Transformation of London clay into construction resources: Supplementary cementitious material and lightweight aggregate
Resource efficiency, regarding waste minimisation and material re-use, is central to infrastructure construction for both environmental and financial sustainability, especially given the sheer scale of such projects. Maximising resource efficiency can significantly reduce impacts, streamline costs and tackle material scarcity.
HS2 will need to manage large amounts of excavation arisings; particularly in Area South, where extensive tunnelling producing high volumes of London clay spoil, will need to be undertaken underneath central London. This challenge is common among underground infrastructure works in urban areas and is typically addressed by transporting the excavated material, often over long distances, to disposal/landfill sites.
A feasibility study based on circular economy principles under the title REAL: Re-purposed Excavated Arisings Loop, has been developed in response to the above. It aims to assess the potential to transform excavated London clay spoil into calcined clay for use as Supplementary Cementitious Material (SCM) in concrete; and expanded clay for use as Lightweight Aggregate (LWA).
The full study consists of 3 stages, each depending on preceding results:
• Testing London Clay for suitability as SCM and LWA (Stage 1a)
• Design, monitoring and optimisation of concrete mixes containing the London Clay-derived SCM and LWA (Stage 1b)
• Set up of pilot clay processing facility on site and use its outputs in construction works (Stage 2)
This paper only covers Stage 1a of the study.
Introduction
Background
Population growth and rapid urbanisation in the context of climate crisis and resource depletion require the construction industry to revisit its traditional linear material sourcing and disposal practices. Alternative techniques should be adopted to respond to increasing need for built assets in an environmentally-sustainable manner.
With concrete being the single most widely used building material, there is growing appetite for exploring new, accessible and low-carbon alternatives for its main constituents – cement and aggregates. Particularly in Europe, stock levels of the currently principal sources of Portland cement replacements (fly ash and GGBS (Ground Granulated Blast furnace slag), are declining due to the gradual phase-out of the industries generating them – coal and primary steel making respectively, combined with the rising concrete demand for new developments.
Waste management and construction logistics, particularly for projects in dense, urban environments are complex to execute and challenging to budget and programme, as well as adversely impacting the environment and local surroundings. Tunnelling and deep excavations generate large volumes of spoil that need to be transported and disposed of offsite with the associated increased carbon emissions, air pollution and costs. In recent years there have been efforts to utilise such arisings in landscaping and as fill material. However, the potential to transform excavated spoil into useful construction resource like concrete has largely remained untapped so far.
Objectives & targets
The overarching objective of the REAL project is to respond to the above challenges through investigating the viability of re-purposing excavation arisings to produce useful construction materials. Successful implementation and roll out of this circular economy approach could result in minimised waste streams to landfill avoiding the environmental impacts and costs associated with transport and disposal, improved resource efficiency, reduced need for imported materials, construction products innovation, new skills & employment and leave a legacy for the industry.
The project is focused on repurposing London Clay, which is the most frequently encountered geological formation in Greater London, including most of the tunnelling and excavation arisings in the southern section of HS2 Area South.
Two main outputs are targeted by processing excavated London Clay spoil:
- Calcined clay, for use as supplementary cementitious material (SCM) in concrete mixes
- Pelletised expanded clay to form light weight aggregates (LWA), for use in concrete mixes and/or as fill material
REAL: Project overview
Because of the complexity of the components of this innovation, the robustness and fitness for purpose of turning clay to resource can only be validated through discrete steps of development. Therefore, REAL is structured as a modular feasibility study with every step of the process, depending on the outcomes of the previous stages.
REAL consists of 2 key phases:
- Stage 1 – Proof of concept: Materials & concrete feasibility study
1.a. Raw material screening: London Clay material characterisation
1.b. London Clay-derived SCM & LWA: Performance testing & concrete trials
- Stage 2 – Pilot: Site trial
On-site production of the London Clay derivatives & trial in HS2 construction works
A schematic overview as well as more detail on the tasks involved in each stage are provided in Figure 1. This paper only covers Stage 1a of the project, where excavated London Clay was tested for suitability producing the targeted outputs: SCM & LWA. Based on the results of the raw material characterisation, fabrication of the clay derivatives and systematic assessment of their technical performance in concrete prototypes will be conducted (Stage 1b). Subject to adequate outcomes of the laboratory concrete trials, production of the clay derivatives at a pilot on-site plant and their incorporation in selected concrete mixes for designated structures of the HS2 works (low risk elements) will follow.
The test results will be verified for compliance against relevant standards to provide confidence in the products and boost their wider uptake and future commercial exploitation for construction applications.
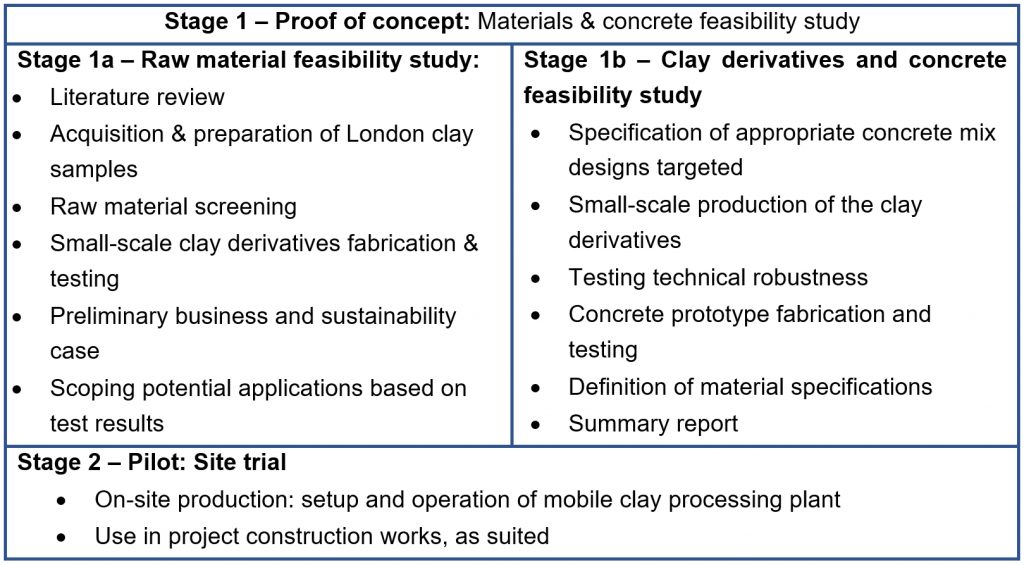
Existing knowledge: Literature review
Calcined clay as SCM in concrete
Clays have been used as construction materials either before or after being processed for many years. In the concrete industry, clays of sufficient kaolinitic content have been used as a cement substitute, as they exhibit pozzolanic behaviour after calcination when combined with cement. A highly reactive mineral addition known as metakaolin is formed when calcining high purity kaolinitic clays. [1] Metakaolin is widely acknowledged as a robust cement substitute. [2,4,5,8]
Over the last decades, material characterisation of clays on the earth’s crust in terms of their pozzolanic activity and suitability as SCMs in concrete, has gained significant popularity. This stems from the limited availability of other traditionally used SCMs in concrete, especially when compared with the profusion of clays globally, as shown in Figure 2 below. Metakaolin has been
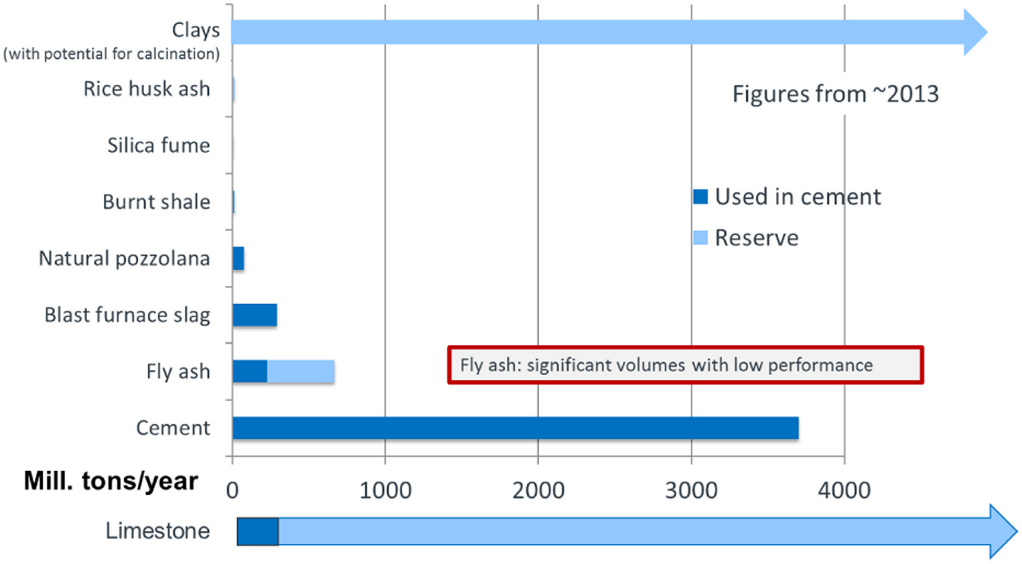
Kaolinite-rich clays are proven to be highly pozzolanic when calcined between approx. 700-850 °C.[7] It has therefore been established that the kaolinite content in the clay after calcination is a key parameter in dictating the suitability of calcined clays as an SCM. This is mainly due to the kaolinite content affecting the pozzolanic activity and hence, strength contribution of calcined clay in concrete. Figure 3 below illustrates the effect of different kaolinite contents on the strength of mortars containing calcined clays (50% ground clinker, 30% calcined clay, 15% limestone, 5% gypsum). Clays with kaolinite content of around 40%, display mechanical properties comparable to Ordinary Portland Cement (OPC) from about 7 days for normal strength concrete. Determining the kaolinite content of a clay is therefore important as an indication of the concrete strength class and percentage of cement replacement that can be potentially achieved.
London Clay properties and calcination performance
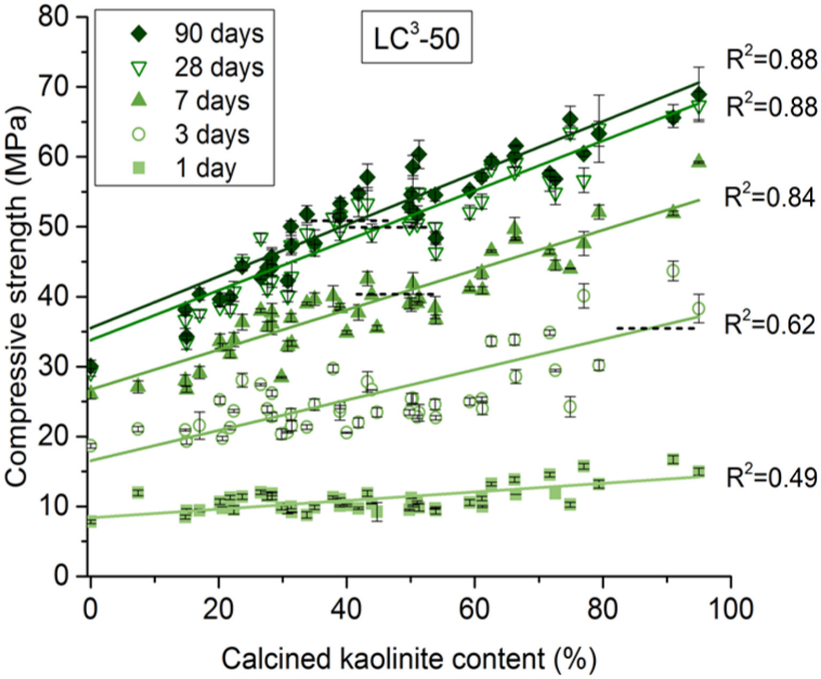
While there is comprehensive literature available on the suitability of several clays for use in concrete as SCM, there is little information specifically for London Clay as a potential SCM. It is therefore important to fill in this knowledge gap and assess the pozzolanic activity of London Clay and its suitability as SCM in concrete, particularly given the abundance of London Clay in the Greater London area and the anticipated excavation works in the area.
The mineralogical characterisation of London Clay [6] suggests a low average kaolinite content of around 13-15%, although several boreholes show higher levels (up to 36%) of kaolinite in distinct horizons within the geological sequence – predominantly in Unit D, but not only. Based on this, London Clay is classed as relatively low grade pertaining to pozzolanic activity. However, the paper represented a small sample of boreholes spread across a significant geographical area; higher kaolinite concentrations could be present in central London locations.
A 2017 research study on London Clay from another tunnelling project in the London area [9] was examined the mineralogical characteristics of clay samples before and after calcination in a range of calcination temperatures (600-1000 °C, optimum 800–900 °C) in order to determine their post-calcination reactivity and therefore their suitability as an SCM . The kaolinite content was around 26%, which is on the high side for London Clay however remains relatively low in terms of pozzolanic activity. The study also investigated the effect of calcined London Clay on the concrete strength, as shown in Figure 4. Cement replacement with calcined London Clay up to 30% was considered, with binder (OPC & SCM) contents ranging from 416 to 550 kg/m3 and w/b ratios of 0.5, 0.4 and 0.3. 40 MPa cube concrete strength was achieved at 28 days with 30% replacement in a 0.5 w/b concrete, corresponding to a C25/30 EN 206-1 concrete, while maintaining a slump in the region of 160mm. The strength increased at lower w/b ratios, however the workability was significantly compromised for practical uses (0mm for 0.3), due to the increased water demand of calcined clays,
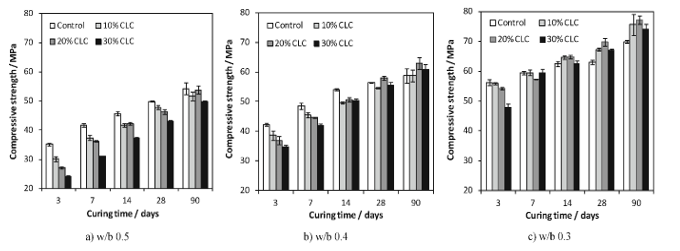
Previously unpublished work from a collaboration between ARUP, SCS and EPFL also provided insights into the reactivity of calcined London Clay, as well as on concrete strength that can be potentially achieved with London Clay as an SCM. Through thermogravimetric analysis (TGA), indicated a kaolinite content of 17% (see Figure 5). Even with lower kaolinite content, it was possible to produce mortar of 50 MPa strength at 28 days, with 50% Clinker, 30% calcined London Clay, 15% limestone and 5% gypsum.
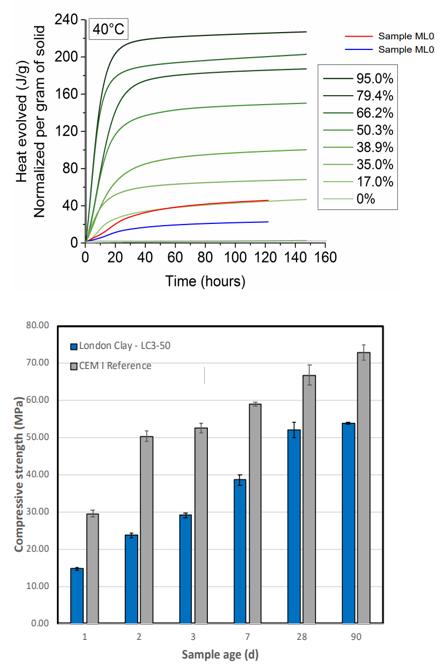
Expanded clay as aggregate
London Clay could also potentially be used in the form of expanded clay pellets serving as lightweight aggregate for different uses as infill, insulation or in low grade lightweight concrete. The process of producing lightweight aggregate out of expanded clay includes the assessment of the material purity and the pelletisation and firing of the clay in high temperature to achieve expansion up to 14mm diameter. Although several clays are used globally to produce expanded lightweight aggregate, there is only one documented attempt to manufacture clay aggregate out of London Clay. This was an innovation project for Crossrail Ltd. [3], where excavated London Clay was converted into expanded clay aggregates in the laboratory and used in concrete samples.
The study indicated that the resulting aggregates exhibit relatively low compressive strengths, in turn compromising the strength of the concrete mixes trialled. Three different aggregate replacement levels were considered in the concrete samples: 33, 66 and 100% of total coarse aggregate content, with 28-day cube strength of 33, 22 and 16 MPa respectively. This suggests that while the expanded London Clay aggregate may not be suitable for structural, reinforced concrete, non-structural applications could be considered, such as mass concrete fills, concrete blinding and similar elements.
Material testing
Sample collection, selection & preparation
Three (3) different types of London Clay samples have been examined to cover the broad range of potential material states likely to be encountered during HS2 tunnelling and excavations:
- Raw/Non-treated London Clay; as dug
- Conditioned/Pre-treated London Clay; mixed with ‘softening’ foaming agent (polymer) used to facilitate TBM tunnelling operations
- Conditioned & stabilised/Pre- & post-treated London Clay; mixed with ‘softening’ foaming agent (polymer) used to facilitate TBM tunnelling operations, then chemically stabilised with quicklime to simulate high moisture content in the excavated material that will require stabilisation to enable handling.
Samples were obtained from various locations within the London area, along the HS2 route and elsewhere. Table 1 below outlines the total of 10x London Clay samples (7x raw; 1x conditioned; 2x conditioned & stabilised) included in the REAL study. The selection was intended to cover location- as well as depth-based variability. Samples from deeper levels were preferred where available to better represent the depths where tunnelling works will take place.
ID | Source location | Details | Condition | Depth |
---|---|---|---|---|
1 |
PVE wall – Euston area |
Borehole code: ML001-CP402B |
Raw/Non-treated |
10 – 15m |
2 |
PVE wall – Euston area |
Borehole code: ML001-CP402B |
Raw/Non-treated |
15 – 20m |
3 |
Euston station |
Borehole code: MS08 POP UP GARDEN ML000 – RC048 (Box 10) |
Raw/Non-treated |
18.8 – 20.3m |
4 |
Euston station |
Borehole code: ML000 – RC051 (Box 9) |
Raw/Non-treated |
14.5 – 16m |
5 |
Euston station |
Borehole code: ML000 – RC051 (Box 10) |
Raw/Non-treated |
16 – 17.5m |
6 |
West Ruislip trial pits |
TH1 |
Raw/Non-treated |
2.9 – 3.2m |
7 |
West Ruislip trial pits |
TH6 |
Raw/Non-treated |
2.7 – 3m |
8 |
Thames Tideway – West |
31.7% natural RH with approx. 1-2% v/v soil conditioner content |
Conditioned/ Pre-treated |
approx. 30m |
9 |
Thames Tideway – West |
31.7% natural RH with approx. 1-2% v/v soil conditioner content Hydrated to 50% RH and then stabilised with 2% lime |
Conditioned & stabilised/Pre- & post-treated |
approx. 30m |
10 |
Thames Tideway – West |
31.7% natural RH with approx. 1-2% v/v soil conditioner content Hydrated to 40% RH and then stabilised with 1% lime |
Conditioned & stabilised/Pre- & post-treated |
approx. 30m |
Samples directly from live or recent excavations were acquired for raw and conditioned London Clay (types 1 & 2). In order to simulate conditioned and stabilised excavation spoil (type 3), representative conditions as such were artificially replicated in the lab, as no source of that type of material was readily available at the time of the study. Conditioned material (type 2) has been separated and broken down in two to be post-treated as appropriate, to 2 different standards. 2 likely stabilisation scenarios were explored to cover common cases acquainted in actual excavations:
- Average case: High moisture content (40% RH)
- Worst case scenario: Very high moisture content, approaching the material’s liquid limit (50% RH)
Testing programme
The testing regime was designed to provide initial material characterisation to serve as an indicator for the suitability of London Clay as cement substitute and lightweight aggregate. The testing covered the microstructural and thermochemical properties of raw and calcined London Clay. The experimental techniques employed in this study are listed in Table 2 below.
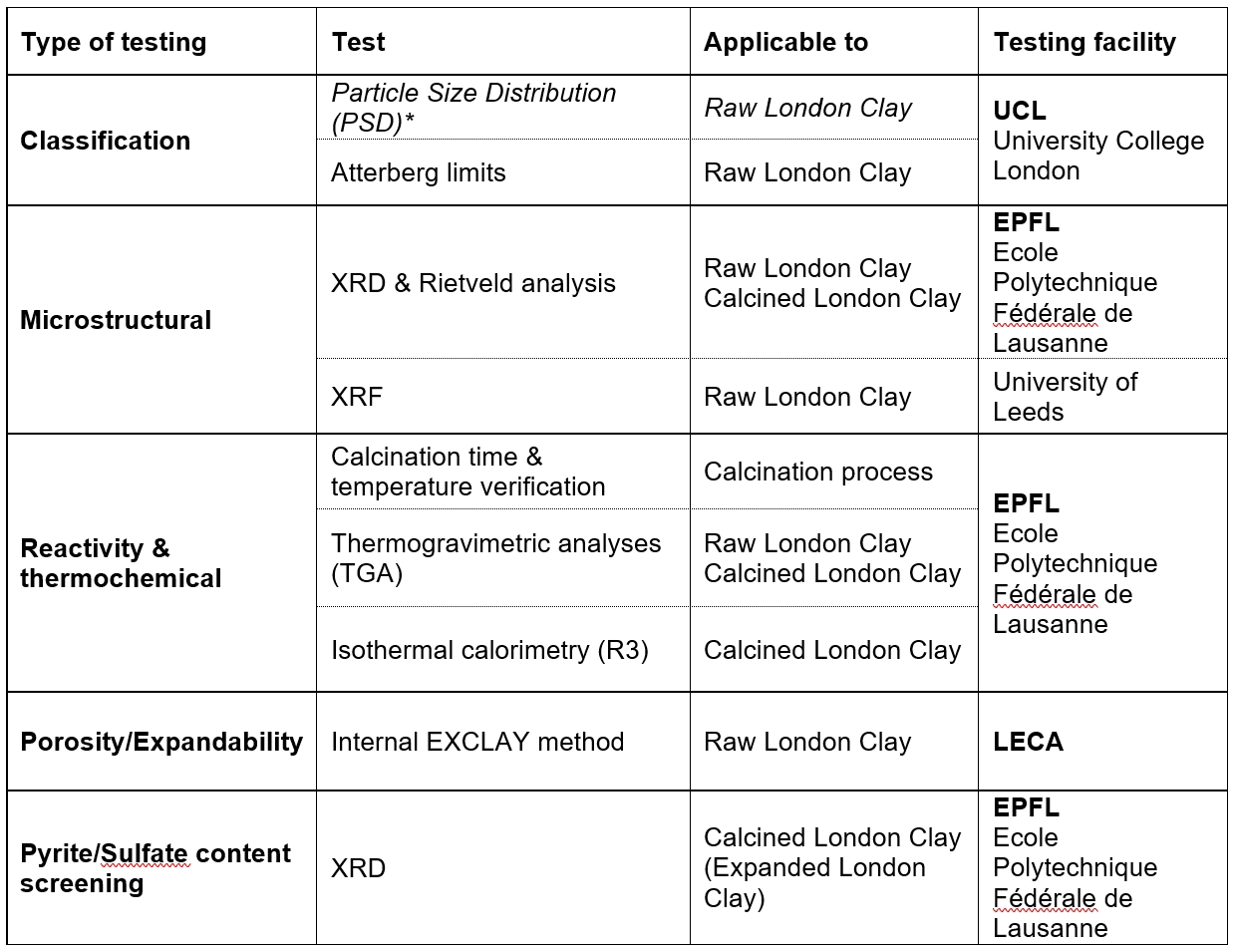
* PSD testing has been disrupted due to the COVID-19 pandemic and will be completed as soon as UCL re-opens, it therefore does not feature in the results and discussion in the following sections.
Testing results
The most relevant results from the testing programme with respect to the suitability of London Clay as SCM and LWA are presented below.
SCM suitability
Thermogravimetric analysis (TGA) determined the kaolinite content of the samples, as shown in Table 3. The decomposition of kaolinite occurs between 350 to 600 °C, and the weight loss of the sample can be used to compute the kaolinite content of the material. Previous research has shown that the kaolinite content of a given clay is the main parameter driving its reactivity when used as a supplementary cementitious material in concrete formulations.
Sample ID | Weight Loss Kaolinite (% initial weight) | Kaolinite content (%) |
---|---|---|
#1 |
2.6328 |
18.86 |
#2 |
2.7472 |
19.68 |
#3 |
2.6120 |
18.71 |
#4 |
2.8994 |
20.77 |
#5 |
2.0485 |
14.67 |
#6 |
2.4500 |
17.55 |
#7 |
1.4800 |
10.60 |
#8 |
2.9100 |
20.84 |
#9 |
3.0793 |
22.06 |
#10 |
2.5134 |
18.00 |
The R3 pozzolanic test rapidly predicts the reactivity of calcined clays by monitoring the heat release of the pozzolanic reaction in portlandite-calcined clay-limestone pastes using isothermal calorimetry, in accordance with ASTM C1897. The London Clay samples were cured at 40 °C and then calcined at 800 °C for 1 hour. The results from this process for all 10 samples are shown in Figure 6.
The isothermal calorimeter curves for London Clay as illustrated in Figure 6 are compared to those of clays with different kaolinitic contents, as shown in Figure 7. London Clay plots in the low end of kaolinitic clays with an average kaolinitic content of approximately 18% (max 22%, min 11%). The similar isothermal calorimeter results for the samples were generally similar, with one low outlier (sample 7 with 11%).
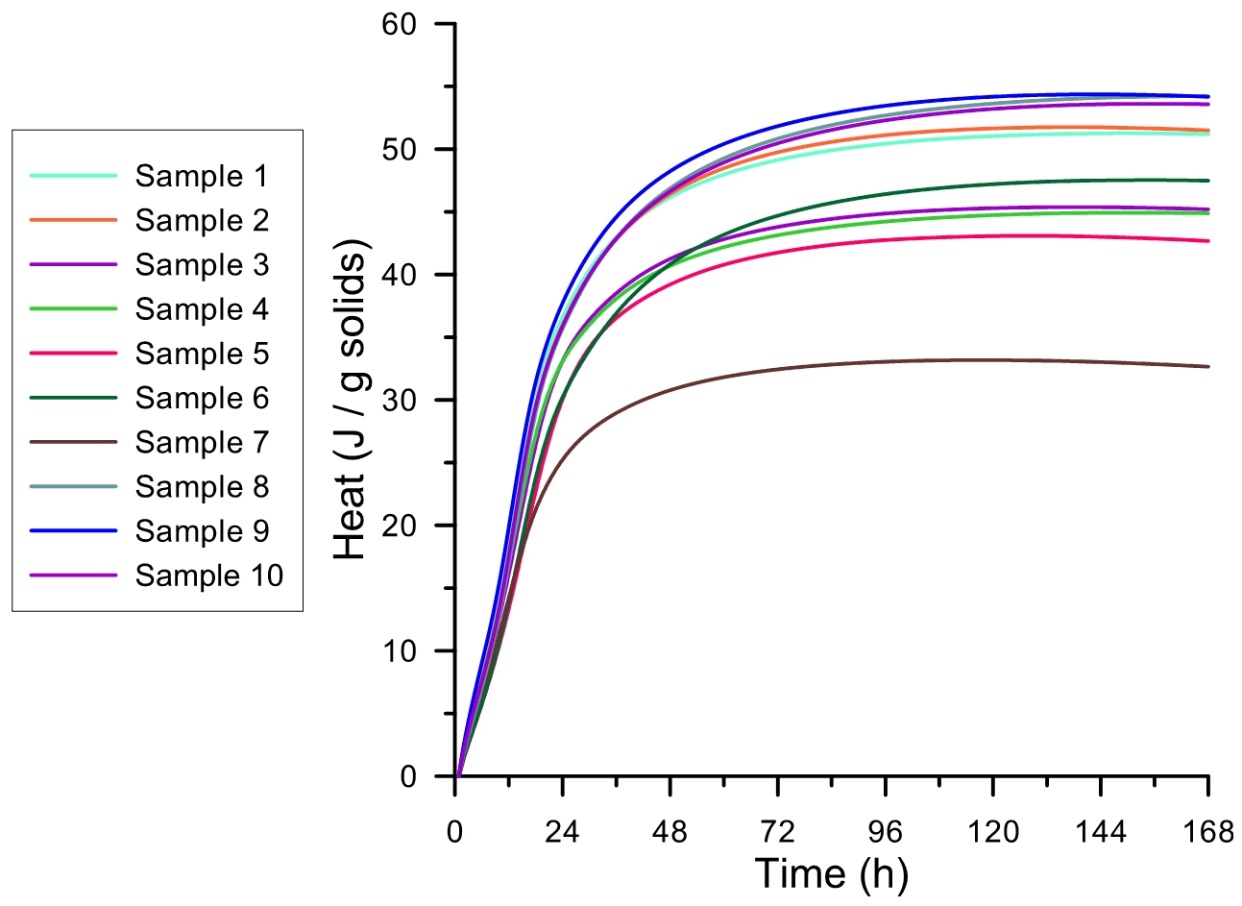
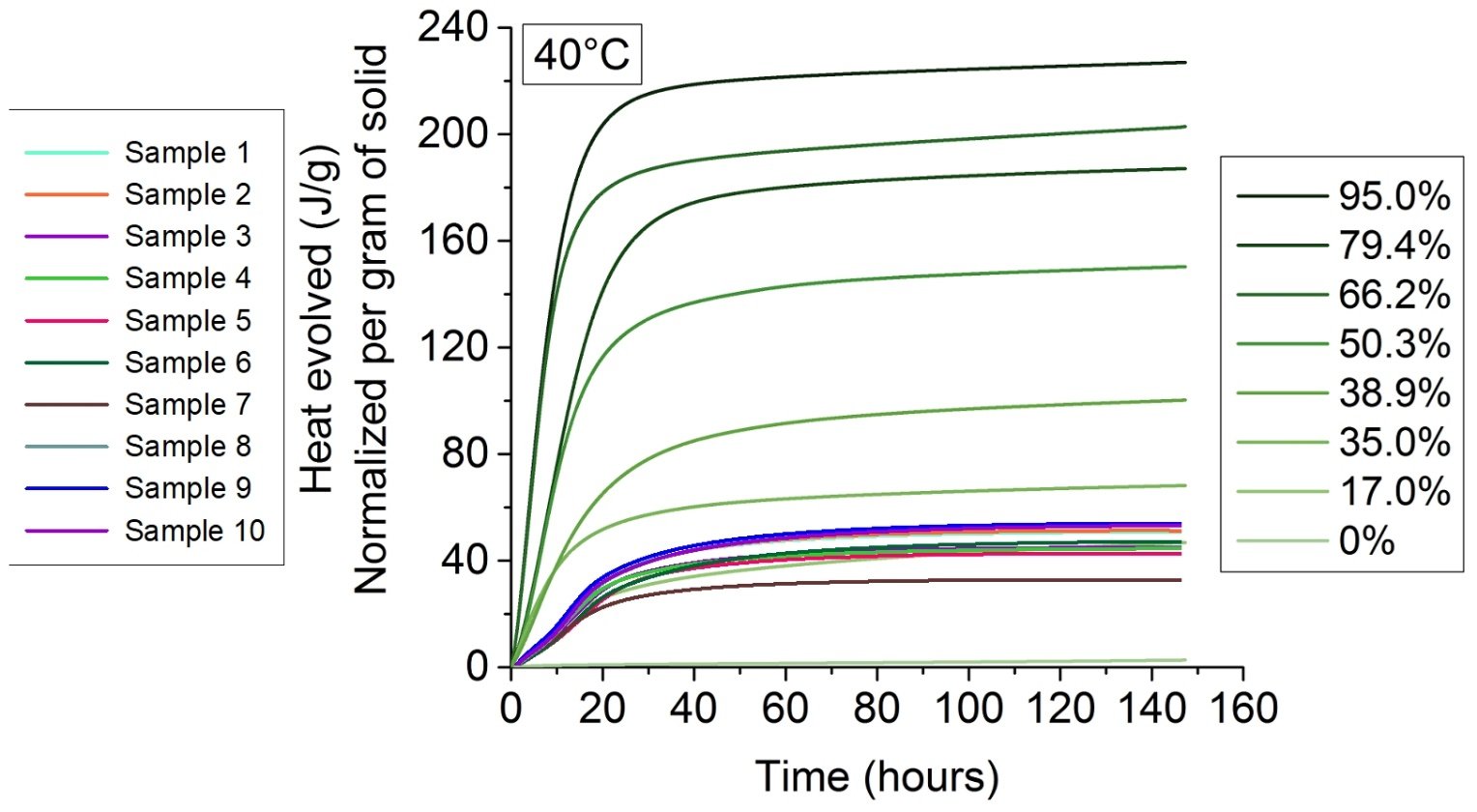
LWA suitability
London Clay pellets were fired in a kiln at different temperatures: 1140, 1160, 1180 and 1200 °C, for 8 minutes to produce lightweight aggregate. The variation in the firing temperature and sample location yielded different particle densities and aggregate particle sizes. This variation is shown in Figure 8 below.
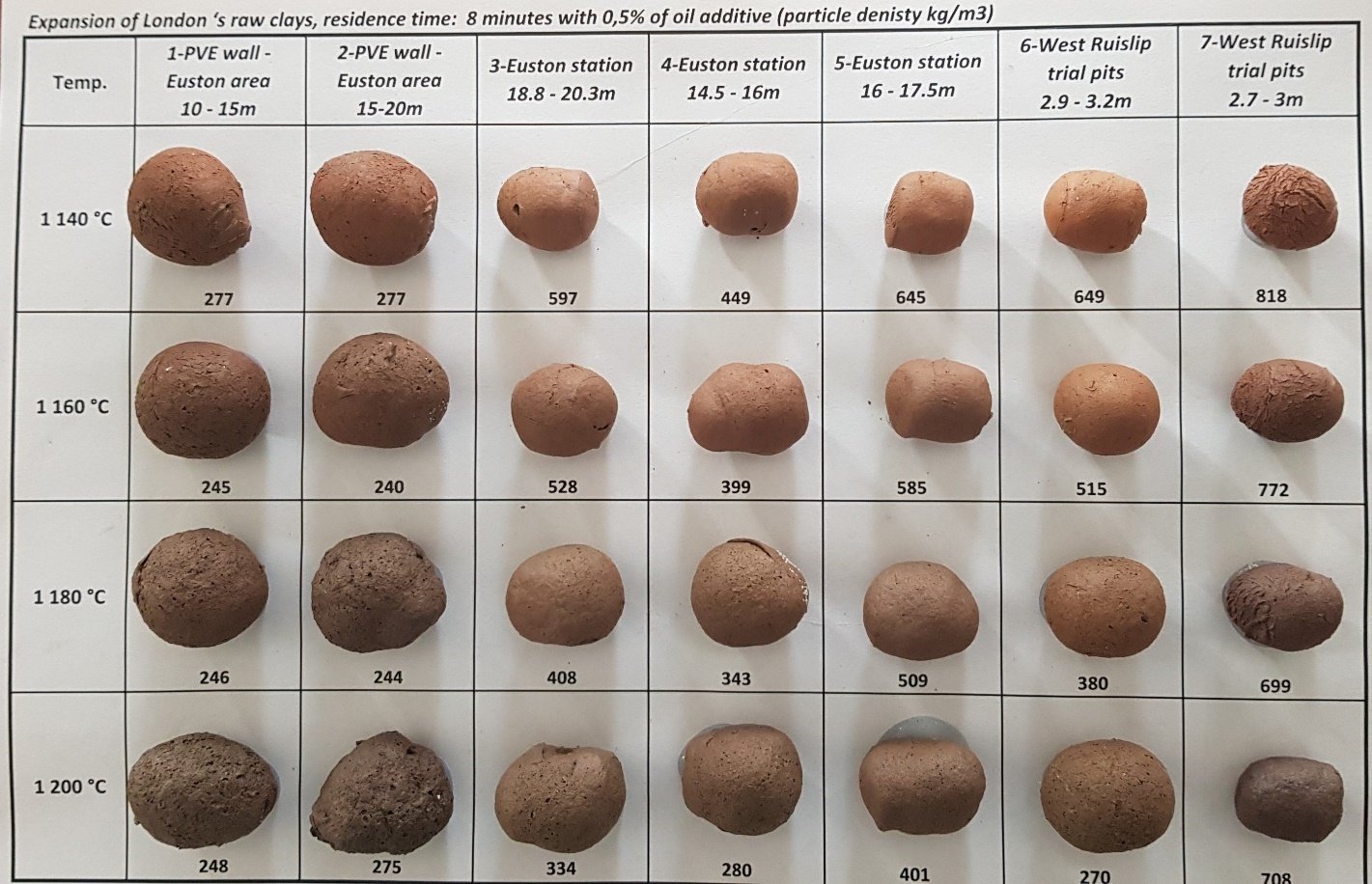
Interpretation of results & conclusions
SCM: Reactivity & concrete strength
The results showed that London Clay has relatively low reactivity potential compared with other reactive clays, such as metakaolin. However, previous work with EPFL (see Section 2.2) indicated that 28-day concrete strengths in the region of 30-40MPa are possible with a kaolinite content of approximately 17-18%. Cement replacements rates with calcined clay up to 55% are currently allowed by relevant standards (BS 8500 and EN 197-1). Such levels of replacement could be justified in low grade concrete, considering these encouraging initial strength results. While such strength grades are not sufficient for structural applications, they could be suitable for non-structural concrete elements such as walkways, mass concrete infills, invert and first stage concrete and blindings.
LWA: Expandability
Expandability results also indicated that London Clay can be suitable for producing lightweight aggregates. Most of the obtained particle densities were within the desired range, varying from 250 to 450 kg/m3, with samples 1 and 2 performing best. It is worth noting that, lower densities i.e. lighter aggregates were achieved in the current testing at lower temperatures, compared with the previous results from the Crossrail study. This is most likely owing to the use of a small amount (0.5% by weight) of organic additive (oil) that was used in the REAL processes that aids the expandability. The additional carbon impacts from the use of the organic additive against the energy savings due to the lower heating temperatures required to achieve the London Clay LWA should be assessed in future work.
Influence of stratigraphic variability
The similar isothermal calorimeter curves for all samples, except the outlier, suggested that:
a) the soil conditioning polymer-based foams used during the TBM excavation process have little or no influence, as such foams decompose at the high clay calcination temperatures
b) the variability of London Clay with regards to its pozzolanic activity and kaolinitic content is low. Once available, the soil classification tests will allow better understanding on this front.
Sample 7 is underperforming both in terms of reactivity/kaolinite content as well as in terms of expandability, compared to the other samples. As this sample was retrieved from a relatively shallow depth, it is possible that it consists of topsoil disposals and it is not pure London Clay.
Influence of pyrite
The presence of pyrite in clays may trigger sulphate attack in buried concrete, if oxidised (FeS2) under certain conditions. However, the experimental programme, specifically XRD & Rietveld refinement, suggested that pyrite transforms to iron oxide after the calcination of London Clay at 800°C, releasing SO2 as gas. This phase is commonly found in natural clays and is stable in concrete mixtures. No remaining pyrite is observed in any of the calcined clay samples after the calcination process applied. Thus, the presence of minor amounts of pyrite in the raw material does not adversely affect its potential for use as a concrete ingredient, as long as proper calcination takes place and pyrite decomposition into hematite is completed.
Summary of findings & conclusions
The material testing programme to date provided promising results regarding the suitability of London Clay for both targeted applications: SCM & LWA.
With respect to SCM, the reactivity observed in the samples via specialist testing (TGA & isothermal calorimetry – R3) suggests that London Clay qualifies to produce calcined clay for use as cement substitute. Because of the relatively low average kaolinite content determined in the samples (15-20%), low to medium strength will pursued in the trial concrete mixes containing the calcined London Clay at the next stage of REAL, targeting the most effective use of the produced SCM. High cement replacement rates will be explored at the concrete trials to maximise the value of the calcined clay as a concrete constituent. The concrete types to be tested will therefore most likely range between 20-30 MPa of strength with 30 – 70% cement replacement.
With respect to LWA, the expandability testing (EXCLAY method) performed well across the London Clay samples, with most of them reaching particle densities of <300 kg/m3 when heated to 1180°C-1200°C. The density levels along with the solid palletisation achieved, are deemed suitable for lightweight aggregate production, primarily for applications such as fill material and insulation and potentially in low strength lightweight concrete.
Next steps
REAL sustainability
HS2 is aspiring to support the UK’s transition to a net zero carbon economy and leave a positive legacy. Sustainability, innovation and collaboration are the key methods to underpin successful delivery of the project, according to HS2’s Sustainability Approach. REAL places all these three key elements at its heart, demonstrating potential for both environmental as well as financial benefits.
The Environment Case
Resource efficiency & circular economy
The REAL innovation proposal is based on circular economy principles, aiming to implement a closed loop waste-to-resource process by turning excavated material into useful construction materials with various positive impacts:
- Minimised waste streams
- Reduced transport impacts from avoided offsite waste disposal resulting in reduced vehicles movements and subsequent emissions
- Reduced need for imported construction material transported to site
- New source of valuable construction raw materials, alleviating dependence on currently diminishing reserves, like PFA and GGBS cement substitutes
Carbon emissions reduction
Direct as well as indirect carbon savings could accrue from using the calcined London Clay as an SCM. Multiple scenarios have been considered to assess the direct carbon reduction potential of the REAL SCM, if used in low strength concrete mixes in the HS2 Area South works instead of more traditional concrete options. Table 4 below summarises the assumptions, variables & results of the carbon sensitivity analysis.
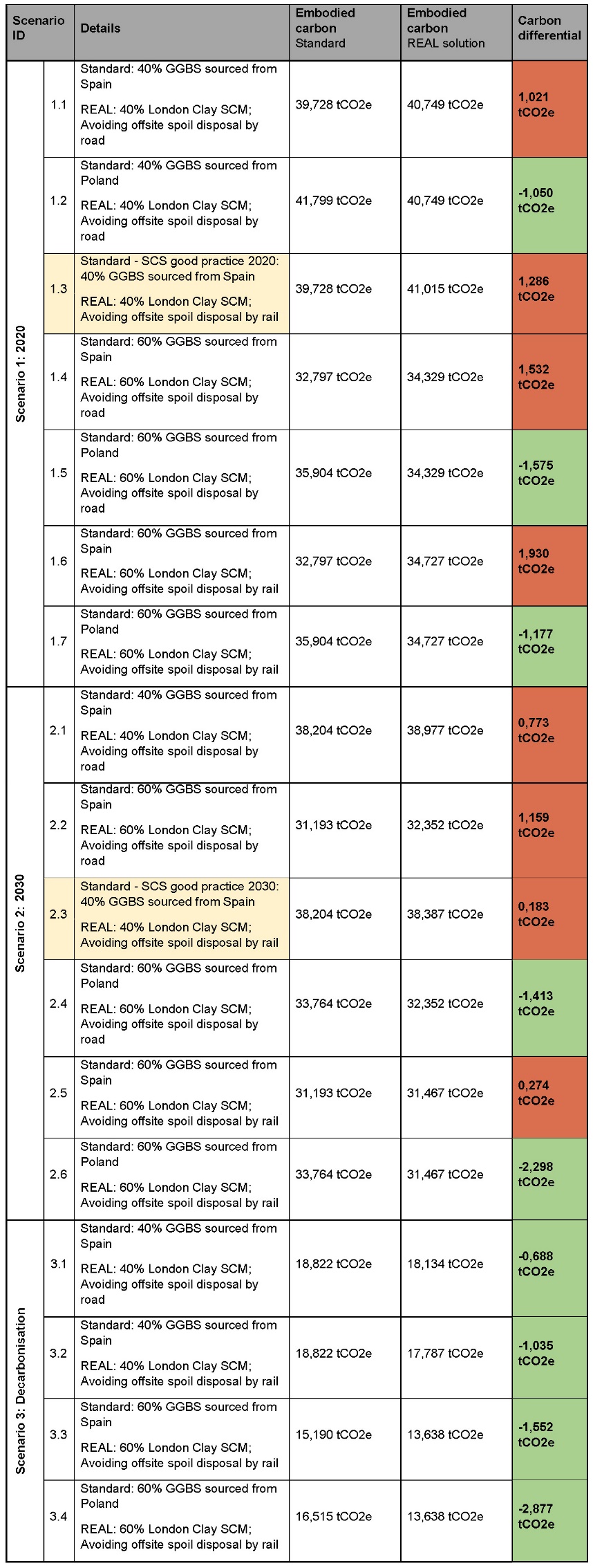
Table Notes:
- The scenarios consider production of all low grade concrete (C20/25) to form the invert & walkways for the SCS S1 & S2 tunnels (181,279 m3).
- The embodied carbon scope covers the emissions associated with the materials/products, their transport and any avoided waste disposal impacts through excavated spoil use for the London Clay SCM production (REAL scenarios).
- Concrete batching takes place at an RMC plant 50km from the production site and is brought in by mixer trucks.
- The 3 scenario categories – 1, 2 & 3, represent energy and fuel intensities used in products/processes involved for 2020 (current), 2030 (projected) and full decarbonisation respectively.
- Standard scenarios consider ordinary concrete mixes with OPC & varying levels of replacement with imported GGBS.
- REAL scenarios consider concrete mixes with OPC & varying levels of replacement with calcined London Clay SCM.
- The REAL calcined London Clay is assumed to be produced at a medium scale processing unit on site, operating over 4 years during SCS construction works.
- Main production parameters below, upon consultation with plant equipment manufacturer:
- Production rate: 1 tonne/hour
- Power consumption: 150 KW
- Natural gas consumption: 72 m3/hour
- Production process material efficiency: 95%
As expected and confirmed by the carbon analysis, the REAL SCM has a higher product carbon footprint than GGBS. GGBS being a by-product of primary steelmaking is only allocated a minor fraction of the process emissions. However, the REAL SCM carbon can significantly improve through procuring clean energy, like renewable electricity and hydrogen fuel for the production process.
It is worth noting that the sourcing of GGBS plays an important role in the carbon balance and can be the differentiating factor in determining less impactful solution. This can be observed in all scenarios where GGBS is sourced from far afield involving significant road transport (Poland), where the REAL concrete solution demonstrated lower carbon than the traditional one with GGBS. Moreover, larger production rates and efficiency of scale can potentially further lower the carbon intensity of the calcined London Clay SCM.
Construction is growing globally and so is the demand for concrete. Concrete is one of the main contributors to the carbon emissions associated with built projects and cement is its most carbon intensive constituent. Against the current climate crisis backdrop, low carbon solutions for concrete are highly sought and consequently the need for robust SCMs becomes apparent to reduce the overall demand for carbon-heavy OPC. Calcined clays like the REAL SCM, originate from abundant resources and require much lower heating temperatures to manufacture than OPC, leading to their significantly lower carbon footprint. Such SCMs can therefore help achieve wider carbon benefits by providing an additional source of cement substitutes, supplementing the traditional SCMs, whose reserves are finite and in a diminishing trajectory wherever they stem from processes being phased out e.g. PFA from the coal industry.
The Business Case
Beyond the environmental benefits, there is indication of potential economic benefits from the implementation and roll out of REAL: early analysis of the cost forecast shows potential savings compared with the traditional construction approach. Key benefits identified are listed below:
- Cost savings from eliminating waste transport and disposal offsite
- Logistics benefits from reduced long-distance material movements
Fine tuning of the excavated material processing rates in line with the progress of the works and resulting volumes of arisings could facilitate optimisation of the scale and production process.
Additionally, further available markets for the new product should be identified. Depending on the production scale, the calcined London Clay SCM could be exported to other HS2 Phase One contracts as well as other construction projects in the vicinity that don’t have direct access clay geology and could also benefit from using it for cement substitution in concrete. Scaling up the processing of soil arisings and the SCM production rate, accruing benefits could be significantly amplified, potentially turning this innovation into a profitable new enterprise, closer to a financially viable circular construction model.
A preliminary estimation exercise of the logistics and costs of the production and use of calcined London Clay in concrete has been carried out. Monte Carlo analysis was run for the different scenarios in order to evaluate the risk of cost deviation, with the following variables: energy & fuel price, energy demand for the mobile production plant, labour costs, price of commonly used concrete binders for such applications in line with BS8500-1 and the equipment resale value.
Lower grade unreinforced concrete, used in for the invert, first and second stage concrete and walkways, was considered. Two different percentages of cement replacement with calcined London Clay SCM were examined: 50% & 70%. As mentioned above, the total volume of lower grade unreinforced concrete for the HS2 Area South tunnels is estimated to be approximately 180,000 m3. However, the calcined London Clay SCM production rate feasible with the small-scale on-site plant assumed cannot compete in pace with the faster concrete placement rates expected to be employed by the construction teams at this stage. Therefore, two different plausible options have been considered, where 40% and 60% of the total low grade concrete volume have been replaced with concrete featuring varying percentages of the calcined London Clay SCM in lieu of the commonly used mixes for such applications.
A summary of the main results of the cost analysis can be found in Table 5. The cost savings are calculated against the total cost for the standard lower grade concrete solution (as per above) that was estimated to be approx. £3,750,000.
All scenarios indicate that using the calcined London Clay SCM can result in a more cost-effective solution compared to that ordinary concrete mixes, with potential savings up to 45%.
Scenarios | Utilisation in total lower grade concrete volume | Cement replacement with calcined London Clay SCM [%] | Mean cost estimate | Mean cost savings estimate |
---|---|---|---|---|
#1 |
40% of total volume [72,000 m3] |
50% of total binder |
£2,145,000 |
£1,605,000 |
#2 |
40% of total volume [72,000 m3] |
70% of total binder |
£2,100,000 |
£1,650,000 |
#3 |
60% of total volume [108,000 m3] |
50% of total binder |
£2,100,000 |
£1,650,000 |
#4 |
60% of total volume [108,000 m3] |
70% of total binder |
£2,050,000 |
£1,700,000 |
An initial estimate on the return of investment indicated that payback of the costs for the mobile calcined clay production equipment, could be achieved approximately halfway through the concreting period and financial savings would accrue thereafter.
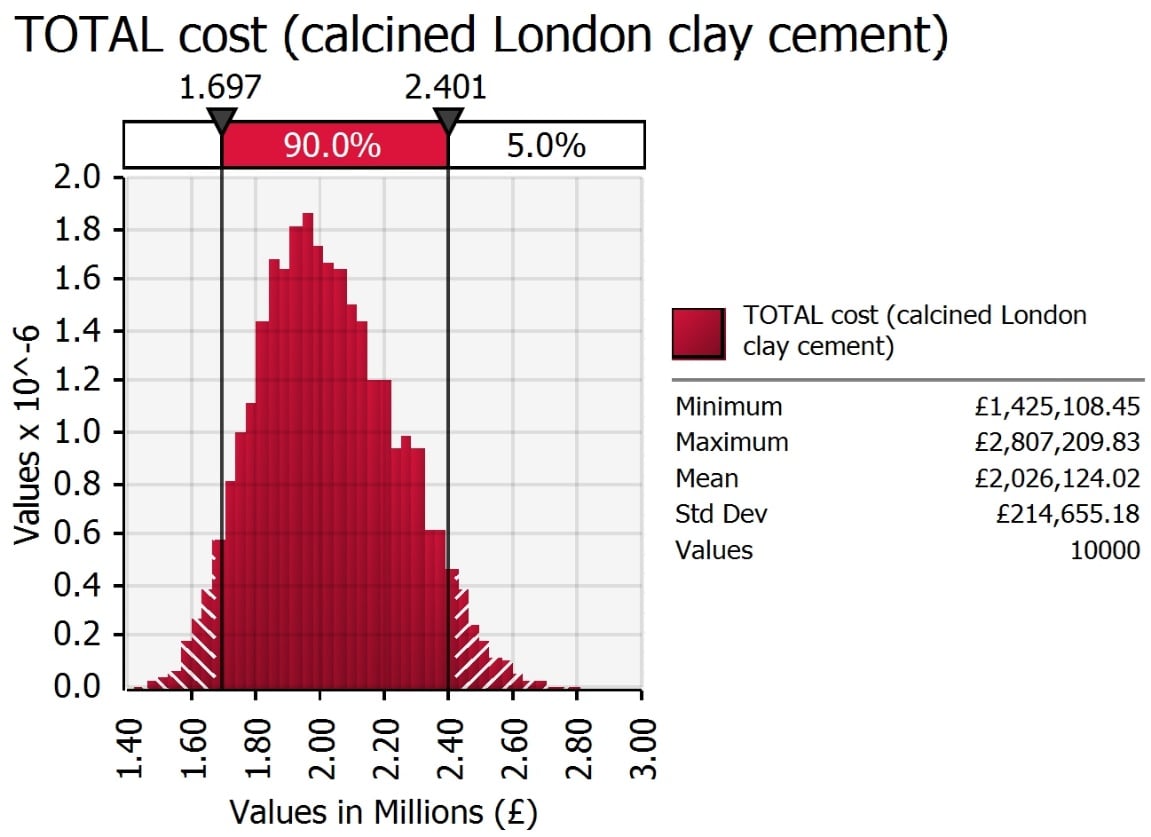
Future work
In the light of the positive results of REAL Stage 1a, as outlined in this paper, the project team’s intention is to proceed with the study, subject to securing funding – see Figure 1. The immediate next step is the preparation for Stage 1b to investigate of behaviour concrete prototypes containing the London Clay derivatives. A detailed proposal and associated budget covering the testing programme, technical details and logistical issues for the mobile production unit and a comprehensive business case, based on the preliminary cost analysis presented above, will be compiled and submitted to HS2 Innovation panel. The concrete mix designs will be optimised with a view to maximise the cement replacement rates, as per the conclusions in 4.5 above. The calcined London Clay will most likely be combined with OPC and limestone powder to opt for a ternary binder system, employing the most efficient known way to use calcined clays in concrete. The experimental regime for the concrete trials will examine the pertinent properties of both fresh (flow and workability, density) and hardened concrete (compressive and flexural strength, density). Upon REAL Stage 1b completion with successful results, Stage 2 will be commenced to acquire, set up and operate the London Clay derivatives production unit on-site and utilise the outputs in designated concrete structures in the HS2 works.
The full programme of REAL aims to trial and verify an open source, scalable, modular and industry flexible process, whereby any infrastructure project involving large scale excavations could utilise the natural resource of London Clay. Regarding HS2 specifically, the sheer scale of each contract and the overall project present both a challenge and an opportunity to transform the construction industry towards a net zero carbon future.
References
- Antoni, M., Rossen, J., Martirena, F. and Scrivener, K., (2012). Cement substitution by a combination of metakaolin and limestone. Cement and Concrete Research, 42(12), pp.1579-1589
- Badogiannis, E., Kakali, G. and Tsivilis, S., (2005). Metakaolin as supplementary cementitious material. Journal of Thermal Analysis and Calorimetry, 81(2), pp.457-462.
- Boarder, R. and Owens, P. (2014). ”The Innovate 18 project: Light weight aggregate for concrete, 21 August 2014; Crossrail Ltd: INV00031 Manufacture of Lightweight Aggregate from London Clay
- Bernal, S., Juenger, M., Ke, X., Matthes, W., Lothenbach, B., De Belie, N. and Provis, J., (2016). Characterization of supplementary cementitious materials by thermal analysis. Materials and Structures, 50(1).
- Fernandez, R., Martirena, F. and Scrivener, K., (2011). The origin of the pozzolanic activity of calcined clay minerals: A comparison between kaolinite, illite and montmorillonite. Cement and Concrete Research, 41(1), pp.113-122.
- Huggett, J. and Knox, R., (2006). Clay mineralogy of the Tertiary onshore and offshore strata of the British Isles. Clay Minerals, 41(1), pp.5-46.
- Scrivener, K., Martirena, F., Bishnoi, S. and Maity, S., (2018). Calcined clay limestone cements (LC3). Cement and Concrete Research, 114, pp.49-56.
- Wimpenny, D., (2009). Low Carbon Concrete – Options for the Next Generation of Infrastructure.
- Zhou, D., Wang, R., Tyrer, M., Wong, H. and Cheeseman, C., (2017). Sustainable infrastructure development through use of calcined excavated waste clay as a supplementary cementitious material. Journal of Cleaner Production, 168, pp.1180-1192.
Peer review
- James Langstraat, Sustainability LeadHS2 Ltd
- Paul Lippitt, Waste and Materials Recovery ManagerHS2 Ltd