Reducing emissions in construction: Non-road mobile machinery retrofit
The latest London Atmospheric Emissions Inventory published by the Greater London Authority, indicated that Non-Road Mobile Machinery (NRMM) is a significant source of air pollution. This poses health risks and contributes to poor local air quality.
To reduce emissions linked to construction activities, HS2 has set stringent engine emission standards for all plant and machinery across the programme. As part of the HS2 innovation programme, a retrofit solution was developed and was the first certified solution. This adds exhaust technology to existing engine systems on plant machinery to upgrade them to meet the latest engine emission class, reducing pollution and leading to cleaner air around construction sites.
The retrofit solution was fitted and trialled on a piling rig and rotary rig. The solution was tested to quantify the emission saving potential of the system.
The results were validated and certified making the solution available industry wide. By reducing emissions and embodied carbon, benefits are realised for the environment, communities, and workforce. In addition, bringing significant direct capital savings of up to £300million on the HS2 programme through the reduction of plant scrappage and the need to purchase high volumes of new large specialist plant.
Introduction
Air quality is important for human health, wellbeing, and the environment. The World Health Organisation (WHO) estimates air pollution as the biggest environmental risk to health, carrying responsibility for about one in every nine deaths annually[1]. As pollution continues to rise at an alarming rate, air pollution has been emphasised as a public health emergency affecting economies as well as quality of life.
The High Speed Two (HS2) Air Quality Strategy aims to raise the bar on emission standards and to share new knowledge as a legacy for future projects[2]. It is aimed to avoid emissions, but where this is not possible, key requirements have been set to ensure emissions are reduced through control measures so that public and workforce exposure is minimised.
While HS2 is ensuring all works are undertaken following Best Practical Means in reducing emissions, it is important to continually ensure that these measures are effective through management, monitoring and mitigating against potential emissions. One mechanism HS2 uses to ensure the Air Quality Strategy objectives are achieved throughout construction is through the implementation of stringent engine emission standards for all plant and machinery, as outlined in the HS2 Code of Construction Practice (CoCP)[3].
To meet these requirements many contractors would need to replace or repower older plant, which can be both a slow and costly process, especially for some of the largest machines that have the longest lifespan within the fleet, such as crawler cranes and piling rigs.
In a bid to ensure all NRMM used across the HS2 programme meet or exceed the HS2 stringent NRMM emission standards, through the HS2 innovation programme, HS2 worked with UK manufacture Eminox Ltd. (Eminox), HS2 Main Work Civil Contractor (MWCC) Balfour Beatty VINCI (BBV) and Imperial College London to develop, trial and test an NRMM retrofit solutions which adds after exhaust technology to existing engine systems on plant machinery to upgrade them to meet or exceed the latest EU Emission Stage leading to cleaner air around construction sites.
Non-Road Mobile Machinery Emissions
The National Atmospheric Emissions Inventory (NAEI) highlights the construction industry as a key source of air pollutants across the United Kingdom, with exhaust emissions from Non-Road Mobile Machinery (NRMM) diesel equipment being a significant contributor[4].
NRMM is defined as any mobile machine, transportable equipment or vehicle, with or without bodywork or wheels, not intended for the transport of passengers or goods on roads, and includes machinery installed on the chassis of vehicles intended for the transport of passengers on roads[5]. Emissions from engines in these machines are regulated under Regulation (EU) 2016/1628 in Europe[5].
The NAEI estimates that NRMM exhaust emissions contributed 14% of PM2.5 (2nd largest source) and 7% of the total NOx (4th largest source). Further to the estimates produced by the NAEI, more robust data models were created for London, to inform policy development.
A London Atmospheric Emissions inventory (LAEI) is produced at a 1km resolution[6]. NRMM emissions are allocated as a proportion NAEI (based on employment in the construction sector) and distributed geographically using the London Development Database[7]. The 2016 London Atmospheric Emissions Inventory (LAEI) estimates that, NRMM diesel equipment contributed 7% of the total NOx emissions – 5th largest source (Figure 1), 34% of the total (including fugitive dust) PM10 – the largest source (Figure 2), 15% of PM2.5 – 3rd largest source, and <1% of CO2 – 6th largest source of emissions across London[8].
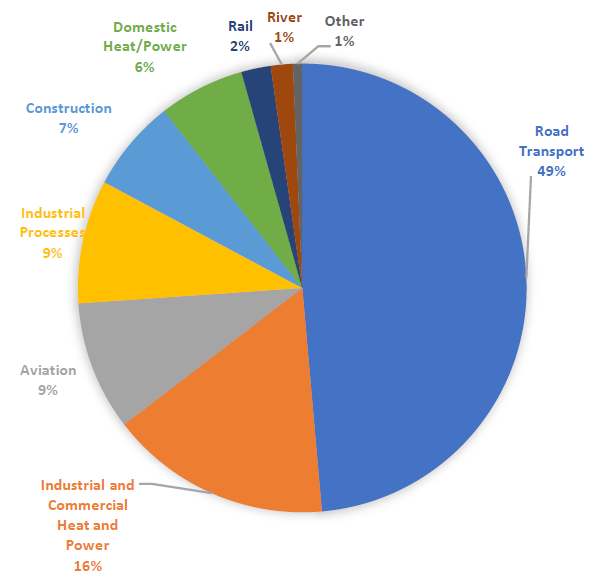
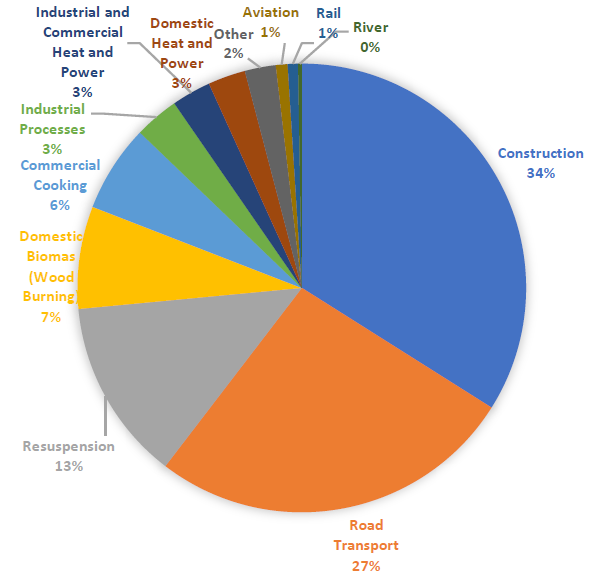
Since most NRMM engines have relatively longer life spans than on road vehicles, it is not uncommon to find machinery with older engines being used in the construction industry, which do not adhere to the current emission standards set by either the Greater London Authority (GLA) or HS2. This has major implications for the ability of national, regional and local governments to comply with legislation. Further, the construction industry is unnecessarily exposing its employees and local communities to increased concentrations of these harmful pollutants.
HS2 have set minimum engine emission requirements for all NRMM with an engine power of between 37kW and 560kW. From 01 January 2022, these include Stage V within the Central Activity Zone, and Stage IV[1] within Greater London and the rest of the country.
Eminox Solution
Eminox has developed reliable and robust exhaust after treatment systems that provide an economical route to meeting stricter emission compliance. Eminox Retrofit SCRT® emissions systems (Figure 4) are certified by the Energy Saving Trust, through the NRMM Retrofit Accreditation Scheme (RAS) to upgrade existing engines to meet EU emission Stage V equivalence.
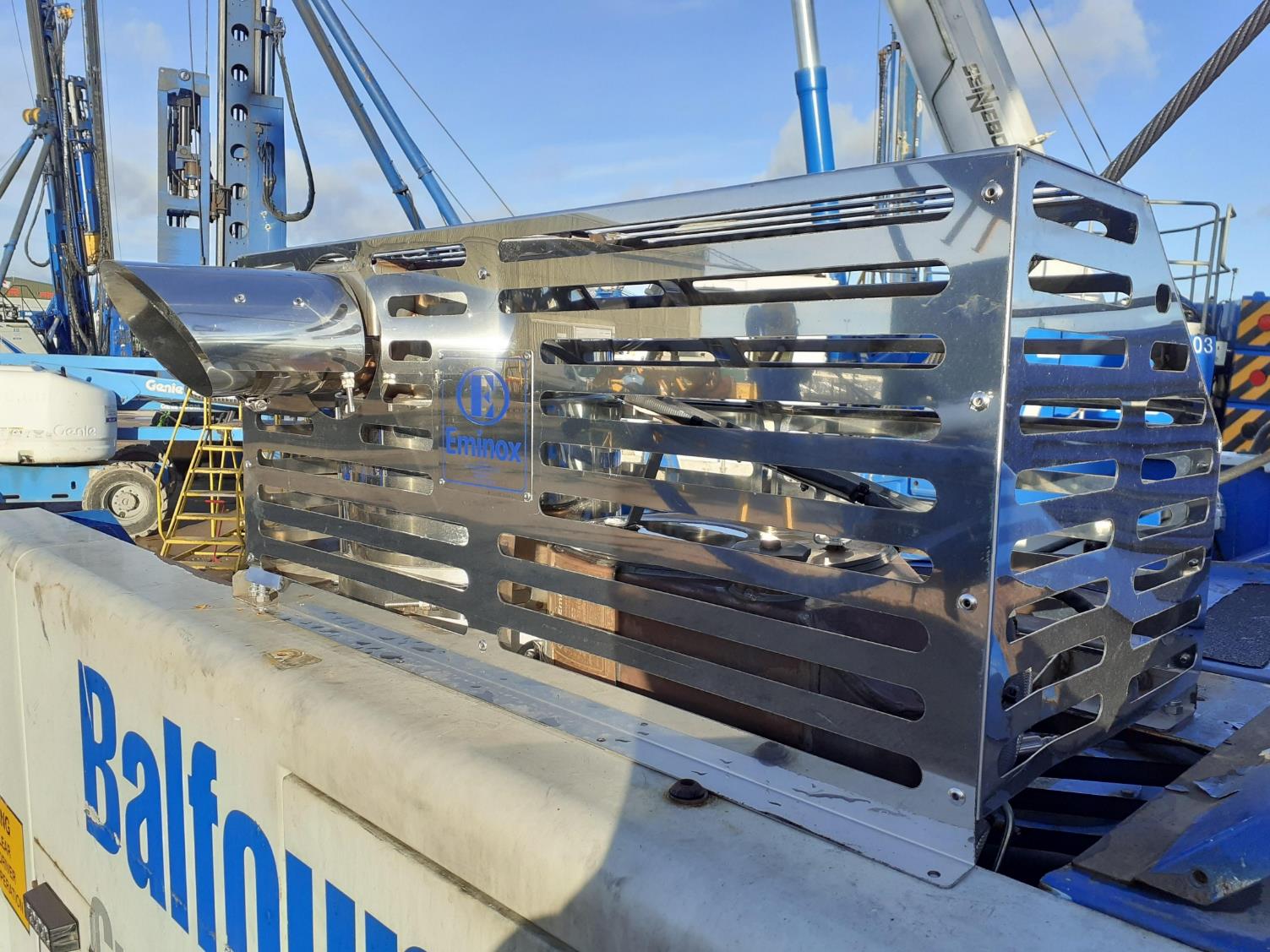
Eminox EMx S5 Technology
The Eminox EMx S5 NOx abatement system is the first product to be approved through the NRMM RAS which brings an EU emission Stage IIIA engine to meet EU emission Stage V equivalence. It comprises of (Figure 5):
- DOC (Diesel Oxidation Catalyst) – which burns hydrocarbons (HC) and carbon monoxide (CO) and converts nitrogen oxide (NOx) into nitrogen dioxide (NO2) to enable the SCR process to take place as rapidly as possible.
- DPF (Diesel Particulate Filter) – which captures particles of HC and CO, which are then oxidised to produce CO2.
- SCR (Selective Catalytic Reduction) – which injects a liquid-reductant (ad-blue) agent through a special catalyst into the exhaust stream of a diesel engine.
- ASC (Ammonia Slip Catalyst) components – Catalyst converters reduce nitrogen oxide, which is converted into harmless substances of nitrogen gas (N2) and water vapour (H2O). Finally, a slip of catalyst deals with the ammonia residue and clean emission are discharged from the exhaust tailpipe
AdBlue/Urea is injected over the SCR catalysts with an airless dosing system to facilitate the reduction of NOx into CO2, N2 and H2O. The EMx S5 systems are also supplied with telematics for in-service remote monitoring, enabling close monitoring of system performance and maintenance requirements.
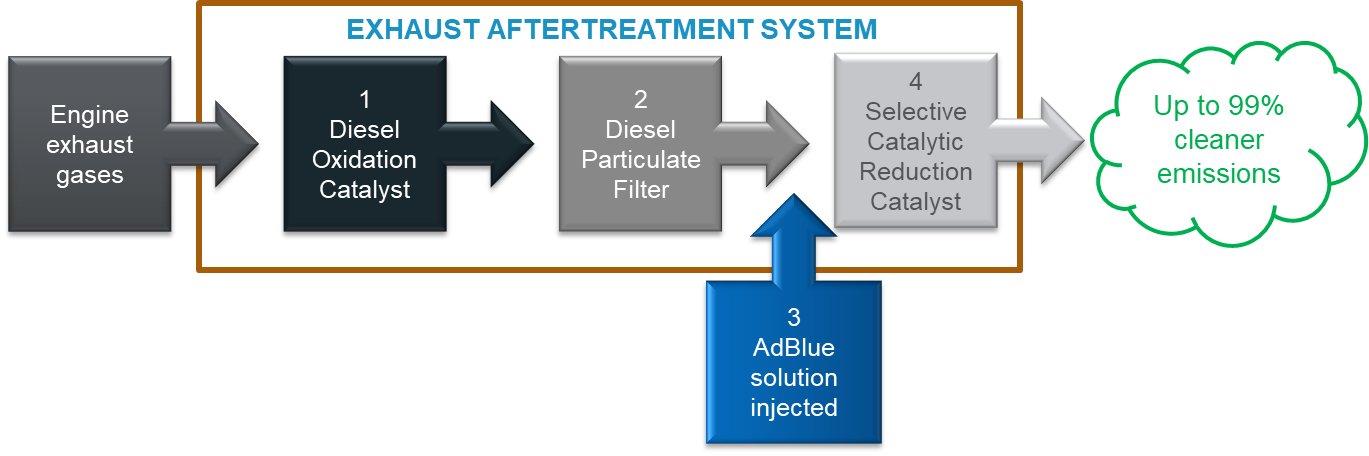
Trials
The Eminox solution was fitted to a BBV Stage IIIA Junttan PM20 Piling Rig (Figure 5) and a Stage IIIB Bauer BG30 Rotary Rig (Figure 6), to demonstrate the upgrading of both a medium and large engine band.
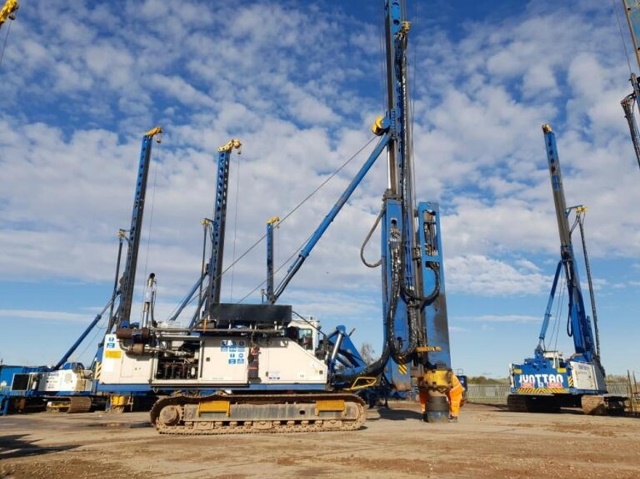
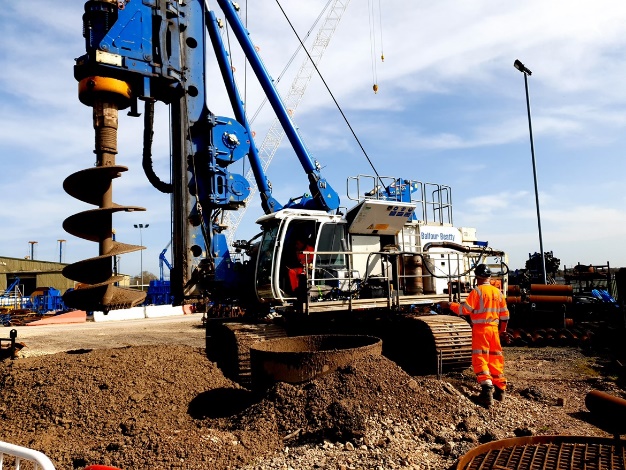
Emission Testing
Emission testing and data analysis was conducted by the Centre for Low Emission Construction (CLEC) at Imperial College London and Emissions Analytics. It demonstrated a significant reduction in emissions to exceed the latest engine EU emission Stage V standards, resulting in reduced pollutant exposure for the workforce and local communities.
Methodology
Transient test cycles were developed by the CLEC to be representative of real-world operation of the rigs[9],[10]. Each machine’s normal operational activity was broken down into several repeatable stages, these included machine idling, tracking, and pile driving or rotary boring.
The entire test cycle was repeated a minimum of three times, with emissions measured before and after the retrofit after exhaust treatment system was installed. All tests were conducted at Balfour Beatty’s ground engineering facility at Bottesford over two consecutive days in October 2020 (Junttan PM20) and March 2021 (Bauer BG30). Bottesford is home to Balfour Beatty’s Ground Engineering Expertise, where new techniques and equipment is developed to improve the design and installation of groundwork solutions.
The same machine operator was used for all tests to normalise for any behavioural changes. All tests were conducted using standard red diesel (EN590).
Tail-pipe concentrations of CO, CO2, NO, NO2, NOx, PN, and THC were measured by Emissions Analytics during the test cycles. Sensors Inc’s SEMTECH® portable emission measurement system (PEMS) was used to measure gaseous pollutants and CPN was used to measure particle number.
Exhaust mass flow (EMF) was also measured during the tests using a 5-inch SEMTECH high-speed exhaust flowmeter. The exhaust mass flow was also calculated from engine parameters (engine speed, intake air pressure, and intake air temperature) to correlate with the measured tailpipe exhaust mass flow. The EMF is required to covert the emission concentrations into mass-based concentrations.
Tailpipe emissions of CO, CO2, NO, NO2, PM, and PN were also measured using a 3DATX parSYNC integrated portable emissions measurement system (iPEMS) by CLEC. Measured emission concentrations from the iPEMS were used to compare with the measured emission concentrations from the PEMS.
Engine speed (rpm) and torque (Nm), was logged from the engine control module/unit (ECM/ECU) via the CAN-bus port by Eminox Ltd. This was used to calculate engine power (kW), to convert measured mass-based emissions to mass-based-per-power (g/kWh), for direct comparison with the EU emission standard limit values. Eminox Ltd also measured exhaust temperature and NOx concentrations from the pre-and-post integrated selective catalytic reduction (SCR) sensors.
The net rated power for the Junttan PM20 tested was 179kW @ 2000rpm (240HP), and for the Bauer BG30 tested was 403kW @ 1800rpm (540HP) therefore both were required to meet the NRE-v/c-6 standards for all pollutants.
Results
The results of the study indicated that the Eminox solution was successfully able to reduce NOx and PM concentrations in line with the EU Stage V expectations, which achieving the EU Stage V emission standards for all pollutants across all activities[9], [10].
The emission testing results are presented as boxplots in Figure 7 and Figure 8. When performing ‘real-world’ emission measurements on variable speed engines, it is not possible to exactly replicate the machine activity across each test cycle. In a laboratory or test-cell facility, a direct comparison can be made since the engine traces a specific load cycle. To overcome any anomalies and outliers that may occur due to operator behaviour or other variable, an inter-quartile range[2] on the measured data has been used.
For the Junttan PM20 indicated an overall-weighted average reduction percentage difference between pre- and post-retrofit of 77.28% for CO, 95.71% for HC, 83.74% for NOx and PN reduction of a 3-order magnitude. Following the same trend, the emission testing results for the Bauer BG30 indicated an overall-weighted average reduction percentage difference between pre- and post-retrofit of 29.9% for CO, 76.58% for HC, 94.16% for NOx and PN reduction of a 4-order magnitude.
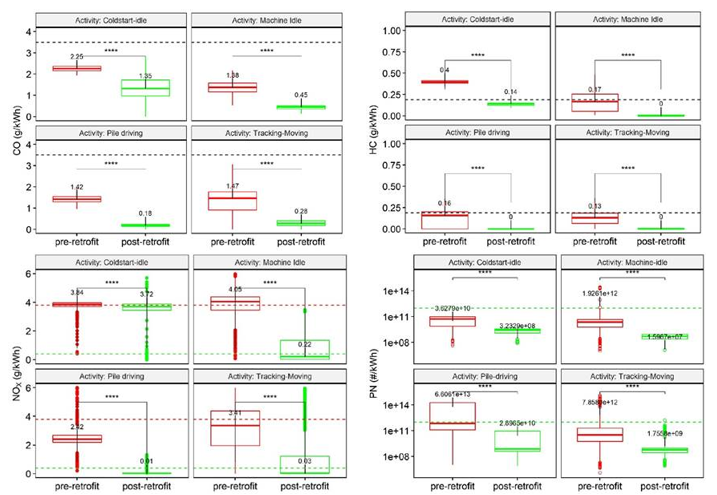
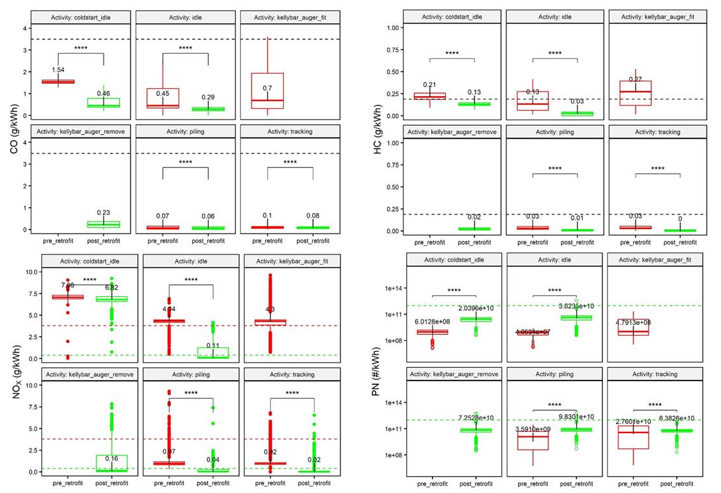
The Eminox EMxS5™ system has subsequently been successfully approved by the EST, as the first certified retrofit solution, and is now included in their NRMM retrofit accreditation scheme, making it available industry wide. This solution therefore supports the HS2 air quality objective of reducing emissions, minimising exposure and improving local air quality around construction sites.
Conclusion
The HS2 Air Quality Strategy aims to raise the bar on emission standards and to leave a legacy for future projects, the outcomes and lessons learnt from the trial have been shared across HS2 contractors.
Results from the trial have been validated and certified by the Energy Saving Trust, making the solution available industry wide. The success of the trial resulted in the certification the retrofit for all engine types in the medium and large engine banding irrelevant of the make or model.
This solution therefore bringing benefits to the environment, communities, and the workforce, by reducing emissions and embodied carbon, while also bringing significant direct capital savings through the reduction of plant scrappage and the need to purchase high volumes of new large specialist plant.
Implementation and rollout across HS2
HS2 has been working with the Manufacturing Technology Centre to support the adoption and rollout of retrofit solutions for existing plant and machinery across the project.
The use of retrofit technology will allow all HS2 contractors the opportunity to upgrade older machinery to meet the latest and more stringent HS2 emission standards without solely purchasing new equipment. This cost-effective measure allows for the HS2 low emission policy to be implemented and helps to bridge the gap in availability of the cleanest technology whilst the NRMM fleet is being renewed.
Due to the long-life use of many large machines a further legacy benefit will include the UK is left with a cleaner low emission fleet after HS2 is completed that will be used across other major projects.
As noted, the Eminox EMxS5™ system was the first solution successfully approved by the EST and is now included in their NRMM retrofit accreditation scheme, making it available industry wide. This has further opened the market to other retrofit suppliers, who have subsequently had their solutions certified and included on the NRMM retrofit accreditation scheme. This will allow for more rapid fleet retrofitting, as well as keeping the price of retrofit competitive.
An example of where this HS2 innovation is already yielding significant cost saving is through BBV who has already worked with Eminox to retrofit 19No. large earthworks equipment so far, with more scheduled in 2022. This has resulted in approximately £50 million cost saving and mitigated against programme delays linked to lead times of new plant.
The results of the work HS2 is undertaking with the Manufacturing Technology Centre will quantify the scale of saving across the programme, as well as provide a roadmap to prioritise retrofit for NRMM where challenges in meeting compliant plant demands across the HS2 programme. It is anticipated that this retrofit solution will save approximately £300 million in cost across the project.
A video of the solution and on-site trial is available to watch .
Acknowledgments
Balfour Beatty Plant and Fleet Hire
Balfour Beatty’s ground engineering facilities team at Bottesford
Bekir Andrews – former Sustainability Director at Balfour Beatty
Costain Skanska JV
Emission Analytics
Eminox Ltd.
Manufacturing Technology Centre
References
[1] World Health Organisation (2016). Ambient air pollution: A global assessment of exposure and burden of disease. Geneva: WHO document production.
[2] High Speed 2 Limited (2017) Air Quality Strategy Online.
[3] High Speed 2 Limited (2017) Environmental Minimum Requirement Annex 1: Code of Construction Practice. Online.
[4] National Atmospheric Emissions Inventory (2019). Online,Department for Business, Energy & Industrial Strategy.
[5] Parliament E. (2016) Regulation 2016/1628 on requirements relating to gaseous and particulate pollutant emission limits and type-approval for internal combustion engines for non-road mobile machinery. In: Parliament E, editor.: Official Journal of the European Union; 2016. p. 65.
[6] Beevers S. KCL urban model description, evaluation and outputs.
[7] Greater London Authority (2018). London Development Database Planning Permissions. In: Authority GL, editor. 2018.
[8] 2016 London Atmospheric Emissions Inventory [Internet]. 2018. Online.
[9] Desouza, C. and Marsh, D (2021). Junttan Piling Rig: Retrofit Emission Report. Centre for Low Emission Construction, Environmental Research Group, Imperial College London – Unpublished.
[10] Desouza, C. and Marsh, D (2021). Bauer BG30 Piling Rig: Retrofit Emission Analyses. Centre for Low Emission Construction, Environmental Research Group, Imperial College London – Unpublished.
- The following exemptions to this requirement apply: Stage IIIB for 37≤ P <56kW, as there is no corresponding Stage IV at EU level and Stage IIIA for constant speed engines of any power, as there is no corresponding Stage IIIB or Stage IV at EU level. ↑
- The inter-quartile range is a measure of where the “middle fifty” is in a data set. It is a measure of where the bulk of the values lie – the 25th to 75th quartile. The median is denoted by the 50th quartile, while the entire range is covered between the 0th to 100th quartile. ↑
Peer review
- Mike WhiteHS2 Ltd