Saving in Ground Granulated Blastfurnace Slag (GGBS) and alternative tests for high sulfate mixtures
Swell or heave of lime stabilised high sulfate material has been the cause of numerous high profile construction failures in the last 50 years. The formation of ettringite and thaumasite at temperatures below the standard laboratory temperature 20C (68F)±5C is commonly accepted to be the cause of the swell. The scope of this project involved assessment of alternative test methods including monitoring at lower than standard laboratory temperature with 10C (50F) chosen to represent site conditions. The purpose of this was to establish robust assessment methods to avoid defects being identified at a later date.
The standard approach in the UK to combating the effects of sulfate swell is the addition of ground granulated blast-furnace slag (GGBS) in the stabilisation process. Theproject described also aimed to prove that the ratio of lime:GGBS could be reduced, reducing cost, carbon and GGBS demand, the supply of which is at a critical level.
The work has validated the need to cure laboratory specimens at a lower temperature of 10C (50F) to detect potential failure mechanisms more effectively. However, due to the slower reaction of lime stabilised mixtures at lower temperatures, failure mechanisms were only detected at a much later age with the need for longer term monitoring. It is recommended that further research is required to develop an alternative or supplementary method to detect high swell swelling material than the currently available methods. Additionally, this work has shown that the reduced lime: GGBS ratio provides a resilient solution to sulfate swell, reducing overall binder required.
Background and industry context
Soil stabilisation primarily with lime has been a popular ground improvement technique in the UK since the 1970s [1]. Soil stabilisation is a process whereby the binder is mixed into the soil and compacted resulting in improved performance of the material. On HS2, due to the high speed of the trains extra consideration must be given to the dynamic resilience of the material and therefore the stiffness of the embankments is an essential characteristic.
Balfour Beatty VINCI (BBV) is the Main Works Contractor constructing the 90km Midlands section of the HS2 route, referred to as Area North. The Integrated Project Team (IPT) is made up of BBV, Mott MacDonald SYSTRA the Design Joint Venture (DJV), and HS2 Ltd.
Mainline South region stretches for approximately 45.5km from Southam to Coleshill through a mixture of rural and suburban landscapes including the 1.6km twin bore Long Itchington Wood tunnel. This region also includes Interchange Station, as well as crossing three major highways (A45, M6 and M42). The Central region runs from Delta Junction to the East of Birmingham into the city centre connecting to Curzon St Station via a series of viaducts. This Region, which covers a complex urban environment, includes more than 50% of the structures within Area North, the 5.6km twin bore Bromford Tunnel and new rail depot at Washwood Heath. Mainline North region runs for approximately 30km Curdworth to Handsacre through a mainly rural landscape from Coleshill and Tamworth towards Lichfield.
Area North (N1 and N2) has many earthworks embankments which will primarily be built using the material excavated from nearby cuttings, the majority of which are cohesive material. The earthworks technical standard prohibits the use of high plasticity cohesive materials within high-speed rail embankments or supporting foundations to mitigate the risk of potential shrinkage or expansion.
Lime stabilisation would normally be used to improve the engineering properties of site won cohesive material. The addition of lime to cohesive material results in cementitious bonds between particles and pozzolanic reactions which improve the long-term strength of the material. However, when gypsum, a sulfate containing compound, is present in the material, it reacts with the lime and compounds such as ettringite and thaumasite can form at temperatures below 15C. This comes with an associated expansion which causes the material to heave. Heave or swell of lime stabilised high sulfate material has been the cause of numerous high profile construction failures in the last 50 years [see references 1,2]. The formation of ettringite and thaumasite is commonly accepted to be the cause of the swell [3]. The mean annual air temperature in the UK is 8 to 10C (50F) which means most engineering earthworks fills will equilibrate to this temperature [4].
The industry standard approach to prevent swell of high sulfate materials is the addition of lime and GGBS in a ratio 1:3 [3]. GGBS is produced in blast furnaces as a by-product in the production of iron and steel. Many of these furnaces are coming to the end of their lifespans and being replaced with greener, electric arc furnaces which do not produce GGBS. As a result, the supply of GGBS in the UK is currently at a critical level with demand far outweighing the supply. This has led to a steep rise in the cost of GGBS as overseas import is being used to fill the shortfall [5].
Concern over potentially high sulfate levels of the Mercia Mudstone (MMG) geology (Figure 1) that underlies the majority of Areas N1 and N2 posed a significant risk prior to extensive ground investigation and this package of work. Published academic research [3] highlighted shortcomings in the standard assessment and testing methods to fully highlight the risk of expansion due to sulfate minerals.
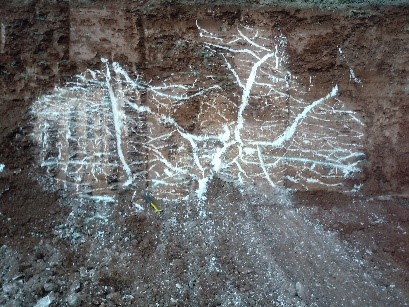
While lab testing is carried out under standard conditions of 20C (68F) ±5C, the Mean Annual Air Temperature (MAAT) is 8 to 10C (50F) [4]. The research from this paper highlights the increased expansion risk at these known lower temperatures and validates test methods to detect this risk more robustly. The work also explores whether GGBS can still provide an effective solution when used in lower proportions.
Approach
Mercia Mudstone Group (MMG) materials are known to have high sulfate levels and early ground investigation showed that some of the deep cuttings in N1 and N2 may reach the level at which gypsum veining is prevalent. A solution was required to de-risk the stabilisation of potential sulfate bearing soils to achieve the mass haul earthworks balance.
A package of work supported by £270,000 innovation funding from HS2 and consisting of extensive laboratory work was scoped out with the aim of assessing the risk and developing a robust strategy to combat sulfate swell. The following four interconnected packages of work were designed to achieve this aim:
- SECTION A: Comparing the effect of temperature on the swell characteristics of high sulfate materials.
- SECTION B: Assessing whether strength gain prior to contact with water could provide an effective mitigation to swell risk.
- SECTION C: Establishing the most effective method of measuring swell.
- SECTION D: Evaluating the impact of high sulfate groundwater on both high and low sulfate host materials.
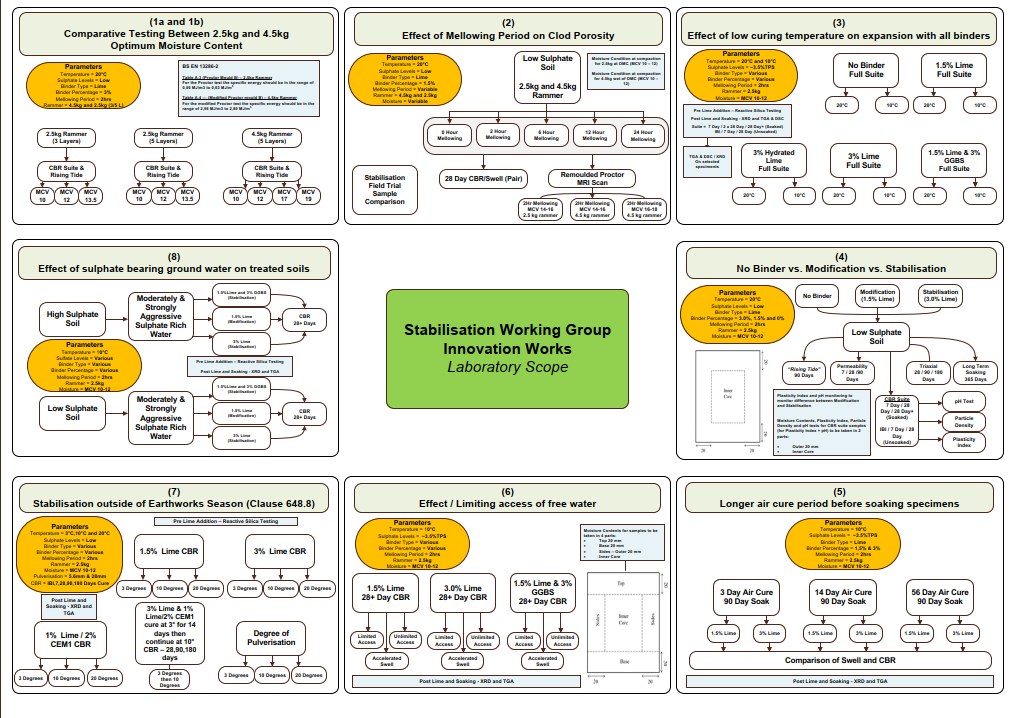
This work was part of larger set of 8 packages (Figure 2) of work related to lime stabilisation funded by the HS2 innovation fund. Prior packages established baseline lab preparation methods also used in this work. Please refer to “HS2 Learning Legacy – Saving Lime in Soil Stabilisation.”
Laboratory trials
The lab trial scope comprised three key stages:
- Characterisation of host material
- Baseline lab preparation methods
- Specific test and assessment methods
Characterisation of host material
A high sulfate host material was created in the lab by blending a high sulfate MMG with a low sulfate source. Samples from recovered borehole stems including some containing gypsum veining were used as no access was available to deeper cuttings to obtains bulk samples of high sulfate materials. Samples were ground down using a mechanical mixer pictured in Figure 3. Samples were then combined to produce a uniform material with a Total Potential Sulfate (TPS) of 3.5% by mixing different ratios of high and low sulfate material. The effectiveness of this mixing process in creating a homogeneous blend was validated by the low variance in TPS results of the blend. Table 1 shows the TPS results.
Sample number | Total potential sulfate (%) |
---|---|
E5722A | 3.24 |
E5723B | 4.11 |
E5724C | 3.39 |
E5725D | 3.45 |
E5726E | 3.48 |
E5727F | 3.60 |
E5728G | 3.90 |
E5729H | 3.60 |
E5730I | 3.69 |
E5731J | 3.36 |
Max | 4.11 |
Min | 3.24 |
Mean | 3.58 |
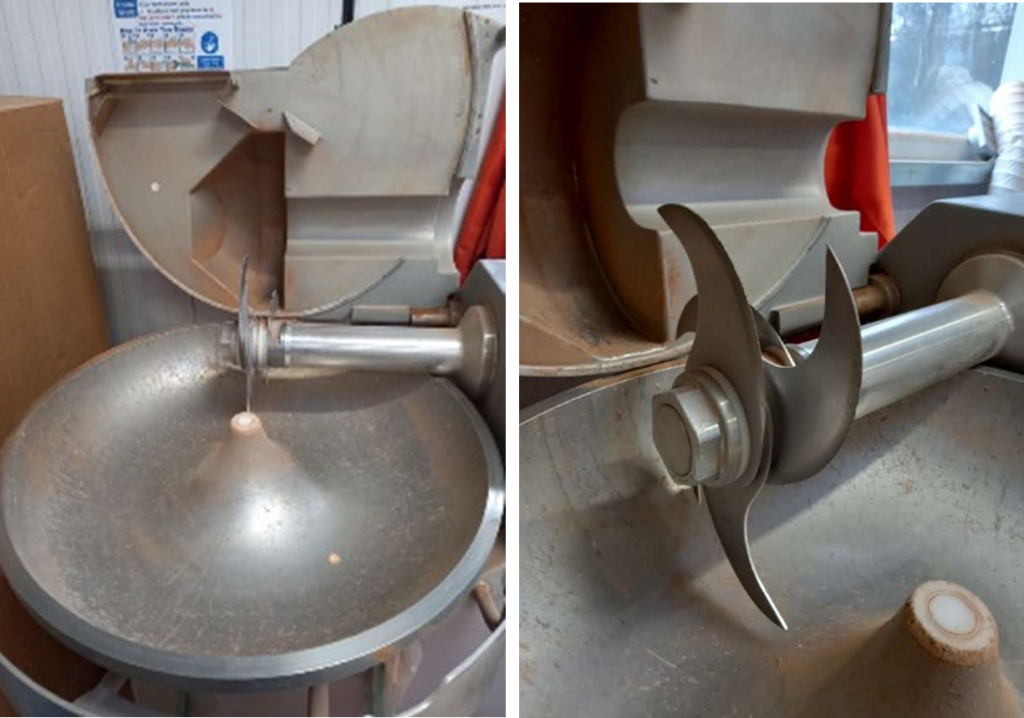
The characterisation results of the final blend are shown below in Table 2. The results show an intermediate plasticity soil suitable for lime treatment. However the material contains high sulfate content suggesting a high risk of swell when treated with lime.

Baseline lab preparation method
A baseline lab preparation method was established as part of the earlier packages of work referenced in “HS2 Learning Legacy – Saving Lime in Soil Stabilisation.” This methodology was proven to optimise durability of mixtures and reduce the risk of later water ingress hence contributing to risk mitigation for treating high sulfate soils. The outputs are summarised as follows:
- Compaction methodology – 2.5kg rammer
- Moisture condition – Moisture condition value (MCV) 10-12
- Mellowing period – 2 hours
SECTION A: Comparing the effect of temperature on the swell characteristics of high sulfate materials
This package of work sought to identify the effect of lower curing temperature on the assessment methodology to establish a robust means of identifying swell risk. The scope included comparison of treatment with varying binder additions with linear swell values compared on specimens cured at both 20C (68F) standard lab temperature and a reduced temperature of 10C (50F). Binder additions included both quicklime at two addition rates and hydrated lime as well as a lime plus GGBS combination at a reduced ratio of 1:2 compared to industry standard 1:3. Specimens were cured in water baths for up to one year.
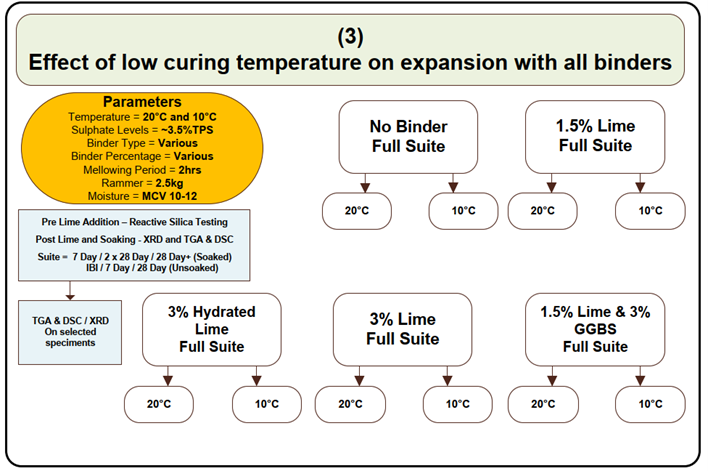
Soaked California Bearing Ratio (CBR) specimens with the below mix designs were soaked for up to a year at both 10C (50F) and 20C (68F). A temperature-controlled container unit was purchased and set at 10C (50F) to enable the samples to cure at the lower than standard laboratory temperature. Other samples were cured in the main laboratory at the standard 20C (68F). For the duration of soaking, the linear swell of the specimens was recorded daily, and the plot below shows the development of swell with time.
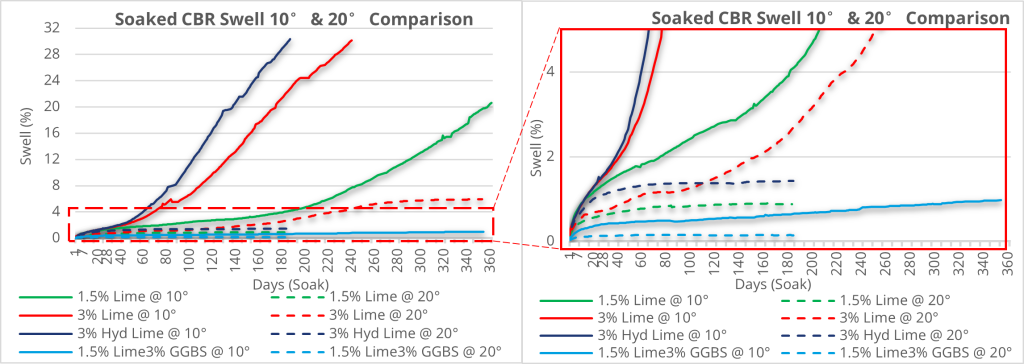
Figure 5 shows the swell plots for all specimens. The 3% hydrated lime specimens at 10C (50F) had the highest linear swell, reaching 30% after 180 days. These specimens reached the top of the mould collar and therefore the test had to be stopped before 365 days. The quicklime specimens both exceeded the specification linear swell limit of 3% however the specification specifies the limit should be reached by 28 days, at which point all samples would have complied. However, the significant increase in swell of samples cured at 10C (50F) occurred after around 40 days so a longer assessment period is also required compared to standard. The GGBS samples showed negligible swell after 365 days. On comparing the 10C (50F) results against the 20C (68F), at 10C (50F) the swell risk is heightened. The corresponding CBR results are presented in Figure 6 below.
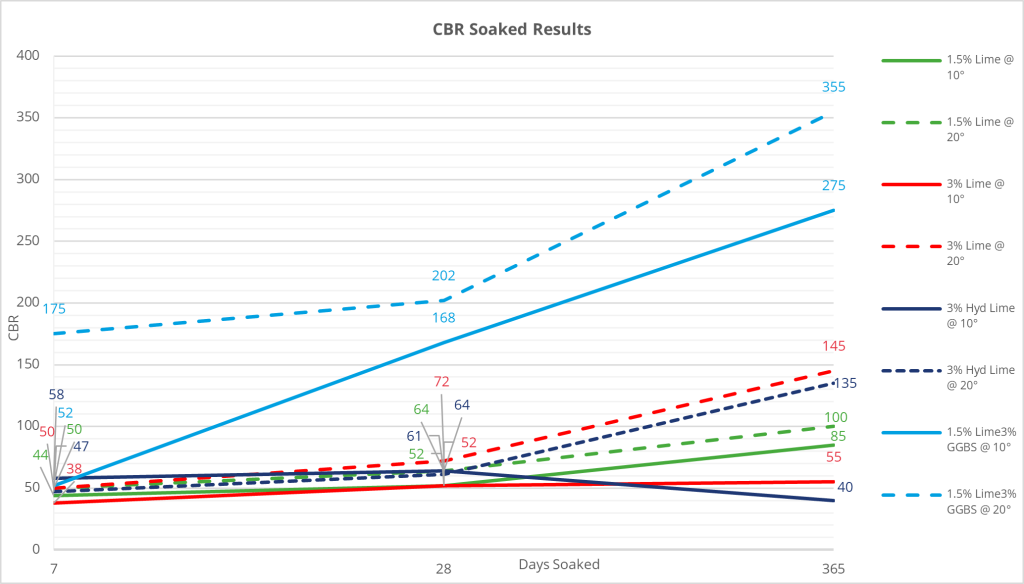
The CBR results of the high swelling specimens were low as expected. It is worth noting the reduction in strength in the 3% hydrated lime specimens at 10C (50F) was due to the high swell causing softening of the material. The 3% quick lime specimens at 10C (50F) gained negligible strength after 28 days reaching only 38% of the equivalent samples cured at 20C (68F). the samples treated with 1.5% lime at 10C (50F) reached 85% of the equivalent samples cured at 20C (68F) The samples treated with lime and GGBS exhibited the highest CBRs after soaking with the samples cured at 10C (50F) reaching 80% of those cured at 20C (68F).
Section A interpretation
This work validated the need to adopt 10C (50F) curing to fully identify the potential expansive behaviour. This method of curing at lower temperature was adopted for all the following packages for this work scope. Due to the lower temperature, slower sulfate bearing mineral crystal growth results in larger crystalline structures leading to a greater expansive reaction. While low lime content successfully treated the high sulfate materials when cured at 20C (68F) complying with the specification swell requirements, curing at 10C (50F) highlighted a significant swell risk at later age. The results of samples cured at 10C (50F) showed extensive linear swell post 28-day soaking despite moderate swell observed until this point. This introduces a significant risk of expansion where longer age testing is not included in the scope of mixture validation trials. In addition, a higher binder content using lime and GGBS proved to be the only successful solution to comply with both specified swell and soil strength properties. Chiller cabinets were installed and set up to facilitate bespoke testing to undertake this work and they are also available now for compliance monitoring of the work where required.
SECTION B: Assessing whether strength gain prior to contact with water could provide an effective mitigation to swell risk
This package of work sought to identify whether a solution for stabilising high sulfate mixtures with lime only could be found. It explored whether having a longer air cure period prior to soaking would allow sufficient strength gain of the mixture to reduce swelling once in contact with water.
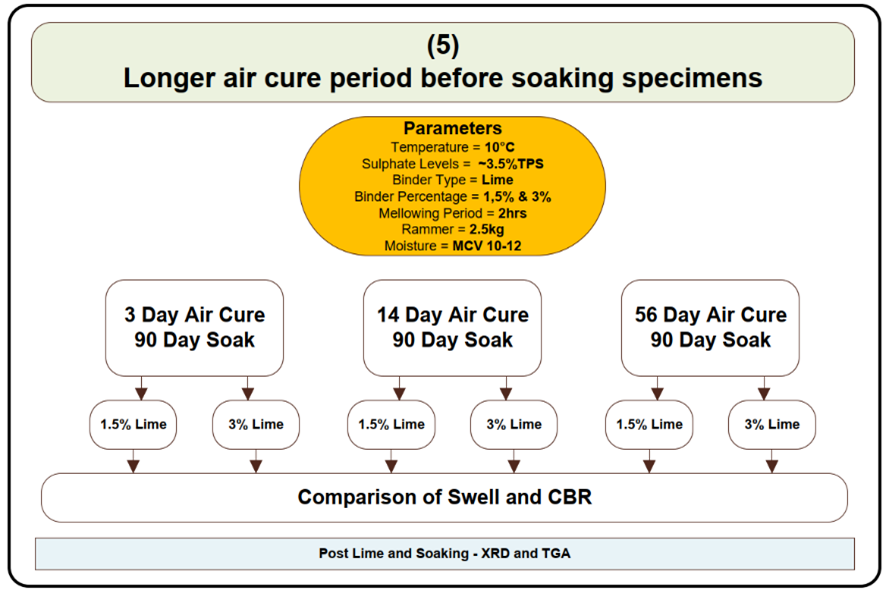
The scope (Figure 7) included comparison of treatment with quicklime only (hydrated lime discounted based on previous findings) with binder additions at 1.5% and 3%. Varying periods of air curing were compared with linear swell values compared on specimens cured at a reduced temperature of 10C (50F) only.
The soaked CBR is not entirely representative of real-world conditions. On soaking, the specimen is submerged in water and both the top and bottom are exposed to the water via small holes in the base plate and top plate. While properly designed drainage would direct water away from any earthworks fill, if water does infiltrate, it is highly unlikely to be fully submerged. With earthworks primarily being carried out in summer, it is likely the fill would have an extended curing period before exposure to water. A second set of trials looked at the effect of extending the air cure period prior to soaking to assess whether this could reduce the swell level.
1.5% and 3% quicklime specimens were air cured for 3, 14 and 56 days before 90 days of soaking. Considering the previous findings, the samples would be soaked at 10C (50F) to subject the material to the “worst case scenario”. The swell during soaking was measured and the plots below (figures 8 and 9 ) show the development of the swell over time.
Section B interpretation
In the 1.5% lime specimens, the longer air cure period appears to have a positive effect on the swell with the maximum swell decreasing from 2.5% in the 3-day air cure to 1.75% in the 56-day air cure specimens.
In the 3% lime specimens the swell appeared to increase with the increased air cure period (Figure 8) however when the plot is shifted (Figure 9) to add the air cure period to the soaked period you can see that the lines all tend to the same point, regardless of cure period. The mixtures gave comparable unsoaked CBRs of 30-40 at 7 days and 50-60 at 28 days with no significant difference between lime contents. Despite high strength prior to soaking, significant swell was observed following immersion in water. Using a prolonged air cure prior to soaking is not an effective mitigation measure for controlling risk of swell in high sulfate materials.
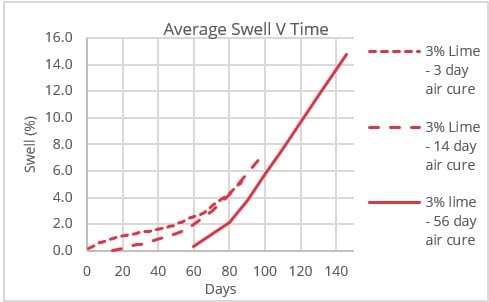
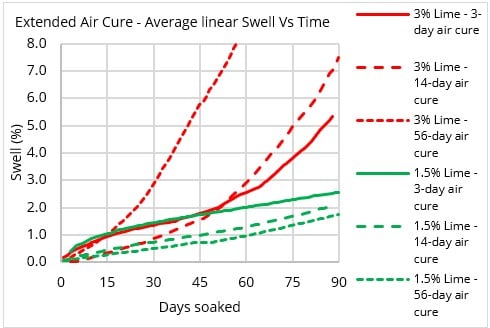
SECTION C: Establishing the most effective method of measuring swell
This package of work compared different swell measurement techniques to establish whether high swell could be identified more effectively than the standard soaked CBR swell test. The intent of this work package was to identify whether the CBR test limits access to soaking water compromising its ability to fully highlight swell risk (Figure 10). Benchmarking alternative tests allowing unconfined access by water against a standard CBR test with limited access could potentially highlight this risk earlier.
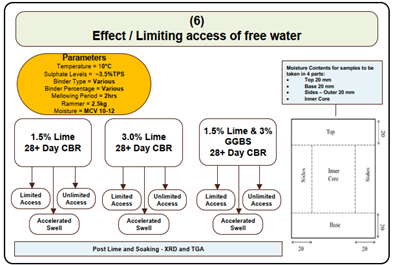
The standard CBR swell test at 10C (50F) was compared to a modified accelerated swell test (AST). BS EN 13286:49 [6] requires an axially compressed 50mm by 50mm cylindrical sample to be produced then stored at 20C (68F) in 90% relative humidity before being soaked at 40C (104F). Due to lack of availability of an external laboratory to carry out the testing it was carried out by the BBV lab team. Several modifications had to be made to the test method and these are as follows:
- 1 litre proctor mould samples were compacted using the 2.5kg rammer.
- Curing was carried out in standard lab conditions at 20C (68F) due to lack of humidity chamber available.
- Soaking was carried out at 10C (50F) and 40C (104F) to compare level of swell.
The volume was measured daily using volume on immersion testing and by measuring the dimensions of each specimen before and after soaking with a comparison of these results presented in Table 3 in Interpretation section below.
The other test that was trialled was a bespoke test called the unlimited access test (UAT) the setup of this is shown in Figure 11 below. Here a 1 litre proctor specimen was placed
in a 2 litre CBR mould and surrounded with sand before being soaked. The idea being that water has access to all sides of the sample but there is still a degree of confinement and therefore the linear swell could be measured using standard linear swell dial gauges
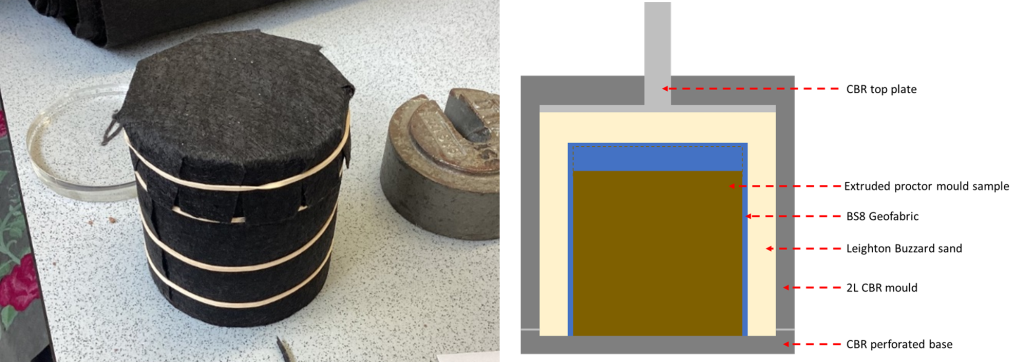
Section C interpretation
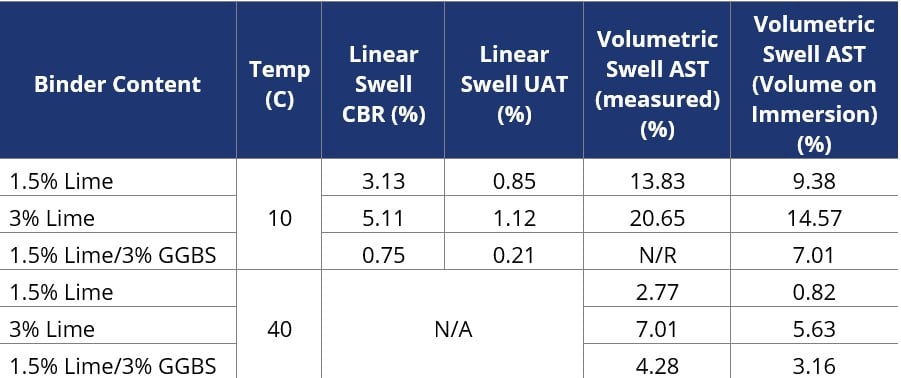
The above Table 3 shows the comparison of swell in all samples. 59 days was chosen as the comparison age as beyond this age unconfined AST samples disintegrated under soaking and no further comparison was available. While the values of linear swell may appear low in this table, this is due to 10C (50F) soaking with ultimate swell manifesting beyond this age. The eventual soaked CBR linear swell results can be seen in Figure 5 above. The values reported from the AST appear to compare well against the standard control limit for volumetric swell detailed below. However, it should be noted that the test was non-standard with the 20C laboratory air cure period not achieving the high humidity specified. Assuming compatibility of this alternative test method with the standard AST method, the results may indicate satisfactory performance in terms of swell. However,results from linear swell testing particularly at 10C (50F) curing temperature highlighted significant swell risk well above the specification limit. In conclusion, accelerated swell testing at the standard 40C is not considered an effective measure in identifying swell risk.
BS EN 16907:4 [7] states:
“Where the volumetric swelling is greater than 5 % but does not exceed 10 %, the use of the mixture is generally not possible; however, a complementary study can be made according to experience at the place of use. “
Figure 12 supports the findings of the earlier packages of work that 3% lime at 10C (50F) produces an unacceptable level of swell. Based on the statement above the 1.5% lime and lime plus GGBS mixtures would require additional testing but the previous results in this paper have shown that only the lime plus GGBS solution is suitable.
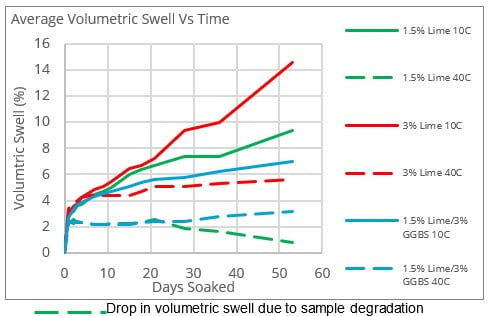
An additional finding is that the standard AST temperature does not effectively identify possible defective materials as Figure 12 shows that 3% lime at 40C (104F) is possibly safe to use. On comparison of the different swell measurement methods, the standard linear swell method is just as effective as the others in identifying swell when tested at 10C.
SECTION D: Evaluating the impact of high sulfate groundwater on both high and low sulfate host materials
Where material is excavated and found to contain high sulfate levels, digging and replacing with stabilised low sulfate material could be used to mitigate the risk of swell. In these areas N1 and N2 the sulfate minerals in the natural soil could have leached into the groundwater and there could be a risk of this stabilised material reacting with the groundwater. This trial assessed the linear swell of both high (3.5% TPS) and low sulfate (0.25% TSP) soils when soaked in aggressive sulfate bearing water. 1.5% and 3% quicklime and 1.5% quicklime + 3% GGBS specimens were made and soaked for up to a year in a moderate and high concentration sulfate water.
Gypsum powder was added to soaking water in the laboratory to achieve concentrations in line with those defined in BS8500-1 Table A.2 and BS EN 206 [8,9]:
-
- Moderately aggressive – 600 to 3000 mg/L, 0.24 to 1.2 % TPS equivalent
- Strongly aggressive – 3000 to 6000 mg/L, 1.2 to 2.4 % TPS equivalent
The linear swell results were as follows:
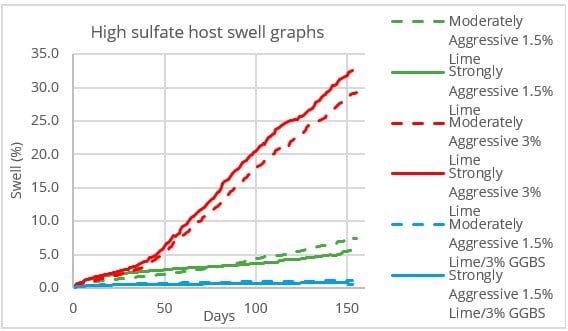
.
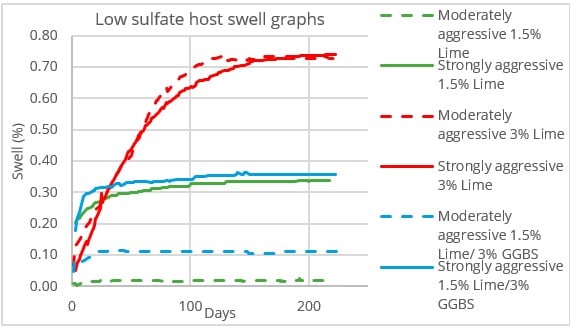
It can be seen from Figure 13 and Figure 14 that the high sulfate host material (3.5% TPS) exceeded the specified 3% linear swell limit for lime only treatment but the lime plus GGBS treated mixture performed satisfactorily in terms of swell. In the low sulfate host material (0.25% TPS) this showed negligible swell irrespective of soaking water concentration.
Section D interpretation
The main conclusion from these results is that the sulfate bearing groundwater does not appear to be affected by the swell of the low sulfate host specimens. The high sulfate host specimens showed very similar results to those in the “effect of temperature” work stream. The second takeaway is the GGBS solution remains effective in preventing swell even when high sulfate host samples are soaked in aggressive soaking water. This provides comfort for dig and replace solutions in aggressive ground where a clean host material can be used effectively.
Upon completion of the CBR tests in all packages, the specimens were sectioned, and moisture contents were taken from the top and bottom of the specimens. Further sub samples were also taken from some specimens for X-Ray Diffraction and Thermal Gravitational Analysis together with Differential Scanning Calorimetry. This indicated the formation of ettringite and thaumasite in the high swelling samples.
Outcomes
This work validated the need to adopt 10C (50F) curing to fully identify the potential expansive behaviour. The results of samples cured at 10C (50F) showed extensive linear swell post 28-day soaking despite moderate swell observed until this point. This introduces a significant risk of expansion where longer age testing is not included in the scope of mixture validation trials. In addition, a higher total binder content using lime and GGBS in a ratio of 1:2 proved to be the only successful solution to comply with both specified swell and soil strength properties.
In the 1.5% lime specimens, the longer air cure period appears to have a positive effect on the swell with the maximum swell decreasing from 2.5% in the 3-day air cure to 1.75% in the 56-day air cure specimens. However, the swell was still increasing at the end of the 90-day soaking period and in the earlier package the swell exceeded the 3% limit after 150 days. It can therefore be concluded that strength gain prior to immersion in water is not an effective swell mitigation measure.
The values reported from the AST appear to compare well against the standard control limit for volumetric swell. However, results from linear swell testing particularly at 10C (50F) curing temperature highlighted significant swell risk well above the specification limit. In conclusion, accelerated swell testing at the standard 40C is not considered an effective measure to identify swell risk.
The outcome from the results of the sulfate bearing ground water trials is that the sulfate bearing groundwater does not appear to affect the swell of the low sulfate host specimens. The high sulfate host specimens showed very similar results to those in the “effect of temperature” work stream. The second takeaway is the GGBS solution remains effective in preventing swell even when high sulfate host samples are soaked in aggressive soaking water. This provides comfort for dig and replace solutions in aggressive ground where a clean host material can be used effectively.
Learnings and recommendations
These trials have successfully shown that high sulfate materials can be treated to produce a durable high speed rail earthworks fill. The validation of reduction of lime: GGBS ratio of 1:2 (compared to 1:3 industry standard) is timely as GGBS supply is at a critical level. Even when given sufficient time to gain strength prior to contact with water, fills treated with lime only are not resilient against the threat of sulfate swell and should therefore be avoided for high sulfate materials.
Alternative testing methods were trialled but did not provide any additional benefit to the standard CBR linear swell test. The accelerated swell test at 40C (104F) has been shown to be a less strenuous test method and perhaps underestimates the potential swell risk of high sulfate materials.
It is recommended that 10C (50F) testing is considered in the future where high sulfate swell is suspected to be a risk as this is more representative of conditions in the field. Further work should investigate the swell mechanism for the high swelling materials as this work could not conclusively assess what the new mechanism was. Developing a new test which could identify sulfate swell risk sooner would also be a beneficial advancement.
Finally, this work has provided evidence that sulfate bearing groundwater does not impact the swell of high or low sulfate materials and therefore dig and replace of high sulfate with low sulfate materials is a suitable alternative should excess material be available.
Conclusions
Replacement of high sulfate host material with low sulfate material is an effective control measure. Provided good earthworks practice is followed to maintain earthworks in a dry condition, suitable and durable stabilised mixtures should not be adversely impacted should aggressive groundwater return post completion of earthworks activities. Allowing sulfate-rich stabilised mixtures to gain strength prior to contact with water does not provide adequate mitigation to swell risk. While the linear swell test appears to identify the swell risk at 10C (50F) curing under long age soaking, further research and development of an appropriate early age test is still required to mitigate the risk of undetected expansion risk. This work also demonstrated that a ratio of 1:2 lime to GGBS worked successfully compared to previous industry knowledge based on 1:3 reducing overall addition required.
The findings have already been shared across HS2 Phase One main works contractors and designers and with Phase Two designers. A detailed technical report has been produced which will inform future knowledge share and industry articles. A summary of the outcomes has also been published by Britpave in a best practice publication: BP 75 “Forwarding soil stabilisation” (2023) [10].
This learning legacy highlights the risk sulfate swell poses to lime stabilised fills. However, a treatment of such soils with lime and GGBS in a ratio of 1:2 provides a suitable level of protection against it. There are opportunities to adopt this mitigation measure on future projects and this work is expected to change industry approach to and inform future specifications on the stabilisation of sulfate materials.
Acknowledgements
Nick Sartain – HS2 Geotechnical Lead
Paul Beetham – HS2 Lime Stabilisation Technical Specialist
Richard Harris – BBV Materials Engineer
Sam Boden – BBV Materials Engineer
BBV Laboratory team
References
[1] E.A. Snedker (1996) M40 – Lime stabilisation experiences n proceedings of a seminar on Lime Stabilisation (C.D.F. Rogers, S. Glendinning and N. Dixon (eds)). Loughborough University, UK, pp.142-153
[2] D. Hunter (1988) Lime induced heave in sulfate bearing clay soils. ASCE Journal of Geotechnical engineering 114(2): 150-167
[3] Beetham, Paul; Dijkstra, Tom; Dixon, Neil; Fleming, Paul; Hutchison, Robert; Bateman, John (2015). Lime stabilisation for earthworks: a UK perspective. Loughborough University. Journal contribution.
[4] ICAX (2022). Mean Annual Air Temperature determines the temperature in the ground. Interseasonal Heat Transfer.
[5] Rihner, Madeline & Marsh, ATM & Provis, John & Koh, LSC & Walkley, Brant & Bernal, Susan. (2022). Legacy slags – a solution to the future shortages of GGBFS in the UK?
[6] British Standards Institute (2004) BS EN 13286-49 Unbound and hydraulically bound mixtures – Accelerated swelling test for soil treated by lime and or hydraulic binder
[7] British Standards Institute (2018) BS EN 16907-4 Earthworks – Soil treatment with lime and or hydraulic binders
[8] British Standards Institute (2023) BS 8500-1 Concrete – Complementary British
Standard to BS EN 206
[9] British Standards Institute (2013) BS EN 206-1 Concrete – Specification, performance, production and conformity
[10] Britpave (2023) BP75 – Forwarding soil stabilisation
Supporting materials
HS2 Specification for Civil Engineering Works (SCEW) 600 series – referred to as the “specification”.
Peer review
- Dimitrios OikonomidisHS2 Ltd