Powerful forces: electric plant and supply chain collaboration
Supply chain partners who are making the switch to low carbon, high efficiency “clean energy” plant and vehicles have been proactively sought out on the High Speed Two (HS2) Enabling Works Contract (EWC) for Area South. With a huge programme of earth moving and excavation being undertaken in Central London and a global drive towards reduced carbon and emissions, as well as HS2’s stringent Environmental Minimum Requirements (EMRs) and Non Road Mobile Machinery (NRMM) requirements, the EWC team have worked to implement the trialling and uptake of low carbon technologies including electric, hydrogen and hybrid plant.
The first phase of activity was powered by a single Euro Stage IIIA generator engine which represents the most current emissions standard in constant speed engines. For upcoming Phase Two works, all generators have been replaced with permanent power being implemented across the site. While this generated 46.595tns C02e over the duration of the project, the electric plant it facilitated enabled a carbon saving of 139.765tns C02e (186tns C02e saved using electric plant minus 46.595tns C02e contributed through use of generator). This was bolstered through the early adoption of the 22-tonne hybrid excavator which reduced carbon emissions by 11.55tns C02e in comparison to a standard diesel 22-tonne tracked excavator.
By placing the values of safety and sustainability at the forefront of the project and work package design, measurable increases have been demonstrated in efficiency, safety, reduced occupational health and wellbeing issues as well as measurable reductions in carbon emissions when working within an enclosed area in Central London. Site trials focused on improving safety, sustainability and productivity on the largest archaeological excavation of human remains in Europe.
Setting the scene for change
High Speed Two (HS2) has a mandate to drive improvement and beneficial change throughout the wider construction industry, through specific environmental targets. The scale and longevity of the project are key enablers, which empower Tier 1 contractors and their supply chains to innovate and challenge the status quo when delivering their portfolios. Carbon emissions and sustainability now sit at the forefront of local, regional and national policy making, and the same is true of major infrastructure projects.
This paper is presented as part of the works to deliver the Enabling Works Contract (EWC) on the southern section (Area South) of High Speed Two (HS2) which includes demolition of buildings within the wider Euston area, utility diversions, environmental and ecological monitoring and a programme of historic environment and archaeological activities, delivered by the Costain Skansja joint venture (CSjv).
Delivery of an exceptional portfolio of works requires an exceptional approach. The enabling works in Area South are scheduled to be completed over a three-year period, providing ample opportunity to drive innovation and change, which can subsequently be deployed across the line of route during main works construction.
The Area South scope of works consists of the large-scale demolition of thirty buildings, multiple utility diversions, extensive environmental and ecological monitoring and a programme of historic environment activities, which included the largest archaeological excavation and exhumation of human remains to take place in Europe, at St James’s Gardens in Euston.
To successfully deliver this complex portfolio of activities in line with the High Speed Rail Act (London to West Midlands) 2017, and drive the team to exceed the challenging environmental targets, it was vital that the newest, most efficient and environmentally sustainable plant and equipment was sourced and deployed to site.
Environmental minimum requirements and the driver for sustainable project delivery
Supply chain selection started early with key partners being identified in early 2017. Central to the delivery of a complex project like HS2 is identification of market leaders, innovators and a supply chain who will help fulfil the client expectation and will meet (and where possible exceed) the project Environmental Minimum Requirements (EMRs) and EU standards.
The HS2 Environmental Minimum Requirements (EMRs), are the set of documented commitments to reduce the environmental impacts of the project. In particular, the HS2 Code of Construction Practice (CoCP) sets out the principles and control measures to be implemented on all site activities and are based on industry best practice; in the case of air quality they actually go beyond current industry best practice. The CoCP ensures “provision of effective planning, management and control during construction to control potential impacts upon people, businesses and the natural and historic environment.”
With historic environment works taking place on such a large scale, the CSjv Environment and Sustainability Opportunities matrix (E&SOM) became a key tool for understanding impacts and developing opportunities at the design phase, particularly for activities in St James’s Gardens. This included a clear overview over plant type, management, frequency of movement and power supply.
Bulk movement and excavation of materials was the focus of a multi-disciplinary E&SOM workshop during design stage along with how this could be managed with minimum impact and maximum innovation. Early identification ensured that these findings and opportunities were carried through the design phase into the construction and archaeological excavation phases. Team members were empowered to implement best practise and engage with innovative solutions through the whole lifecycle of the project. The outcome was the alignment of environmental specialists, generalists and the forward-thinking project managers and front-line supervisors and a desire for continuous improvement.
One of the key requirements within the CoCP is air quality and the need to drive down air quality impacts from the emissions of operational machinery through the stipulation of Non-road Mobile Machinery (NRMM) emission standards specific to the HS2 Project. These standards are based on the Greater London Authority’s (GLA) NRMM emission standards framework but are even more stringent, requiring the use of ‘cleaner’ machines – a first for the construction industry throughout the UK.
The project team took advantage of the early opportunity to quickly identify which plant was immediately available and which products were still at prototype phase. The suppliers were then challenged to see which machines could be brought to market in a quicker, and more streamlined manner. The 1.9-tonne non umbilical electric mini digger was one such asset. The project team resolved to communicate openly with the supply chain, providing a clear assurance to all parties that innovation was actively sought and welcomed.
By delivering direct assurance that we would support then in delivering and using new equipment and by providing on-site quantitative and qualitative feedback the supply chain was empowered to effect immediate change. They could confidently invest in state-of-the-art clean technology with higher CAPEX outlay if it supported the project EMRs and a wider UK move toward hybrid, all electric and hydrogen powered plant and equipment.
It quickly became apparent that there was a limited supply of available equipment which complied with client Euro Stage IV Non Road Mobile Machinery (NRMM) emissions for plant weighing in at ten tonnes and above and that a wider piece of industry collaboration was needed to drive the urgency in getting this plant to market to support operational delivery.
One of the key principles contained within the EMRs is to use reasonable endeavours to adopt mitigation measures that will further reduce any adverse environmental impacts without adding unreasonable cost or delays. In the spirit of this principle the St James’ Garden site team aimed to further reduce the air quality impacts from the emissions of its operational plant by working closely with the supply chain to deploy even cleaner machines, including:
- Electric powered,
- Euro Stage IV hybrid; and
- Since November 2019, new Euro Stage V machines thereby exceeding expectations.
To be assured of a meaningful change, the project team had to identify and provide suitable and sufficient trial locations to set the supply chain up for success. Where electric plant is concerned this inevitably necessitates provision of correctly designed and positioned infrastructure including charging points and lay down areas. One of the most important considerations was strategic planning to prevent electric plant from being stranded if it ran out of charge.
Figure 1 shows the first-to-market 22-tonne hybrid excavator deployed for loading of wagons thereby ensuring it was principally operating on its electric function within the encapsulation structure.
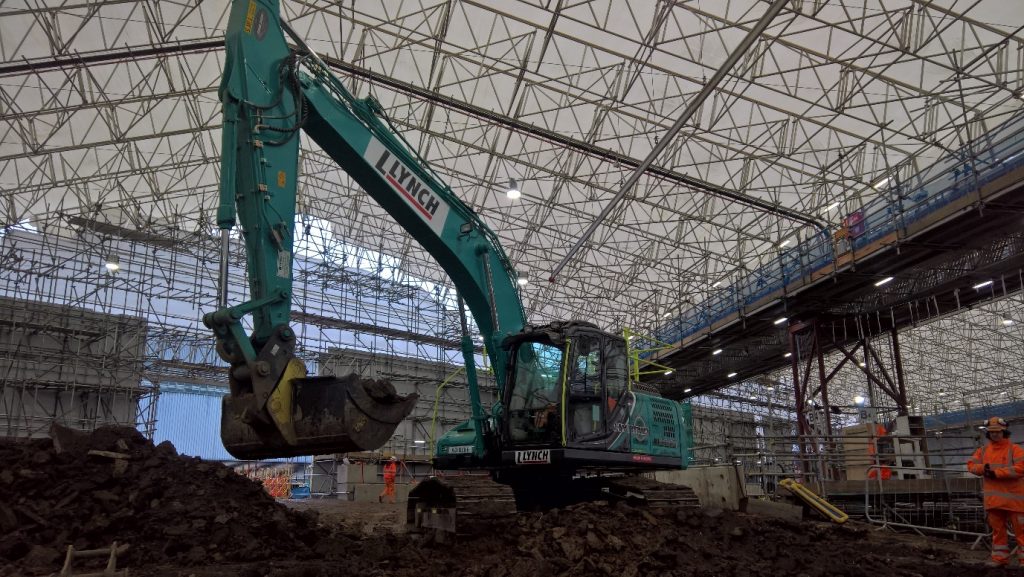
Selecting the correct site and tools for the job
The former post-medieval burial ground site of St James’s Gardens at Euston was identified as the principle operational viability study area for a variety small plant and larger 22-tonne hybrid excavators because of the longevity and complexity of the project activities and the sheer volume of material to be managed and excavated (34,857m3 of London Clay was excavated from the site during the first phase of works).
The majority of prototype and new-to-market plant was assessed off-site to better understand the potential benefits. This also gave the opportunity for the operational teams to work with the supply chain in identifying and reducing or removing any safety risks identified at trial phase. It was vital that this was done before the equipment was deployed amongst the site teams in Central London.
Plant and equipment were inspected and put through its paces at various off-site testing grounds by the Plant Steering group, a panel of experts from different construction backgrounds (Figure 2). Drawing on interdisciplinary knowledge including safety, carbon strategy, operational management, sustainability and functionality the expert scrutiny of the group allowed a measured, quantitative and qualitive approach to determining the best plant for the job and the most effective sites for trials and ultimately, deployment. This provided an opportunity to scrutinise the plant and determine any changes which might be required. All plant was put through a plant inspection process upon arrival to site and on-site training given to site operatives where CPCS training was not mandated.
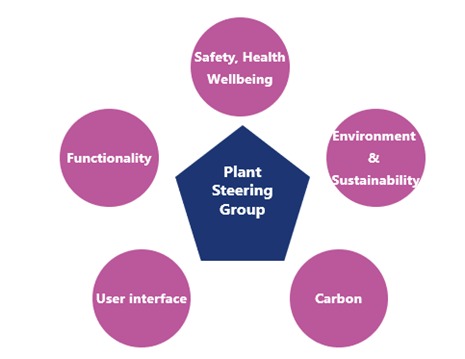
The 1-tonne electric ride-on dumper provides a good example of continuous improvement and collaborative innovation. Originally the 1-tonne electric tracked dumper was equipped with a scissor lift function which, when deployed lifted the hopper to an elevated position allowing materials to be placed in skips. This function was not required on site, as all spoil material was to be stockpiled, segregated, and sustainably managed. Therefore, it was determined that this facility should be disabled to eradicate the risk of pinch points.
At the same time the site foremen discussed the need to eliminate manual loading (the hoppers of the 1-tonne barrows sit higher than standard small manual wheelbarrows and are therefore more difficult to load) and communicated this to the suppliers and manufacturers who took this on board, and added a front shovel loading tool which completely eradicated the need for manual loading by the archaeologists.
The number of charging stations was initially determined based on the estimated number of small electric dumpers required for the works, because it quickly became apparent that these, and the two 1.9-tonne all electric non-umbilical excavators would become the most utilised pieces of plant because of their battery longevity and agile nature which was well suited to moving amongst the archaeological features and areas of excavation. Charging was facilitated by a single Euro Stage IIIA diesel generator, however this facilitated the immediate charging of 25 pieces of plant over the day to day site activities with an overall measurable reduction in carbon emissions of 139.765tns C02e.
22-tonne hybrid excavators were identified as being the most efficient way of combining the necessary power and sustainability inside the encapsulation structure. Hybrid power limited emissions during specific operations such as continuous slewing to load wagons. The roof clearance was designed to accept this large piece of plant without risk of impact. This was further mitigated as the daily reduced dig meant that the base of the excavation was progressively getting further away from the roof line, day by day.
Modified 1-tonne all electric ride on mini dumpers with front loading mechanisms were used widely across site to replace traditional hand barrows which are normally deployed by archaeological teams.
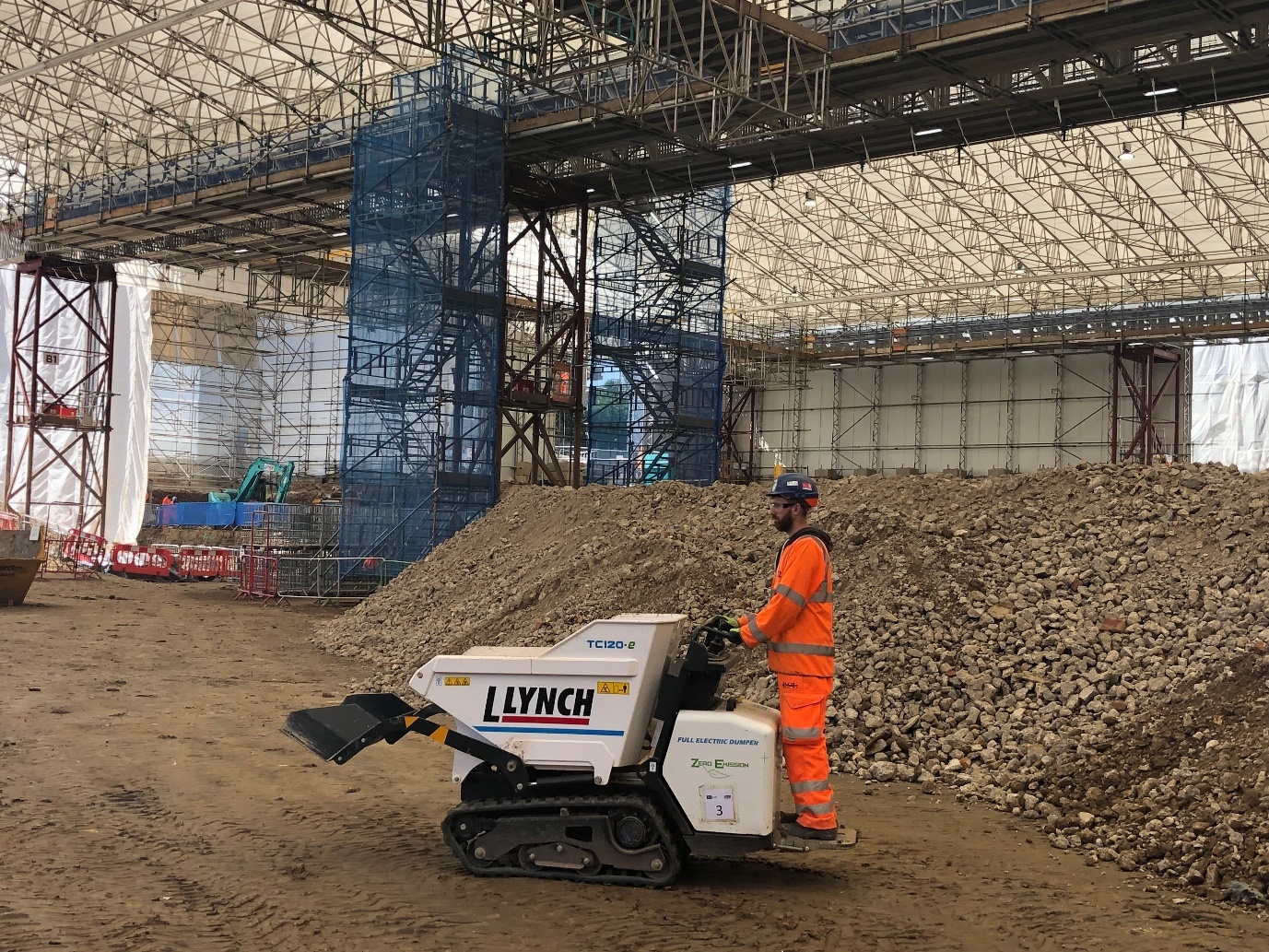
St James’s Gardens is located directly to the west of Euston Station and sits within the footprint of the proposed new Euston Station development. As such it also sits within the Greater London Authority (GLA) Central Activity Zone (CAZ) and therefore the highest emissions standard of Euro Stage IV applies. Since commencement on site at St James’s Gardens in summer 2017, all plant deployed on the site, without exception, has met this emission standard. This achievement is notable for being more than three years ahead of programme for the implementation of the equivalent GLA NRMM requirement for Euro Stage IV which comes into effect in September 2020.
Figure 4 is the plan showing location of St James’s Gardens in relation to Euston Station and neighbouring residential areas and work sites (courtesy of HS2 Gviewer)
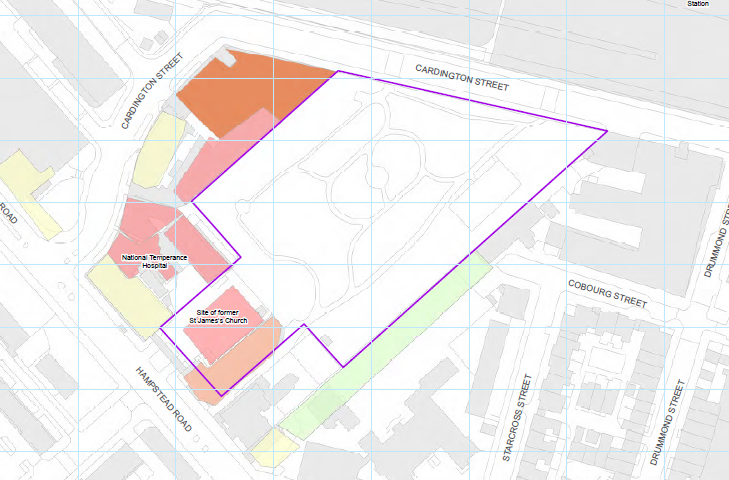
St James’s burial ground was in use between 1789 and 1853, when it was closed as result of the Metropolitan Burial Act[1]. The site acted as an extra-parochial burial ground for the parish of St James’s in Westminster and the Grade I listed church still stands proudly today on Piccadilly, not far from the Royal Academy.
The historic record indicates that around 61,000 burials were interred on the site, with the burial ground being divided into four grounds according to class (upper, middle, lower and pauper’s grounds). The site became a public park and was managed by the Vestry of St Pancras following the expansion of Euston station in the 1880’s, when roughly twenty percent of the site (the majority of the pauper’s ground and likely the most populous area of the burial ground) was subsumed by the additions of platforms 17 and 18.
Scant evidence of the burial ground remained aside from 128 partially-buried funerary monuments including two Grade II Listed monuments. The majority of these were no longer in situ having been impacted by both the Victorian desire to “civilise” the site to make it more aesthetically pleasing, coupled with the adverse effects caused by bombing of the area around Euston Station during World War II.
Historic England and specialist groups including the Advisory Panel on the Archaeology of Burials in England (APABE) provide expert support and guidance on projects of this scale. Their recent 2015 guidance “Large Burial Grounds: Guidance on sampling in archaeological fieldwork projects”[2] provides detailed advice on sampling from large assemblages of human remains for research purposes, however very little has been written to guide the process of how to manage archaeological excavations of this size in terms of safety and occupational health and wellbeing, logistics or spoil and materials management.
Ensuring the care, dignity and respect of the deceased are the primary drivers in delivering projects associated with the excavation or handling of human remains from any time-period. On a project of this scale there is also an increased need to consider the safety, occupational health and wellbeing of the specialist archaeology and exhumation team delivering the works. Such labour-intensive activities carried out by a large specialist team had the potential to be a high-risk area for occupational health issues including Musculo-skeletal injuries, slips, trips and falls and fatigue to name but a few.
Figure 5 provides a view of how the site was covered. The site was encapsulated using system scaffold and 15no bespoke hot rolled steel tower legs. This ensured compliance with legal requirements however encapsulation increased the need for clean fuels and electric plant.
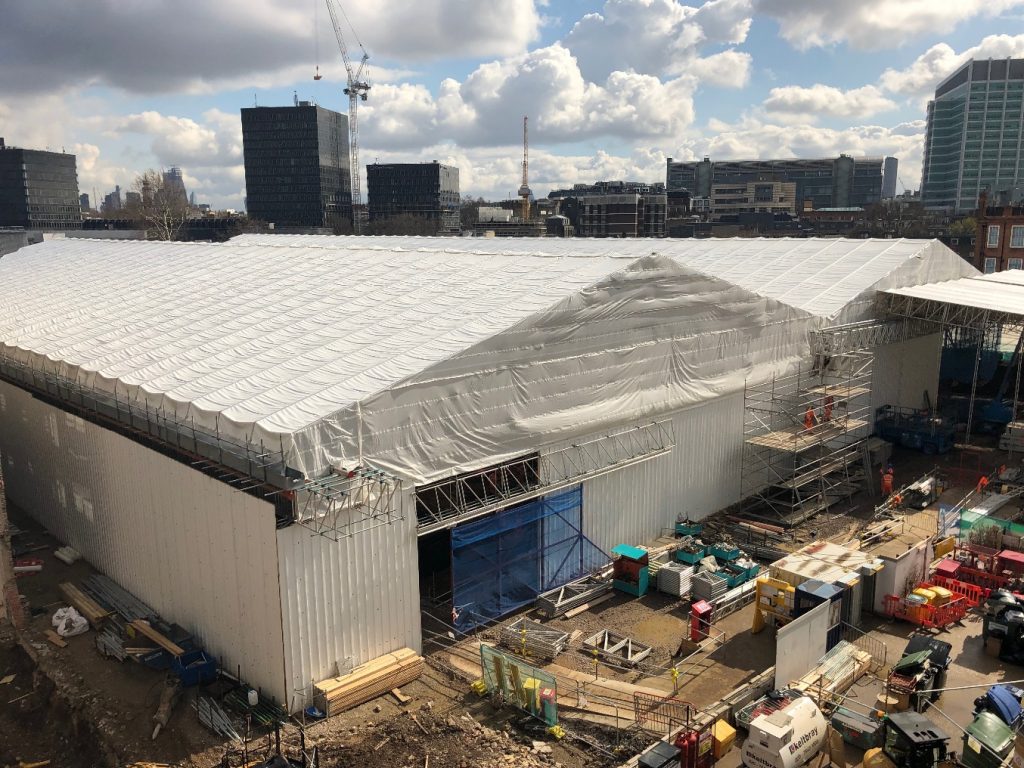
The site was encapsulated using a complex bespoke scaffold structure to ensure compliance with the relevant Undertakings and Assurances, and in line with requirements set out by the Church of England. Encapsulation of the site increased the need to identify, select and deploy plant and equipment powered by clean fuels and in meeting this target, the need for costly bespoke ventilation within the encapsulation structure was avoided.
Below in figure 6 demonstrates the archaeological investigations at evaluation stage which served to reinforce the challenging nature of work manually excavating burials in consolidated London Clays.

Archaeology as a discipline has experienced limited change in some methodologies over the last 40 years, and traditional measures are often deployed without examining the potential value which could be added through interrogating new and developing technologies available within the wider construction industry.
This is, in part, because archaeology sits outside Construction Design Management Regulations and archaeological excavation often takes place without the interaction or direct management of a Tier 1 construction contractor in place. When this interaction does not occur the opportunity for shared learning and development of new processes or implementation of new technology and interdisciplinary learning is often lost.
Identifying and managing these occupational health risks was particularly significant on a site of this magnitude and duration, where all burials would be hand-excavated and subject to varying degrees of complex archaeological recording, assessment and analysis to support the academic research strategy set out in the HS2 Phase One Historic Environment Research Delivery Strategy (GWSI-HERDS)[3]. Hand excavation was mandated and the excavation methodology was agreed taking into consideration Schedule 20 of the High Speed Rail Act (London-West Midlands) 2017, Undertakings and Assurances, and the expectations of our key stakeholders including the Church of England, Greater London Archaeological Advisory Services and Historic England.
Early consultation with the specialist archaeological and exhumation contractors indicated that each discipline had its own benchmark volumetric for hand excavation within post-medieval burial grounds. The archaeological contractor indicated a rate of 1m3 per person per day was a reasonable assumption based on assumed levels of preservation and ground conditions (the site is cut into consolidated London Clay, a challenging environment for hand excavation). Similarly, the exhumation contractors indicated a likely rate of 2-3m3 per person per day in the same ground conditions.
Lean was identified as a tool which could be utilised to support management of the on-site archaeological works considering the manual labour, human factors, and electric plant. Lean was originally developed by the Japanese car manufacturing industry (specifically Toyota) in the 1960s and built upon the work done by Henry Ford who pioneered the moving production line in the early twentieth century. Archaeology is not a production line and no two archaeological sites are the same, however archaeology is a highly process-driven activity. Real benefit can be derived from identifying some, if not all of the eight wastes classified by Lean practitioners (in this instance waste does not refer to rubbish although eliminating unwanted, hazardous or costly by-products may be a desirable secondary outcome) including the wastes of motion, waiting and transport. Strategic deployment of electric plant contributed beneficially to limiting or eradicating these wastes.
A Lean control board was introduced as a management tool to benchmark daily progress against programme and ensure that there was a structured dataset around which to frame discussions regarding challenges and opportunities. This also aligned with the iterative process associated with the Environment and Sustainability Opportunities matrix which was developed by the Environment and Sustainability teams.
The shared ownership of this data created an open and honest platform for discussion and fostered a “no blame” culture. It was also key to recording the improvements in efficiency and productivity which were being delivered on site by a wider range of hybrid and all-electric plant, the majority of which was deployed for the sole purposes of supporting the archaeological excavation and the two-hundred-strong team of archaeologists, engineers, surveyors, scaffolders and site operatives who worked collaboratively to deliver the works.
Benefits of electric plant: reducing black carbon, and improving safety and productivity
The deployment of lower emissions machines on site has had both local air quality benefits and health benefits to on-site operatives.
Both Euro Stage IV and Euro Stage V machines emit up to 75% less Nitrogen Oxides (NOx) (g/kWh) compared to a comparable Euro Stage IIIB machine. Similarly, Euro Stage V machines also emit up to 40% less Particulate Matter (g/kWh) than both Stage IV and IIIB. Over and above that, the deployment of zero emissions electric machines clearly surpasses these requirements and provided 100% reduction in emissions.
During 2019, a study was carried out on-site by King’s College London, on behalf of HS2, to characterise the diesel exposure of workers on HS2 construction sites. It found that work exposures contributed the highest proportion of total black carbon exposure, over the monitoring period, accounting for 66% of participants’ total exposure during a working day. Black carbon is an indicator of incomplete fuel combustion, the primary source of which on-site was diesel exhaust. Elimination of exposure to black carbon where reasonably practicable within the wider construction industry is wholly desirable and beneficial to site operatives and the wider neighbourhood within which the construction team are operating. This forms part of a wider HS2 Innovation project looking at the reduction of NRMM emissions linked to construction activities. The site team within St James’s Gardens participated through the wearing of passive personal exposure monitoring to support the research.
Efforts were focused on providing as much mechanical intervention as possible. This helped to limit the time-consuming manual excavation element, permitting the specialist archaeological team to focus >75% of their time on task managing archaeological processes. This contributed toward eliminating occupational health issues as well as eradicating the eighth waste in Lean – the waste of talent, where time is spent on unproductive works unrelated to a person’s core skill or specialist ability. Archaeological teams are a finite resource and delivery of HS2 has absorbed a large percentage of available archaeological fieldwork teams along the line of route between London and Birmingham. Deploying electric plant to permit them to deliver archaeological works more efficiently was therefore of paramount importance. Safe and early completion freed the team to move on to other archaeological sites on the critical path.
By focusing the archaeological team’s efforts on key archaeological tasks and deploying the electric plant to manage spoil movement and ground reduction where archaeological activities had been completed, the archaeologists and exhumation contractors were able to manage their time more efficiently.
This also generated a marked upturn in productivity with the archaeological team delivering 5m3 per person per day on average at the peak of works and the exhumation contractor delivering productivity levels in excess of 6m3 per person per day at the peak of the works. This produced a marked effect on morale and occupational health. Zero occupational health related issues or incidents were reported in the on-site laboratories and zero incidents or issues associated with Musculo-skeletal disorders and manual handling were reported during the ten-month archaeological excavation.
Overall electric plant used
In total, eight of the 1-tonne electric ride on dumpers were deployed to site and when paired with one of the two 1.9-tonne all electric excavators were one of the most beneficial and widely used pieces of plant on the project. Their charge held for around six hours of discontinuous use and localised charging points permitted “booster sessions” during break and lunch times to extend their use life. The dumpers were agile enough to manoeuvre around archaeological features and reach localised work sites where they were filled by the 1.9-tonne excavators or self-loaded from the archaeologist’s small local spoil heaps using the front-loading mechanism.
The 1.9-tonne electric excavators also proved to be a great boon and expedited ground reduction increasing archaeological outputs. Initially, charge was found to diminish rapidly where challenging consolidated London Clay made digging difficult. This was fed back to the supply chain who were quick to recall the product temporarily and effect rapid modifications to double the battery capacity thus increasing both performance longevity, and power.
Hybrid excavators were identified as best placed for management of spoil at a centralised laydown area where material could be stockpiled and loaded from a central point. While hybrid excavators have now been available for more than a decade, their implementation is still not widespread. As with popular hybrid vehicles they have obvious benefits in terms of reduced emissions and fuel consumption and the subsequent air quality improvement. The 22-tonne hybrid was selected for its power and reach and as it operates primarily on electric-only when slewing it was given an optimal position which permitted the loading of wagons from a largely stationary position with slewing being the main form of movement. The 22-tonne hybrid excavator remained on site for a forty week period operating primarily on muck shift duties.
Six smaller 0.6-tonne all-electric wheelbarrows were also deployed however their four-wheeled design rendered them less flexible and more difficult to manoeuvre over the soft uneven terrain and their charging connections were found to be less robust. Suitability of materials and location of charging points built into machines was identified as a vital design element which, if inadequately designed, could affect the use-life and suitability of equipment. Failure of plug and charging points integral to machinery could easily lead to short-medium periods of downtime and inefficiency. These failure events were also recorded by the site team using the Lean control board in order to account for any downturn in productivity and to rule out human factors.
The site team was open to receipt of all new-to-market electric plant, where a function could be found for it and this led to the trialling of a total of eight different pieces of new-to-market or prototype plant in St James’s Gardens.
This project marks the start of a shift change in how large-scale archaeological projects can be delivered and aligned with major infrastructure projects. It also highlights that there are no real barriers to delivering innovation across a multi-disciplinary suite of activities if everyone is fully appraised of the strategic goals and potential benefits from the outset.
Encouraging direct dialogue with the plant supply chain should not be under-rated as the proactive relationship paid dividends in terms of access to new equipment and the willingness of the supply chain to invest with the surety that there was a market for electric and hybrid plant. It has also helped multiple suppliers and disciplines to collectively nurture and drive a clear set of sustainable goals and values. Ultimately the safe delivery of the project ahead of programme and under budget is testament to the approach led by Costain-Skanska JV and supported by HS2. The goal is to ensure that this learning is disseminated, and the powerful combined forces of plant manufacturers, suppliers and principle contractors can continue to grow and shape the shift towards a more sustainable future.
Table 1 shows the types, number and duration of electric plant trialled on site during the discharging of the archaeological works
Plant Type | No of items trialled | Activity type | Trial/ use Duration | Outcomes |
---|---|---|---|---|
1.9-tonne all electric non-umbilical mini excavator |
3 |
Archaeology Utilities General Civils |
40 weeks (6000 hours) | Deployed along line of route and adopted by other Tier 1 contractors on HS2 |
1-tonne electric track barrows |
8 |
Archaeology Utilities |
40 weeks (16,000 hours) | Deployed along line of route and adopted by other Tier 1 contractors on HS2 |
22-tonne hybrid 360 tracked excavator |
8 |
Archaeology Utilities General Civils |
40 weeks (16,000 hours) | Deployed along line of route and adopted by other Tier 1 contractors on HS2 |
Electric Road Sweeper |
1 |
General maintenance |
1 week (50 hours) | Not deployed due to limited availability in supply chai |
Electric 3-tonne dumper |
1 |
Archaeology |
2 weeks (100 hours) | Not deployed due to lack of requirement |
Electric front-loading shovel excavator |
1 |
Archaeology General Civils |
6 weeks (300 hours) | Not deployed due to limited power and battery life. Quantitative and qualitative feedback provided to supplier to expedite improvements |
Electric forklift |
1 |
Logistics |
3 weeks (150 hours) | As above |
Battery powered compactor plate |
1 |
General civils |
2 weeks (100 hours) | Not deployed due to limited suitability to task (geology and materials on site) |
Remote controlled electric bob-cat |
1 |
Demolition General civils and materials management |
1 week (50 hours) | Deployed for limited duration in line with programmed activities |
Other Vehicles |
No of items |
Activity type |
Trial/ use Duration | Outcomes |
Electric people carrier |
1 |
Staff transport Logistics |
130 weeks (6500 hours) | Deployed across parent company projects |
Electric 2-seater short wheelbase van |
6 |
Staff transport Logistics |
78 weeks (3900) | Deployed across parent company projects |
Hydrogen sprinter van 2-seater short wheelbase |
1 |
Staff transport Logistics |
130 weeks (6500 hours) | Retained however not yet part of parent company offering due to limited fuel supplies in Greater London |
Total No of items of all electric plant across project | Cumulative number of weeks | Cumulative number of hours | ||
33 | 473 | 55,650 |
Figure 7 shows the Encapsulation tower legs (fifteen in total). These were designed to accommodate local charging points eliminating the risk of stranded plant within the 11,000m2 site. By placing them at a high level within the infrastructure the temporary utilities were placed above the excavation limiting the risk of localised utilities strikes.
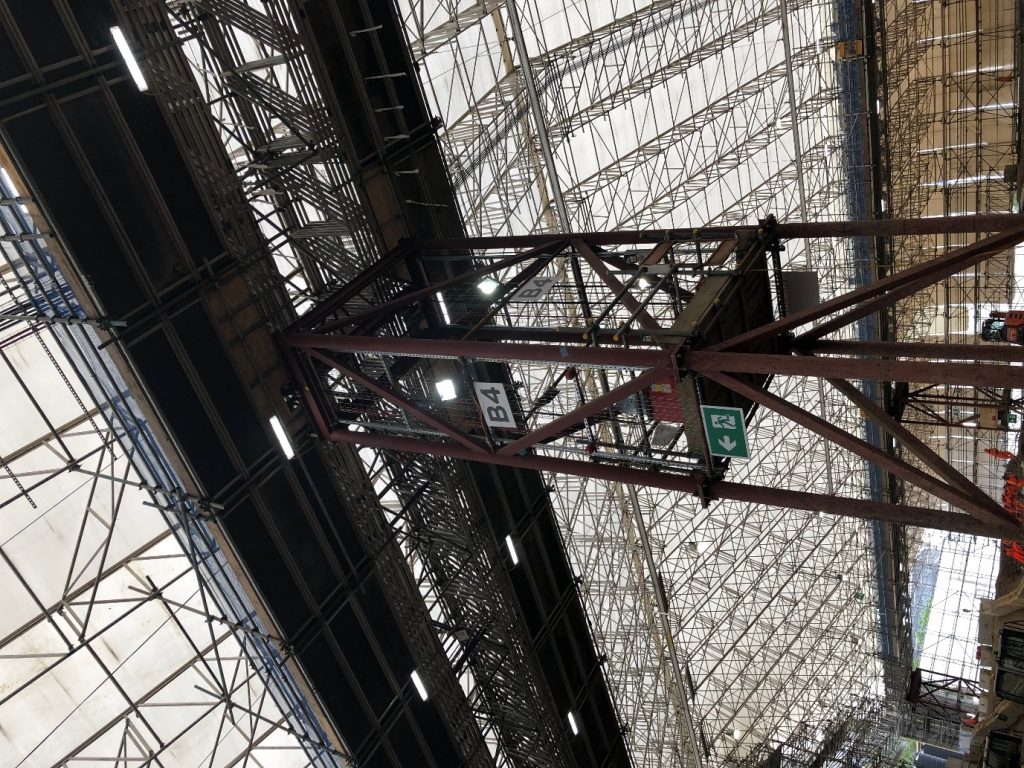
Conclusion
This project marks the start of a shift change in how large-scale archaeological projects can
be delivered and aligned with major infrastructure projects. It also highlights that there are no real barriers to delivering innovation across a multi-disciplinary suite of activities if everyone is fully appraised of the strategic goals and potential benefits from the outset. The team operating within St James’s Gardens offered a unique sub-set of cognitive diversity with the construction sector (engineers, construction managers, safety, health and environment specialists, archaeologists, LEAN planner and business improvement managers), which generated an opportunity to identify, adopt and deliver innovations in an interdisciplinary setting.
The importance of encouraging direct dialogue with the plant supply chain should not be under-estimated. The proactive relationship paid dividends in terms of access to new equipment and the willingness of the supply chain to invest with the surety that there was a market for electric and hybrid plant. It has also helped multiple suppliers and disciplines to collectively nurture and drive a clear set of sustainable goals and values as there was a clear message that they were values held by the Tier One contractors and by the client. Supply chain engagement also permitted an opportunity to proactively review plant operability and suitability before it was deployed to site. At this stage subtle mechanical and electrical changes could be made which reduced risk and eliminated hazards at an early stage.
Despite the power source for Phase One of the works being a single Euro Stage IIIA generator, the presence of electric plant eradicated fifteen diesel engines from site activities for a period of forty weeks. Phase Two works are in preparation with the switch to full electric being made and the single generator replaced with mains power.
Huge benefits were realised in terms of archaeological productivity where physical activities linked to local excavation and spoil management were increased by a factor of 5 at the peak of works. The selection of small electric plant to support the manual excavations within the burial ground allowed the archaeological team to focus on delivering high quality archaeological outputs including a detailed record to support academic research and the HS2 Generic Written Scheme of Investigations – Historic Environment Research Delivery Strategy (GWSI-HERDS) which guides the archaeological process along the line of route.
Ultimately the safe delivery of the project ahead of programme and under budget is testament to the approach led by Costain-Skanska JV and supported by HS2. The goal is to ensure that this learning is disseminated, and the powerful combined forces of plant manufacturers, suppliers and principle contractors can continue to grow and shape the shift towards a more sustainable future.
Acknowledgements
The authors would like to thank HS2 for their support during this venture. They would also like to thank the wider Costain-Skanska JV team for their support throughout the course of the works and supply chain members LLynch, M O’Brien and Flannery Plant hire for their collaborative support and expert input. The authors would also like to extend thanks to the wider specialist supply chain within St James’s Gardens including MOLA-Headland Infrastructure, TCS Exhumations, Palmers Scaffolding Ltd and Bowercross Construction Ltd.
Thanks are due to the award winning St James’s Gardens construction and engineering team; Michael Eborn, Andrew Alexander, Myles Johnstone, Arty Taylor, Kearney Sullivan, Aaron Murphy, Michael Ridley, Shannon O’Keeffe, Mark Ballard, Ette Roberts, Richard Martin, Amy Kwok, Jason Bicknell, Andrew Foster, Abid Noori, Alganit Tabir, Ben Lennon, James Todd, Taylor Mack, John Greggains, Daniel Suttie, Polly Gourlay, Woan Teng Lee, James Beard, Charles Nicholson and Robbie McCabe.
References
[1] Burial Act of 1852. An Act to amend the Laws concerning the Burial of the Dead in the Metropolis
[2] Mays, S et al. 2015. Large Burial Grounds: Guidance on sampling in archaeological field work projects (APABE). Historic England Publishing
[3] HS2 2017. Historic Environment Research and Delivery Strategy Phase One
Peer review
- Mark Fenton, Climate change Specialist-CarbonHS2 Ltd
- Andrea Davidson, Air Quality LeadHS2 Ltd