Transformation of London Clay into construction resources: Calcined London Clay (CLC) as Supplementary Cementitious Material (SCM) in concrete mixes
This study has shown that London Clay, that is moderately reactive, can be successfully processed into Calcined London Clay (CLC) to be used as an alternative cementitious material in concrete. Concrete mixes containing CLC have been tested and have demonstrated robust performance in terms of both fresh and hardened properties.
Building upon prior relevant work, London Clay samples from 3 different excavation locations have been investigated in terms of both raw and calcined properties and approx. 200kg of CLC were industrially produced with material from one of the locations and used for designing and testing concrete mixes containing it. 13 concrete batches with 260 – 307 kg of total cementitious material, 50%-70% wt. replacement of Portland cement with CLC and optimised admixture levels have been tested so far and displayed adequate strength development (average of approx. 45MPa at 28 days), workability and workability retention.
Using CLC as a cement alternative in concrete can have significant environmental benefits and decarbonisation potential due to its lower carbon footprint compared to Portland cement and the abundance of London Clay as a raw material.
The learnings from this study are relevant to other projects, particularly in the London area, as well as the wider concrete and construction industry. More work is however needed to verify the findings with further testing results and also investigate further CLC concrete aspects such as durability.
Background and industry context
Environmental sustainability and the role of concrete in it
The need for more sustainable practices across all sectors and activities in today’s wide environmental crisis is evident and well documented. The construction industry plays a significant part in it with extensive resource use, emissions of Greenhouse Gases (GHG), and overall pollution risks. Particularly major projects, with high requirements for both materials, energy and water, complex logistics and generating large waste quantities, can incur substantial environmental impacts and therefore call for careful addressing of such challenges.
Concrete is a key construction material and extremely widely used due to its excellent strength and durability properties, versatility, profusion and widespread nature of its raw materials and relatively low cost. Portland cement (PC/clinker) is the main contributor to concrete’s embodied carbon footprint, typically accounting for over 75% thereof in most mixes, according to current practice. At global scale, cement production yields about 14 billion tonnes of material per year requiring vast amounts of raw materials (primarily limestone and clay) and energy and is responsible for approx. 7% of all energy- and process-related CO2 emissions annually. [1][2]
Due to the apparent significance of the cement and concrete sectors for transitioning into a more sustainable economy towards net-zero carbon, decarbonisation pathways have been developed over the past years by industry associations (e.g. GCCA, LCCG, etc.) and businesses as well as by international organisations (e.g. IEA, ECF, etc.) and governments. Alternative cementitious materials (binders) feature as an essential part of the solution in all of them yet with a relatively smaller contribution compared to other technologies with higher uncertainty such as Carbon Capture, Utilisation & Storage (CCUS), as also noted by Marsh et al. [3] The fairly low future emissions reduction potential attributed to alternative binder materials in most decarbonisation roadmaps may be due to the progress made so far in cement replacement which has already realised part of the carbon mitigation potential as well as the limited alternative cementitious materials currently readily available at scale. Yet pursuing promising solutions for cement alternatives can add to this potential more imminently and confidently compared to more complex technological options with less technical readiness and more limitations.
Stakeholders from all facets of the concrete value chain are currently engaging in looking for more sustainable concrete solutions in the backdrop of the environmental urgency and race to net zero by 2050: cement and concrete producers, academics and researchers, construction investors and clients as well as professionals of all relevant trades: designers, consultants and contractors.
Calcined London Clay – key potential benefits
Traditional cement (clinker) is manufactured by gradually heating minerals, mainly limestone, to approx. 1450oC. The first key chemical reaction that that takes place along the process is the breakdown of limestone via calcination – CaCO3 à CaO + CO2. The CO2 released through it accounts for approx. 60% of all CO2 emissions from clinker production, with the remaining 40% owing to fuel combustion to reach the high temperatures required. [4][5] Further reactions occur thereafter between CaO and the rest of the minerals in the mix to form the final binder product – clinker.
Calcined clay production is expected to have significantly reduced overall carbon emissions compared to PC manufacturing, primarily due to avoiding the CO2 emissions from limestone breakdown but also due to the potential for lower energy/heat requirements of the calcination process, especially upon optimisation of clay type selection and calcination methods. In the production of calcined clays, the calcination reaction is fundamentally different for clays compared to limestone and forms different products – alumina silica phases and water via dehydroxylation, and therefore does not give rise to CO2. Minor amounts of carbon dioxide emissions are only expected when calcite/carbonate impurities are mixed in the clays. [6] The temperatures required for clay calcination are also significantly lower – typically 700-800oC, than those required for clinker production. However, there are further parameters influencing the energy/heat demand of the process, such as the calcination method and its efficiency as well as the type of clay and its moisture content. [7]
Moreover, calcined clays can play another important role in global concrete decarbonisation from the resource availability perspective due to their wide occurrence. Calcined clays can offer an additional option to the restricted current commercial cement replacement alternatives such as GGBS and PFA, that are by-products of other carbon-intensive industries. According to recent studies [8], the total supply of GGBS – one of the two most used cement alternatives, can only suffice for approx.10% of the cement replacement in global concrete demand and this percentage is forecasted to remain quite stable over the coming decades.
The circular approach taken by REAL, where excavated London Clay, that would otherwise be treated as waste, is studied for its suitability to be repurposed and upcycled into a Supplementary Cementitious Material (SCM), adds another dimension to the resource efficiency potential of the undertaking. Use of excavated clays from construction projects can contribute towards waste minimisation as well as reduce the need for virgin materials extractions with the associated depletion of habitats.
REAL – Aims and previous work
REAL was designed to explore the potential of London Clay to be transformed into high value construction resources to address the above challenges of decarbonisation, resource efficiency and waste reduction in construction in a more sustainable fashion. The main aim of the REAL feasibility study is to unlock the use of materials derived from excavated London Clay arisings from project operations – that would otherwise constitute waste requiring disposal, in construction works. REAL assesses the viability of two clay derivative products: Calcined London Clay (CLC) as cement replacement in concrete – which is the main focus of the REAL project, and expanded London Clay as lightweight aggregate (LWA). The initiative is not only relevant to HS2 works but could also be useful for other infrastructure projects, particularly in the London area, as well as the wider industry.
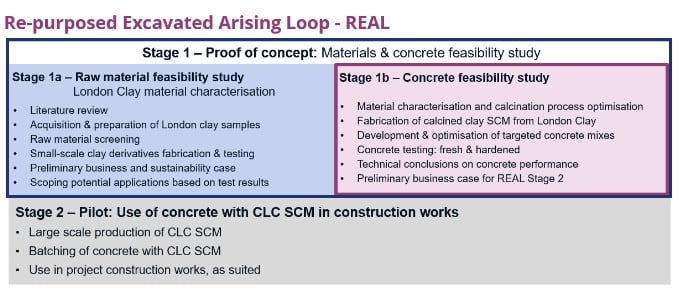
Stage 1a of the REAL project examined existing knowledge on calcined clays as well as London Clay mineralogy specifically. London Clay raw material from 10 different locations was sampled and characterised, followed by small-scale production of CLC and LWA from the samples and testing of their reactivity and expandability respectively, that constitute key performance indicators for their suitability as SCM and LWA. The results of this initial set of tests were satisfactory, therefore opening the door to advance into actual concrete trials in REAL1b. REAL 1a is covered more extensively in previous publications. [9, 10, 11]
REAL 1b – approach and structure
This paper presents the process and findings of REAL 1b, regarding CLC production and CLC concrete mix trials. REAL 1b focused on CLC as SCM because of its high decarbonisation and resource efficiency potential, if proven appropriate for use in concrete applications. A systematic sequence of sampling, testing and analysis took place at specialist laboratories to determine the composition and relevant characteristics of both the raw and calcined London Clay. A larger volume of London Clay was calcined and ground at industrial facilities thereafter to produce sufficient CLC SCM to develop and test concrete mix designs containing it.
REAL 1b process – work packages
- London Clay sampling
- Material characterisation for raw & calcined London Clay incl. calcination process optimisation
- London Clay industrial calcination & grinding
- Concrete mix design development
- Concrete trials
London Clay sampling
3x samples of excavated London Clay were collected from 3 different locations across the stretch of the SCS works in north-west London (Euston, Westgate, Victoria Road) and shipped to the University of Leeds for material testing.
Material characterisation
The tests, presented in Table 1 below, were conducted to characterise the raw and calcined London Clay samples. The clay samples received were initially broken down and dried out (at 40oC for 24 hours) and then crushed and homogenised. The calcination process in the laboratory static furnace was undertaken progressively at two different temperatures – 700oC and 800oC to select the optimum reactivity outcome.
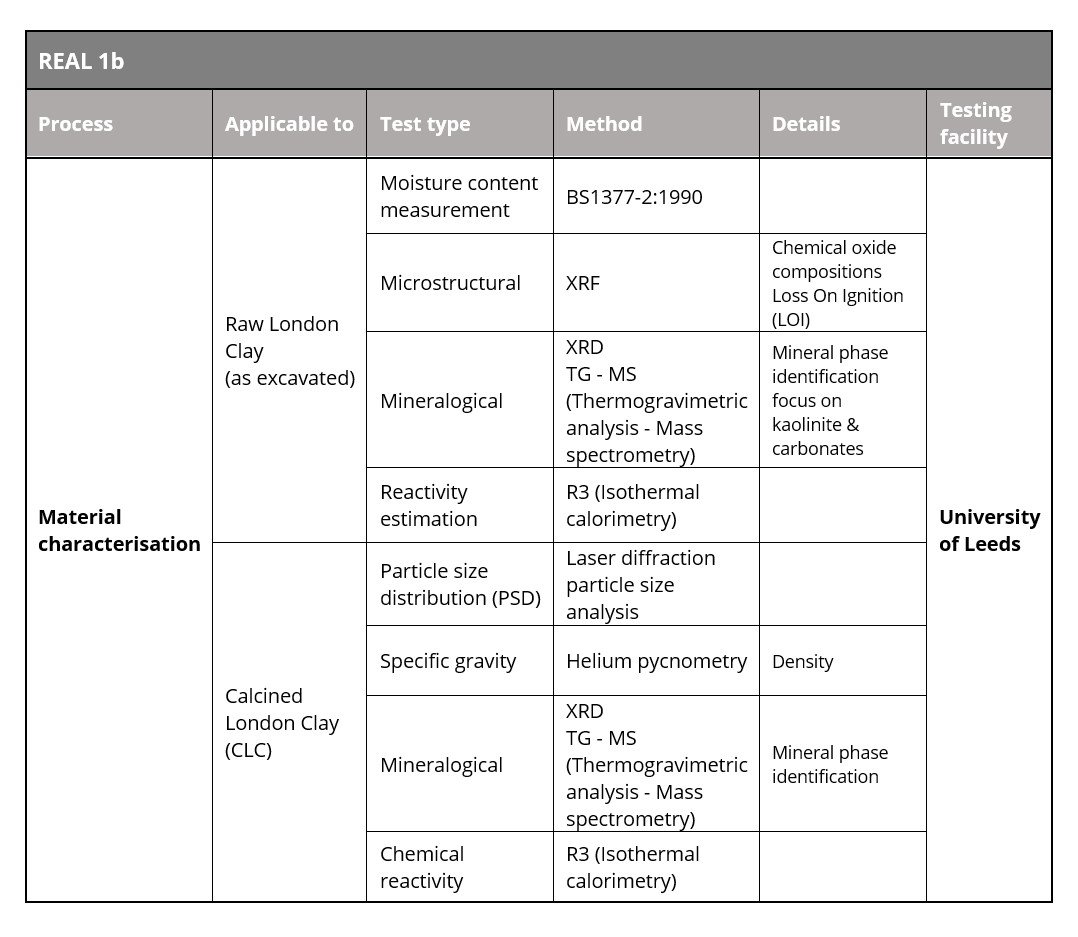
London Clay industrial calcination & grinding
Upon the material characterisation, a larger amount – approx. 300kg, of excavated London Clay from one of the sampled locations (Westgate) was collected and sent to a special industrial thermal processing facility to be calcined. The raw London Clay material was prepared and granulated and then fed continuously into an indirect rotary calciner at 800oC, aiming for each batch of material feed to have a residence time of 1 hour in the ‘hot zone’ of the calciner shell. The calcined material was then sent to be ground down to powder specification (D50 < 20 μm and D90 <100 μm), using a ball mill for use in concrete mixes.
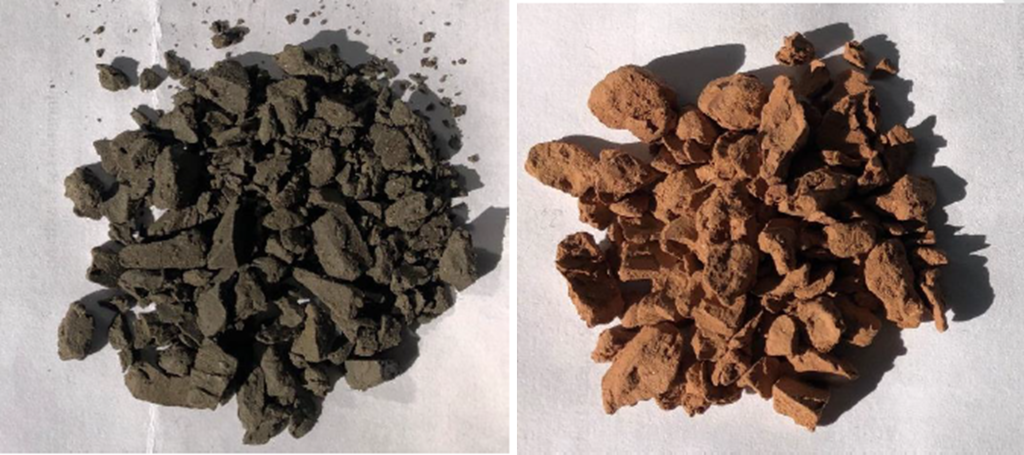
Concrete mix design development
Mix designs were developed by the University of Leeds based on existing research [12] on concrete mix development with calcined clay as SCM, considering the specific requirements of calcined London Clay for use in concrete based on material characterisation investigations and the specialist experience of the team on the topic. The mixes were initially developed and tested at mortar/paste level. The key aspects considered were optimised balance between maximised CLC cement replacement levels and compressive strength development, optimised gypsum and admixture (superplasticiser) content for adequate fresh concrete properties: workability, flowability and setting time.
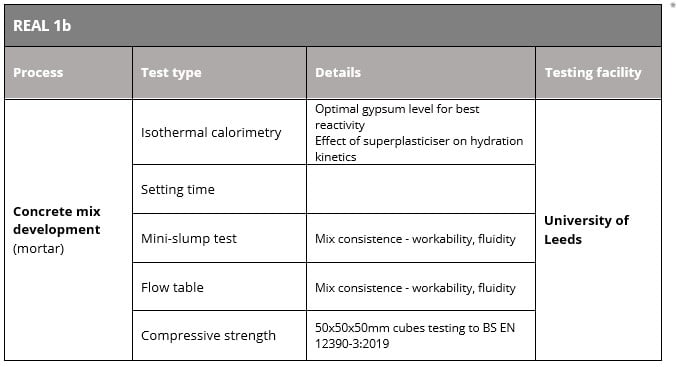
Concrete trials
Concrete trials were conducted at the SCS laboratories in the period between the summer of 2022 and end of 2023. 13x batches of different mix designs containing the produced CLC were completed and tested for physical characteristics and essential fresh and hardened concrete properties: workability (slump), flowability and workability retention time (slump retention). dry density and compressive strength. A continual observation and optimisation process was followed, whereby the mix designs were progressively being adjusted, based on the test results of the previous ones.
Outcomes
London Clay material characterisation results – Raw & calcined
The tests listed in Table 1 were undertaken at the specialist laboratory facilities at the University of Leeds. The material characterisation results for the raw, as excavated London Clay were within the same range as those of REAL 1a in terms of the estimated based in the kaolinite content of the samples, based on the thermogravimetric analysis (TG – MS). The moisture and estimated carbonates contents are also disclosed in Table 3 below.
Sample location | Moisture content (%) | Estimated kaolinite content (wt.%) | Estimated carbonates content (wt.%) |
Westgate | 43.2 ± 4.3% | 22.5 ± 3.6% | 8.4 ± 0.6% |
Euston | 22.3 ± 2.7% | 28.3 ± 4.1% | 5.0 ± 0.8% |
Victoria Road | 35.9 ± 3.9% | 28.6 ± 4.4% | 5.4 ± 0.9% |
As far as the calcined state of the clays is concerned, the CLC formed by processing the London Clay samples at 800oC for 1 hour demonstrated approx. 300 J/g of SCM by 7-day cumulative heat evolved in reactivity testing as per ASTM C1897-20. No significant traces of pyrite, a substance potentially adverse in concrete mixes, remained in the calcines samples – this result was in line with results from other relevant published research. [13, 14] The decomposition of carbonates during the calcination process was estimated to give rise to 24-42 kg CO2/tonne of calcined clay, which is deemed marginal taking into account that this is equivalent to max. 5% of the average carbon emissions from traditional clinker production. [15]
The industrially calcined London Clay from Westgate was also characterised using the same methods and the mineralogical analysis (XRD, TG-MS) and reactivity testing (R3 isothermal calorimetry) demonstrated very similar properties to the those of Westgate London Clay sample processed at the University of Leeds laboratories.
CLC classifies as moderately reactive calcined clay, according to the threshold proposed by Londono-Zuluaga et al. [16]
Initial checks of key chemical composition characteristics of the CLC meet the requirements of BS8615-1: 2019 – Specification for pozzolanic materials for use with Portland cement. [17] A complete exercise on this front is however needed to verify full compliance against BS8615. Subject to final compliance of CLC with BS8615, concrete mixes with up to 55% CLC are covered by existing concrete standards – BS8500-1:2015+A2:2019 [18], in the CIVB-P type.
Mix development at concrete mortar/paste level
The tests listed in Table 2 above were undertaken at the University of Leeds to help determine the optimum proportions for the different constituents.
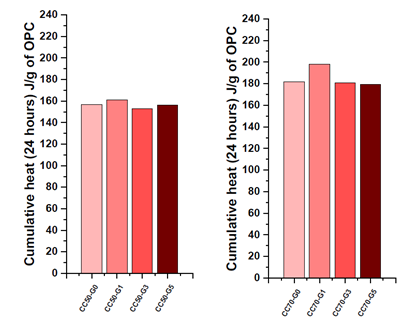
Mixes with two different levels of cement replacement with CLC – 50% & 70%, were developed upon SCS request. 5x mix variants with total binder (cementitious material) contents of 280 – 310 kg/m3, w/b ratios of 0.4 – 0.6, gypsum addition of 1% wt. and superplasticiser dosages optimised accordingly (0.5 – 1.1%) were proposed by the University of Leeds for each replacement level (10x mix designs in total), based on the cement paste level tests. Figure 3 above illustrates the impacts of varying gypsum levels on mix reactivity showing that 1% wt. resulted in the highest reactivity for both CLC replacement levels – 50% CLC on the left and 70% CLC on the right.
Concrete trials results
Initial concrete trials
The mixes in Table 4 below were developed by SCS for the concrete trials at the SCS materials labs, based on the original mix designs provided by the University of Leeds.
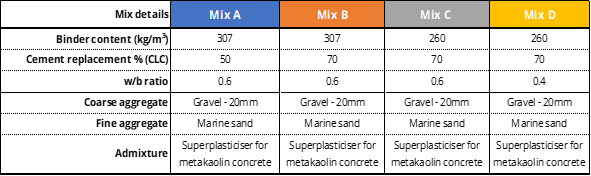
The total cementitious (binder) contents and water-to-binder (w/b) ratios for Mixes A and B were determined based on the University of Leeds propositions, while Mixes C and D were developed following initial assessment of the test results achieved from Mixes A and B, that showed sufficient strength development. On this basis, the total binder content was reduced to investigate the effect on strength. The type of aggregates was chosen based on the availability at the time of the laboratory concrete trials. Mix D was developed with a low w/b ratio to assess the behaviour of a concrete mix with CLC SCM, using lower water content compared to the other mixes.
The admixture used was a high range water reducing/superplasticising admixture for metakaolin concrete. The initial dosage of the superplasticiser was based on the mix design suggestions from the University of Leeds, where superplasticizer dosage was optimised using mini-slump measurements. The superplasticiser admixture dosage between the different batches was adjusted, while trying to achieve a consistence class of S4, which would be the most widely used consistence class on the project and very commonly used in the industry, especially for pumpable concrete. The effect of the superplasticiser dosage variability on the mix consistence and its retention was observed to inform progressive adjustments. In general, the concrete mixes demonstrated adequate consistence with the superplasticiser dosage set at approx. 0.8% but did not retain workability. Some shear slumps were recorded during the consistence testing, which, in conjunction with the visual appearance of the concrete produced, showed that the fines content should be increased to counteract this. Some discrepancies were observed between certain batches of the same mixes which can be attributed to differences in aggregates moisture content and casting temperatures. Notably, the mix with the lowest paste volume and w/b ratio exhibited very low slump for the considered superplasticiser content, highlighting the need for further optimisation in the mix design with CLC, particularly for mixes with relatively low total binder content and w/b ratio.
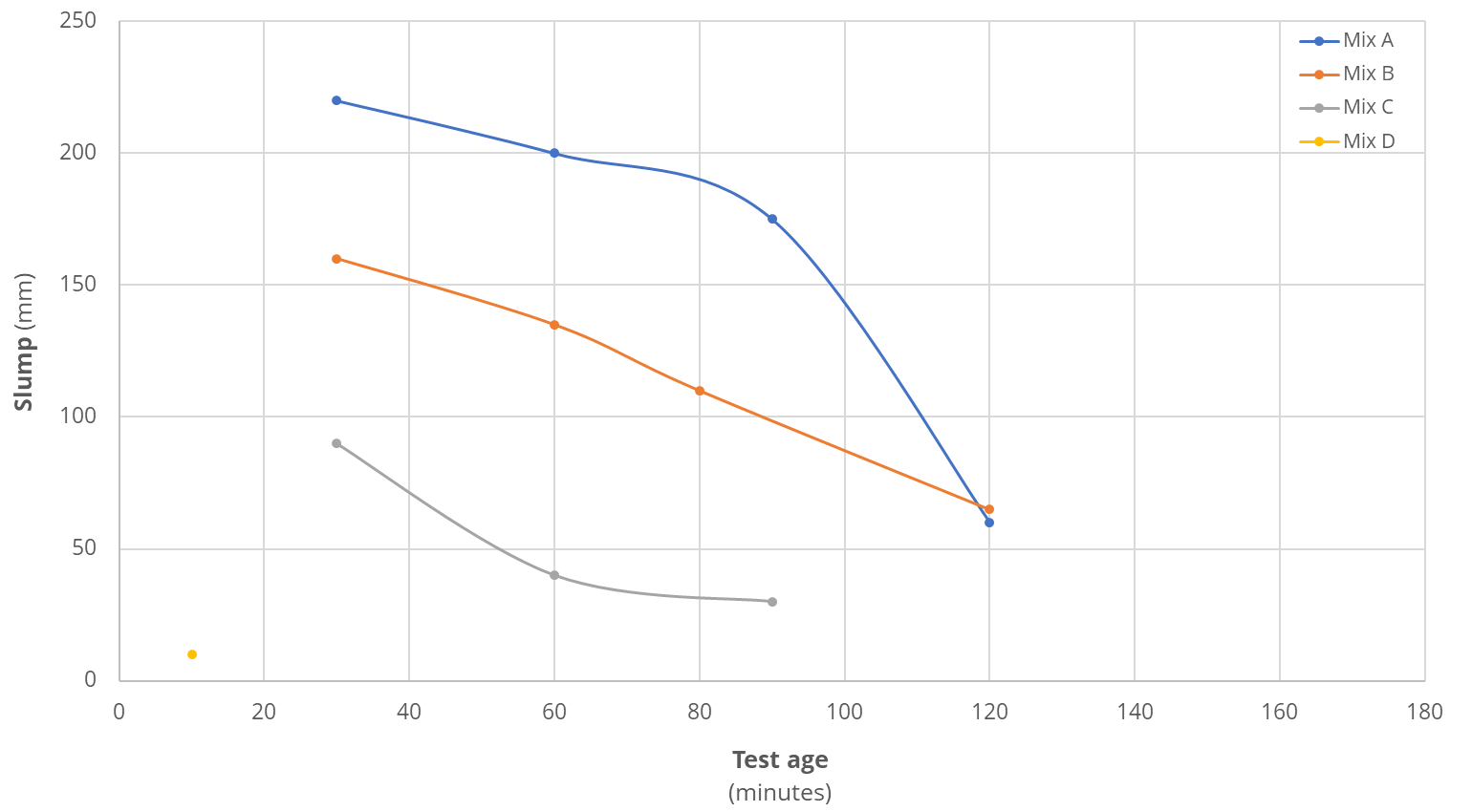
The compressive strength development of the trialled concrete mixes exceeded the design expectations, achieving an average of 47.6MPa for Mix A, 39.5MPa at 28 days for Mix B, 35.2MPa for Mix C and 57.4MPa for Mix D, all at 28 days. The results for compressive strength are summarised in Figures 5 and 6 below, presented in different formats to facilitate clarity.
It is noted that two batches from Mix B have been excluded from the results reporting with a view to provide an as consistent picture as possible – one batch was considered an outlier due to relatively very high strength development and one batch contained mixed types of aggregates. The concrete performance presented in this paper is progressively building upon the test results published previously. [19, 20]
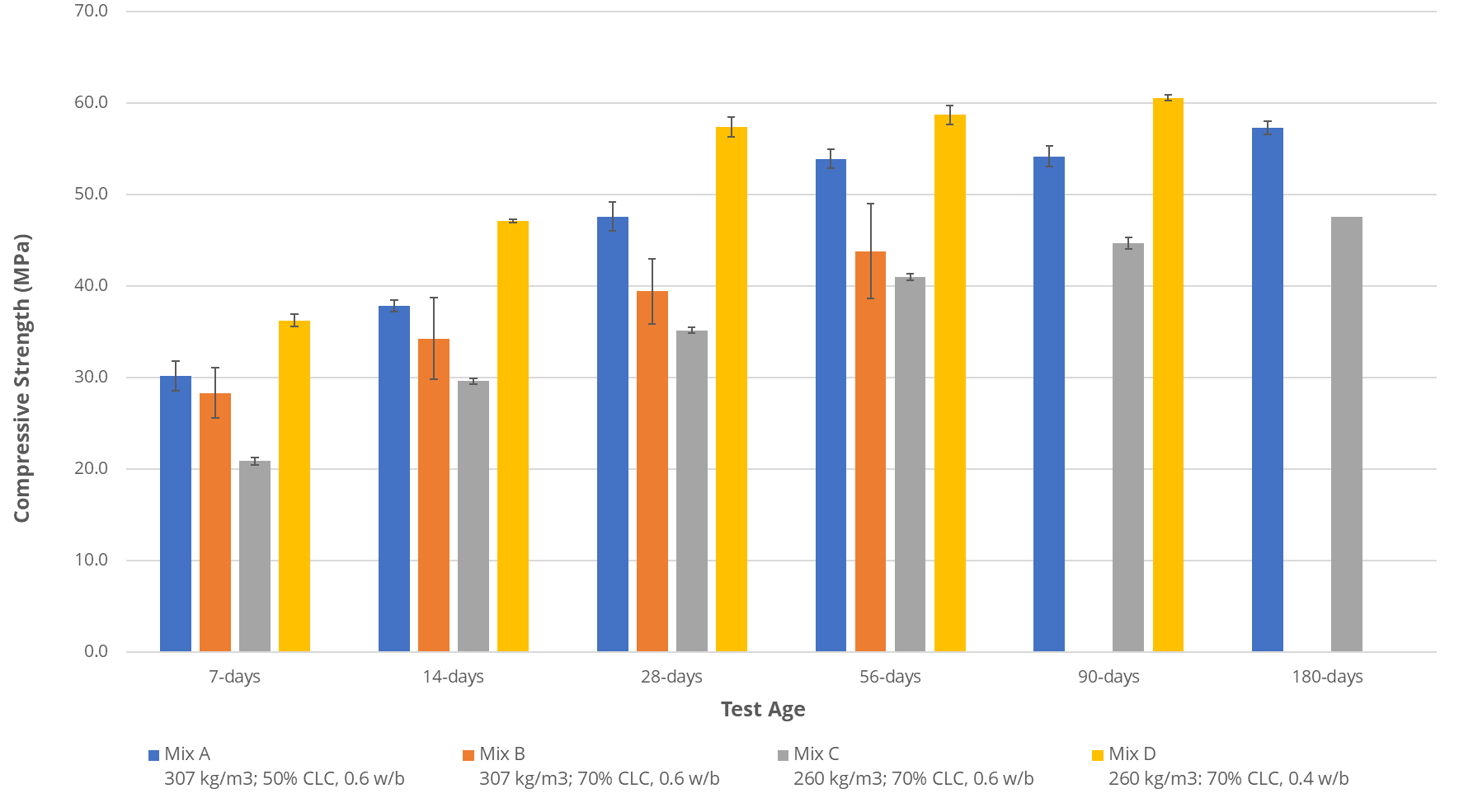
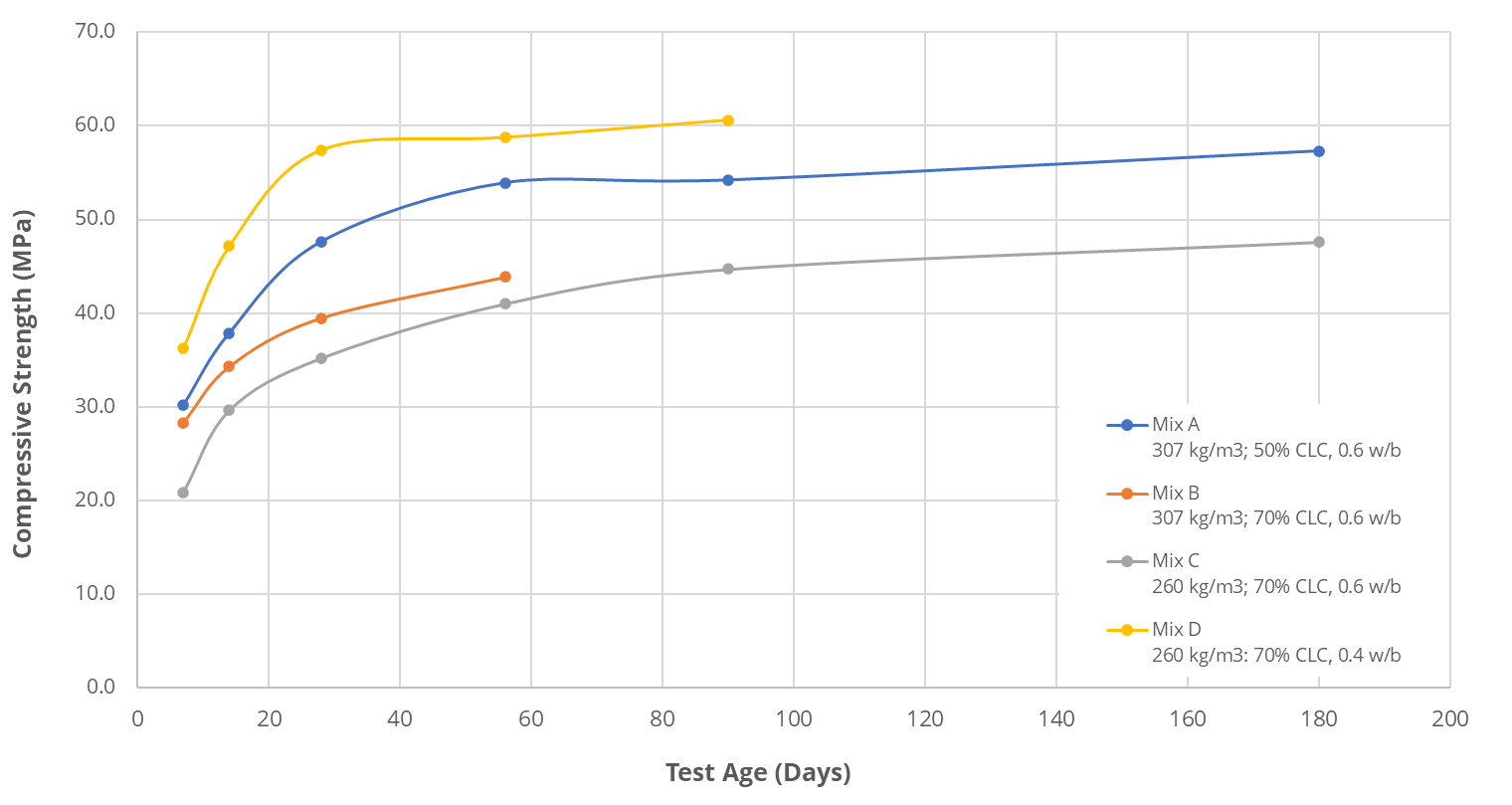
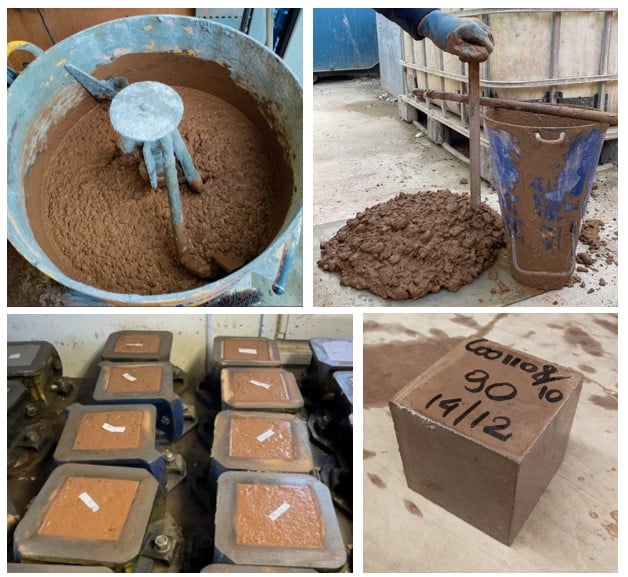
Optimised concrete trials
The assessment of the fresh and hardened concrete test results drove the development of the optimised concrete mixes, which were prepared and then tested at the on-site SCS laboratory.
A number of adjustments were made to the mix design, primarily aiming to improve workability and workability retention:
- Increased fine aggregate content (from 38% to 44%)
- Limestone, instead of gravel, coarse aggregates were used for one of the batches to assess the effect of change in aggregate type on mix performance
- A special superplasticiser for concrete mixes with calcined clay and limestone (LC3) was used – this admixture is not yet commercialised, and the results from the mix trials containing it were shared with the manufacturer as feedback for the superplasticiser’s performance.
The higher total binder content (307 kg/m3) was selected for the optimised mix variants to avoid compromising strength gain. 50% cement replacement with CLC was chosen to fall within the allowance of existing concrete codes with a view to focus on mixes that could be readily approved for use in actual construction works, if their performance is proven. 3x optimised mixes with the 307 kg/m3 and 50 wt.% cement replacement with CLC were designed to study the fresh concrete behaviour in particular: A control mix (Mix A1) with the original metakaolin superplasticiser and another two mixes with the specialist LC3 superplasticiser using gravel and limestone coarse aggregates, respectively. The optimised concrete mix details are shown in Table 5 below.
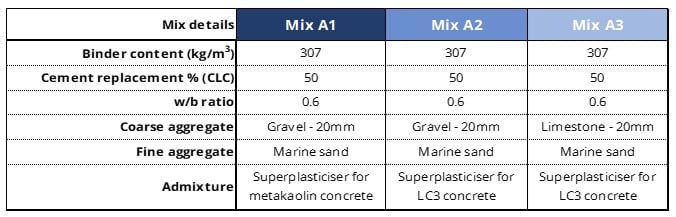
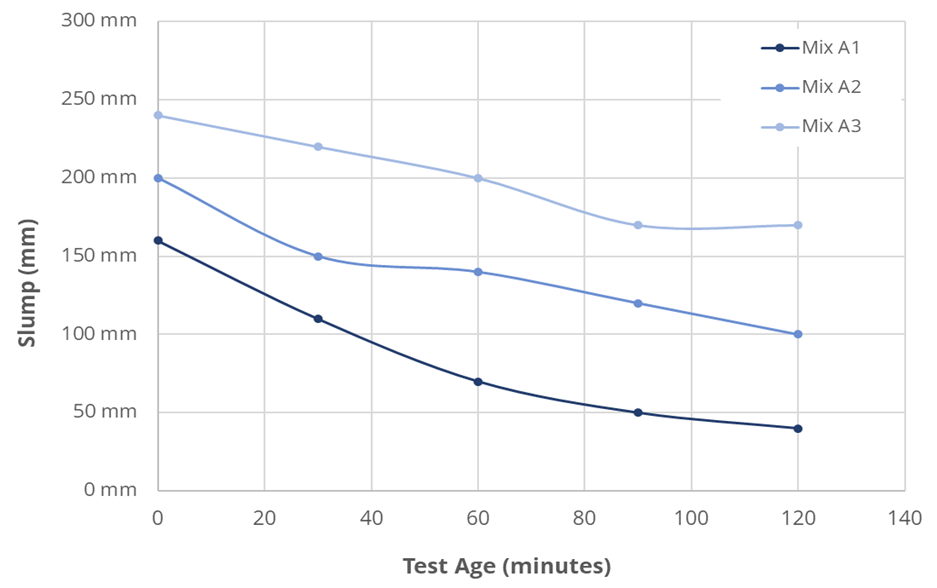
The average compressive strength results for the optimised mixes was slightly higher yet consistent with that of Mix A of the original batch, achieving approx. 50MPa at 28 days.
Learnings and recommendations
The REAL project has shown that concrete containing the moderately reactive CLC can demonstrate robust performance in terms of both fresh and hardened properties. More work is needed to verify these outcomes with further testing results and also investigate further characteristics that have not been looked at so far. Recommended next steps are listed below:
Specific to CLC concrete:
- A detailed compliance exercise against BS8615 should be undertaken for CLC to ensure it qualifies as an SCM for use in concrete against the requirements of the standard. This should assure the quality of CLC and allow for its use in commercial batching plants.
- Feasibility to achieve adequate key fresh concrete behaviour was demonstrated at the optimised REAL concrete trials. Nevertheless, more work is needed on the workability and workability retention front with special focus on admixtures to establish the mix designs and constituent proportions that work best.
- Further hardened properties of the CLC concrete, such as flexural and tensile splitting strength need to be tested.
- Investigation into the microstructures of the CLC concrete affecting strength development is required to understand the mechanisms of the high strengths shown during trials and establish whether kaolinite content is the only decisive factor influencing reactivity and strength development or whether more aspects to be considered that are not yet sufficiently understood.
- Further testing is required on the durability characteristics of the CLC concrete – resistance to carbonation, chlorides, etc. to assess its suitability for use in permanent reinforced concrete elements.
- Ternary concrete mixes containing Portland cement, CLC and limestone (LC3 with CLC) to be trialled.
- Investigation of the properties of CLC over time could be useful to assess any variations.
For all calcined clays and overall concrete decarbonisation:
- Gradual yet imminent adoption of mixes with calcined clays by designers as well as contractors, for use in actual construction works – initially low risk, is required for industry practitioners and site teams to familiarise themselves with this type of concrete.
- The concrete and cement suppliers need to accelerate progress on calcined clays production and the optimisation of relevant technologies, supporting appropriate research and development.
Conclusion
The results of REAL 1b have validated the findings of REAL 1a showing that London Clay, although containing relatively low levels of kaolinite content – approx. 19-33% wt., can be turned into moderately reactive calcined clay that can perform adequately as an SCM in concrete.
The results of the laboratory concrete trials undertaken by SCS have demonstrated consistently robust compressive strength development. 13x binary concrete mixes with 260-307kg/m3 of total binder content and 50-70% cement replacement with CLC were batched and tested for key fresh and hardened properties. The average strength developed across all mixes was 46.5MPa at 28 days. The mix designs were also adjusted to optimise workability and workability retention that has initially been challenging. The last set of the REAL concrete trials was focused on these aspects and demonstrated that viable workability and slump retention levels can be achieved for CLC concretes with suitable admixtures and appropriate mix constituent proportions.
Overall, it was proven that CLC concretes can display satisfactory technical performance regarding key characteristics – compressive strength, workability and workability retention for use in real world applications. More work is needed to verify further key properties, primarily around durability aspects of the CLC concretes.
Recommendations for further research and testing, compliance with relevant standards (BS8615, etc.) to enhance confidence in CLC, optimisation of calcination methods, acceleration of scaling up calcined clay production and adoption of CLC/calcined clay concretes by the stakeholders of the construction industry were made based on the findings of the REAL study. Advancing the uptake of calcined clays as SCMs in concrete can reduce the demand of PC as well as the reliance on the currently available yet restricted lower carbon cement replacements – GGBS and PFA. Calcined clays can therefore significantly contribute to the decarbonisation of the concrete industry and present new commercial opportunities too.
Acknowledgements
The authors would like to acknowledge Alastair Marsh and Suraj Rahmon from the University of Leeds for their scientific contribution to this project and the SCS Materials Laboratory team for their support in the concrete trails.
The authors would also like to thank the HS2 Materials and Durability team as well as the HS2 and SCS representatives from the project management and environment functions of the HS2 London Tunnels Integrated Project Team for their active support, without which this work would not have been possible.
Many thanks also to all the specialist academic and industry collaborators who have contributed to the REAL work (EPFL, UCL, SIKA, Mitchell Dryers, LECA).
References
- IEA Cement Net Zero Emissions Guide Paris (2023), Licence: CC BY 4.0
- Annual carbon dioxide (CO₂) emissions worldwide from 1940 to 2023
- Marsh, A.; Dillon, T.; Bernal, S. Cement and Concrete Decarbonisation Roadmaps – a Meta-Analysis Within the Context of the United Kingdom. RILEM Tech Lett 2023, 8, 94-105
- Global Cement and Concrete Association The GCCA 2050 Cement and Concrete Industry Roadmap for Net Zero Concrete
- The Manufacturing Process (cembureau.eu)
- Alujas Diaz, A., Almenares Reyes, R.S., Hanein, T. et al. Properties and occurrence of clay resources for use as supplementary cementitious materials: a paper of RILEM TC 282-CCL. Mater Struct 55, 139 (2022).
- Hanein, T., Thienel, KC., Zunino, F. et al. Clay calcination technology: state-of-the-art review by the RILEM TC 282-CCL. Mater Struct 55, 3 (2022).
- The Institution of Structural Engineers The efficient use of GGBS in reducing global emissions
- Papakosta, A., Kanavaris, F., Pantelidou, H. et al. Transformation of London clay into construction resources: Supplementary cementitious material and lightweight aggregate. HS2 Learning Legacy (2020)
- Kanavaris, F., Papakosta, A., Zunino, F. et al. Suitability of Excavated London Clay from Tunnelling Operations as a Supplementary Cementitious Materials and Expanded Clay Aggregate. International Conference on Calcined Clays for Sustainable Concrete, 5-7 July 2022, Lausanne, Switzerland.
- Kanavaris, F., Papakosta, A. Calcining excavated London Clay to produce supplementary cementitious material and lightweight aggregate. Concrete 56, 40-42 (2022)
- Zunino, F., Dhandapani, Y., Ben Haha, M. et al. Hydration and mixture design of calcined clay blended cements: review by the RILEM TC 282-CCL. Mater Struct 55, 234 (2022).
- Zunino, F., Scrivener, K. Oxidation of pyrite (FeS2) and troilite (FeS) impurities in kaolinitic clays after calcination. Mater Struct 55, 9 (2022).
- Dhandapani, Y., Marsh, A.T.M., Rahmon, S. et al. Suitability of excavated London clay as a supplementary cementitious material: mineralogy and reactivity. Mater Struct 56, 174 (2023)
- Environmental Product Declaration
- Londono-Zuluaga, D., Gholizadeh-Vayghan, A., Winnefeld, F. et al. Report of RILEM TC 267-TRM phase 3: validation of the R3 reactivity test across a wide range of materials. Mater Struct 55, 142 (2022).
- British Standards Institution (BSI). (2019). BS 8615-1: 2019 Specification for pozzolanic materials for use with Portland cement: Natural pozzolana and natural calcined pozzolana. London: BSI. ISBN: 9780539002089
- British Standards Institution (BSI). (2019). BS 8500-1:2015+A2:2019 Concrete. Complementary British Standard to BS EN 206. Method of specifying and guidance for the specifier
- Dhandapani, Y., Rahmon, S., Marsh, A.T.M. et al. Fresh state properties of low clinker cement made of excavated London Clay from tunnelling operations. 41st Cement & Concrete Science Conference, 12-13 September 2022, Leeds, UK
- Papakosta, A., Tsoumelekas, A., Wichman, W. et al. Using Non-standard Concretes in a Major Infrastructure Project: A Multidisciplinary Approach for Implementation. In: Jędrzejewska, A., Kanavaris, F., Azenha, M., Benboudjema, F., Schlicke, D. (eds) International RILEM Conference on Synergising Expertise towards Sustainability and Robustness of Cement-based Materials and Concrete Structures. SynerCrete 2023. RILEM Bookseries, vol 44. Springer, Cham.
Peer review
- Dimitrios OikonomidisHS2 Ltd