Training supervisors for excellence now and the future
Frontline supervisors (FLS) play a critical role in safely supervising and coordinating activities on site. A shortage of FLSs within the construction industry was identified and those that were available generally did not have the required set of competencies for the more complex role required for the High Speed Two (HS2) enabling works,
The Enabling Works Contractor for Area South decided to invest in an FLS training programme which developed a set of standard requirements for the role to achieve a higher standard of practice across the works.
The programme resulted in five-hundred FLSs being upskilled resulting in better supervision, safer works, and fewer defects.
This learning legacy will be of interest to future projects looking to implement their own upskilling programme for front line supervisors.
Background and industry context
A frontline supervisor’s (FLS) task is primarily to safely supervise and coordinate activities on site. Successful execution of the role requires a good level of understanding of the project, the trades, and also ensuring a good level of control on site to maintain safe operations.
The works on the High Speed Two (HS2) Programme are very diverse and they capture a broad spectrum of high risk construction activities. It was necessary for the FLSs on Area South Enabling Works Contract to possess a wide range skills and experience.
Area South of the Enabling Works Contract (EWC) is the southern section of High Speed Two (HS2) phase one, delivered by the Costain Skansja joint venture (CSjv). The works include demolition of buildings within the wider Euston area, utility diversions, environmental and ecological monitoring and a programme of historic environment and archaeological activities.
The minimum industry requirement for an FLS is the completion of the Site Supervision Safety Training Scheme (SSSTS). With this qualification, an FLS would be able to arrive on site and start a day’s work without the need to know the processes, systems or even the company they work for. Due to the complex nature of the HS2 Programme, it was deemed that an SSSTS qualification alone was inadequate.
As a project it was felt that by asking that all FLS were trained in SMSTS this would give the skills they needed and would leave a legacy of FLS’s who had the right skill set.
FLSs are at the fore-front of delivery and are seen to be last line of defence for managing the safety of individuals. It is therefore also essential to empower FLSs and ensure they have the confidence to discharge their responsibilities.
The CSJV team recognised this need for improvement in FLS training. The team took the opportunity to shape and nurture development of FLSs and raise standards by putting them through a competency training programme and introduced a formalised structure for the role.
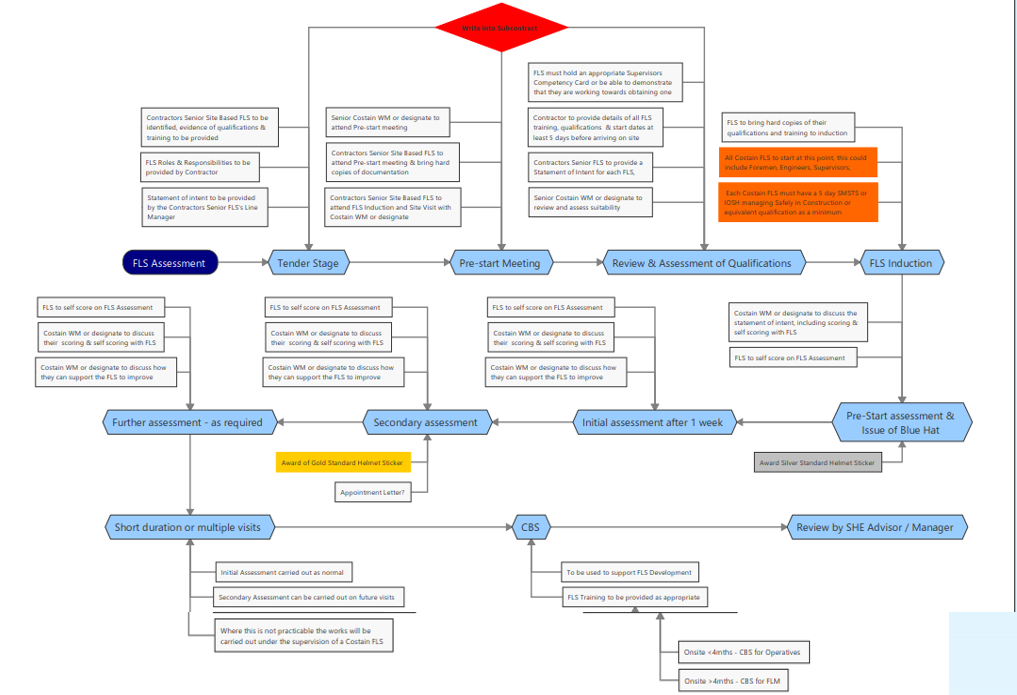
Implementation of the FLS Training
CSJV provided training and support for the FLSs. The minimum requirement for an FLS on the project was to pass the Supervision Level 4 National Vocational Qualification (NVQ), a graded scale training programme centred on industry best practices and legal requirements. If the individuals chose to, there was opportunity to progress to Management Black CSCS Card Level 6 NVQ.
500 supervisors were put through the NVQ Level 4 training on the CSJV HS2 Enabling Works Contact.
On site, an assessment was carried out for each FLS within their first week, followed by a 12-week review process to ensure the FLS had attained the competency level required. This allowed a thorough assessment of the individual’s suitability as a supervisor in the HS2 environment. If the individual was found to be under-performing, their FLS status would be withheld and further training and coaching was provided.
The FLSs achieved technical competency at the end of their assessments. They also demonstrated improvements in their safety behaviours as FLSs and saw improvements in their own leadership capabilities.
On-site coaching was also provided through analysing behaviour, which increased awareness, bettered safety performance and improved communication skills on site. From the point of starting-out on site as a general operative, support was provided to develop people’s skills. The growth of each of the FLS’s capabilities was tracked and monitored as they developed into adopting a qualified supervisory position.
The implementation of the FLS training structure included consideration of the following:
- Specifying the FLS skill set needed depending on where they were to be deployed
- Diversity of supervisory experience and aligning the role with CSJV standards
- Including the FLS in the staff onboarding process and embedding our values and safety culture
- Subjecting the FLSs to ongoing assessments to maintain and improving their skills as shown in Figure 2
- Highlighting and embedding the JV’s parent companies’ commitment to FLS excellence.
As a result of the training, the FLSs felt valued and empowered, demonstrated through their positive behaviour and accountability.
Finally, a central system was developed for the programme of works to allow easy movement of FLSs from one site to another, reducing the amount of time having to re-assess the FLS every time they move from site to site. The central system contained shared data and was under the control of the Works Managers, as shown in Figure 2
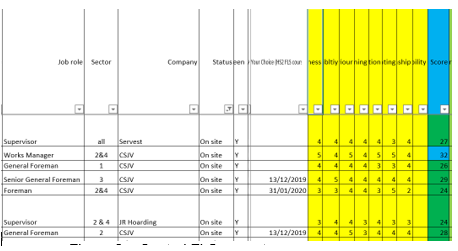
Lessons learned and benefits of the programme
To achieve high quality results the initiative was led by the CSJV Works Managers across the programme and was supported by the CSJV Delivery Directors and Commercial Leads.
The benefits of this initiative include:
- Works were better supervised and conducted more safely.
- Better trained supervisors are more able to detect work of poor quality and reduce the need subsequent rework.
- Tangible social value in developing, upskilling and qualifying our people.
- Control and awareness of the organisational structure for the FLSs meant that all teams were aligned and staff were put to work safely and efficiently
- On complex sites FLSs were working incredibly well together, working as a team towards common goals.
- Development of FLS central system allowing quick and efficient transfer between sites. This is used for audits to be able to demonstrate the assurance process
- Able to raise the standards, leaving a legacy of upskilled and valued FLS that will benefit other industries and companies.
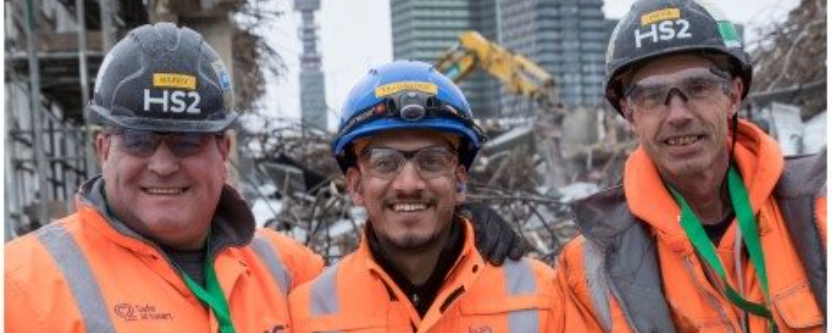
Recommendations
In deploying this approach, it is recommended that:
- You set the standard at the early stages of the project and align the commercial model to ensure the supply chain is aware of the high standards required of FLSs.
- Engage with the supply chain early to give them understanding of the FLS process and share the initiative with internal teams to prepare them for what is required when procuring suppliers. As per Figure 2 this sets out how we engage with the supply chain as early as the tender stage and start those conversations and upskilling of the FLS before they start on site.
- Ensure the commercial mechanisms are in place and that there is support to fund such an initiative – highlighting the benefits as justification
- Different people require different coaching methods, and it important to adapt styles appropriately to suit different individuals.
Acknowledgements
CSJV Works Managers who led the initiative across the programme, supported by the CSJV Delivery Directors and Commercial Leads.
Costain and Skanska Assurance Teams who carried out assurance checks to ensure these standards were implemented across the programme.
The supply chain who took responsibility to ensure that the training programme was mandated to all FLSs and provided support to their people.
Costain Group and HS2 who developed the initiative creating a working standard that aligns with the requirements of an FLS.