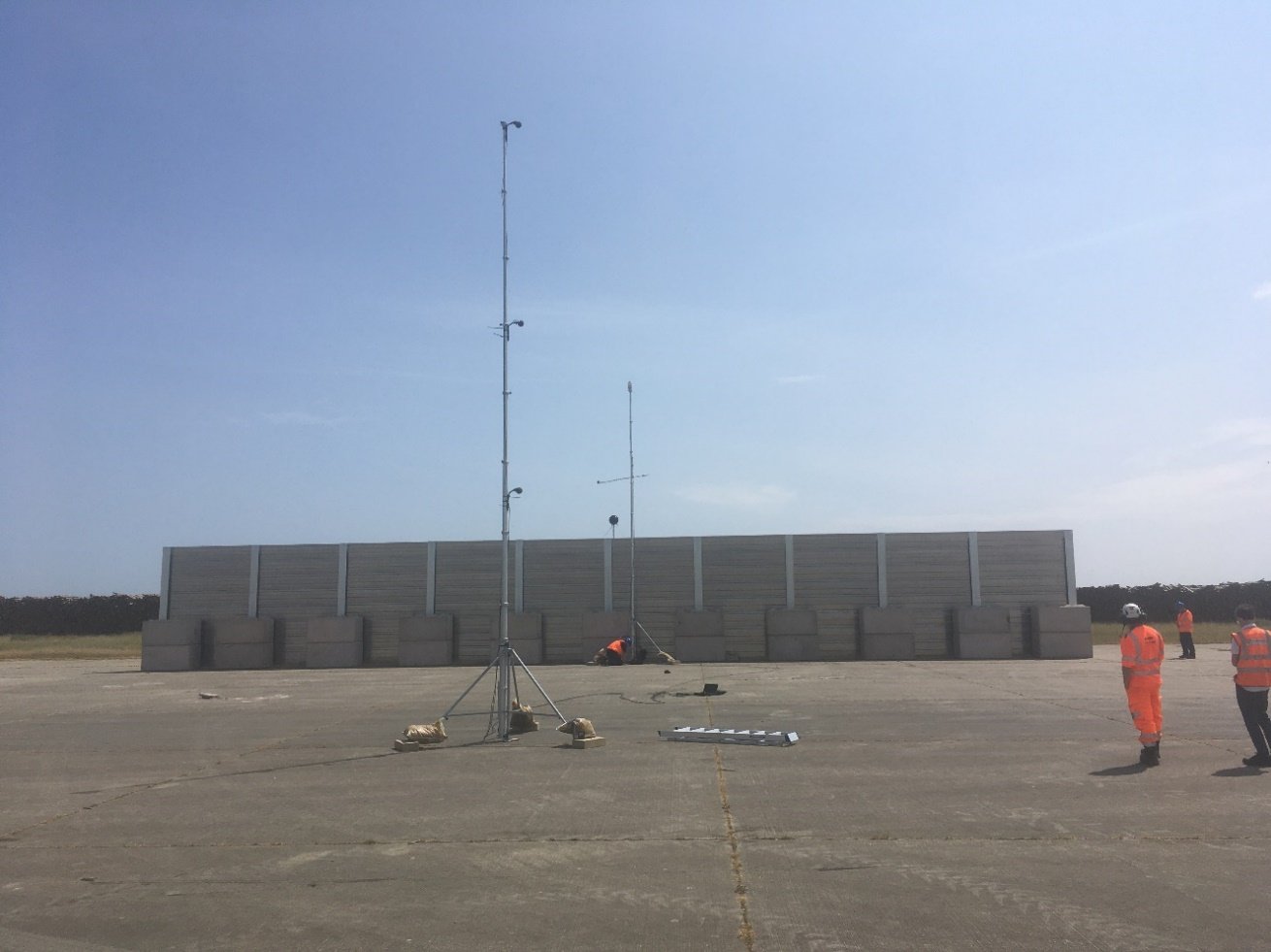
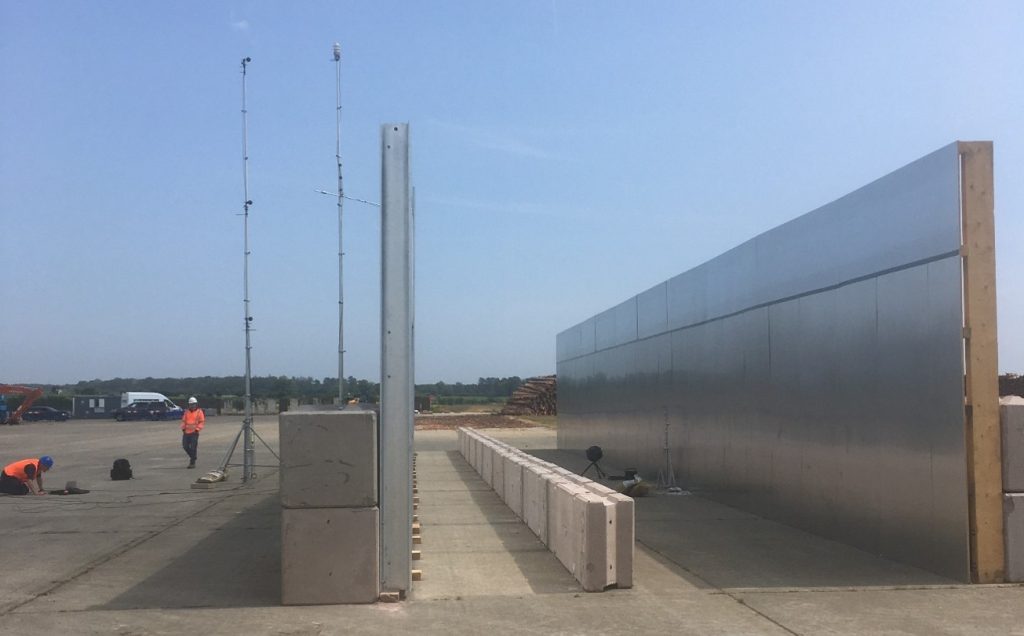
Moving from right to left, Figure 2 shows:
- train side reflector screen;
- sound source speaker (low height position);
- derailment barrier (robust kerb);
- barrier under test (only post can be seen);
- concrete blocks to support barrier;
- tripod with meteorological station and reference microphone; and
- tripod with receiver microphone array.
In general, the weather during the tests was favourable. However, for completeness and to ensure wind speed and direction did not significantly affect the results, with reference to the meteorological condition requirements of PD CEN/TS 16272-7[1], the tests were repeated at least twice for each barrier type.
Barrier insertion loss performance for each barrier type was derived by subtracting the ‘no barrier’ measured levels with the ‘with barrier’ measured level at each grid position.
A COMSOL Multiphysics® model[2] was produced to calculate the equivalent modelled insertion losses for each barrier type, allowing a comparison with the insertion losses derived through measurement. The models exactly replicated the test arrangement cross sections used for the physical tests, including:
- Exact dimensions and geometry of the barrier mock up;
- Exact acoustic performance of the barrier mock-up materials;
- two source heights; and
- all microphone positions.
The set-up parameters were identical to those used for the COMSOL modelling for the CVV.
A cross section of the COMSOL model is provided in Figure 3.
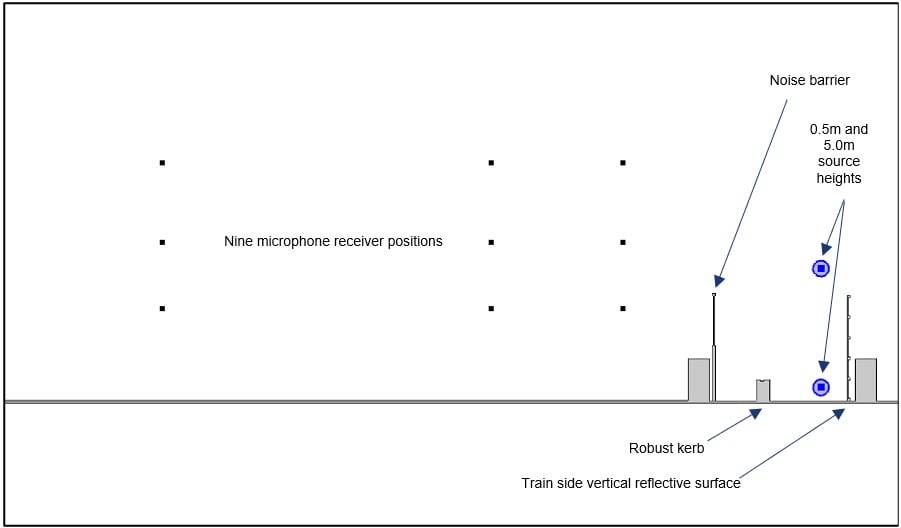
These COMSOL models allowed a comparison between measured and modelled insertions losses, forming the basis of the validation process. This was achieved by comparing the measured insertion loss levels with the equivalent COMSOL prediction model insertion loss levels.
A measurement in decibels of the difference between the measured and predicted insertion loss of the noise barrier was used to assess model validation. In addition, to account for the spectral shape of the HS2 train noise emissions (which were used in the prediction modelling), a process was developed to derive a single figure value (Lvalidation).
The validation of the airborne noise model was assessed by comparing the calculated Lvalidation values with the criteria in Table 2.
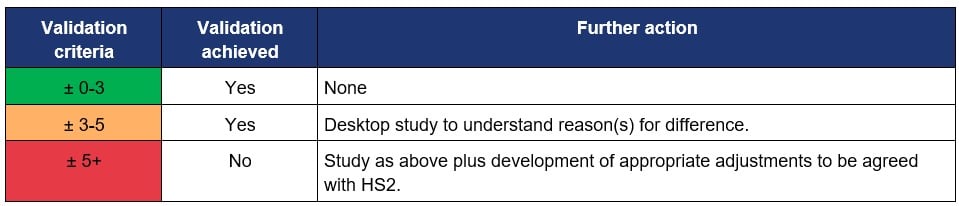
Outcomes
The test results with the most favourable meteorological conditions were used to derive the Lvalidation value for each barrier type and in the vast majority of cases, the wind conditions were compliant with the requirements of PD CEN/TS 16272-7. Note in addition, the standard requires the weather conditions for the ‘no barrier’ test and ‘with barrier’ test to be suitably similar.
For simplicity, only the validation results from the hybrid barrier (the most critical of all the barrier types) are presented in Table 3.

The overall results showed that validation was achieved at 53 of the 54 validation locations and it is considered that these results demonstrate clear agreement between the modelled and measured insertions losses. For the example above, the results show that at all locations the difference between the predicted and measured performance of the noise barrier was 2dB or less. Therefore, it is considered that the COMSOL prediction model has been validated following the procedures in the bespoke methodology.
As stated in PD CENTS 16272-7, since the model has been validated at the grid positions, insertion loss values outside the receiver grid positions can be characterised by prediction i.e., the COMSOL model is valid for predictions at all path differences.
This validation procedure therefore demonstrably provides confidence that the forecast noise levels, within the calculated confidence limits, are going to be met in reality.
Learnings and recommendations
Whilst the barrier insertion loss test has largely followed the requirements of PD CEN/TS 16272-7, certain refinements and adjustments of the process have been developed to account for practical and commercial considerations. These considerations included:
- deriving a minimum barrier length to avoid compromising the test results, whilst avoiding the need for a prohibitively costly long test barrier arrangement;
- use of a vertical reflective surface to represent the train body to allow the performance of absorption on the barrier to be accounted for in the tests;
- use of pink noise as the sound source (rather than the normalised train spectrum provided in the standard) to avoid signal to noise ratio problems;
- correcting the derived levels to account for the HS2 train noise emission spectrum;
- the importance of considering site set up and prevailing wind conditions; and
- the reassurance of second tests to ensure accuracy.
It took considerable time to define the overall approach as well as agree the barrier testing and model validation technical scope with HS2. This process could be significantly shortened with the knowledge and experience reported here. To assist future contractors and programme efficiencies, HS2 could provide guidance and structure to support the development and approval for testing arrangements, for example in the form of a decision tree.
The amount of planning required to undertake the testing should not be underestimated, in particular, agreeing commercial issues, designing the test arrangement, procuring the noise barrier materials, identifying a suitably experienced testing contractor and suitable test location. From initial planning to completion of the testing, a 12-month period should be considered to be a minimum.
Suitable weather conditions are vital to ensure the results are acceptable and compliant with CEN 16272 [1]. It is considered that attempting to undertake the results during the winter months could lead to an excessively drawn-out test, with associated increased costs and programme delays whilst waiting for suitable weather conditions.
The three-stage airborne noise model validation process described in this paper is a bespoke approach developed for the CVV, which nevertheless could be deployed elsewhere on HS2 and therefore could streamline the validation of noise barriers or other acoustic mitigation assets.
Undertaking full scale barrier insertion loss testing to validate or confirm airborne noise predictions represents a considerable undertaking, both practically and commercially, and indeed is unlikely to be necessary for most projects. Nevertheless, this process using simplified off-site mock up testing could potentially be used on other rail or even highway applications, where increased confidence is required when predicting barrier performance, in particular for complex barrier arrangements.
Conclusion
The cost and planning required to undertake a noise barrier insertion loss test is considerable and, for most projects, it is unlikely to be necessary. However, in certain situations where barrier arrangements are complex and mitigation performance paramount and the risk of non-compliance is high, the cost could be justified.
This study has provided a summary of potential test options and explained why the off-site mock-up was considered to be the best and provided some practical guidance based on the experience gained from planning and undertaking the test.
The airborne noise model validation has been a success which will be of great benefit to HS2 when providing evidence to stakeholders regarding the confidence of the predicted noise barrier performance.
Through careful planning and evaluation of technical and practical issues, ALIGN has demonstrated that this is a suitable testing approach and thus provided HS2 with a validated prediction methodology that can be used for complex barrier arrangements at other locations.
Acknowledgements
The authors would like to acknowledge the input and support of Littlewood Fencing Ltd and SRL Technical Services Limited, without whom this work would not have been possible.
References
[1] PD CEN/TS 16272-7:2015 Railway applications. Track. Noise barriers and related devices acting on airborne sound propagation. Test method for determining the acoustic performance-Extrinsic characteristics. In situ values of insertion loss.
[2] Hood, R.A. et al. : “Calculation of railway noise” Institute of Acoustics Proceedings Volume 13 Part 8. Accessed 25 June 2024.
[3] High Speed Rail (London – West Midlands). Environmental Statement Volume 5: Technical appendices. Sound, noise and vibration methodology, assumptions and assessment (SV-001-000) / November 2013. Accessed 25 June 2024.
[4] COMSOL Multiphysics®.
Peer review
- Oliver BewesHS2 Ltd