Eliminating harm using exclusion zone technology
The failure of exclusion zones is one of the construction industry’s biggest risks leading to injury of personnel. This paper details the efforts to reduce harm and improve safety during a floor-by-floor demolition to prevent demolition materials being dropped into areas where there was a potential for a workforce interface. Passive Infrared (PIR) technology was used to optimise the exclusion zone for safe working and is now being developed for other areas on site and future use.
The learning in this paper will be of interest to project teams responsible for managing exclusion zones on construction sites.
Background and industry content
The Enabling Works Contract (EWC) on the southern section (Area South) is part of High Speed Two (HS2) phase one which includes demolition of buildings within the wider Euston area, utility diversions, environmental and ecological monitoring and a programme of historic environment and archaeological activities, delivered by the Costain Skansja joint venture (CSjv).
Possession of Regent’s Park Estate in the London Borough of Camden (Figure 1) took place in February 2019, and the site consisted of 6 buildings:
- Ainsdale
- Old Tenants Hall
- Eskdale
- Silverdale
- Granby House
- Stalbridge house
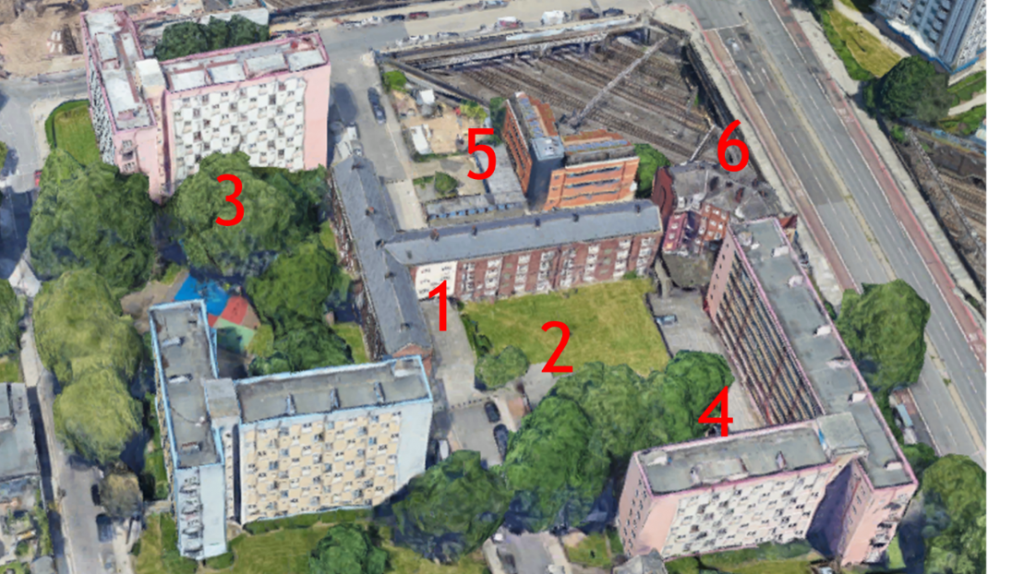
Due to the proximity of the Coniston Building (London Borough of Camden) the West Wing of Silverdale (Figure 2) had to be encapsulated in scaffolding and demolished using a floor-by-floor method.
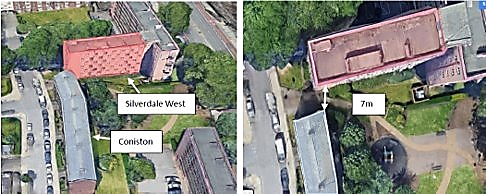
As part of the top-down demolition, 8 tonne machines were lifted on to each floor where they demolished the floor above and the walls around them, with the arisings from the demolition falling on to the floor slab. As there was a very restrictive limit of permissible loading on the floor slab (including the machines and attendant machines), the demolition arisings needed to be regularly cleared arisings from each floor of the building as the demolition progressed. This was done with the use of a Skid-Steer Loader (Figure 3), using the lift shaft as a chute to drop material from high to low level.
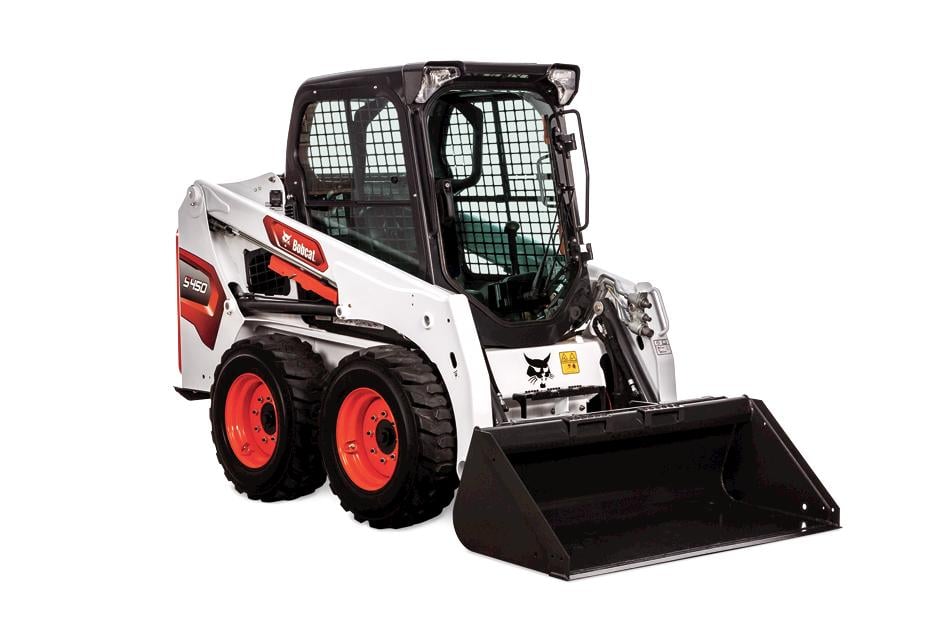
The arisings would then be cleared on the ground floor out of the shaft by Skid steer. This was identified in the planning stage as high risk, as there was no line of sight for the team working on the top level, who could not tell when the bottom Skid-Steer was accessing the lift shaft or in the exclusion zone.
Demolition Activities have three defined zones for operation:
- Full Exclusion Zones – no one enters at all – typically used for drop zones
- Restricted Access Zones – only Demolition Personnel can enter with the right skills, training and knowledge of the risk associated with the ongoing activities
- Normal zones – access to and from the demolition point of works, non-demolition work activities
Development of safer exclusion zone approach
Aware of the inherent risks and having assessed the situation, a Passive Infrared (PiR) exclusion zone system was included (Figure 4) as an additional control measure. This was to ensure the skid steer nor anyone else entered the exclusion zone at the bottom of the shaft while arisings were being loaded down the shaft. Due to no visibility and no clear lines of sight, this system deployed technology to provide an automated stop works message to those working above.
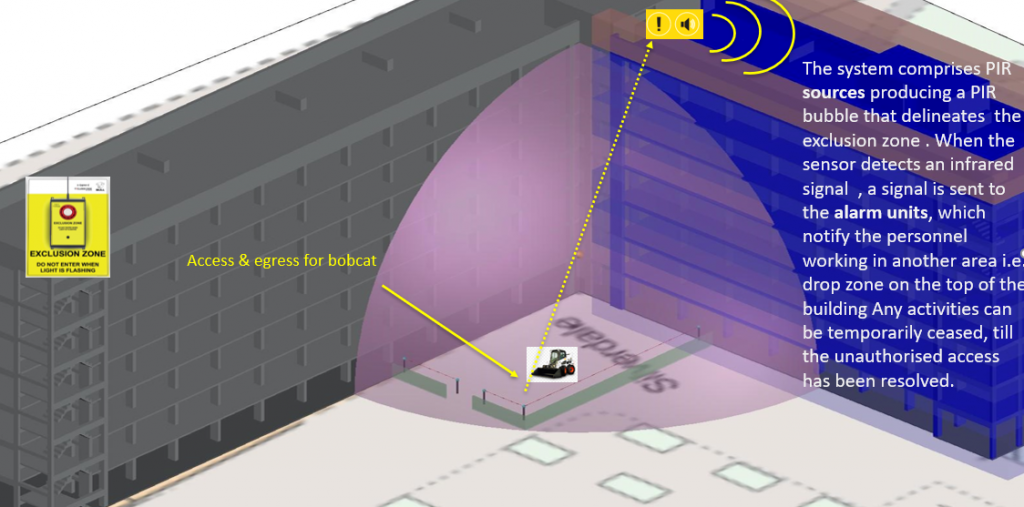
The system was set to monitor the exclusion area and then detected any break in the infrared signals entering that area. This in turn triggered both an audio and visual alarm alerting the team at high level to stop clearing arisings down the shaft immediately. This allowed the demolition supervisor to radio through to the bottom team to see who or what had breached the exclusion zone.
The lift shafts were closed on all floors except the top floor where arisings are created and pushed down the chute, and the bottom floor. There was also a detailed inspection regime of the system to ensure it was fully functional in its operation at the start of each shift, ensuring it was working correctly prior to any works beginning that day.
Lessons learned
The use of the PiR system gave confidence that no one was being put at risk when dropping demolition arising down the lift shaft.
The visual alert is more important than the audible alert, this is due to the noise of the demolition activities and hearing protection worn making it difficult to hear the alarm. It is also invasive for our surrounding neighbours.
It is important to be aware that the visual alert needs to be positioned in the path of the Skid-Steer Loader, which depending on the demolition sequencing, could require moving as works progress.
The automation of the PiR system, as opposed to a manually operated traffic light system, removed human error and reduced required labour in and around the demolition interface.
A member of the demolition team stated: “The PIR system gave us confidence to drop material knowing we were not going to hurt someone. Demolition is loud and you can’t always hear to shout and in this case we couldn’t see down the bottom either. The flashing lights and alarm is very clear, even in demo”
Recommendations
Linking the PiR system to a traffic light system to create a go/no-go visual display would be better than a flashing beacon that only warns when there is a breach.
A PIR system could be used for a number of demolition practises requiring exclusion zones, not just drop zones and anywhere else requiring exclusion zones, e.g., under lifting or scaffold installation activities.
PIR can also be used in plant and pedestrian interfaces, highlighting when personnel have breached barriers.
The next steps would be to link this into auto-cut offs for machines when exclusion zones are breached which is currently under consideration.
Acknowledgements
- The Euston Approaches Demolitions Team; Dan Brown, Era Shah, Joe Jelfs, George Horsley, Hanna Toorabally, Ricky Prett, Andy Evans
- HS2; Martin Oates, Neil Bishop, Andreas Michael
- Clifford Devlin