Health and safety by design: managing risk on Enabling Works
High Speed Two’s (HS2’s) aspiration is to manage health like safety. The Enabling Works South contractor approached this is by incorporating safety and health risks in a master register, coded by hazard type. Through sharing with the supply chain, nearly 20% of risks were identified as being related to potential occupational health hazards that traditionally would have been overlooked. This increased emphasis on health risk assessment identification also provided confidence to the Principal Designer that the principles of prevention in our designs were actively being employed. The master register has allowed feedback and knowledge sharing including best practice on risk mitigation. This has successfully linked to the BIM model to enable others to understand risks.
This learning will be of interest to other projects in developing their risk management systems and in particular the incorporation of health risk assessment into that process.
Background and industry context
The Enabling Works Contract (EWC) on the southern section of High Speed Two (HS2) phase one includes demolition of buildings within the wider Euston area, utility diversions, environmental and ecological monitoring and a programme of historic environment and archaeological activities, delivered by the Costain Skansja joint venture (CSjv).
The CSjv delivery strategy was to utilise a series of autonomous work packages, grouped in regional parcels. These provided flexibility to manage emerging and variable scopes including surveys, heavy civil engineering, utility diversions and demolition works. Over the life cycle of the EWC, over 90 individual work packages will have been delivered including design only, construction only and design and construction packages. Although this delivery model is well suited to enabling works contracts, it was important to be able to share best practice across work packages and to understand what the overall highest EWC risks were. The master register addressed this by ensuring consistency and sharing of best practice across the individual work packages, as well as the identification of the EWC highest risks.
HS2 aspiration is to treat health like safety, an emphasis historically lacking on other infrastructure projects. The master risk register ensured that both health and safety risks were identified and shared across work packages, together with best practice in risk mitigation. As this developed, assessing and feeding back how designers were implementing the principles of prevention was undertaken.
Health and safety risk management
To allow risks to health and safety to be assessed, four types of risk assessments covering the relevant aspects of each work package lifecycle were produced (Figure 1).

- Designer’s Risk Assessments (DRAs) included those undertaken for both temporary and permanent works. If the work package was design-only, residual risks were identified in the DRA and transferred to either the relevant construction work package or to HS2 for issue to the future constructor.
- Risk Assessment Method Statements (RAMS) managed risks that had not been eliminated by the designer.
- Health Hazard Evaluation and Mitigation Plans (HHEMPs) provided an enhanced assessment of specific occupational health risks identified during design relevant to the work package and how they were to be managed during construction.
- Residual Risk Assessments were produced on completion of a construction work package and were detailed in the relevant health and safety file (HSF), for management by future parties.
To ensure consistency in health and safety risk management and appropriate focus on higher risks across work packages, a system was required to assimilate the assessments. This paper discusses how CSjv’s Lead Design Team1 addressed this issue on EWC.
Initially, each work package produced risk assessments following Figure 1 in isolation. As increasing numbers of work packages were instructed by HS2 to the EWC, to ensure consistent health and safety risk management, continued compliance with both CDM2 and HS2 requirements and oversight of all the work packages and sharing of best practice, EWC considered using Safetibase3 an i3P platform to manage their risk assessments. However, at initial contract stages, this was not considered as developed sufficiently for a contract the size of EWC to adopt and so alternative risk management systems were evaluated.
The key considerations were:
- To ensure all health and safety risks were appropriately assessed.
- To enable continuous improvement and feedback to the supply chain.
- To facilitate sharing of best practice risk mitigation.
- To understand overall contract highest risks to health and safety.
- To provide consistency in risk assessments across all work packages.
- To allow classification of risks to enable review and evaluation of metrics.
Initial steps
After a review of suitable software packages, SharePoint lists was initially adopted to hold a master CDM risk register of all DRAs. This was to ensure that EWC and the supply chain could easily access and share the information, without a requirement for purchasing and training in specialist software. It was also compatible with excel which formed the basis of most risk assessments. Information was inputted via excel, which many of the individual work package risk assessments already used. SharePoint lists allowed the Master Risk Register to be accessed by EWC, their supply chain and by HS2’s Principal Designer Representatives. The Master Risk Register used the standard HS2 DRA template with the following fields:
- Reference number
- Location
- Classification
- Hazard description
- Risk description
- Current risk impact
- Design mitigation action
- Risk owner
- Residual risk
- Interface description
- Comments
- Status
- Residual risk owner
- Design document number
Additional columns were added to provide focus on:
- A risk reduction index (Winters4)
- Risk origin and type
- Occupational health
- Individual work package SharePoint details
- A 9 x 9 hazard class and category system adopted from that used at London Bridge station redevelopment (Figure 2)
- A free text field for additional notes
- Classification of residual risk in the overall context of EWC to allow identification of top risks
- Risk location coordinates (for as-built model)
These additional columns allowed interrogation of specific risks such as those related to occupational health or environment, by sorting (Figure 2). They also ensured consistency and enabled identification of the highest risks across the whole EWC contract.

Only DRAs were proposed to be added to the Master Risk Register initially, prioritised by order of importance. However, health and safety risk management including the transfer of risks that have not been eliminated by the designer or constructor, is a process through a project lifecycle (Figure 1) and to only input DRAs would have skewed reporting on EWC’s top risks.
As an example, a DRA for office refurbishment had a high residual risk of leptospirosis because the designer was unable to design out this risk during drainage works associated with toilet refurbishment. However, the corresponding RAMS was able to manage this risk to a low level after control measures of use of PPE, good site hygiene and welfare facilities were introduced.
This led to all health and safety risk assessments being added to the Master Risk Register, and the residual risk of each hazard being re-categorised in the context of the overall EWC risk hierarchy, to enable EWC to understand their highest risks and review these with the Principal Designer.
A series of roadshows were presented to all work packages, engineering teams and the client’s Principal Designer representatives to enable them to understand the risk management process and the role of the Master Risk Register, as well as a refresher on CDM and HS2 health and safety processes. As new risk assessments were produced at work package level, these were progressively added to the Master Risk Register to allow for wider review and sharing.
Maturing of risk management processes
Once the Master Risk Register was established, and risks assessments added to allow use of the centralised data, regular feedback reports were produced on the quality of the risk assessments. These were issued to the supply chain and provided feedback on common issues relating to assessing risk, such as missing information and inconsistencies in risk scoring. The aim of these feedback reports was to share best practice, continuous improvement and included a link to the Master Risk Register.
To ensure the feedback reports also provided leading indicators of the EWC risk management process, hazard classes and hazard categories were used. The top six occupational health risks (noise; vibration; COSHH; manual handling; mental health; dust and particulates) were specifically reviewed in detail against each of the principles of prevention5 and these were re-assessed for the next issue of the feedback report to determine any changes in mitigation. Table 1 is included as an example of the review undertaken of noise mitigation in EWC risk assessments against each of the principles of prevention. Percentages are the proportion of risk mitigations against each of the principles of prevention at the time of the feedback report. Figures in brackets are those produced for the previous report, showing changes as the EWC contract progressed.
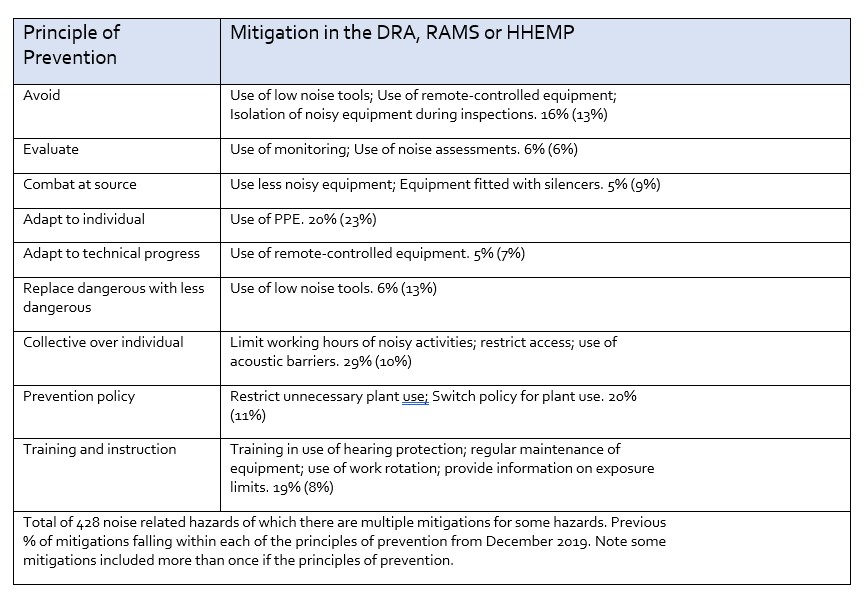
Assessing against each of the principles of prevention enabled EWC to understand how designers and contractors were managing their risk mitigations. Some risk assessments included multiple mitigations to the same risk, which encompassed more than one of the principles of prevention.
The Master Risk Register was used by new work packages to prompt reviews of best practice risk mitigation for similar hazards, by sorting on hazard classes and categories (Figure 2) and modifying/adapting similar existing assessments for new works, which was a more efficient process than starting from the beginning. As an example, demolition work packages could use similar demolition risk assessments as the basis for developing their own assessments, including acting as an aide memoir for considering hazards.
A further benefit of the feedback reports and the Master Risk Register was to reinforce the requirement to risk assess works and to ensure staff were aware of what constitutes design risk and their legal responsibilities under CDM2.
The register and associated feedback reports also provided another method of building EWC’s strong health and safety culture, which was embedded in the contract, and demonstrated to the Principal Designer that EWC were managing their risks across all their work packages, as well as continuously improving their risk management processes.
Period reporting
Adoption of a centralised master register of health and safety risk assessments, containing hazard classes and categories, allowed EWC to provide period reports on their health and safety risks through use of PowerBI. The re-assessment of health and safety risks provided a ranking for the entire EWC contract and enabled the top ten highest residual risk items to be reported. These did not tend to change between reporting periods unless works were handed over or de-scoped. Figure 3 shows an example reporting dashboard. The ‘No. by Hazard Class’ pie chart shows the breakdown of all EWC health and safety risks by hazard class. As would be expected for an enabling works contract, the majority fall within the site and environment hazard classes. The six occupational health charts, derived from all DRAs, RAMS and HHEMPS, show the impact of EWC risk mitigations. Those coloured blue had the greatest impact by reducing high risk activities to low risk after mitigation. Tracking every month provided additional focus on the success of occupational health risk mitigation as the project progressed. As the project moves into handover phase, reporting can be easily adapted to show residual risk transfer. Use of PowerBI provided flexibility in reporting and allowed data to be provided to other initiatives within the contract, such as incident investigation and health and safety improvement trials.
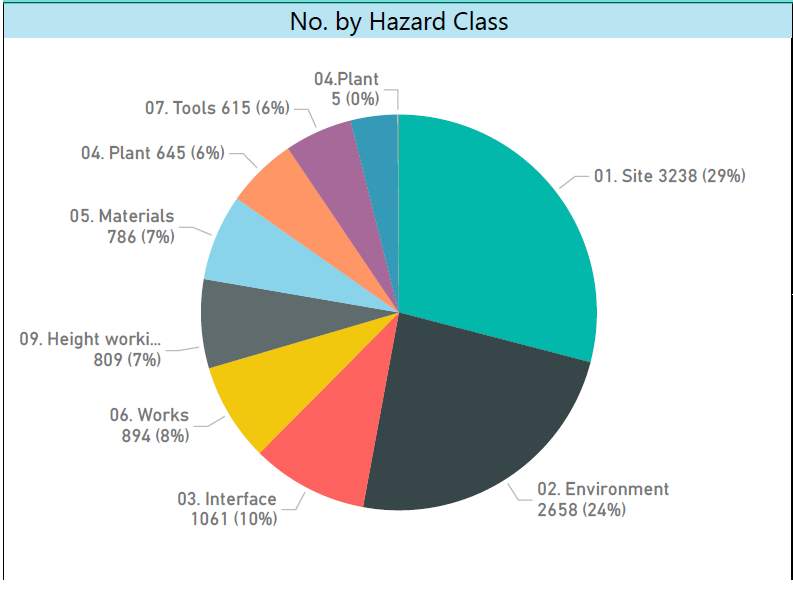
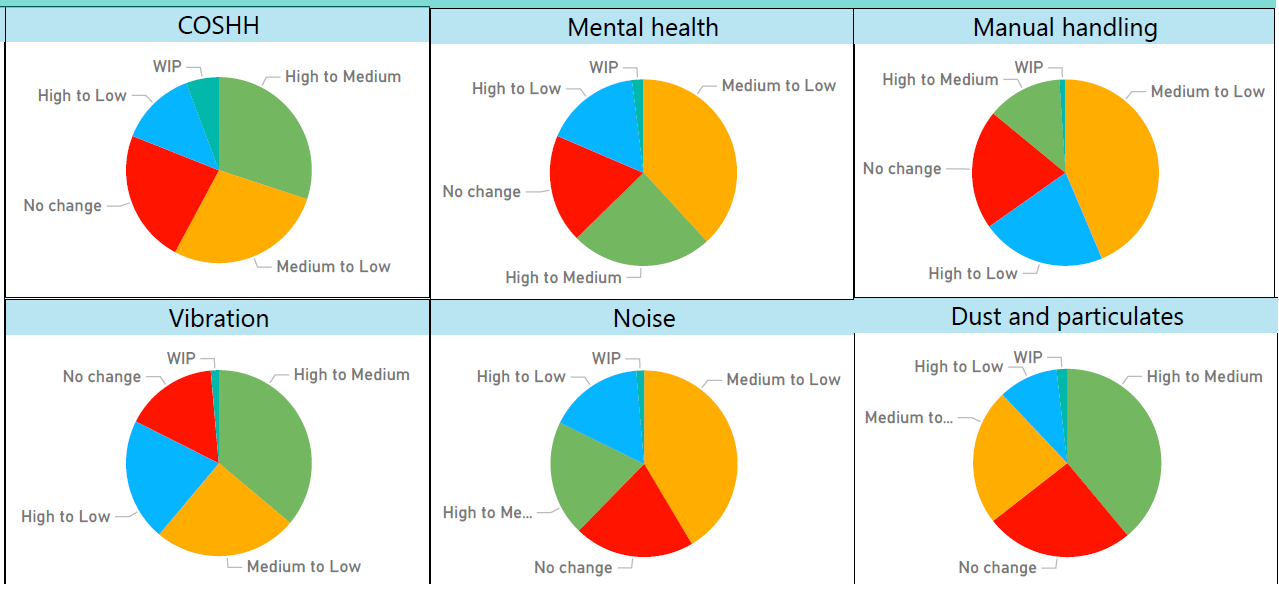
Risk transfer in BIM
Use of the Master Risk Register allowed transfer of residual risks to the EWC BIM model. These were completed for each work package and coordinates added to the Master Register which then linked to the BIM model following the principles of PAS1192-6:20186 (Figure 4). Risk symbols (totems) for residual risks were in the same format as the adjacent Skanska Costain STRABAG joint venture (SCSjv) main works contract for consistency. The register also allowed tracking of work packages which still required residual risks to be prepared in advance of their handover dates. Once residual risks for a package had been identified, a workshop was held for both risk review and to ensure locations were the most appropriate for the communication of risk (Figure 5). This was an efficient method of working and could be completed in approximately 30 minutes for a single work package, due to the elimination of most risks at design or construction stages and the attendance of the BIM manager.
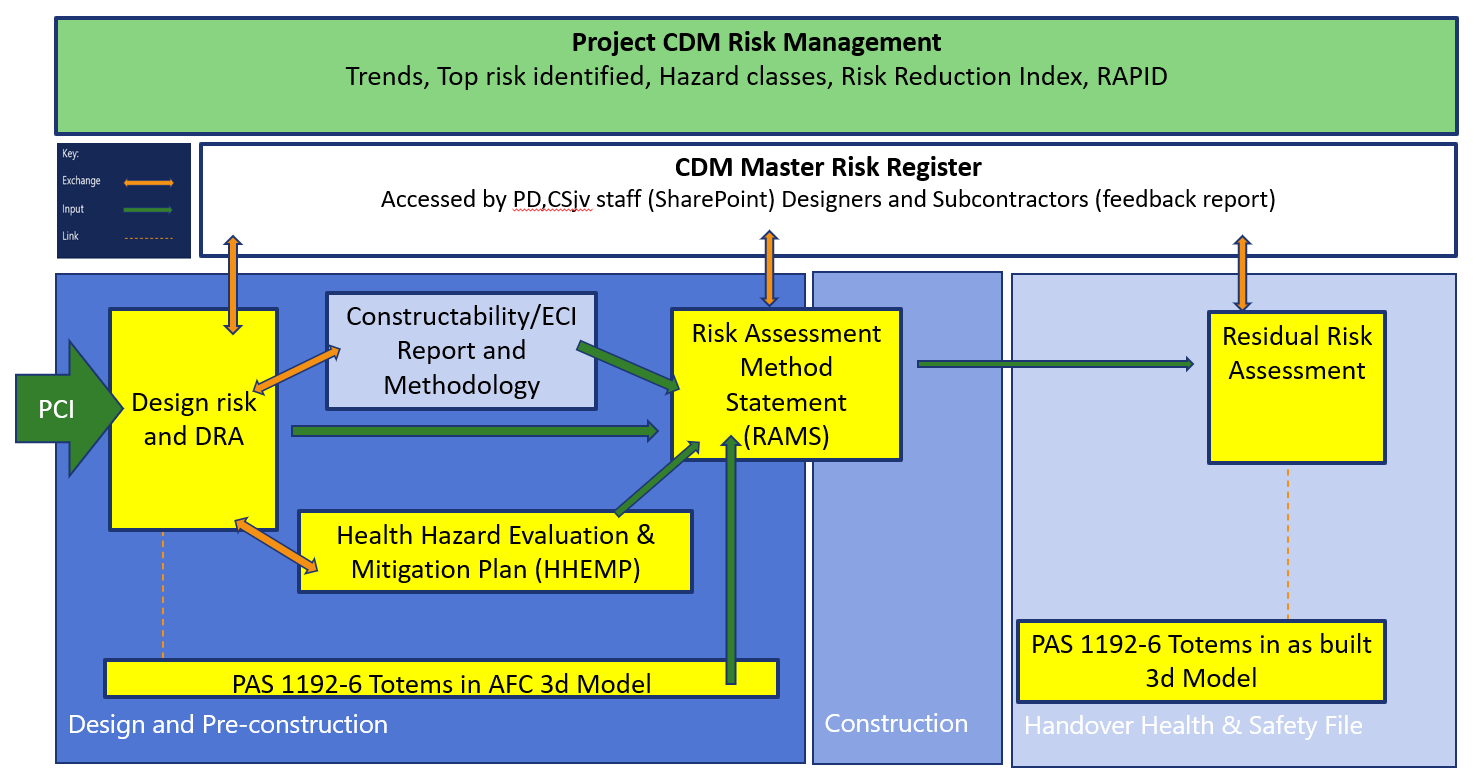
PCI Pre Construction Information; ECI Early Contractor Involvement; PD Principal Designer; RAPID Record Apply Pin-Point Inform Develop; AFC Approved for Construction
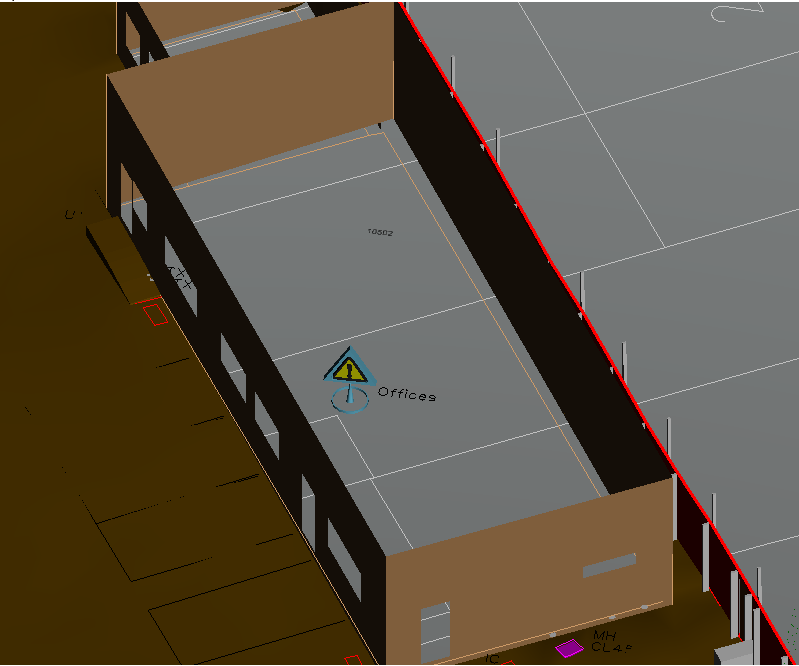
Lessons learned and successes
Use of a central health and safety risk register and the associated feedback reports provided consistency on the EWC contract across over 90 different work packages of varied scope. It allowed sharing of best practice and could be used by work package teams as the basis for preparing risk assessments for newly instructed work, adapting them and ensuring best practice in mitigation was adopted.
SharePoint lists was chosen as the platform for the register to enable embedment within the EWC SharePoint site and to facilitate sharing with the supply chain and Principal Designer. Consideration had been given to use of a database such as MS Access, but a readily available package was required by EWC and their supply chain. Challenges were faced in the functionality of SharePoint lists as the register grew, due to the list view threshold which is set at 5,000 entries. Although a work around could have been undertaken in SharePoint lists, the decision was made to use an excel register once 5,000 risks were reached but to continue to use all the fields from the SharePoint lists register and provide access to the excel register in SharePoint. Excel has a row limit of over 1 million which was far more than required for the EWC register. Functionality with PowerBI was maintained and excel had the added advantage of familiarity by all users. If undertaking the same exercise again, Safetibase3, which is now developed and was used successfully on one EWC work package would be adopted. This would have the added benefit of more rigorously controlling risk transfer between design, construction and handover activities.
EWC and their supply chain generally used a 5 x 5 scoring system to assess likelihood and severity, but some sub-contractors used 3 x 3, 4 x 4, 6 x 6 or even more complex systems. These were adapted to ‘fit’ the Master Register 5 x 5 scoring system. Use of risk scoring systems was invaluable when managing large numbers of risks, to ensure those with higher residual risks received increased attention. However, use of an independent review of risks as they were added to the register, reviewing against the principles of prevention and CDM workshops with the work packages, ensured that numbers were not just being added to the register irrespective of the suitability of the mitigation proposed. A review independent of the work package team ensured this was achieved and was one of the areas discussed by White6.
Adding a ‘health’ column in the risk assessment template whilst simple, focused designers on considering occupational health as well as safety. Occupational health risks were identified in 17% of all EWC design risk assessments which may be higher than what would have traditionally been considered for a similar contract. Occupational health risks accounted for 22% of all risks identified in the Master Risk Register.
A risk reduction index was added to the register and provided the basis of a quantitative approach to understanding the reduction in risk before and after mitigation based on a perceived benefit. Further details are provided by Winters4.
Use of a centralised risk register enabled tracking of individual work elements, highlighting where risk assessments had not been produced. As an example, it could be used to highlight where a structural assessment, used as the basis for future demolition methodologies, had not adequately risk assessed all the proposed works. Feedback was provided to the relevant team which led to improved assessment of risks, including over-arching risk assessments, not just those of individual elements.
The EWC risk management process described in this paper was successful and the principles were transferred to the adjacent HS2 main works civils contractor SCSjv. Close links with equivalent counterparts in SCSjv ensured lessons learned were shared between contracts.
Recommendations
The following are recommendations for managing health and safety risks learnt from over three years of EWC works.
Adopting standardised likelihood and severity definitions for the risk assessment matrix across the supply chain eases input and allows easier communication across the contract. This may lead to some of the supply chain having to change their own procedures but does ensure consistency. It also prevents the need for re-assessment of risk when reviewing overall contract health and safety risks, as all risks to health and safety are to the same risk matrix scoring system.
It was important to undertake risk reviews and to ensure that residual risk scores were a true reflection of the successful impact of risk mitigation, rather than just being reduced after mitigation irrespective of the suitability of the proposed mitigation.
Ensuring teams input their risk assessments into the central data source increases ownership and reduces data entry tasks for those not involved with the work packages. This would be addressed using Safetibase3 or a similar system.
Oversight of all health and safety risk assessments was a positive benefit of the CSjv risk management process and ensured consistency and a framework for continuous improvement and feedback. Use of the data by other work packages as the basis for developing their own risk assessments led to efficiencies in risk management.
The risk reduction index was an attempt to quantify the success of mitigations. There is scope when coupled with PowerBI to link other information sources to a master health and safety risk register such as person hours; concrete poured; material excavated; dust prevention measures; COSHH data. This will allow further occupational health benefits of risk management on an individual risk basis to be realised and the data recorded to provide evidence of the positive effects of risk mitigation.
The final benefit of risk management was the positive impact on EWC’s safety culture, increasing staff competencies relating to risk management, enabling good communication between parties and to enable active cooperation, all principles of CDM2.
Acknowledgements
The authors wish to thank all those who have contributed to the successful implementation of EWC’s risk management process. These include:
- Andre Stockbridge (formerly CSjv Head of Engineering)
- Richard Collins (formerly CSjv SharePoint expert)
- Sandra Winters (CSjv Occupational Health)
- Work Package Managers
- Design Managers
- Delivery Directors
Thanks also go to HS2 Principal Designer representatives, particularly Alasdair Hassan and Graham Church who were consistently supportive in EWC’s management of risks to health and safety.
References
- White, I, Harris D and Ridley, M. Lead Design Team embedded as a ‘Critical Friend’ within the Contractor Team (CSjv on HS2’s Enabling Works South) achieved high quality assured deliverables
- Health and Safety Executive. Construction (Design and Management) Regulations 2015. HSE Books. 2015
- Safetibase [Accessed 2 February 2021]
- Winters, S. RAPID Response
- Legislation.gov.uk. Management of Health and Safety at Work Act 1999. [Accessed 3 February 2021]
- BSI. London. PAS1192-6:2018 Specification for collaborative sharing and use of structured Health and Safety information using BIM. 2018