Thermal recycling
As part of demolition works for the northern section of the High Speed Two (HS2) Phase One, the Main Works Civils Contractor – Balfour Beatty VINCI (BBV), will handle an estimated 15,000m2 of cement-bonded asbestos. Traditionally, asbestos is sent to hazardous landfill sites however BBV in partnership with Thermal Recycling have adopted an alternative innovative approach. Thermal Recycling converts asbestos into a non-hazardous product, making a safe, inert material which can be used as a sustainable substitute for aggregate. This practice preserves landfill space, reduces the risk of mesothelioma for future generations, and offers cost efficiencies whilst aligning with circular economy principles. BBV has enhanced operational safety, improved environmental performance and helped drive a more sustainable culture when managing asbestos.
Background and industry context
Asbestos is a group of naturally occurring silicate minerals which are composed of long and thin fibres. These fibres are made up of many microscopic “fibrils” that can be released into the atmosphere by abrasion and other processes.
Asbestos can be divided into two sub-groups: serpentine and amphiboles. Serpentine asbestos, also known as chrysotile or white asbestos, was historically the most commonly used type of asbestos [1].
Inhalation of asbestos fibres can lead to various dangerous conditions, including cancer and lung disease, which are often incurable. According to the NHS, more than 2,700 people are diagnosed with mesothelioma each year in the UK [2]. Asbestos-related illnesses are a devastating consequence of asbestos exposure.
Importation, supply, and use of all asbestos has been banned since 1999, with the enactment of the Asbestos (Prohibitions) (Amendments) Regulations 1999. However, the risk of exposure to asbestos still exists as it was widely used in building materials due to its fire resistant and insulating properties.
Currently, most asbestos containing materials go to hazardous landfill or a landfill with a special cell for hazardous waste. Arguably, this is not the best solution for several reasons. Firstly, landfill capacity is depleting [3] and hazardous waste capacity must be safeguarded for wastes that currently have no alternative treatment option. Secondly, the risk of release of fibres is not eliminated by landfilling. The problem is temporarily managed as asbestos fibres are almost indestructible [4], deferring the risks for future generations [5]. There also remains a risk that leachate from landfills can mobilise fibres, with the potential to cause pollution to groundwater [6].
The risk of asbestos exposure is pertinent to High Speed Two (HS2) as a programme of demolition works is required. This includes demolishing various buildings refurbished or built before 2000.
Approach
Balfour Beatty Vinci (BBV) is the integrated team delivering the Main Works Civils Contract (MWCC) for the northern section of HS2 Phase One including Long Itchington Wood Green Tunnel to Delta Junction and Birmingham Spur and the Delta Junction to the West Coast Main Line (WCML) tie-in. These works included several sites and buildings with asbestos containing materials. Many of these buildings required demolishing as part of preparation for works.
Due to the historic wide-spread use of asbestos and the risks it poses to health, pre-demolition surveys must be undertaken to ascertain the presence of asbestos containing materials (ACM). These are completed by specialist contractors who have the skills and knowledge to identify asbestos safely. Most of the surveys have been completed and it is estimated that there is approximately 15,000m2 of cement-bound chrysotile roof sheets. This equates to roughly 285 tonnes of ACM.
‘My Contribution’ is a platform used by BBV which allows any member of staff to suggest innovative ideas to increase environmental performance, cost efficiencies and productivity. One idea posed was to utilise an innovative technique to dispose of asbestos through a company called Thermal Recycling. The plant, located locally in Wolverhampton, is permitted to accept cement-bonded chrysolite (white) asbestos. When received, the asbestos roof sheets are placed into a large kiln which heats the asbestos, denaturing it. Denaturing is a process that changes the essential characteristic of a substance, so that it is no longer that same substance.
The careful, scientific, and precise application of heat causes a number of thermal and recrystallisation processes and chemical reactions that convert the chrysotile asbestos into magnesium oxide and other crystalline and amorphous fractions (mostly silicates). The end product is a new material named Calmag and contains no asbestos. It is crushed to a powder which can be used as an aggregate. Thermal Recycling has built the first plant in the world to denature asbestos in a commercially viable way.
Usually, asbestos is placed into a lockable skip. However, this process required the subcontractor to load and secure bags provided by Thermal Recycling. These were temporarily stored on site (figure 2) until they could be collected, then stacked on pallets and loaded into the lorry using on-site plant (figure 3). Guidance was provided by Thermal Recycling to assist with this whole process. It should be noted that no BBV operative or any other person came in to contact with the asbestos.
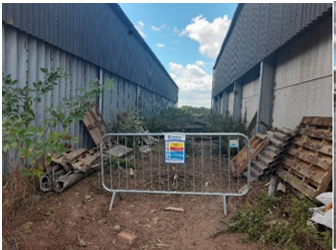
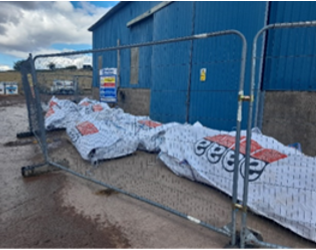
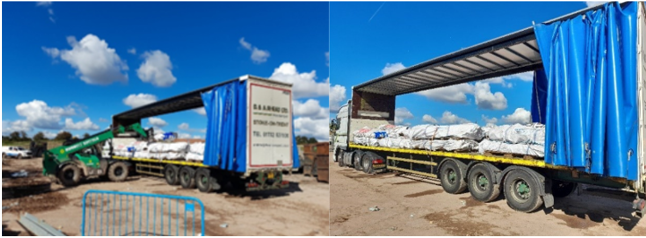
BBV anticipated 20 tonnes of waste would be collected but only 13 were removed for treatment. The full 20 tonnes could have been removed if more asbestos roof sheets were stacked on each pallet. However, because the sub-contractor was inexperienced with the new process, the pallets and bags were not used as efficiently as possible. This meant that the other 7 tonnes of asbestos roof sheets went to a permitted landfill and was a missed opportunity.
Outcomes
Thirteen tonnes of cement-bonded chrysotile roof sheets were sent to be denatured at the Thermal Recycling facility. This equates not only to thirteen tonnes of hazardous waste being diverted from landfill, but at the time of collection, saw savings of £425.29 per tonne of waste. The waste is charged on a rate per tonne along with optional transport fees.
If replicable across the estimated tonnage of cement bonded chrysotile on BBV’s sites, savings in the region of £700,000 could have been attained. Coupled with Early Works stages, the savings would have been even more substantial. Unfortunately, BBV were already most of the way through the demolition programme before this idea was explored and trialled.
Learnings and recommendations
Using Thermal Recycling, BBV has reduced the risk of further asbestos exposure and has helped drive circular economy models.
Although this technology is a world-first, the facility is currently operating as a demonstration plant. This means under the facility’s environmental permit, storage of the waste prior to processing is not possible. It also means that the facility can only accept a small amount of the waste each month to process. This posed a logistical challenge for sites due to programme constraints and required space on HS2 sites for storage. Currently, Thermal Recycling are in discussions with potential partners to upscale to a full-size plant. However, due to permitting requirements, this would unlikely be before 2026.
Additionally, asbestos waste must be managed in accordance with the Control of Asbestos Regulations 2012, and the Approved Code of Practice (ACOPs). There were some differing interpretations of what would be acceptable in terms of storage on site and a plan had to be agreed with the local Health and Safety Executive (HSE) officer which included air monitoring.
BBV recommends that shipping containers with side openings are purchased. They should have sufficient space to allow operation of a forklift. This would satisfy the requirement for a secure container that can have restricted access. Together with a thorough method statement, storage on site may be attainable without a permit. Engagement with the local HSE officer early in the process is vital.
As Thermal Recycling’s process is still very new, specialist demolition contractors were hesitant to utilise the new method; they had reservations about diverging from the norm. For future projects, it is advised that tender documents for asbestos-related packages indicate the intention to utilise Thermal Recycling. Upon award, concerns can be addressed, and processes and procedures established through early engagement.
This opportunity was identified and trialled when major works were already under way. It would have realised further benefits if implemented at the Early Works stage when the majority of demolition work was contracted. If managed correctly, savings could be made on disposal costs of chrysotile roof sheets as well as improved environmental outcomes.
Finally, the rate of disposal is prone to fluctuate in line with the energy prices. After a cost comparison exercise, recycling remained significantly cheaper compared to disposing in landfill. Regarding energy, it is recommended that further study should be carried out on the energy consumption as this is likely to have a significant environmental impact in itself.
Conclusion
In summary, BBV has trialled an innovative approach to handle asbestos within their demolition works, partnering with Thermal Recycling to convert asbestos into a non-hazardous substitute for aggregate. This practice diverts hazardous waste from landfills and mitigates health risks associated with asbestos exposure.
The successful diversion of 13 tonnes of cement-bonded chrysotile roof sheets demonstrates significant cost savings and underscores the potential for widespread adoption across BBV’s sites. However, logistical challenges and regulatory considerations highlight the need for proactive engagement with regulatory authorities and strategic planning in future implementations. Despite initial hesitancy from contractors, early integration of Thermal Recycling’s technology into tender documents can facilitate smoother adoption and maximize benefits.
Looking ahead, opportunities for further refinement, such as exploring energy consumption implications and optimizing storage solutions, underscore the ongoing commitment to sustainability and continuous improvement. Through strategic partnerships, innovative solutions, and proactive adaptation, BBV is leading innovation in responsible asbestos management, paving the way for a more sustainable future in the construction industry.
Acknowledgements
Lyndon Trinder
Simon Thorne
Rakesh Korotana
William Stephenson
Aishwarya Selva
Joshua Heaney
Graham Gould
References
[1] Public Health England. Asbestos: General Information 2017. [Accessed 29 February 2024].
[2] National Health Service. Health A-Z: Mesothelioma 2022. [Accessed 29 February 2024].
[3] Environment Agency. Waste Data Interrogator 2018 2024. [Accessed 29 February 2024].
[4] Ramazzini C. The global health dimensions of asbestos and asbestos-related diseases. Journal of Occupational Health. 2016 58(2): 220-223. [Accessed 29 February 2024].
[5] Official Journal of the European Union. European Parliament resolution of 14 March 2013 on asbestos related occupational health threats and prospects for abolishing all existing asbestos (2012/2065(INI)). [Accessed 29 February 2024].
[6] Tomassetti L, Giuseppe D, Zoboli A, Paolini V, Torre M, Paris E, Guerriero E, Petracchini F, Gualtieri A. Emission of fibres and atmospheric pollutants from the thermal treatment of asbestos containing waste (ACW). Journal of Cleaner Production. 2020 268(122179). [Accessed 29 February 2024].
[7] https://www.thermalrecycling.co.uk/converting-asbestos. [Accessed 11 July 2024].